Introduction to Printed and Flexible Electronics
Printed and flexible electronics represent an exciting new frontier in electronics technology. Unlike traditional rigid electronics based on silicon wafers and printed circuit boards, printed and flexible electronics utilize novel materials like conductive inks, polymers, and thin films to create electronic devices and circuits that are lightweight, low-cost, and can conform to various shapes and surfaces. This emerging field promises to revolutionize the electronics industry with innovative applications in consumer electronics, healthcare, energy, automotive, and beyond.
Key Technologies Enabling Printed and Flexible Electronics
Several key technologies are driving the development and commercialization of printed and flexible electronics:
Conductive Inks and Pastes
Conductive inks and pastes form the core building blocks of printed electronics. These materials typically contain metal nanoparticles (silver, copper, gold) or conductive polymers dispersed in a liquid vehicle. When printed onto a substrate and cured, they form conductive traces and interconnects. Advances in ink formulation have improved conductivity, printability, and adhesion to enable high-performance printed circuits.
Flexible Substrates
Unlike rigid PCBs, printed electronics require flexible substrates that can bend, stretch, and conform to surfaces. Polymer films like PET and PEN are commonly used due to their flexibility, transparency, and compatibility with roll-to-roll printing processes. Researchers are also exploring novel substrates like paper, textiles, and stretchable elastomers to enable new form factors and functionalities.
Printing Technologies
Various printing methods are used to deposit functional inks onto flexible substrates:
– Screen Printing: A mesh stencil is used to transfer ink onto the substrate. Suitable for thick film deposition.
– Inkjet Printing: Digitally controlled nozzles spray droplets of ink onto the substrate. Enables high-resolution patterning.
– Gravure Printing: Ink is transferred from engraved cells on a rotating cylinder onto the substrate. High-throughput roll-to-roll process.
– Flexographic Printing: Raised patterns on a flexible plate transfer ink onto the substrate. Another roll-to-roll compatible method.
Advances in printing equipment, resolution, and registration are enabling the scalable manufacturing of complex printed electronic devices.
Thin Film Transistors
Thin film transistors (TFTs) are the workhorse devices in printed and flexible electronics. Unlike conventional silicon MOSFETs, TFTs are fabricated using amorphous or polycrystalline semiconductor materials like amorphous silicon, metal oxides, and organic semiconductors. These materials can be deposited and patterned at low temperatures compatible with plastic substrates. Printed TFTs are the key components enabling active-matrix displays, logic circuits, and sensors.
Applications of Printed and Flexible Electronics
Printed and flexible electronics are enabling a wide range of applications across industries:
Flexible Displays
One of the most prominent applications is in flexible displays. Printed OLED and LCD displays on plastic substrates are being integrated into smartphones, smartwatches, and TVs. These displays offer lighter weight, thinner form factors, and greater design freedom compared to rigid glass displays. They also enable new use cases like rollable and foldable displays.
Wearable Electronics
Printed electronics are ideally suited for wearable devices that require conformability to the human body. Printed sensors, antennas, and interconnects can be integrated directly into textiles and garments. Applications include smart clothing for health monitoring, fitness tracking, and fashion. Printed electronics also enable skin-mounted patches for medical sensing and drug delivery.
Healthcare and Medical Devices
Printed and flexible electronics are revolutionizing healthcare with low-cost, disposable diagnostic devices. Printed biosensors can detect biomarkers, electrolytes, and pathogens from body fluids. Lab-on-a-chip devices integrate sample preparation, sensing, and microfluidics in a thin, flexible format. Printed smart bandages can monitor wound healing. Implantable devices like retinal implants and neural probes also benefit from the flexible form factors enabled by printed electronics.
Energy Harvesting and Storage
Printed electronics are enabling flexible, large-area energy devices. Printed solar cells on plastic films can be integrated into buildings, vehicles, and consumer devices to harvest renewable energy. Printed batteries and supercapacitors provide thin, flexible energy storage solutions. Thermoelectric generators and piezoelectric nanogenerators can also be printed to harvest energy from body heat and motion.
Smart Packaging and Labels
Printed electronics are being integrated into product packaging and labels to enable intelligent functions. Printed RFID tags enable wireless tracking and authentication of goods. Printed sensors can monitor product quality, freshness, and tampering. Interactive packaging with printed displays and touch sensors enhances customer engagement. Smart labels with printed memory can store product information and operational history.
Automotive and Transportation
Printed electronics are finding applications in the automotive industry for lightweight, space-saving solutions. Printed sensors and heaters can be integrated into car seats and interiors for occupant detection, climate control, and styling. Printed antennas and EMI shielding enable in-vehicle connectivity and infotainment. Flexible lighting solutions enhance safety and aesthetics.
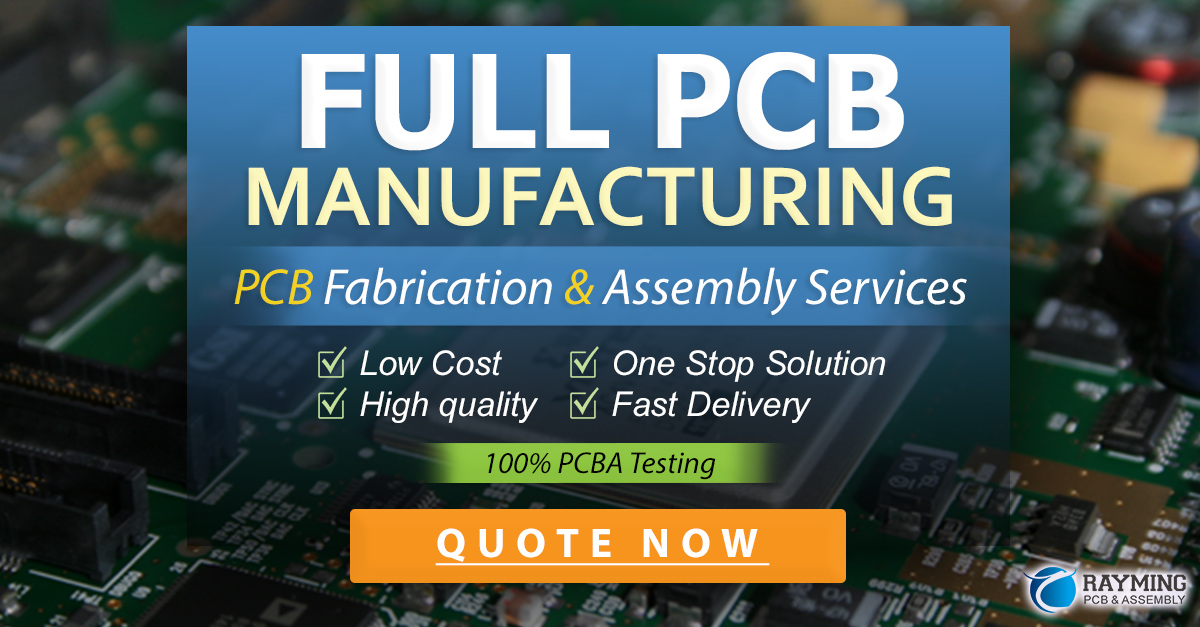
Challenges and Future Outlook
Despite the promising potential of printed and flexible electronics, several challenges remain:
-
Material Performance: Printed materials often have lower electrical performance compared to conventional electronics. Improving the conductivity, mobility, and stability of inks and semiconductors is an active area of research.
-
Manufacturing Scalability: Transitioning from lab-scale printing to high-volume manufacturing requires overcoming issues with process variability, yield, and reliability. Standardization of materials, processes, and testing methods is crucial.
-
System Integration: Integrating printed electronics with conventional silicon ICs and components poses challenges in interconnection, packaging, and reliability. Hybrid integration approaches need to be developed.
-
Cost Competitiveness: While printed electronics offer potential cost savings, the economies of scale and performance-cost trade-offs need to be carefully evaluated against conventional electronics for each application.
Despite these challenges, the future outlook for printed and flexible electronics remains bright. Market analysts predict significant growth in the coming years, driven by the increasing adoption of smart wearables, IoT devices, and intelligent packaging. Continued research and development in materials, printing processes, and device designs will unlock new possibilities and applications.
In conclusion, printed and flexible electronics represent a disruptive technology that is poised to transform the electronics industry. With their unique attributes of flexibility, low cost, and large-area scalability, printed electronics enable a wide range of innovative applications that were previously impossible with conventional rigid electronics. As the technology matures and overcomes current challenges, we can expect to see printed and flexible electronics become an integral part of our daily lives, from smart clothing and medical devices to sustainable energy solutions and intelligent environments.
Frequently Asked Questions (FAQ)
- What are the key benefits of printed and flexible electronics compared to conventional electronics?
Printed and flexible electronics offer several advantages over conventional rigid electronics:
– Flexibility and conformability: Printed electronics can bend, stretch, and conform to curved surfaces, enabling integration into wearables, clothing, and non-flat objects.
– Lightweight and thin form factors: By using thin plastic substrates and printed materials, flexible electronics can be made much thinner and lighter than rigid PCBs and components.
– Lower cost and scalability: Printing processes like roll-to-roll printing enable high-throughput, low-cost manufacturing of electronics over large areas, reducing the cost per unit area compared to silicon wafer processing.
– Design freedom: Printed electronics allow for new form factors, shapes, and sizes that are not possible with rigid electronics, enabling greater design flexibility and customization.
- What are some of the key challenges facing the adoption of printed and flexible electronics?
While printed and flexible electronics offer many advantages, there are still several challenges to overcome:
– Lower performance: Printed materials and devices often have lower electrical performance (conductivity, mobility, stability) compared to single-crystal silicon and other conventional electronic materials.
– Manufacturing scalability: Transitioning from lab-scale printing to high-volume manufacturing requires overcoming issues with process variability, yield, and reliability.
– Integration with conventional electronics: Integrating printed electronics with silicon ICs and other conventional components poses challenges in interconnection, packaging, and reliability.
– Cost competitiveness: The cost-performance trade-offs of printed electronics need to be carefully evaluated against conventional solutions for each specific application.
- What are some of the most promising application areas for printed and flexible electronics?
Printed and flexible electronics are enabling innovative applications across several industries:
– Wearables and smart clothing: Printed sensors, antennas, and circuits can be integrated into textiles and garments for health monitoring, fitness tracking, and fashion.
– Healthcare and medical devices: Printed biosensors, lab-on-a-chip devices, and smart bandages enable low-cost, disposable diagnostics and monitoring solutions.
– Flexible displays: Printed OLED and LCD displays on plastic substrates are being used in smartphones, smartwatches, and TVs, offering thinner, lighter, and more flexible form factors.
– Smart packaging and labels: Printed electronics can be integrated into product packaging and labels for intelligent functions like wireless tracking, quality monitoring, and customer interaction.
– Energy harvesting and storage: Printed solar cells, batteries, and thermoelectric generators enable flexible, large-area energy solutions.
- What are some of the key materials used in printed and flexible electronics?
Several materials are commonly used in printed and flexible electronics:
– Conductive inks and pastes: These contain metal nanoparticles (silver, copper, gold) or conductive polymers dispersed in a liquid vehicle, and form conductive traces when printed and cured.
– Flexible substrates: Polymer films like PET and PEN are commonly used as substrates for their flexibility, transparency, and compatibility with printing processes. Paper, textiles, and stretchable elastomers are also being explored.
– Semiconductors: Amorphous silicon, metal oxides, and organic semiconductors are used to fabricate thin film transistors (TFTs) for active devices like displays and sensors.
– Dielectrics and encapsulants: Insulating polymers and inorganic materials are used as dielectric layers, barriers, and encapsulants to protect devices from the environment.
- What is the future outlook for printed and flexible electronics?
The future of printed and flexible electronics looks bright, with significant growth expected in the coming years. Market analysts predict the global market for printed and flexible electronics to reach tens of billions of dollars by 2030, driven by the increasing adoption of IoT devices, smart wearables, and intelligent packaging.
Continued research and development in materials, printing processes, and device designs will unlock new possibilities and applications. As the technology matures and overcomes current challenges, printed and flexible electronics are poised to become an integral part of our daily lives, transforming industries from healthcare and consumer electronics to automotive and energy.
In the longer term, the convergence of printed electronics with other emerging technologies like 5G, AI, and robotics will enable even more disruptive innovations. We can envision a future where printed electronics are ubiquitous, from smart clothing that adapts to our needs, to flexible solar cells that power our homes and vehicles, to intelligent environments that sense and respond to our presence.
However, realizing this vision will require collaboration across the value chain, from material suppliers and equipment manufacturers to designers and end-users. Standardization, education, and innovation ecosystems will be key to accelerating the adoption and commercialization of printed and flexible electronics.
In conclusion, printed and flexible electronics represent a game-changing technology that has the potential to revolutionize the way we design, manufacture, and use electronic devices. With their unique attributes and diverse applications, printed electronics are set to shape the future of electronics and enable a smarter, more sustainable, and more connected world.
No responses yet