What is PCB Testing?
PCB (Printed Circuit Board) testing is a crucial process in the manufacturing of electronic devices. It involves verifying the functionality, reliability, and performance of PCBs to ensure they meet the required specifications and standards. PCB testing helps identify defects, shorts, opens, and other issues that may affect the overall quality and performance of the final product.
PCB testing can be performed at various stages of the manufacturing process, from the initial design phase to the final assembly. It is essential to catch any issues early on to avoid costly rework and delays in production.
Types of PCB Testing
There are several types of PCB testing, each designed to identify specific issues and ensure the overall quality of the PCB. Some of the most common types of PCB testing include:
-
Visual Inspection: This is the first step in PCB testing, where the board is visually inspected for any obvious defects, such as incorrect component placement, solder bridges, or damaged traces.
-
Automated Optical Inspection (AOI): AOI uses cameras and image processing software to automatically inspect the PCB for defects, such as missing components, incorrect polarity, or solder issues.
-
In-Circuit Testing (ICT): ICT involves using a bed of nails fixture to make contact with specific points on the PCB and test the functionality of individual components and circuits.
-
Flying Probe Testing: Flying probe testing uses movable probes to make contact with specific points on the PCB and test for shorts, opens, and other issues.
-
Functional Testing: Functional testing involves testing the PCB under real-world conditions to ensure it performs as expected in the final product.
-
Boundary Scan Testing: Boundary scan testing uses a special test access port (TAP) to test the interconnections between components on the PCB.
-
Burn-In Testing: Burn-in testing involves subjecting the PCB to extreme environmental conditions, such as high temperature and humidity, to ensure it can withstand the rigors of real-world use.
Why is PCB Testing Important?
PCB testing is essential for several reasons, including:
-
Quality Assurance: PCB testing helps ensure that the final product meets the required quality standards and specifications. It helps identify any defects or issues that may affect the product’s performance, reliability, or safety.
-
Cost Savings: Catching defects early in the manufacturing process can save significant costs associated with rework, scrap, and delays in production. PCB testing helps identify issues before they become more expensive to fix.
-
Reliability: PCB testing helps ensure that the final product will perform reliably in the field. By subjecting the PCB to various tests and environmental conditions, manufacturers can identify potential failure modes and take steps to mitigate them.
-
Compliance: PCB testing helps ensure that the final product meets various regulatory and industry standards, such as UL, CE, and RoHS. This is essential for products that will be sold in different markets around the world.
Best Practices for PCB Testing
To ensure effective and efficient PCB testing, manufacturers should follow some best practices, including:
-
Early Testing: PCB testing should be performed as early as possible in the manufacturing process to catch defects before they become more expensive to fix.
-
Comprehensive Testing: PCB testing should cover all aspects of the board, including functionality, performance, and reliability. Manufacturers should use a combination of different testing methods to ensure thorough coverage.
-
Automated Testing: Automated testing methods, such as AOI and flying probe testing, can help speed up the testing process and reduce the risk of human error.
-
Proper Documentation: Manufacturers should maintain proper documentation of all testing procedures and results. This can help with troubleshooting, root cause analysis, and continuous improvement efforts.
-
Continuous Improvement: Manufacturers should continuously monitor and analyze testing results to identify areas for improvement. This can help optimize the testing process and catch defects more effectively.
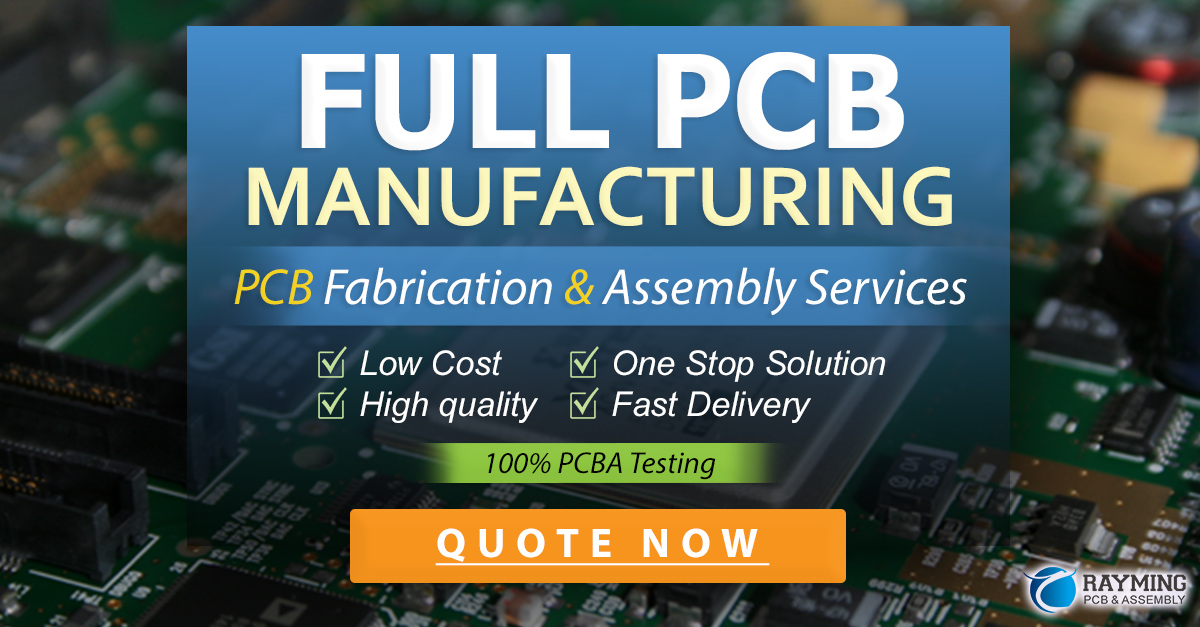
Common PCB Testing Challenges
While PCB testing is essential for ensuring the quality and reliability of electronic products, it can also present some challenges, including:
-
Complexity: As PCBs become more complex and feature-rich, testing becomes more challenging. Manufacturers need to ensure that all aspects of the board are thoroughly tested, which can be time-consuming and expensive.
-
Miniaturization: As electronic devices become smaller and more compact, PCBs are also shrinking in size. This can make it more difficult to access certain parts of the board for testing.
-
High-Speed Signals: Testing high-speed signals on PCBs can be challenging, as they are more susceptible to noise and interference. Manufacturers need to use specialized testing equipment and techniques to ensure accurate results.
-
Environmental Factors: PCBs may be subjected to various environmental factors, such as temperature, humidity, and vibration, which can affect their performance and reliability. Manufacturers need to ensure that their testing procedures account for these factors.
-
Cost: PCB testing can be expensive, especially for complex boards or high-volume production runs. Manufacturers need to balance the cost of testing with the potential cost of defects and failures in the field.
Future Trends in PCB Testing
As electronic devices continue to evolve and become more complex, PCB testing will also need to adapt to keep pace. Some of the future trends in PCB testing include:
-
Increased Automation: Automated testing methods, such as AOI and flying probe testing, will become more prevalent as manufacturers seek to reduce costs and improve efficiency.
-
Advanced Analytics: Manufacturers will increasingly use advanced analytics and machine learning techniques to analyze testing data and identify patterns and trends. This can help optimize the testing process and catch defects more effectively.
-
Industry 4.0: The rise of Industry 4.0 technologies, such as the Internet of Things (IoT) and artificial intelligence (AI), will also impact PCB testing. Manufacturers will need to ensure that their testing procedures can accommodate these new technologies.
-
Sustainability: As environmental concerns continue to grow, manufacturers will need to ensure that their PCB testing procedures are sustainable and environmentally friendly. This may involve using renewable energy sources, reducing waste, and minimizing the use of hazardous materials.
FAQs
-
What is the difference between ICT and flying probe testing?
In-circuit testing (ICT) uses a bed of nails fixture to make contact with specific points on the PCB and test the functionality of individual components and circuits. Flying probe testing, on the other hand, uses movable probes to make contact with specific points on the PCB and test for shorts, opens, and other issues. Flying probe testing is more flexible and can accommodate smaller PCBs, but it is also slower than ICT. -
How often should PCB testing be performed?
PCB testing should be performed at various stages of the manufacturing process, from the initial design phase to the final assembly. The frequency of testing will depend on the complexity of the board, the volume of production, and the potential cost of defects and failures. In general, manufacturers should aim to catch defects as early as possible to minimize costs and delays. -
What are some common defects that can be detected through PCB testing?
Some common defects that can be detected through PCB testing include shorts, opens, incorrect component placement, solder bridges, and damaged traces. Other defects may include incorrect polarity, missing components, and functionality issues. -
How can manufacturers ensure the accuracy and reliability of PCB testing results?
To ensure the accuracy and reliability of PCB testing results, manufacturers should use a combination of different testing methods, such as visual inspection, AOI, ICT, and functional testing. They should also ensure that their testing equipment is properly calibrated and maintained, and that their testing procedures are well-documented and standardized. -
What are some of the benefits of automated PCB testing methods, such as AOI and flying probe testing?
Automated PCB testing methods, such as AOI and flying probe testing, can help speed up the testing process and reduce the risk of human error. They can also accommodate smaller and more complex PCBs, and provide more consistent and repeatable results. Additionally, automated testing methods can help reduce costs associated with manual testing and rework.
PCB Testing Method | Advantages | Disadvantages |
---|---|---|
Visual Inspection | Quick and easy to perform, can catch obvious defects | Limited to visible defects, may miss internal issues |
Automated Optical Inspection (AOI) | Fast and accurate, can inspect large volumes of PCBs | Limited to surface-level defects, may require additional testing for internal issues |
In-Circuit Testing (ICT) | Can test individual components and circuits, provides detailed diagnostics | Requires custom fixtures, limited to accessible points on the PCB |
Flying Probe Testing | Flexible and can accommodate smaller PCBs, does not require custom fixtures | Slower than ICT, limited to accessible points on the PCB |
Functional Testing | Tests the PCB under real-world conditions, ensures overall functionality | May not catch all defects, requires specialized equipment and setup |
Boundary Scan Testing | Can test interconnections between components, does not require physical access to the PCB | Limited to components that support boundary scan, may not catch all defects |
Burn-In Testing | Ensures the PCB can withstand extreme environmental conditions, catches early-life failures | Time-consuming and expensive, may not catch all defects |
In conclusion, PCB testing is a critical process in the manufacturing of electronic devices. It helps ensure the quality, reliability, and performance of PCBs, and can save manufacturers significant costs associated with defects and failures. To ensure effective and efficient PCB testing, manufacturers should follow best practices such as early testing, comprehensive testing, automated testing, proper documentation, and continuous improvement.
As PCBs become more complex and feature-rich, testing will continue to evolve and adapt to new challenges and technologies. By staying up-to-date with the latest trends and best practices in PCB testing, manufacturers can ensure that their products meet the highest standards of quality and performance.
No responses yet