What are HDI PCBs?
HDI (High Density Interconnector) PCBs are printed circuit boards that feature higher wiring density per unit area compared to conventional PCBs. This is achieved through the use of smaller vias, finer trace widths and spaces, and more advanced manufacturing techniques. HDI PCBs allow for the miniaturization of electronic devices while maintaining or even improving their performance.
Key Features of HDI PCBs
- Smaller vias (micro vias and buried vias)
- Finer trace widths and spaces
- Higher layer counts
- Advanced manufacturing processes (sequential lamination, laser drilling, etc.)
Benefits of Using HDI PCBs
Miniaturization
One of the primary benefits of HDI PCBs is their ability to enable the miniaturization of electronic devices. By utilizing smaller components and denser wiring, designers can create more compact and lightweight products without sacrificing functionality.
Improved Performance
HDI PCBs offer improved electrical performance compared to traditional PCBs. The shorter signal paths and reduced layer counts result in lower signal loss, reduced crosstalk, and better overall signal integrity. This is particularly important for high-speed applications, such as 5G wireless communication and high-performance computing.
Cost Reduction
Although the initial Manufacturing costs of HDI PCBs may be higher than those of conventional PCBs, the overall cost of the final product can be reduced. This is because HDI PCBs enable the use of fewer components, smaller form factors, and simplified assembly processes. Additionally, the improved reliability and performance of HDI PCBs can lead to reduced maintenance and replacement costs over the product’s lifecycle.
HDI PCB Manufacturing Processes
Sequential Lamination
Sequential lamination is a key process in the fabrication of HDI PCBs. This technique involves building up the PCB Layer by layer, allowing for the creation of micro vias and buried vias. The process begins with the lamination of a core layer, followed by the drilling and plating of vias. Additional layers are then added, and the process is repeated until the desired layer count is achieved.
Laser Drilling
Laser drilling is used to create the micro vias in HDI PCBs. This process offers several advantages over traditional mechanical drilling, including higher precision, smaller via diameters, and the ability to create blind and buried vias. Laser drilling also enables the creation of via-in-pad structures, which further increases the wiring density of the PCB.
Plasma Etching
Plasma etching is a process used to remove unwanted copper from the PCB surface, creating the desired trace patterns. This technique offers higher precision and finer feature sizes compared to traditional chemical etching methods. Plasma etching is particularly useful for creating the fine trace widths and spaces required in HDI PCBs.
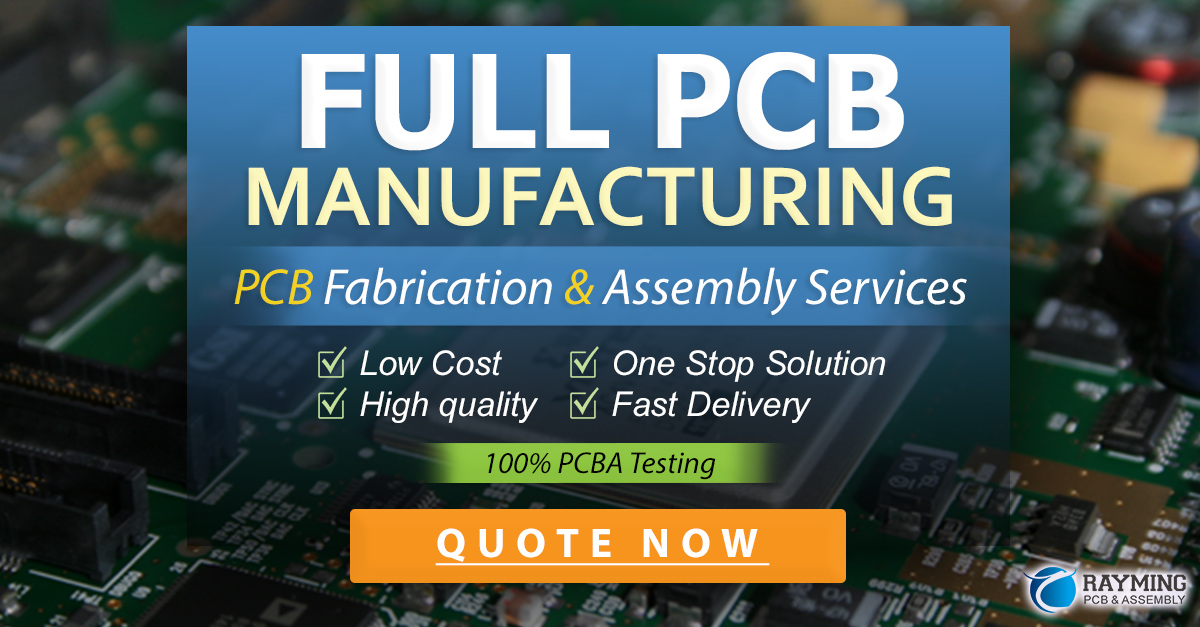
HDI PCB Design Considerations
When designing HDI PCBs, several factors must be taken into account to ensure optimal performance and manufacturability.
Signal Integrity
Signal integrity is a critical consideration in HDI PCB design. Designers must carefully manage impedance, crosstalk, and signal loss to ensure reliable high-speed performance. This can be achieved through proper trace routing, via placement, and the use of appropriate materials and manufacturing techniques.
Thermal Management
HDI PCBs often feature higher power densities compared to traditional PCBs, which can lead to increased heat generation. Effective thermal management is essential to ensure the reliability and longevity of the final product. Designers can incorporate thermal vias, heat sinks, and other cooling solutions to dissipate heat effectively.
Manufacturing Constraints
HDI PCBs require advanced manufacturing capabilities, and designers must be aware of the limitations and constraints of the chosen fabrication process. This includes minimum via sizes, trace widths and spaces, and layer count limitations. Close collaboration between the design and manufacturing teams is essential to ensure the successful realization of the HDI PCB.
RAYPCB’s HDI PCB Solutions
RAYPCB is a leading provider of high-quality HDI PCB solutions. With state-of-the-art manufacturing facilities and a team of experienced engineers, RAYPCB offers a range of HDI PCB services to meet the diverse needs of its customers.
HDI PCB Capabilities
Feature | Capability |
---|---|
Minimum Via Diameter | 0.1mm |
Minimum Trace Width/Space | 0.075mm |
Maximum Layer Count | 20+ |
RAYPCB’s advanced HDI PCB capabilities enable the fabrication of highly complex and dense PCBs for a wide range of applications, including:
- 5G wireless communication
- High-performance computing
- Automotive electronics
- Medical devices
- Aerospace and defense systems
Quality Assurance
RAYPCB is committed to providing its customers with the highest quality HDI PCBs. The company employs a rigorous quality assurance process, which includes:
- Automated optical inspection (AOI)
- X-ray inspection
- Electrical testing
- Visual inspection
This multi-stage quality control process ensures that every HDI PCB meets or exceeds the specified requirements for performance, reliability, and durability.
Customer Support
RAYPCB understands the importance of timely and effective customer support. The company’s dedicated team of sales representatives and technical experts is available to assist customers throughout the entire HDI PCB design and manufacturing process. From initial concept development to final product delivery, RAYPCB is committed to providing its customers with the support they need to succeed.
Frequently Asked Questions (FAQ)
- What is the minimum via size that can be achieved with HDI PCBs?
-
RAYPCB’s HDI PCB capabilities allow for a minimum via diameter of 0.1mm.
-
How many layers can an HDI PCB have?
-
RAYPCB can fabricate HDI PCBs with 20 or more layers, depending on the specific requirements of the project.
-
What are the advantages of using HDI PCBs compared to traditional PCBs?
-
HDI PCBs offer several advantages, including miniaturization, improved electrical performance, and reduced overall product costs.
-
What industries commonly use HDI PCBs?
-
HDI PCBs are used in a wide range of industries, including telecommunications, computing, automotive, medical, aerospace, and defense.
-
How does RAYPCB ensure the quality of its HDI PCBs?
- RAYPCB employs a comprehensive quality assurance process that includes automated optical inspection, X-ray inspection, electrical testing, and visual inspection to ensure the highest quality HDI PCBs for its customers.
In conclusion, HDI PCBs offer a powerful solution for the miniaturization and performance enhancement of modern electronic devices. With its advanced manufacturing capabilities and commitment to quality and customer support, RAYPCB is well-positioned to meet the growing demand for HDI PCBs across a wide range of industries. As technology continues to evolve, HDI PCBs will play an increasingly important role in enabling the next generation of electronic innovations.
No responses yet