Understanding FR4 and Its Yellowing Phenomenon
What is FR4?
FR4 (Flame Retardant 4) is a widely used material for manufacturing printed circuit boards (PCBs). It is a composite material made of woven fiberglass cloth with an epoxy resin binder. The “FR” in FR4 stands for “Flame Retardant,” indicating its ability to self-extinguish and resist the spread of flames in case of a fire.
FR4 is known for its excellent mechanical, electrical, and thermal properties, making it an ideal choice for PCBs in various applications, including:
- Consumer electronics
- Automotive industry
- Aerospace and defense
- Medical devices
- Telecommunications
Composition and Manufacturing Process of FR4
FR4 is composed of two main components:
- Woven fiberglass cloth: This provides the structural reinforcement and dimensional stability to the material.
- Epoxy resin: The resin acts as a binder, holding the fiberglass cloth together and providing insulation and protection.
The manufacturing process of FR4 involves several steps:
- Impregnation: The fiberglass cloth is impregnated with the epoxy resin.
- Drying: The impregnated cloth is dried to remove any excess resin and moisture.
- Layering: Multiple layers of the impregnated cloth are stacked together to achieve the desired thickness.
- Pressing: The stacked layers are pressed under high temperature and pressure to cure the epoxy resin and form a solid laminate.
- Cutting: The cured laminate is cut to the desired size and shape for PCB fabrication.
Properties of FR4
FR4 exhibits several desirable properties that make it suitable for PCB Applications:
Property | Description |
---|---|
Mechanical Strength | High tensile and flexural strength, providing durability and resistance to stress |
Electrical Insulation | Excellent dielectric properties, preventing electrical leakage and short circuits |
Thermal stability | Able to withstand high temperatures during soldering and operation |
Flame Retardancy | Self-extinguishing properties, reducing the risk of fire spread |
Moisture Resistance | Low moisture absorption, maintaining its properties in humid environments |
Yellowing of FR4
One of the challenges associated with FR4 is its tendency to yellow over time. This yellowing phenomenon can be attributed to several factors:
- Exposure to UV light: Prolonged exposure to ultraviolet (UV) light can cause the epoxy resin in FR4 to degrade and yellow.
- Thermal aging: High temperatures during manufacturing or operation can accelerate the yellowing process.
- Chemical exposure: Exposure to certain chemicals, such as acids or alkaline solutions, can lead to discoloration.
While yellowing does not necessarily affect the electrical or mechanical properties of FR4, it can be a cosmetic concern for some applications, particularly in consumer electronics where aesthetics are important.
Strategies to Minimize FR4 yellowing
UV Stabilizers and Additives
One approach to reduce FR4 yellowing is the use of UV stabilizers and additives in the epoxy resin formulation. These additives help absorb and dissipate UV radiation, protecting the material from degradation. Some commonly used UV stabilizers include:
- Hindered Amine Light Stabilizers (HALS)
- Benzotriazoles
- Benzophenones
- Triazines
The selection and concentration of UV stabilizers depend on the specific requirements of the application and the expected level of UV exposure.
Alternative Resin Systems
Another strategy to mitigate FR4 yellowing is the use of alternative resin systems that are less prone to discoloration. Some examples include:
- Halogen-free epoxy resins: These resins are formulated without halogenated flame retardants, which can contribute to yellowing.
- High-temperature epoxy resins: These resins are designed to withstand higher temperatures, reducing the risk of thermal aging and yellowing.
- Polyimide resins: Polyimide-based laminates offer excellent thermal stability and resistance to yellowing, making them suitable for high-temperature applications.
However, it is important to note that alternative resin systems may have different properties and processing requirements compared to traditional FR4, and their suitability for a specific application should be carefully evaluated.
Protective Coatings and Finishes
Applying protective coatings or finishes to the surface of FR4 can help prevent yellowing by shielding the material from UV light and environmental factors. Some common coating options include:
- Conformal coatings: These thin, protective layers can be applied to the PCB surface to provide protection against moisture, dust, and UV radiation. Common conformal coating materials include acrylic, silicone, and polyurethane.
- Solder mask: The solder mask layer on a PCB not only provides insulation and protection for the copper traces but also helps shield the underlying FR4 from UV exposure.
- UV-resistant inks and labels: Using UV-resistant inks and labels for marking and labeling PCBs can help prevent discoloration and maintain the aesthetic appeal of the product.
Design Considerations
In addition to material selection and protective measures, design considerations can also play a role in minimizing FR4 yellowing:
- Minimize UV exposure: When possible, design enclosures or housings that shield the PCB from direct sunlight and UV radiation.
- Optimize thermal management: Proper thermal management, such as the use of heat sinks and ventilation, can help reduce the operating temperature of the PCB and slow down thermal aging.
- Consider alternative materials: In applications where yellowing is a critical concern, consider using alternative substrate materials, such as ceramic or Metal-Core PCBs, which are less susceptible to discoloration.
Case Studies and Examples
Consumer Electronics: Smartphone PCBs
In the highly competitive smartphone market, aesthetic appeal is a key differentiator. Yellowing of the PCB can be a significant concern, as it may be visible through transparent or translucent phone casings. To address this issue, smartphone manufacturers often employ a combination of strategies:
- Using halogen-free, low-yellowing FR4 laminates
- Applying UV-resistant conformal coatings or solder masks
- Designing phone casings that minimize UV exposure to the PCB
Automotive Electronics: Under-Hood Applications
PCBs used in under-hood automotive applications are subjected to high temperatures and harsh environmental conditions. Yellowing of FR4 in these applications is primarily driven by thermal aging. To mitigate this issue, automotive PCB manufacturers may:
- Use high-temperature epoxy resins or polyimide-based laminates
- Implement robust thermal management solutions
- Employ conformal coatings to protect against moisture and contaminants
Industrial Electronics: Outdoor Signage
Outdoor electronic signage, such as digital billboards and information displays, are exposed to direct sunlight and UV radiation for extended periods. To prevent yellowing and maintain readability, PCB designers in this field may consider:
- Selecting UV-stabilized FR4 laminates
- Applying UV-resistant conformal coatings or solder masks
- Designing enclosures with UV-blocking properties
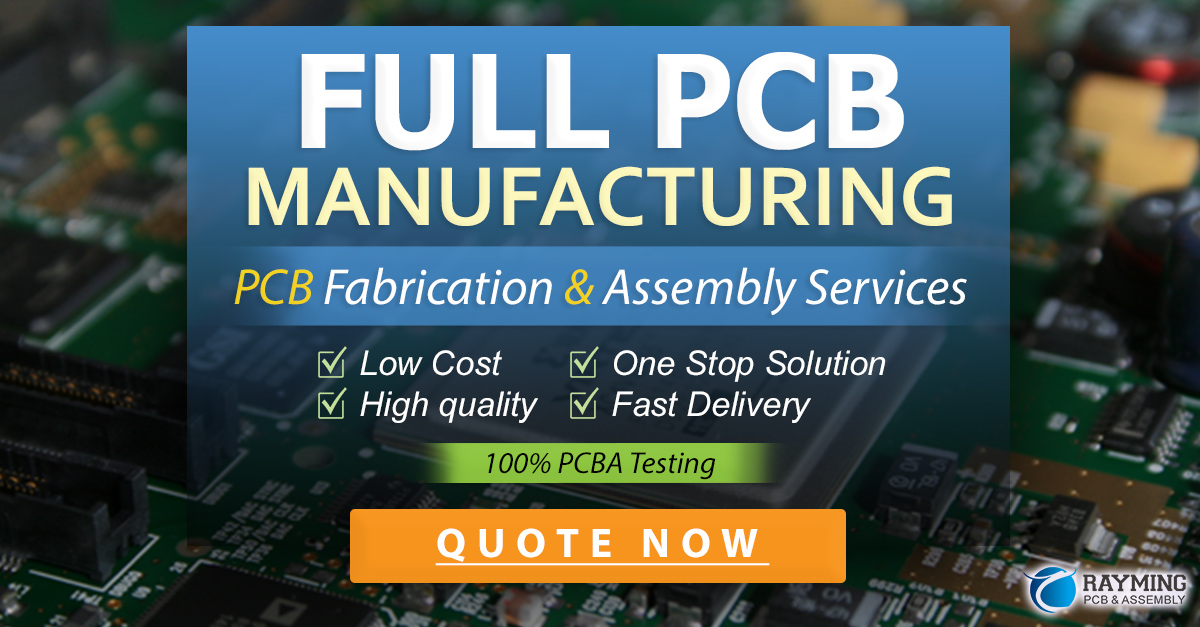
Frequently Asked Questions (FAQ)
-
Q: Does FR4 yellowing affect the electrical performance of a PCB?
A: In most cases, yellowing of FR4 does not directly impact the electrical performance of a PCB. However, severe yellowing may indicate degradation of the material, which could potentially lead to reduced insulation resistance or other issues over time. -
Q: Can FR4 yellowing be reversed?
A: Once FR4 has yellowed, it is generally not possible to reverse the discoloration. The best approach is to prevent yellowing through the use of UV stabilizers, protective coatings, and proper design considerations. -
Q: Are there any industry standards or guidelines for acceptable levels of FR4 yellowing?
A: There are no universally accepted industry standards for FR4 yellowing. Acceptable levels of discoloration depend on the specific application and the aesthetic requirements of the end product. Some manufacturers may have internal standards or guidelines based on their experience and customer expectations. -
Q: How can I test the UV resistance of an FR4 laminate?
A: UV resistance of FR4 laminates can be evaluated through accelerated aging tests, such as exposure to high-intensity UV light in a controlled environment. These tests can help compare the yellowing resistance of different laminate formulations and predict their long-term performance. -
Q: Are there any eco-friendly alternatives to FR4 that are less prone to yellowing?
A: Some eco-friendly PCB materials, such as those based on natural fibers (e.g., bamboo or paper) or biodegradable resins, may offer improved resistance to yellowing compared to traditional FR4. However, these materials may have limitations in terms of their electrical, mechanical, and thermal properties, and their suitability for a specific application should be carefully evaluated.
Conclusion
FR4 yellowing is a common challenge in PCB manufacturing, driven by factors such as UV exposure, thermal aging, and chemical exposure. While yellowing does not necessarily impact the electrical performance of a PCB, it can be a cosmetic concern in certain applications.
To minimize FR4 yellowing, manufacturers can employ strategies such as using UV stabilizers and additives, exploring alternative resin systems, applying protective coatings, and implementing design considerations to reduce UV exposure and thermal stress.
By understanding the causes and implementing appropriate mitigation strategies, PCB manufacturers can produce FR4 laminates with improved resistance to yellowing, ensuring the long-term aesthetic appeal and reliability of their products.
No responses yet