What are HDI PCBs?
HDI PCBs are printed circuit boards that feature higher wiring density per unit area compared to conventional PCBs. This increased density is achieved through the use of smaller vias, finer trace widths and spaces, and advanced manufacturing techniques. The Institute for Printed Circuits (IPC) defines HDI PCBs as having a higher wiring density per unit area than traditional PCBs, with any of the following features:
- Via hole diameters smaller than 0.15 mm (6 mils)
- Line width and space less than 0.09 mm (3.5 mils)
- Capture pad diameters smaller than 0.25 mm (10 mils)
HDI PCBs can be categorized into three main types based on their via structure:
- Through-hole via (THV) PCBs
- Blind via PCBs
- Buried via PCBs
Through-hole via (THV) PCBs
THV PCBs are the most common type of HDI PCBs. They feature vias that go through the entire thickness of the board, connecting the top and bottom layers. THV PCBs are cost-effective and suitable for less complex designs.
Blind via PCBs
Blind via PCBs have vias that start from either the top or bottom layer and terminate at an inner layer, without going through the entire board thickness. This allows for higher density routing and better signal integrity.
Buried via PCBs
Buried via PCBs have vias that connect inner layers without reaching the top or bottom layer of the board. This type of HDI PCB offers the highest density and best signal integrity, but it is also the most expensive and complex to manufacture.
Advantages of HDI PCBs
HDI PCBs offer several advantages over traditional PCBs:
-
Miniaturization: HDI PCBs enable the production of smaller and lighter devices by accommodating more components and interconnects in a smaller area.
-
Improved signal integrity: The shorter traces and smaller vias in HDI PCBs reduce signal distortion and noise, leading to better signal integrity and overall performance.
-
Increased functionality: With higher wiring density, HDI PCBs allow for more complex designs and increased functionality in a smaller footprint.
-
Reduced power consumption: The shorter traces in HDI PCBs result in lower resistance and capacitance, leading to reduced power consumption and improved energy efficiency.
-
Cost-effectiveness: Although the initial Manufacturing costs of HDI PCBs may be higher than traditional PCBs, they often lead to overall cost savings by reducing the number of layers, board size, and assembly complexity.
HDI PCB Manufacturing Processes
The manufacturing of HDI PCBs involves several advanced processes and technologies to achieve the required high density and precision. Some of the key processes include:
Microvias
Microvias are small, laser-drilled holes that connect the outer layers to the inner layers of the PCB. They are typically less than 0.15 mm (6 mils) in diameter and can be drilled using CO2, UV, or Excimer lasers. Microvias enable higher density interconnects and shorter signal paths.
Sequential lamination
Sequential lamination is a process where the PCB Layers are laminated in stages, allowing for the creation of blind and buried vias. This process involves laminating a subset of layers, drilling and plating the vias, and then laminating the remaining layers. Sequential lamination enables more complex HDI designs with multiple via types.
Modified semi-additive process (mSAP)
The modified semi-additive process is a advanced manufacturing technique that allows for the creation of fine traces and spaces. In mSAP, a thin layer of copper is deposited on the PCB substrate, followed by the application of a photoresist. The desired circuit pattern is then exposed and developed, and additional copper is plated onto the exposed areas. Finally, the photoresist is removed, and the thin copper layer is etched away, leaving the fine traces and spaces.
Embedded components
HDI PCBs can also incorporate embedded components, such as resistors, capacitors, and active devices, within the layers of the board. This further increases the density and functionality of the PCB while reducing the overall size and assembly complexity.
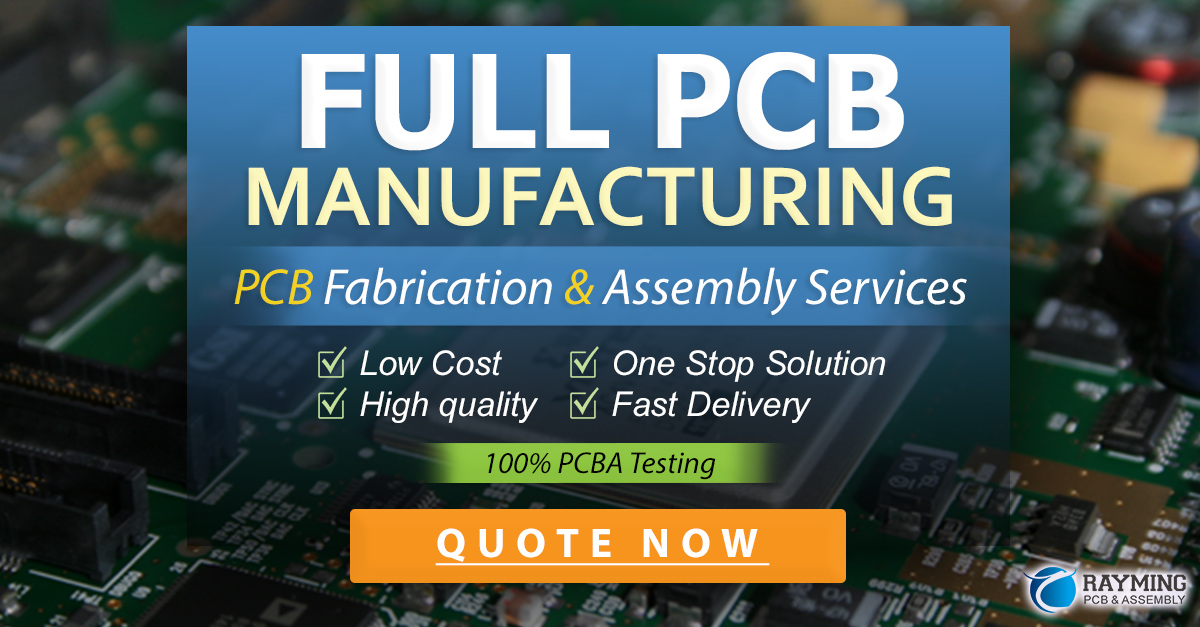
Applications of HDI PCBs
HDI PCBs find applications in a wide range of industries and products where size, weight, and performance are critical factors. Some of the main applications include:
-
Consumer electronics: Smartphones, tablets, laptops, and wearables rely on HDI PCBs to achieve compact sizes, high functionality, and low power consumption.
-
Medical devices: Implantable devices, diagnostic equipment, and medical wearables use HDI PCBs for their small size, reliability, and high performance.
-
Aerospace and defense: Satellites, drones, and military equipment employ HDI PCBs to meet the stringent requirements of size, weight, and reliability in harsh environments.
-
Automotive Electronics: Advanced driver assistance systems (ADAS), infotainment systems, and electric vehicle components use HDI PCBs for their high-density interconnects and robust performance.
-
Industrial automation: Robotics, machine vision systems, and industrial IoT devices leverage HDI PCBs for their compact size, high-speed communication, and reliable operation in demanding environments.
HDI PCB Design Considerations
Designing HDI PCBs requires careful consideration of several factors to ensure optimal performance, manufacturability, and reliability. Some of the key design considerations include:
-
Via type and placement: Choosing the appropriate via type (THV, blind, or buried) and optimizing their placement is crucial for achieving the desired interconnect density and signal integrity.
-
Trace width and spacing: HDI PCBs require fine traces and spaces, which must be carefully designed to maintain signal integrity and avoid manufacturing issues such as shorts or opens.
-
Layer stackup: The layer stackup of an HDI PCB must be carefully planned to accommodate the required interconnects, minimize signal distortion, and ensure proper impedance control.
-
Material selection: Choosing the right substrate material, copper weight, and laminate thickness is essential for achieving the desired electrical, thermal, and mechanical properties of the HDI PCB.
-
Design for manufacturing (DFM): Collaborating with the PCB manufacturer and following their DFM guidelines is crucial for ensuring the producibility and reliability of the HDI PCB design.
Future Trends in HDI PCBs
As technology continues to advance and the demand for smaller, faster, and more complex electronics grows, HDI PCBs are expected to evolve further. Some of the future trends in HDI PCBs include:
-
Increased via density: The development of new laser drilling technologies and materials will enable even smaller microvias and higher via densities.
-
Finer traces and spaces: Advancements in manufacturing processes like mSAP will allow for even finer traces and spaces, pushing the limits of HDI PCB density.
-
3D packaging: The integration of HDI PCBs with 3D packaging technologies, such as through-silicon vias (TSVs) and stacked die, will enable the creation of highly compact and complex electronic systems.
-
Flexible and stretchable HDI PCBs: The development of flexible and stretchable HDI PCBs will open up new possibilities for wearable electronics, medical implants, and other applications requiring conformal and bendable circuits.
-
Advanced materials: The adoption of new materials, such as low-loss dielectrics, high-frequency laminates, and thermally conductive substrates, will enhance the performance and reliability of HDI PCBs in demanding applications.
Frequently Asked Questions (FAQ)
-
What is the difference between HDI PCBs and traditional PCBs?
HDI PCBs have higher wiring density per unit area compared to traditional PCBs. They feature smaller vias, finer traces and spaces, and advanced manufacturing techniques, enabling the production of smaller, lighter, and more complex devices. -
What are the main types of HDI PCBs?
The three main types of HDI PCBs are: - Through-hole via (THV) PCBs
- Blind via PCBs
-
Buried via PCBs
-
What are the advantages of using HDI PCBs?
The advantages of HDI PCBs include: - Miniaturization
- Improved signal integrity
- Increased functionality
- Reduced power consumption
-
Cost-effectiveness
-
What are microvias, and how are they used in HDI PCBs?
Microvias are small, laser-drilled holes that connect the outer layers to the inner layers of the PCB. They are typically less than 0.15 mm (6 mils) in diameter and enable higher density interconnects and shorter signal paths in HDI PCBs. -
What are some of the key applications of HDI PCBs?
HDI PCBs find applications in various industries, including: - Consumer electronics
- Medical devices
- Aerospace and defense
- Automotive electronics
- Industrial automation
Conclusion
HDI PCBs have become an essential component in the electronics industry, enabling the production of smaller, faster, and more complex devices. By employing advanced manufacturing techniques and materials, HDI PCBs offer numerous advantages over traditional PCBs, including miniaturization, improved signal integrity, increased functionality, and reduced power consumption. As technology continues to evolve, HDI PCBs are expected to play an even more significant role in shaping the future of electronics, with trends such as increased via density, finer traces and spaces, 3D packaging, flexible and stretchable designs, and advanced materials. By understanding the fundamentals of HDI PCBs and their applications, engineers and designers can leverage this powerful technology to create innovative and high-performance electronic products that meet the ever-growing demands of the market.
No responses yet