Introduction to QFP Solder Bridging
Quad Flat Package (QFP) is a surface-mounted integrated circuit package with leads extending from each of the four sides. QFP packages are widely used in various electronic devices due to their compact size and high pin count. However, one of the common issues faced during the soldering process of QFP packages is solder bridging.
What is Solder Bridging?
Solder bridging, also known as short circuits, occurs when excess solder accidentally connects two or more adjacent pins, creating an unintended electrical connection. This can lead to malfunctions, reduced performance, or even complete failure of the electronic device.
Causes of QFP Solder Bridging
Several factors can contribute to the occurrence of solder bridging in QFP packages:
1. Excessive Solder Paste
Applying too much solder paste during the stencil printing process can lead to excess solder on the pads. When the component is placed and the solder melts during reflow, the excess solder can flow between the pins, causing bridges.
2. Improper Stencil Design
An improperly designed stencil can result in an uneven distribution of solder paste on the pads. If the apertures are too large or the stencil thickness is incorrect, it can lead to excessive solder deposition, increasing the risk of bridging.
3. Misaligned Components
If the QFP component is not accurately placed on the pads during the pick-and-place process, it can cause misalignment. Misaligned components can result in solder bridging during reflow, as the pins may not be properly seated on the pads.
4. Inadequate Reflow Profile
An incorrect reflow profile, such as insufficient peak temperature or incorrect dwell time, can cause issues with solder melting and flow. If the solder does not melt properly or flows excessively, it can lead to bridging between the pins.
5. Contamination
Contamination on the PCB or component surfaces, such as dust, dirt, or oxidation, can interfere with proper solder wetting and flow. Contaminants can cause the solder to flow unevenly, increasing the chances of bridging.
Solutions to Prevent QFP Solder Bridging
To minimize the occurrence of solder bridging in QFP packages, several preventive measures can be implemented:
1. Stencil Optimization
Ensure that the stencil design is optimized for the specific QFP package and pad layout. The aperture sizes should be appropriate to deposit the correct amount of solder paste without excess. Additionally, consider using a stepped stencil or modifying the aperture shape to improve solder paste release and distribution.
Stencil Thickness | Aperture Size | Solder Paste Type |
---|---|---|
100µm | 80% of pad size | Type 3 |
125µm | 90% of pad size | Type 4 |
150µm | 100% of pad size | Type 5 |
Table 1: Recommended stencil parameters for QFP packages
2. Solder Paste Selection
Choose a solder paste with the appropriate particle size and flux chemistry for the QFP package. Fine-pitch QFP packages require solder pastes with smaller particle sizes to ensure even distribution and prevent bridging. Additionally, select a flux that provides good wettability and minimizes solder balling.
3. Precise Component Placement
Ensure accurate placement of the QFP component on the pads using a pick-and-place machine with high precision. Regularly calibrate the machine and use vision systems to verify the alignment before placement. Proper alignment reduces the risk of solder bridging during reflow.
4. Reflow Profile Optimization
Optimize the reflow profile for the specific QFP package and solder paste. Follow the manufacturer’s recommendations for peak temperature, dwell time, and ramp rates. A well-controlled reflow profile ensures proper solder melting and minimizes the risk of bridging.
Reflow Stage | Temperature Range | Time |
---|---|---|
Preheat | 150°C – 180°C | 60-120s |
Soak | 180°C – 200°C | 60-120s |
Reflow | 230°C – 250°C | 30-60s |
Cooling | < 100°C | 30-60s |
Table 2: Typical reflow profile parameters for lead-free solder
5. Cleaning and Contamination Control
Maintain a clean manufacturing environment to minimize contamination on the PCB and components. Regularly clean the stencils, pick-and-place nozzles, and reflow oven to prevent the buildup of contaminants. Use appropriate cleaning agents and methods to remove any residues or oxides from the surfaces.
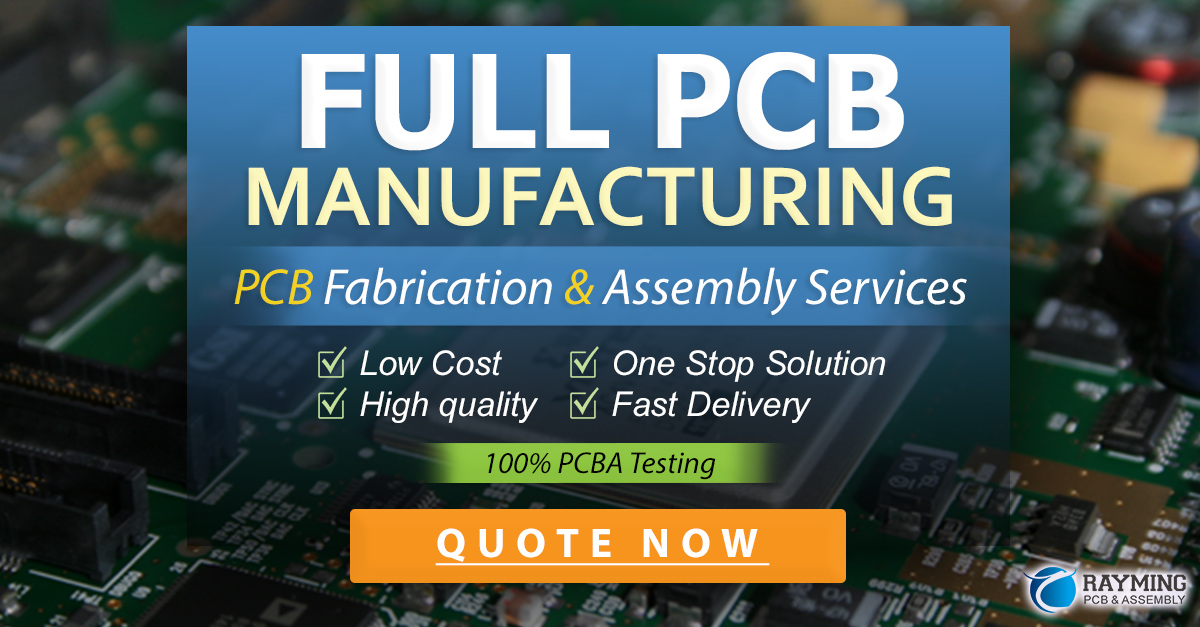
Inspection and Rework Techniques
Despite implementing preventive measures, solder bridging may still occur. In such cases, inspection and rework techniques can be employed to identify and correct the issues.
1. Visual Inspection
Perform a visual inspection of the soldered QFP package using a magnifying lens or microscope. Check for any visible solder bridges between the pins. Visual inspection can quickly identify large or obvious bridges.
2. Automated Optical Inspection (AOI)
Use AOI systems to detect solder bridging automatically. AOI systems capture high-resolution images of the soldered QFP package and compare them against predefined templates. Any deviations, such as solder bridges, are flagged for further review and rework.
3. X-ray Inspection
For QFP packages with hidden or obstructed solder joints, X-ray inspection can be used. X-ray systems provide a clear view of the solder joints beneath the component, allowing the detection of bridging that may not be visible through visual inspection.
4. Manual Rework
If solder bridging is identified, manual rework can be performed to remove the excess solder and correct the issue. Use a fine-tipped soldering iron or a desoldering tool to carefully remove the solder bridge without damaging the component or PCB pads. Exercise caution to avoid introducing new defects during the rework process.
5. Automated Rework Systems
For large-scale production or complex rework, automated rework systems can be employed. These systems use precision robotics and vision guidance to remove solder bridges and resolder the affected areas. Automated rework systems provide consistent and reliable results, reducing the risk of manual rework errors.
Frequently Asked Questions (FAQ)
-
What is the main cause of solder bridging in QFP packages?
The main cause of solder bridging in QFP packages is excessive solder paste deposition, which can occur due to improper stencil design, incorrect solder paste volume, or misaligned components during placement. -
How can I prevent solder bridging during the assembly process?
To prevent solder bridging, optimize the stencil design, select the appropriate solder paste, ensure precise component placement, and control the reflow profile. Additionally, maintain a clean manufacturing environment to minimize contamination. -
What are the consequences of solder bridging in QFP packages?
Solder bridging in QFP packages can lead to short circuits, causing malfunctions, reduced performance, or complete failure of the electronic device. It can also impact the reliability and longevity of the product. -
How can I detect solder bridging in QFP packages?
Solder bridging in QFP packages can be detected through visual inspection using magnification, automated optical inspection (AOI) systems, or X-ray inspection for hidden or obstructed solder joints. -
What should I do if I discover solder bridging in a QFP package?
If solder bridging is discovered, careful manual rework using a fine-tipped soldering iron or desoldering tool can be performed to remove the excess solder. For large-scale production or complex rework, automated rework systems can be employed to ensure consistent and reliable results.
Conclusion
Solder bridging is a common issue encountered during the assembly of QFP packages. Understanding the causes and implementing preventive measures can significantly reduce the occurrence of solder bridging. By optimizing the stencil design, selecting the appropriate solder paste, ensuring precise component placement, controlling the reflow profile, and maintaining a clean manufacturing environment, the risk of solder bridging can be minimized.
However, if solder bridging still occurs, effective inspection techniques such as visual inspection, AOI, and X-ray inspection can help identify the issues. Manual rework or automated rework systems can then be employed to correct the solder bridges and ensure the reliability and functionality of the electronic device.
By following best practices and implementing a comprehensive approach to prevent and address solder bridging, manufacturers can improve the quality and yield of their QFP assembly process, ultimately leading to more reliable and robust electronic products.
No responses yet