What is PCB Routing?
PCB routing is the process of creating electrical connections between components on a printed circuit board (PCB) using conductive traces. The goal of PCB routing is to ensure that all the components are properly connected according to the schematic design while minimizing the length of the traces, reducing crosstalk and interference, and ensuring proper signal integrity.
Why is PCB Routing Important?
PCB routing is important for several reasons:
-
Signal Integrity: Proper PCB routing ensures that the signals transmitted through the traces maintain their integrity and do not suffer from distortion, attenuation, or interference.
-
Noise Reduction: Effective PCB routing helps in minimizing noise and interference by reducing crosstalk between traces and ensuring proper grounding.
-
Manufacturability: Good PCB routing practices ensure that the board is easy to manufacture and assemble, reducing the chances of defects and errors.
-
Cost Reduction: Efficient PCB routing can help in reducing the overall cost of the PCB by minimizing the board size, reducing the number of layers, and optimizing the placement of components.
PCB Routing Tips for Beginners
1. Start with a Good Schematic Design
Before starting the PCB routing process, it is essential to have a good schematic design in place. The schematic should be complete, accurate, and properly labeled. It should also follow good design practices such as proper component selection, power supply decoupling, and signal integrity considerations.
2. Use a Grid System
Using a grid system can help in creating a more organized and efficient PCB layout. Most PCB Design software tools have built-in grid systems that can be customized according to the design requirements. A grid system helps in aligning components, creating consistent trace widths, and ensuring proper spacing between traces.
3. Define the Board Stackup
The board stackup refers to the arrangement of copper layers and insulating materials in the PCB. It is important to define the board stackup before starting the routing process as it affects the signal integrity, impedance, and manufacturability of the board. The stackup should be designed based on the signal requirements, power supply requirements, and manufacturability constraints.
4. Use Proper Trace Widths
The width of the traces used in the PCB routing should be based on the current carrying capacity and the required impedance of the signal. Wider traces can carry more current and have lower resistance, but they also take up more space on the board. Narrower traces have higher resistance and are more susceptible to noise and interference. The trace width should be selected based on the signal requirements and the available board space.
Signal Type | Trace Width (mm) |
---|---|
Power | 0.5 – 2.0 |
Ground | 0.5 – 2.0 |
Signal | 0.1 – 0.3 |
High-speed | 0.1 – 0.2 |
5. Minimize Trace Length
The length of the traces used in the PCB routing should be minimized as much as possible. Longer traces have higher resistance, inductance, and capacitance, which can affect the signal integrity and increase the susceptibility to noise and interference. Minimizing the trace length also helps in reducing the overall size of the board and improving the manufacturability.
6. Avoid Acute Angles
Acute angles in traces can cause signal reflections and reduce the manufacturing yield. It is recommended to use 45-degree angles instead of 90-degree angles whenever possible. If 90-degree angles are unavoidable, they should be mitered to reduce the stress on the trace during manufacturing.
7. Use Vias Appropriately
Vias are used to connect traces on different layers of the PCB. They should be used appropriately to minimize the number of layers and reduce the overall cost of the board. The size and placement of vias should be based on the signal requirements and the manufacturing constraints. It is recommended to use smaller vias for high-speed signals to minimize the discontinuity in the signal path.
8. Follow the Manufacturer’s Design Rules
Each PCB manufacturer has their own set of design rules that specify the minimum trace width, spacing, and hole size requirements for their manufacturing process. It is important to follow these design rules to ensure that the board is manufacturable and meets the required specifications. Violating the design rules can result in manufacturing defects and increase the overall cost of the board.
9. Use Ground Planes
Ground planes are used to provide a low-impedance return path for the signals and to reduce the noise and interference in the board. They also help in reducing the electromagnetic interference (EMI) and improving the signal integrity. It is recommended to use ground planes on both sides of the board and to connect them using vias at regular intervals.
10. Perform Design Rule Checks (DRC)
Most PCB design software tools have built-in design rule checks (DRC) that can be used to verify the PCB layout against the design rules specified by the manufacturer. It is important to perform DRC regularly during the routing process to catch any errors or violations early in the design process. DRC can help in identifying issues such as short circuits, open circuits, and spacing violations.
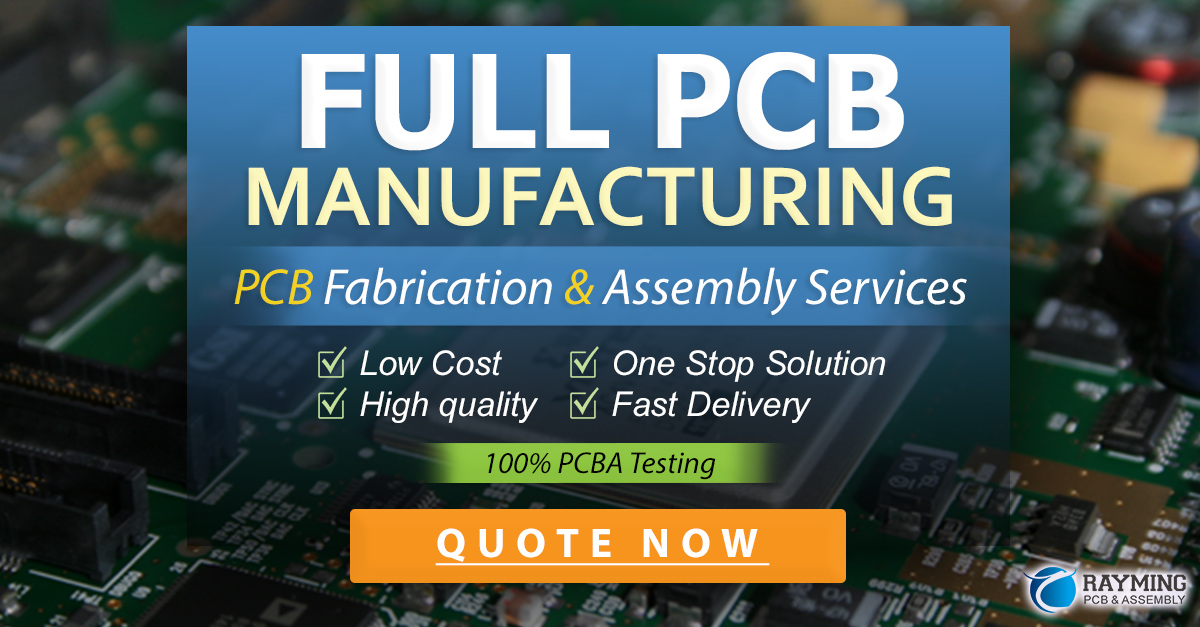
Frequently Asked Questions (FAQ)
1. What is the difference between a trace and a via?
A trace is a conductive path on the surface of the PCB that connects components together. A via is a conductive hole that is drilled through the board to connect traces on different layers.
2. How do I determine the appropriate trace width for my design?
The appropriate trace width depends on several factors such as the current carrying capacity, the required impedance, and the available board space. It is recommended to use a trace width calculator or consult the manufacturer’s design guidelines to determine the appropriate trace width for your design.
3. Can I route traces on both sides of the board?
Yes, traces can be routed on both sides of the board. However, it is important to ensure that the traces on opposite sides do not overlap to avoid short circuits and signal integrity issues.
4. How do I minimize crosstalk between traces?
Crosstalk can be minimized by ensuring adequate spacing between traces, using ground planes to provide shielding, and avoiding parallel runs of traces whenever possible. It is also recommended to use different signal layers for different signal types to reduce crosstalk.
5. What is the purpose of a ground plane in PCB routing?
A ground plane serves several purposes in PCB routing. It provides a low-impedance return path for the signals, reduces noise and interference, and helps in reducing electromagnetic interference (EMI). It also improves the signal integrity by providing a constant reference voltage for the signals.
Conclusion
PCB routing is a critical step in the PCB design process that requires careful planning and attention to detail. By following the tips and best practices outlined in this article, beginners can create high-quality PCB designs that meet the required specifications and are easy to manufacture. It is important to start with a good schematic design, use a grid system, define the board stackup, use proper trace widths, minimize trace length, avoid acute angles, use vias appropriately, follow the manufacturer’s design rules, use ground planes, and perform regular design rule checks. By following these guidelines, beginners can create PCB designs that are reliable, efficient, and cost-effective.
No responses yet