Introduction to PCB Transmission Lines
Printed circuit boards (PCBs) are the foundation of modern electronics, providing a platform for interconnecting various components and enabling the flow of electrical signals. As the demand for high-speed and high-frequency applications grows, understanding the principles of PCB transmission lines becomes crucial for designing reliable and efficient electronic systems. In this article, we will delve into the fundamentals of PCB transmission line theory, exploring its importance, key concepts, and design considerations.
What are PCB Transmission Lines?
PCB transmission lines are the conductive paths on a printed circuit board that carry electrical signals between components. These lines are designed to transmit signals with minimal distortion, ensuring the integrity of the information being transmitted. Transmission lines can be classified into two main categories:
-
Microstrip Lines: Microstrip lines consist of a conductive trace on one side of the PCB, with a ground plane on the opposite side. The Dielectric Material of the PCB separates the trace and the ground plane.
-
Stripline: Striplines are embedded within the PCB, with conductive traces sandwiched between two ground planes. This configuration provides better shielding and reduces electromagnetic interference (EMI).
Transmission Line Type | Description |
---|---|
Microstrip | Conductive trace on one side, ground plane on opposite |
Stripline | Conductive trace embedded between two ground planes |
The Importance of Transmission Line Theory
Understanding transmission line theory is essential for several reasons:
-
Signal Integrity: Proper design of transmission lines ensures that signals maintain their shape and timing, minimizing distortion and ensuring reliable communication between components.
-
Impedance Matching: Transmission lines must be matched to the characteristic impedance of the source and load to prevent reflections and standing waves, which can degrade signal quality.
-
EMI Reduction: Well-designed transmission lines minimize electromagnetic interference, reducing the impact of noise on the system and preventing interference with other electronic devices.
-
High-Speed Applications: As the operating frequencies of electronic systems increase, the effects of transmission line phenomena become more pronounced. Understanding these principles is crucial for designing High-Speed PCBs.
Transmission Line Parameters
To effectively design and analyze PCB transmission lines, it is essential to understand the key parameters that characterize their behavior.
Characteristic Impedance
Characteristic impedance (Z0) is a fundamental property of a transmission line, representing the ratio of voltage to current for a propagating wave. It is determined by the geometry and materials of the transmission line. Matching the characteristic impedance of the transmission line to the source and load impedances minimizes reflections and ensures maximum power transfer.
The characteristic impedance of a microstrip line can be calculated using the following formula:
Z0 = (87 / √(εr + 1.41)) * ln(5.98 * h / (0.8 * w + t))
Where:
– εr is the relative permittivity of the dielectric material
– h is the thickness of the dielectric material
– w is the width of the conductive trace
– t is the thickness of the conductive trace
For striplines, the characteristic impedance is given by:
Z0 = (60 / √εr) * ln(4 * b / (0.67 * π * (0.8 * w + t)))
Where:
– b is the distance between the ground planes
Parameter | Symbol | Description |
---|---|---|
Relative Permittivity | εr | Dielectric Constant of the PCB material |
Dielectric Thickness | h | Thickness of the dielectric layer |
Trace Width | w | Width of the conductive trace |
Trace Thickness | t | Thickness of the conductive trace |
Ground Plane Spacing | b | Distance between ground planes (stripline) |
Propagation Delay
Propagation delay (tpd) is the time it takes for a signal to travel from one end of the transmission line to the other. It is determined by the dielectric constant of the PCB material and the length of the transmission line. Minimizing propagation delay is crucial for maintaining signal integrity and synchronization in high-speed systems.
The propagation delay can be calculated using the following formula:
tpd = √εr * l / c
Where:
– l is the length of the transmission line
– c is the speed of light in vacuum (approximately 3 x 10^8 m/s)
Parameter | Symbol | Description |
---|---|---|
Relative Permittivity | εr | Dielectric constant of the PCB material |
Transmission Line Length | l | Length of the transmission line |
Speed of Light | c | Speed of light in vacuum (3 x 10^8 m/s) |
Losses
Transmission lines experience losses due to various factors, including conductor losses and dielectric losses. Conductor losses are caused by the resistance of the conductive traces, while dielectric losses occur due to the dissipation of energy in the dielectric material. These losses can attenuate the signal and degrade its quality.
The attenuation constant (α) represents the losses per unit length of the transmission line and is given by:
α = (Rs / (2 * Z0)) + (G * Z0 / 2)
Where:
– Rs is the series resistance per unit length
– G is the shunt conductance per unit length
Parameter | Symbol | Description |
---|---|---|
Series Resistance | Rs | Resistance per unit length of the conductor |
Shunt Conductance | G | Conductance per unit length of the dielectric |
Characteristic Impedance | Z0 | Ratio of voltage to current for a propagating wave |
Transmission Line Design Considerations
When designing PCB transmission lines, several factors must be taken into account to ensure optimal performance and signal integrity.
Impedance Matching
Matching the impedance of the transmission line to the source and load impedances is essential to minimize reflections and ensure maximum power transfer. This is achieved by carefully selecting the trace width, dielectric thickness, and dielectric constant of the PCB material.
Common impedance values used in PCB design include:
Impedance (Ω) | Application |
---|---|
50 | RF and high-speed digital systems |
75 | Video and cable applications |
100 | Ethernet and telecommunications |
Termination Techniques
Proper termination of transmission lines is necessary to prevent reflections and maintain signal integrity. There are several termination techniques commonly used in PCB design:
-
Series Termination: A resistor is placed in series with the source, matching the impedance of the transmission line. This technique is suitable for point-to-point connections.
-
Parallel Termination: A resistor is placed in parallel with the load, matching the impedance of the transmission line. This technique is used for multi-drop buses and can be implemented at the source or load end.
-
AC Termination: A series resistor and capacitor are used to provide termination at high frequencies while allowing DC bias. This technique is commonly used in high-speed digital systems.
Termination Technique | Description |
---|---|
Series Termination | Resistor in series with the source |
Parallel Termination | Resistor in parallel with the load |
AC Termination | Series resistor and capacitor for high frequencies |
Routing Guidelines
Proper routing of transmission lines is crucial for maintaining signal integrity and minimizing crosstalk and EMI. Some key routing guidelines include:
-
Minimize Discontinuities: Avoid sharp bends, vias, and stubs in the transmission line path to minimize reflections and impedance discontinuities.
-
Maintain Constant Impedance: Keep the trace width and dielectric thickness consistent along the length of the transmission line to maintain a constant characteristic impedance.
-
Provide Adequate Spacing: Ensure sufficient spacing between transmission lines to reduce crosstalk and EMI. The spacing should be based on the operating frequency and the desired level of isolation.
-
Use Ground Planes: Incorporate ground planes in the PCB design to provide a low-impedance return path for the signals and shield the transmission lines from external noise.
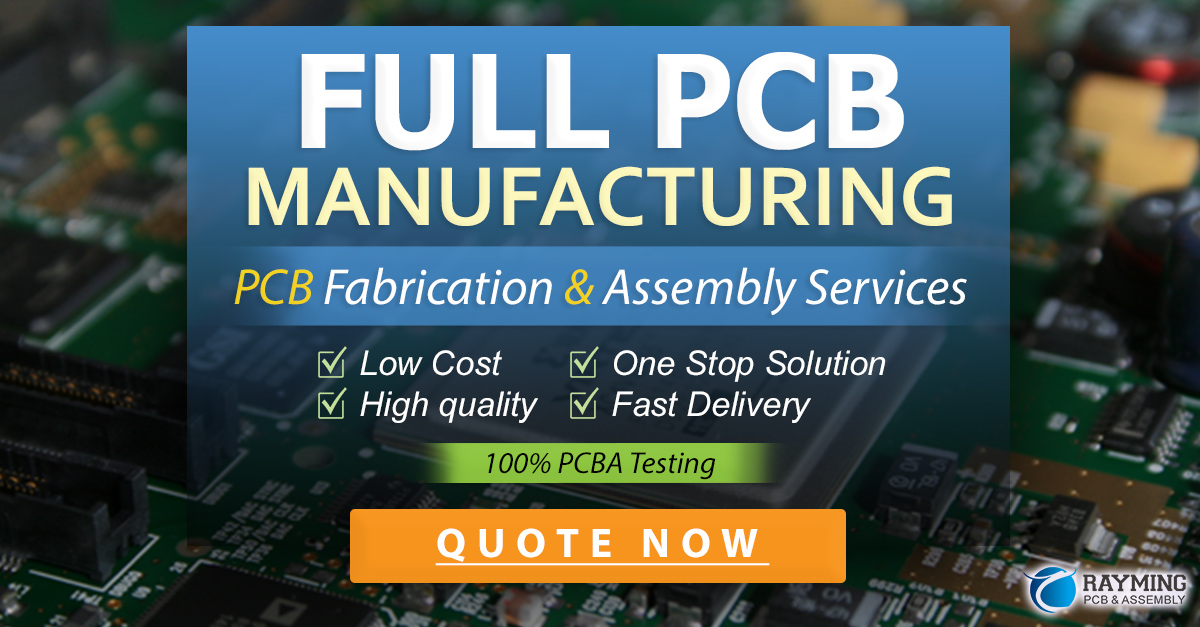
Simulation and Analysis
To optimize the design of PCB transmission lines, simulation and analysis tools are commonly used. These tools allow designers to model the behavior of transmission lines, analyze signal integrity, and identify potential issues before fabrication.
Some popular simulation and analysis tools for PCB transmission lines include:
-
SPICE: SPICE (Simulation Program with Integrated Circuit Emphasis) is a widely used circuit simulation software that can model transmission line behavior and analyze signal integrity.
-
Electromagnetic Simulators: Tools like Ansys HFSS, CST Studio Suite, and Keysight ADS provide full-wave electromagnetic simulations, allowing designers to analyze the electromagnetic fields and interactions in PCB transmission lines.
-
Time-Domain Reflectometry (TDR): TDR is a measurement technique that sends a fast-rising pulse through the transmission line and analyzes the reflected waveform to characterize impedance discontinuities and locate faults.
FAQs
Q1: What is the difference between microstrip and stripline transmission lines?
A1: Microstrip lines have a conductive trace on one side of the PCB and a ground plane on the opposite side, while striplines have conductive traces embedded between two ground planes within the PCB. Striplines provide better shielding and reduced EMI compared to microstrip lines.
Q2: Why is impedance matching important in PCB transmission line design?
A2: Impedance matching is crucial to minimize reflections and ensure maximum power transfer between the source and load. Mismatched impedances can lead to signal distortion, reduced signal integrity, and potential damage to components.
Q3: How can I calculate the characteristic impedance of a transmission line?
A3: The characteristic impedance of a transmission line can be calculated using formulas that take into account the geometry and materials of the transmission line. For microstrip lines, the formula involves the dielectric constant, trace width, trace thickness, and dielectric thickness. For striplines, the formula also includes the spacing between ground planes.
Q4: What are some common impedance values used in PCB design?
A4: Common impedance values used in PCB design include 50 Ω for RF and high-speed digital systems, 75 Ω for video and cable applications, and 100 Ω for Ethernet and telecommunications.
Q5: What are some key routing guidelines for PCB transmission lines?
A5: Some key routing guidelines for PCB transmission lines include minimizing discontinuities, maintaining constant impedance, providing adequate spacing between lines, and incorporating ground planes. These guidelines help maintain signal integrity, reduce crosstalk and EMI, and ensure optimal performance of the transmission lines.
Conclusion
Understanding the principles of PCB transmission lines is essential for designing reliable and efficient high-speed electronic systems. By considering factors such as characteristic impedance, propagation delay, losses, and proper routing techniques, designers can ensure signal integrity and minimize the impact of transmission line effects.
Through the use of simulation and analysis tools, designers can model and optimize the behavior of transmission lines, identifying potential issues before fabrication. By following best practices and staying up-to-date with the latest advancements in PCB transmission line theory, engineers can create robust and high-performance electronic systems that meet the demands of today’s applications.
No responses yet