How X-ray Inspection Works
X-ray inspection relies on the principle of X-ray attenuation. When an X-ray beam passes through an object, some of the X-rays are absorbed or scattered by the material, while others penetrate through. The amount of attenuation depends on the density, thickness, and composition of the object. Dense materials, such as metals, absorb more X-rays than less dense materials, like plastics or composites.
In an AXI system, an X-ray source generates a beam of X-rays that is directed towards the object being inspected. As the X-rays pass through the object, they are attenuated differently based on the internal structure and composition. A digital X-ray detector captures the resulting X-ray image, which represents the variations in X-ray intensity after passing through the object. This image is then processed and analyzed by specialized software to identify defects, measure dimensions, or assess the overall quality of the object.
Components of an AXI System
A typical AXI system consists of the following key components:
-
X-ray Source: Generates the X-ray beam used for inspection. The X-ray source can be a sealed tube or a more advanced microfocus X-ray tube, which provides higher resolution images.
-
X-ray Detector: Captures the X-ray image after the beam passes through the object. Detectors can be based on different technologies, such as flat-panel detectors or line scan cameras.
-
Manipulation System: Positions and moves the object being inspected relative to the X-ray source and detector. This can include a conveyor belt, a rotary table, or a robotic arm.
-
Image Processing Software: Analyzes the captured X-ray images to detect defects, measure dimensions, or perform other quality control tasks. Advanced software algorithms can enhance image contrast, remove noise, and apply various image processing techniques to extract meaningful information.
-
User Interface: Provides a graphical interface for operators to control the AXI system, set inspection parameters, and view the results. The user interface may include features like real-time image display, defect classification, and reporting tools.
Benefits of Automated X-ray Inspection
AXI offers several key benefits over traditional manual inspection methods:
-
Non-Destructive Testing: AXI allows for the inspection of objects without damaging or altering them. This is particularly important for critical components or finished products that cannot be disassembled or destroyed during testing.
-
High Throughput: Automated systems can inspect objects at a much faster rate compared to manual inspection. This increased throughput enables manufacturers to maintain high production volumes while ensuring comprehensive quality control.
-
Consistent and Objective Results: AXI eliminates the subjectivity and variability associated with human operators. The automated system applies the same inspection criteria consistently, reducing the risk of human error and ensuring reliable and repeatable results.
-
Improved Defect Detection: X-ray inspection can reveal internal defects that may not be visible on the surface, such as voids, cracks, or inclusions. AXI systems can detect even small defects with high accuracy, ensuring the quality and reliability of the inspected objects.
-
Cost Savings: By automating the inspection process and reducing the need for manual labor, AXI can lead to significant cost savings in the long run. The increased efficiency and reduced scrap rates also contribute to overall cost reductions.
Applications of Automated X-ray Inspection
AXI finds applications in various industries where quality control and defect detection are critical. Some common applications include:
Electronics Manufacturing
In the electronics industry, AXI is widely used for inspecting printed circuit boards (PCBs) and electronic components. It can detect defects such as:
- Solder joint defects (e.g., voids, bridges, insufficient solder)
- Component placement errors
- Broken or missing components
- Counterfeit or incorrect components
AXI is particularly valuable for inspecting complex, multi-layered PCBs where visual inspection is not feasible. It can also inspect ball grid array (BGA) and quad flat no-lead (QFN) packages, which have hidden solder joints underneath the component.
Automotive Industry
In the automotive industry, AXI is used to inspect critical components and assemblies for defects that could compromise safety or performance. Applications include:
- Inspection of castings and forgings for internal voids or inclusions
- Examination of welds for porosity, cracks, or lack of fusion
- Verification of proper assembly and alignment of components
- Detection of foreign objects or debris in assembled parts
AXI helps automotive manufacturers ensure the quality and reliability of their products, reducing the risk of failures and recalls.
Aerospace and Defense
The aerospace and defense industries rely on AXI for inspecting high-performance components and structures. Applications include:
- Inspection of turbine blades for internal defects
- Examination of composite materials for delamination or porosity
- Verification of proper assembly and alignment of complex mechanical systems
- Detection of foreign object debris (FOD) in critical areas
AXI plays a vital role in ensuring the safety and reliability of aircraft, spacecraft, and defense equipment.
Medical Devices
In the medical device industry, AXI is used to inspect implantable devices, surgical instruments, and other critical components. Applications include:
- Inspection of orthopedic implants for internal defects or manufacturing anomalies
- Examination of catheters and stents for proper assembly and dimensions
- Verification of the integrity of sealed medical packages
- Detection of contaminants or foreign objects in medical devices
AXI helps medical device manufacturers comply with strict quality standards and regulatory requirements, ensuring patient safety and product efficacy.
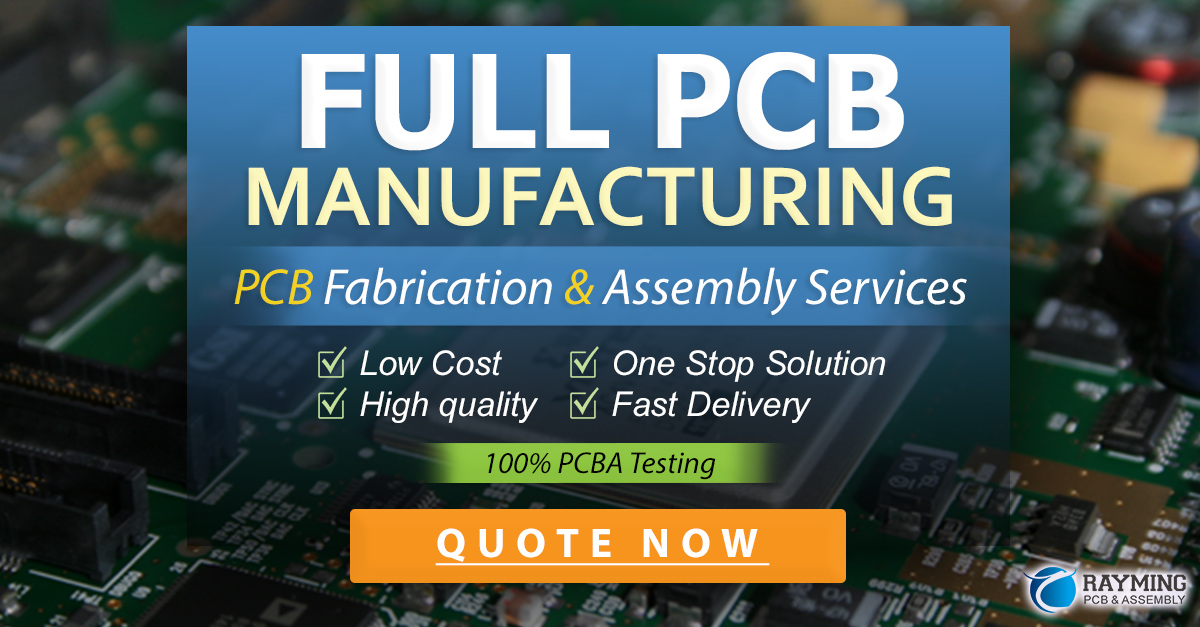
Advancements in Automated X-ray Inspection
AXI technology continues to evolve, with ongoing advancements in X-ray sources, detectors, and image processing algorithms. Some notable developments include:
Micro-CT Scanning
Micro-computed tomography (micro-CT) is an advanced X-ray imaging technique that provides high-resolution 3D images of objects. Micro-CT scanners use a rotating X-ray source and detector to capture multiple 2D projections of the object from different angles. These projections are then reconstructed into a detailed 3D model using specialized algorithms. Micro-CT enables the inspection of internal structures with sub-micron resolution, making it valuable for research, product development, and failure analysis.
AI-Powered Defect Detection
Artificial intelligence (AI) and machine learning algorithms are being increasingly integrated into AXI systems to enhance defect detection capabilities. AI-based algorithms can learn from large datasets of X-ray images and automatically identify defects or anomalies. These algorithms can adapt to different product types and continuously improve their performance over time. AI-powered defect detection can significantly reduce false positives and false negatives, improve inspection accuracy, and speed up the overall inspection process.
In-Line AXI Integration
Traditionally, AXI systems were used as standalone inspection stations, requiring objects to be removed from the production line for testing. However, advancements in AXI technology have enabled the integration of X-ray inspection directly into the production line. In-line AXI systems can inspect objects in real-time as they move along the conveyor, without interrupting the production flow. This integration allows for 100% inspection coverage, early defect detection, and immediate feedback for process control.
Challenges and Considerations
While AXI offers numerous benefits, there are also challenges and considerations to keep in mind:
-
Radiation Safety: X-rays are a form of ionizing radiation that can be harmful to human health if not properly controlled. AXI systems must be designed with adequate shielding and safety features to protect operators and the environment. Proper training and safety protocols are essential when working with X-ray equipment.
-
Cost and ROI: AXI systems can be a significant investment, especially for high-end systems with advanced features. Manufacturers need to carefully evaluate the return on investment (ROI) and consider factors such as inspection volume, defect rates, and the cost of quality issues. Proper system selection and optimization are crucial to maximizing the value of AXI.
-
Data Management and Analysis: AXI generates large amounts of data, including X-ray images and inspection results. Effective data management and analysis are essential to derive meaningful insights and make informed decisions. Manufacturers need to have robust data storage, retrieval, and analysis systems in place to handle the volume and complexity of AXI data.
-
Operator Training: While AXI systems are automated, operator training is still important. Operators need to understand the principles of X-ray inspection, system operation, and result interpretation. Proper training ensures that operators can effectively use the system, troubleshoot issues, and make informed decisions based on the inspection results.
-
Integration with Other Quality Control Methods: AXI is not a standalone solution but rather a complementary tool in a comprehensive quality control strategy. Manufacturers need to consider how AXI integrates with other inspection methods, such as visual inspection, Functional Testing, or electrical testing. Effective integration ensures a holistic approach to quality control and maximizes the benefits of each method.
Frequently Asked Questions (FAQ)
-
What types of defects can AXI detect?
AXI can detect a wide range of internal defects, including voids, cracks, inclusions, porosity, missing or broken components, solder joint defects, and alignment issues. It can also detect foreign objects or contaminants within the object. -
Is AXI suitable for inspecting all types of materials?
AXI is effective for inspecting objects made of materials with different densities, such as metals, plastics, composites, and ceramics. However, the inspection capability may be limited for extremely dense materials or objects with very thick walls, as the X-rays may not penetrate sufficiently. -
How does AXI compare to other non-destructive testing methods?
AXI offers several advantages over other non-destructive testing methods. Compared to ultrasonic testing, AXI can inspect objects with complex geometries and provide detailed images of internal structures. Compared to radiographic testing (RT), AXI offers higher throughput, real-time results, and easier data interpretation. -
Can AXI be used for inspecting large objects?
Yes, AXI can be used for inspecting large objects, such as automotive parts or aerospace components. However, the size of the object may be limited by the dimensions of the X-ray cabinet or the manipulation system. Large objects may require specialized AXI systems with extended X-ray source-to-detector distances and larger inspection areas. -
How do I select the right AXI system for my application?
Selecting the right AXI system depends on several factors, including the size and complexity of the objects being inspected, the required resolution and accuracy, the production volume, and the budget. It is important to consult with AXI equipment manufacturers or experienced technology partners to evaluate your specific requirements and determine the most suitable system for your application.
Aspect | Description |
---|---|
Defect Detection | AXI can detect internal defects such as voids, cracks, inclusions, porosity, missing or broken components, solder joint defects, and alignment issues. |
Material Compatibility | AXI is effective for inspecting objects made of materials with different densities, such as metals, plastics, composites, and ceramics. |
Comparison to Other NDT Methods | AXI offers advantages over ultrasonic testing for inspecting objects with complex geometries and provides higher throughput and easier data interpretation compared to radiographic testing. |
Large Object Inspection | AXI can inspect large objects, but the size may be limited by the dimensions of the X-ray cabinet or manipulation system. Specialized systems may be required for very large objects. |
System Selection | Selecting the right AXI system depends on factors such as object size and complexity, required resolution and accuracy, production volume, and budget. Consultation with experts is recommended. |
Conclusion
Automated X-ray Inspection (AXI) is a powerful non-destructive testing method that has transformed quality control processes across various industries. By leveraging the penetrating power of X-rays and advanced image processing algorithms, AXI systems provide accurate and reliable inspection results, detecting internal defects and ensuring the integrity of products. The benefits of AXI include non-destructive testing, high throughput, consistent and objective results, improved defect detection, and cost savings.
AXI finds applications in electronics manufacturing, automotive, aerospace, medical devices, and other industries where quality control is critical. Ongoing advancements in AXI technology, such as micro-CT scanning, AI-powered defect detection, and in-line integration, continue to enhance its capabilities and value proposition.
However, implementing AXI also comes with challenges and considerations, such as radiation safety, cost and ROI, data management, operator training, and integration with other quality control methods. Manufacturers need to carefully evaluate their specific requirements and work with experienced technology partners to select the right AXI system and optimize its performance.
As industries continue to prioritize product quality, reliability, and safety, the role of Automated X-ray Inspection will only grow in importance. By embracing AXI technology and integrating it into their quality control strategies, manufacturers can gain a competitive edge, reduce defects, and deliver high-quality products to their customers.
No responses yet