Introduction to PCB Assembly and FIA
Printed Circuit Board (PCB) assembly is a crucial process in the manufacturing of electronic devices. It involves the placement and soldering of electronic components onto a PCB, which serves as the foundation for the device’s functionality. To ensure the quality and reliability of the assembLED PCBs, a First Article Inspection (FIA) is conducted. In this article, we will delve into the PCB assembly process and the importance of FIA, with a focus on the services provided by RAYPCB.
The PCB Assembly Process
Step 1: Solder Paste Application
The first step in the PCB assembly process is the application of solder paste onto the PCB. Solder paste is a mixture of tiny solder particles suspended in a flux medium. It is applied to the PCB using a stencil or screen printing technique, ensuring that the paste is deposited precisely on the designated pads where the components will be placed.
Step 2: Component Placement
Once the solder paste is applied, the next step is to place the electronic components onto the PCB. This is typically done using a pick-and-place machine, which accurately positions the components based on the design specifications. The machine uses a vacuum nozzle to pick up the components from a feeder and place them onto the PCB with high precision.
Step 3: Reflow Soldering
After the components are placed, the PCB undergoes a reflow soldering process. The PCB is passed through a reflow oven, which heats the board to a specific temperature profile. The heat causes the solder paste to melt and form a strong electrical and mechanical connection between the components and the PCB pads. The reflow soldering process is carefully controlled to ensure proper solder joint formation and to prevent any damage to the components.
Step 4: Inspection and Testing
Once the PCB has cooled down after the reflow soldering process, it undergoes inspection and testing. This is where the First Article Inspection (FIA) comes into play. FIA is a comprehensive inspection process that verifies the quality and conformity of the assembled PCB against the design specifications and industry standards.
First Article Inspection (FIA) by RAYPCB
RAYPCB, a leading PCB manufacturing and assembly service provider, offers comprehensive FIA services to ensure the highest quality of assembled PCBs. Let’s explore the various aspects of FIA conducted by RAYPCB.
Visual Inspection
The first step in FIA is a thorough visual inspection of the assembled PCB. Trained inspectors examine the board for any visible defects, such as incorrect component placement, solder bridges, or missing components. They also check for any signs of damage or contamination on the PCB surface.
Automated Optical Inspection (AOI)
In addition to visual inspection, RAYPCB utilizes Automated Optical Inspection (AOI) systems to detect any manufacturing defects. AOI systems use high-resolution cameras and advanced image processing algorithms to scan the PCB and identify any anomalies or deviations from the design specifications. This automated inspection process ensures a high level of accuracy and consistency in detecting defects.
X-Ray Inspection
For complex PCBs with high-density component placement or hidden solder joints, RAYPCB employs X-ray inspection techniques. X-ray inspection allows for a non-destructive examination of the internal structure of the PCB, revealing any hidden defects or voids in the solder joints. This is particularly important for BGAs (Ball Grid Arrays) and other components with hidden connections.
Electrical Testing
Electrical testing is a crucial part of FIA to verify the functionality and performance of the assembled PCB. RAYPCB conducts various electrical tests, including:
- Continuity Test: Verifies that all the connections on the PCB are intact and there are no open circuits.
- Insulation Resistance Test: Measures the resistance between different conductors on the PCB to ensure proper insulation.
- Functional Test: Checks the PCB’s functionality by applying input signals and measuring the output response.
These electrical tests help identify any shorts, opens, or other functional issues that may impact the PCB’s performance.
Dimensional Verification
RAYPCB also verifies the dimensional accuracy of the assembled PCB. Using precision measurement tools, they check the PCB dimensions, hole sizes, and component placement against the design specifications. This ensures that the PCB meets the required mechanical tolerances and fits properly into the intended enclosure or assembly.
Documentation and Reporting
Throughout the FIA process, RAYPCB maintains detailed documentation and generates comprehensive inspection reports. These reports include:
- Inspection checklist
- Defect summary
- Measurement data
- Test results
- Corrective actions (if required)
The FIA report serves as a record of the inspection process and provides valuable information for quality control and traceability purposes.
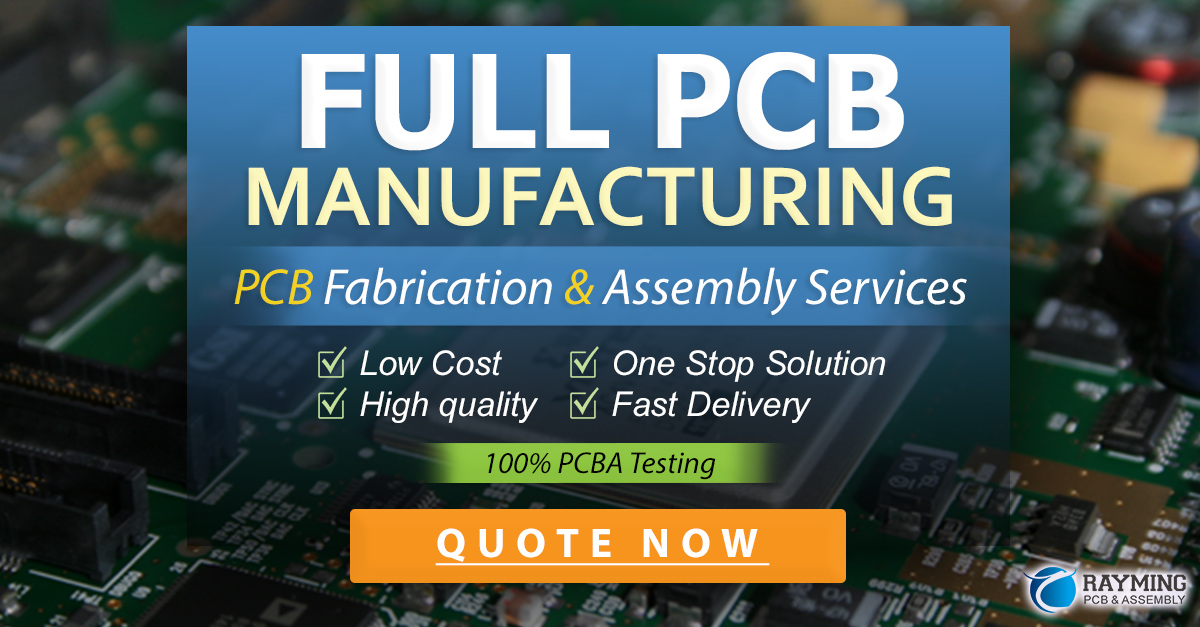
Benefits of FIA by RAYPCB
Conducting a thorough FIA offers several benefits to both the PCB manufacturer and the end customer. Some of the key benefits include:
-
Quality Assurance: FIA ensures that the assembled PCBs meet the highest quality standards and are free from defects. It helps identify and rectify any issues early in the manufacturing process, preventing potential failures or reliability problems down the line.
-
Cost Savings: By detecting defects early through FIA, costly rework or scrap can be avoided. It is much more cost-effective to identify and correct issues during the inspection stage rather than discovering them later in the production process or after the product has been shipped to the customer.
-
Improved Reliability: FIA contributes to the overall reliability of the assembled PCBs. By verifying the quality and conformity of the PCBs, the risk of field failures or product returns is minimized. This enhances customer satisfaction and builds trust in the manufacturer’s capabilities.
-
Regulatory Compliance: Many industries have specific quality and reliability standards that PCBs must adhere to. FIA helps ensure compliance with these standards, such as IPC (Association Connecting Electronics Industries) standards, by verifying that the PCBs meet the required specifications and tolerances.
-
Documentation and Traceability: The detailed documentation generated during FIA provides a comprehensive record of the inspection process. This documentation can be used for quality control, auditing, and traceability purposes. In case of any issues or customer inquiries, the FIA report serves as a valuable reference point.
Conclusion
The PCB assembly process and First Article Inspection (FIA) are critical elements in ensuring the quality, reliability, and functionality of electronic devices. RAYPCB, as a trusted PCB manufacturing and assembly service provider, offers comprehensive FIA services to meet the highest industry standards.
By conducting thorough visual inspections, utilizing automated optical inspection systems, employing X-ray inspection techniques, performing electrical testing, and verifying dimensional accuracy, RAYPCB ensures that the assembled PCBs meet the design specifications and exceed customer expectations.
Investing in FIA not only guarantees the quality of the PCBs but also provides cost savings, improves reliability, ensures regulatory compliance, and enhances documentation and traceability. With RAYPCB’s expertise and commitment to quality, customers can have confidence in the assembled PCBs they receive.
Frequently Asked Questions (FAQ)
1. What is the purpose of First Article Inspection (FIA) in PCB assembly?
First Article Inspection (FIA) is a comprehensive inspection process that verifies the quality and conformity of the assembled PCB against the design specifications and industry standards. It ensures that the PCB is free from defects, meets the required dimensions, and functions as intended.
2. What are the different inspection techniques used in FIA?
FIA typically involves various inspection techniques, including:
– Visual inspection: Manual examination of the PCB for visible defects.
– Automated Optical Inspection (AOI): Using high-resolution cameras and image processing algorithms to detect manufacturing defects.
– X-ray inspection: Non-destructive examination of the internal structure of the PCB to identify hidden defects or voids.
– Electrical testing: Verifying the functionality and performance of the PCB through continuity tests, insulation resistance tests, and functional tests.
– Dimensional verification: Checking the PCB dimensions, hole sizes, and component placement against the design specifications.
3. What are the benefits of conducting FIA in PCB assembly?
Conducting FIA offers several benefits, including:
– Quality assurance: Ensuring that the assembled PCBs meet the highest quality standards.
– Cost savings: Identifying and rectifying defects early in the manufacturing process to avoid costly rework or scrap.
– Improved reliability: Minimizing the risk of field failures or product returns.
– Regulatory compliance: Verifying compliance with industry standards and regulations.
– Documentation and traceability: Providing a comprehensive record of the inspection process for quality control and auditing purposes.
4. How does RAYPCB ensure the quality of assembled PCBs through FIA?
RAYPCB conducts a thorough FIA process that includes visual inspection, automated optical inspection, X-ray inspection, electrical testing, and dimensional verification. They employ trained inspectors and use advanced inspection systems to detect any defects or deviations from the design specifications. RAYPCB also maintains detailed documentation and generates comprehensive inspection reports for quality control and traceability purposes.
5. What industries require FIA for PCB assembly?
FIA is commonly required in industries that have stringent quality and reliability standards for electronic devices. These industries include:
– Aerospace and defense
– Medical devices
– Automotive
– Industrial equipment
– Telecommunications
– Consumer electronics
Conducting FIA is essential to meet the specific quality and regulatory requirements of these industries and ensure the reliable functioning of the assembled PCBs.
Inspection Technique | Purpose | Benefits |
---|---|---|
Visual Inspection | Manual examination for visible defects | Identifies surface-level defects and workmanship issues |
Automated Optical Inspection (AOI) | Detects manufacturing defects using cameras and image processing | High accuracy, consistency, and speed in defect detection |
X-Ray Inspection | Non-destructive examination of internal PCB structure | Identifies hidden defects, voids, and solder joint issues |
Electrical Testing | Verifies functionality and performance of the PCB | Ensures proper electrical connections and circuit operation |
Dimensional Verification | Checks PCB dimensions, hole sizes, and component placement | Confirms compliance with mechanical tolerances and design specifications |
By incorporating these inspection techniques into the FIA process, RAYPCB ensures the highest quality and reliability of the assembled PCBs, meeting the demands of various industries and customer requirements.
No responses yet