Introduction to PCB materials
Printed Circuit Boards (PCBs) are the backbone of modern electronics. They provide a platform for mounting electronic components and establishing electrical connections between them. The choice of PCB material is crucial for the performance, reliability, and longevity of your electronic project. With a wide range of PCB Materials available, each with its unique properties and characteristics, selecting the right one can be a daunting task. In this comprehensive guide, we will explore the various factors to consider when choosing the right PCB material for your electronic project.
Factors to Consider When Selecting PCB Materials
1. Dielectric Constant (Dk)
The dielectric constant, also known as relative permittivity, is a measure of a material’s ability to store electrical energy. It indicates how much the material will concentrate electric flux lines. A higher dielectric constant means that the material can store more electrical energy. The dielectric constant is an important factor to consider when designing high-frequency circuits, as it affects the signal propagation speed and impedance matching.
Material | Dielectric Constant (Dk) |
---|---|
FR-4 | 4.2 – 4.5 |
Rogers RO4003C | 3.38 |
Polyimide | 3.5 |
PTFE (Teflon) | 2.1 |
Alumina (Ceramic) | 9.8 |
2. Dissipation Factor (Df)
The dissipation factor, also known as loss tangent or tanδ, is a measure of a material’s ability to dissipate electrical energy as heat. It represents the inefficiency of the material in terms of power loss. A lower dissipation factor is desirable for high-frequency applications, as it minimizes signal loss and ensures better signal integrity.
Material | Dissipation Factor (Df) |
---|---|
FR-4 | 0.02 |
Rogers RO4003C | 0.0027 |
Polyimide | 0.002 – 0.003 |
PTFE (Teflon) | 0.0002 – 0.0005 |
Alumina (Ceramic) | 0.0001 |
3. Thermal conductivity
Thermal conductivity is a measure of a material’s ability to conduct heat. It is an important factor to consider when dealing with high-power applications or environments with significant temperature variations. A higher thermal conductivity allows for better heat dissipation, preventing the buildup of excessive heat that can damage components or affect circuit performance.
Material | Thermal Conductivity (W/mK) |
---|---|
FR-4 | 0.3 – 0.4 |
Aluminum-backed PCB | 1.0 – 2.0 |
Copper-backed PCB | 380 – 400 |
Ceramic (Alumina) | 20 – 30 |
Aluminum Nitride (AlN) | 140 – 180 |
4. Mechanical Strength and Flexibility
The mechanical strength and flexibility of a PCB material are crucial factors to consider, especially in applications that involve physical stress, vibrations, or bending. The material should be able to withstand the expected mechanical forces without cracking, delaminating, or losing its structural integrity.
- FR-4: FR-4 is a rigid material with good mechanical strength. It is suitable for most standard PCB applications.
- Polyimide: Polyimide is a flexible material that can withstand repeated bending and flexing. It is often used in flexible PCBs and applications where the board needs to conform to a specific shape.
- High-Tg FR-4: High-Tg FR-4 (Tg: Glass Transition Temperature) offers improved mechanical strength and thermal stability compared to standard FR-4. It is suitable for high-reliability applications.
5. Temperature Resistance
The temperature resistance of a PCB material determines its ability to withstand high temperatures without degrading or losing its properties. This is particularly important in applications that involve soldering, reflow processes, or exposure to high-temperature environments.
Material | Maximum Operating Temperature (°C) |
---|---|
FR-4 | 130 – 140 |
High-Tg FR-4 | 170 – 180 |
Polyimide | 260 – 300 |
PTFE (Teflon) | 260 – 280 |
Ceramic (Alumina) | 1500 – 1700 |
6. Moisture Resistance
Moisture resistance is a critical factor for PCBs that will be exposed to humid environments or subjected to cleaning processes. Moisture absorption can lead to dimensional changes, delamination, and degradation of the PCB material. It is essential to choose a material with low moisture absorption to ensure the long-term reliability of the circuit.
- FR-4: FR-4 has moderate moisture resistance and is suitable for most indoor applications.
- Polyimide: Polyimide has excellent moisture resistance and is often used in harsh environments.
- PTFE (Teflon): PTFE has very low moisture absorption and is suitable for high-reliability applications in humid conditions.
7. Cost and Availability
Cost and availability are practical considerations when selecting a PCB material. Some specialized materials, such as high-frequency laminates or ceramic substrates, can be significantly more expensive than standard FR-4. It is important to balance the performance requirements with the budget constraints of your project. Additionally, ensure that the chosen material is readily available from PCB manufacturers to avoid delays in production.
Common PCB Materials and Their Applications
1. FR-4
FR-4 (Flame Retardant 4) is the most widely used PCB material. It is a composite material made of woven fiberglass cloth reinforced with an epoxy resin binder. FR-4 offers a good balance of electrical, mechanical, and thermal properties at a relatively low cost. It is suitable for a wide range of applications, including:
- Consumer electronics
- Industrial control systems
- Telecommunications equipment
- Automotive electronics
2. High-Frequency Laminates
High-frequency laminates, such as Rogers RO4000 series or Isola IS680, are specifically designed for high-frequency and high-speed applications. These materials have low dielectric constant and low dissipation factor, enabling faster signal propagation and minimizing signal loss. They are commonly used in:
- RF and microwave circuits
- Radar systems
- Wireless communication devices
- High-speed digital circuits
3. Flexible PCB Materials
Flexible PCB materials, such as polyimide (Kapton) or polyester (PET), are used when the circuit needs to bend, flex, or conform to a specific shape. These materials have excellent mechanical flexibility and can withstand repeated bending without damage. Flexible PCBs are used in:
- Wearable electronics
- Medical devices
- Aerospace and defense applications
- Flexible sensors and displays
4. Metal-Backed PCBs
Metal-backed PCBs use a metal substrate, such as aluminum or copper, to enhance thermal conductivity and heat dissipation. They are commonly used in high-power applications or environments with significant heat generation. The metal substrate acts as a heat sink, efficiently transferring heat away from the components. Metal-backed PCBs are used in:
- Power electronics
- LED lighting systems
- Automotive power modules
- High-power RF amplifiers
5. Ceramic PCBs
Ceramic PCBs use ceramic substrates, such as alumina (Al2O3) or aluminum nitride (AlN), instead of traditional organic materials. Ceramic materials offer excellent thermal conductivity, high temperature resistance, and low dielectric loss. They are used in applications that require high reliability and performance, such as:
- High-temperature electronics
- High-power RF and microwave circuits
- Aerospace and defense systems
- Medical implantable devices
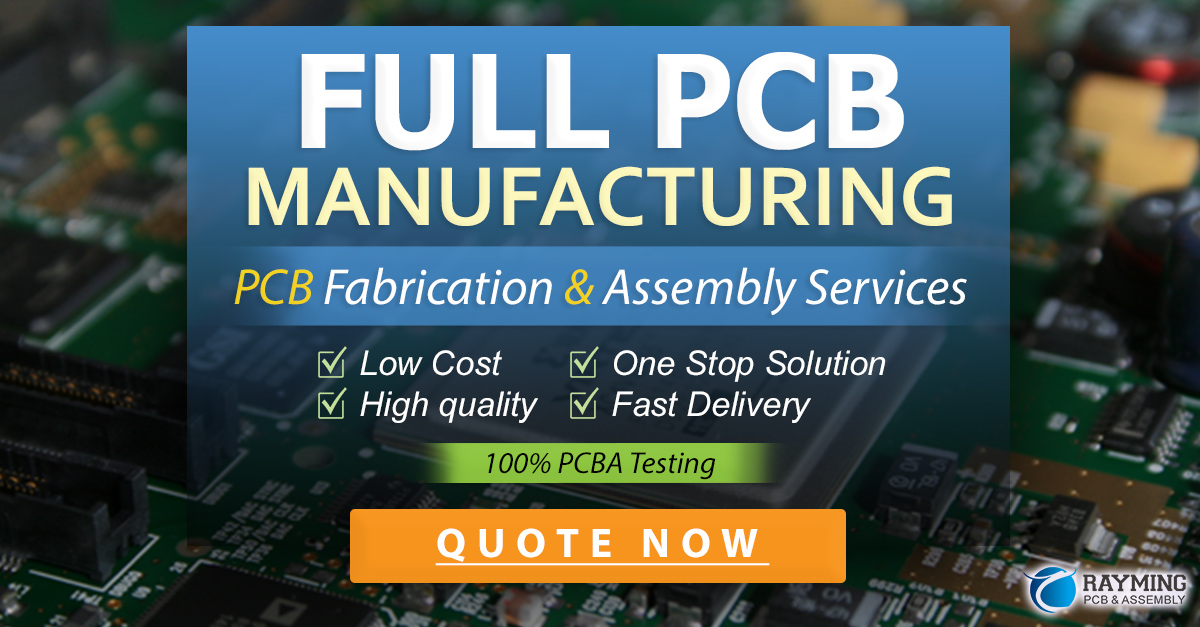
Design Considerations for Different PCB Materials
When designing a PCB, it is important to consider the specific properties and limitations of the chosen material. Here are some design considerations for different PCB materials:
1. FR-4
- Ensure proper copper weight and thickness for current carrying capacity and heat dissipation.
- Consider the glass transition temperature (Tg) of the FR-4 material for high-temperature applications.
- Use appropriate trace widths and spacing to minimize crosstalk and signal integrity issues.
2. High-Frequency Laminates
- Design controlled impedance traces to match the desired characteristic impedance.
- Minimize discontinuities and abrupt changes in trace geometry to reduce signal reflections.
- Use proper grounding techniques and avoid split planes to minimize electromagnetic interference (EMI).
3. Flexible PCBs
- Consider the bend radius and flexing requirements when designing the trace layout and component placement.
- Use strain relief techniques, such as stiffeners or flexible-to-rigid transitions, to prevent damage during flexing.
- Choose appropriate adhesives and coverlay materials for protection and insulation.
4. Metal-Backed PCBs
- Ensure proper thermal interface between the components and the metal substrate for efficient heat transfer.
- Consider the thermal expansion mismatch between the metal substrate and the components when selecting soldering techniques.
- Use appropriate insulation and dielectric materials to prevent electrical shorting.
5. Ceramic PCBs
- Consider the brittle nature of ceramic materials during handling and assembly processes.
- Use appropriate metallization techniques, such as thick-film or thin-film deposition, for creating conductive patterns.
- Ensure proper matching of thermal expansion coefficients between the ceramic substrate and the components to avoid stress and cracking.
Frequently Asked Questions (FAQ)
1. What is the most commonly used PCB material?
The most commonly used PCB material is FR-4 (Flame Retardant 4). It is a composite material made of woven fiberglass cloth reinforced with an epoxy resin binder. FR-4 offers a good balance of electrical, mechanical, and thermal properties at a relatively low cost, making it suitable for a wide range of applications.
2. What are high-frequency laminates, and when should they be used?
High-frequency laminates are PCB materials specifically designed for high-frequency and high-speed applications. They have low dielectric constant and low dissipation factor, enabling faster signal propagation and minimizing signal loss. High-frequency laminates, such as Rogers RO4000 series or Isola IS680, should be used in applications like RF and microwave circuits, radar systems, wireless communication devices, and high-speed digital circuits.
3. What are the advantages of using flexible PCB materials?
Flexible PCB materials, such as polyimide (Kapton) or polyester (PET), offer several advantages:
- Mechanical flexibility: Flexible PCBs can bend, flex, and conform to specific shapes without damage.
- Space savings: Flexible PCBs can be folded or rolled up, allowing for more compact designs.
- Durability: Flexible materials can withstand repeated bending and flexing, making them suitable for applications with moving parts or frequent handling.
- Lightweight: Flexible PCBs are generally lighter than rigid PCBs, which is advantageous for portable and wearable devices.
4. When should I consider using metal-backed PCBs?
Metal-backed PCBs are recommended when your application involves high-power components or generates significant heat. The metal substrate, such as aluminum or copper, acts as a heat sink, efficiently transferring heat away from the components. Metal-backed PCBs are commonly used in power electronics, LED lighting systems, automotive power modules, and high-power RF amplifiers.
5. What are the benefits of using ceramic PCBs?
Ceramic PCBs offer several benefits compared to traditional organic PCB materials:
- High thermal conductivity: Ceramic materials, such as alumina or aluminum nitride, have excellent thermal conductivity, enabling efficient heat dissipation.
- High temperature resistance: Ceramic PCBs can withstand extremely high temperatures, making them suitable for high-temperature electronics.
- Low dielectric loss: Ceramic materials have low dielectric loss, minimizing signal attenuation and power dissipation at high frequencies.
- Dimensional stability: Ceramic PCBs have low thermal expansion coefficients, ensuring dimensional stability over a wide temperature range.
- High reliability: Ceramic PCBs offer high reliability and long-term stability in demanding environments.
Conclusion
Choosing the right PCB material is a critical decision that impacts the performance, reliability, and cost of your electronic project. By considering factors such as dielectric constant, dissipation factor, thermal conductivity, mechanical strength, temperature resistance, moisture resistance, and cost, you can select the most suitable material for your specific application.
FR-4 remains the go-to choice for a wide range of general-purpose applications, while high-frequency laminates cater to the demands of RF, microwave, and high-speed digital circuits. Flexible PCB materials offer mechanical flexibility and conformability, while metal-backed PCBs provide enhanced thermal management capabilities. Ceramic PCBs excel in high-temperature, high-reliability applications.
When designing with different PCB materials, it is essential to consider their unique properties and limitations. Proper design techniques, such as controlled impedance routing, thermal management, and strain relief, should be employed to ensure optimal performance and reliability.
By understanding the characteristics and applications of various PCB materials, you can make informed decisions and optimize your electronic designs. Whether you are working on consumer electronics, industrial systems, or advanced aerospace and defense projects, selecting the right PCB material is key to achieving the desired functionality, reliability, and cost-effectiveness.
No responses yet