What are SMT Stencils?
SMT stencils are thin, flat sheets of metal or other materials with precisely cut openings that correspond to the solder pads on a PCB. They are used in the solder paste printing process, where solder paste is applied onto the PCB through the stencil openings using a squeegee. The stencil ensures that the right amount of solder paste is deposited on each pad, leading to a consistent and reliable solder joint after the components are placed and reflowed.
Types of SMT Stencils
There are three main types of SMT stencils used in PCB assembly:
- Framed Stencils
- Frameless Stencils
- Step-Up Stencils
Let’s explore each type in more detail.
Framed Stencils
Framed stencils are the most common type of SMT stencils. They consist of a thin metal foil (usually stainless steel) stretched and glued onto a rigid aluminum frame. The frame provides stability and ease of handling during the printing process.
Advantages of Framed Stencils
- Durable and long-lasting
- Easy to handle and store
- Compatible with most stencil printers
- Suitable for high-volume production
Disadvantages of Framed Stencils
- Higher cost compared to frameless stencils
- Larger storage space required
- Limited flexibility for quick changeovers
Frameless Stencils
Frameless stencils, also known as foilless or meshless stencils, are made of a thin metal foil without a supporting frame. They are typically used in specialized stencil printers that have a built-in tensioning system to keep the stencil flat and stable during the printing process.
Advantages of Frameless Stencils
- Lower cost compared to framed stencils
- Reduced storage space requirements
- Faster changeover times
- Improved print quality due to better gasketing
Disadvantages of Frameless Stencils
- Requires specialized stencil printers with tensioning systems
- Less durable than framed stencils
- Harder to handle manually
Step-Up Stencils
Step-up stencils, also called multi-level or 3D stencils, have different thicknesses in specific areas to accommodate components with varying heights or to improve the solder paste deposit for fine-pitch components. They are created by selectively etching or electroforming the stencil to achieve the desired step-up profile.
Advantages of Step-Up Stencils
- Improved solder paste deposition for fine-pitch components
- Better gasketing for uneven PCB surfaces
- Accommodates components with different heights
- Reduces the need for multiple stencils
Disadvantages of Step-Up Stencils
- Higher cost compared to standard stencils
- More complex design and manufacturing process
- Requires specialized expertise for proper implementation
Stencil Materials
SMT stencils can be made from various materials, each with its own characteristics and advantages. The most common materials used are:
- Stainless Steel: Durable, long-lasting, and suitable for high-volume production.
- Nickel: Harder and more wear-resistant than stainless steel, ideal for fine-pitch applications.
- Polyimide: Non-metallic material, suitable for prototyping and low-volume production.
The choice of material depends on factors such as the desired durability, print quality, and cost.
Stencil Thickness
The thickness of an SMT stencil plays a crucial role in determining the amount of solder paste deposited on the PCB pads. The most common stencil thicknesses are:
Thickness (mm) | Thickness (mil) | Typical Application |
---|---|---|
0.100 | 4 | Standard components |
0.125 | 5 | Fine-pitch components |
0.150 | 6 | Ultra-fine pitch components |
0.200 | 8 | Power components or connectors |
The optimal stencil thickness depends on the component pitch, pad size, and solder paste type used in the assembly process.
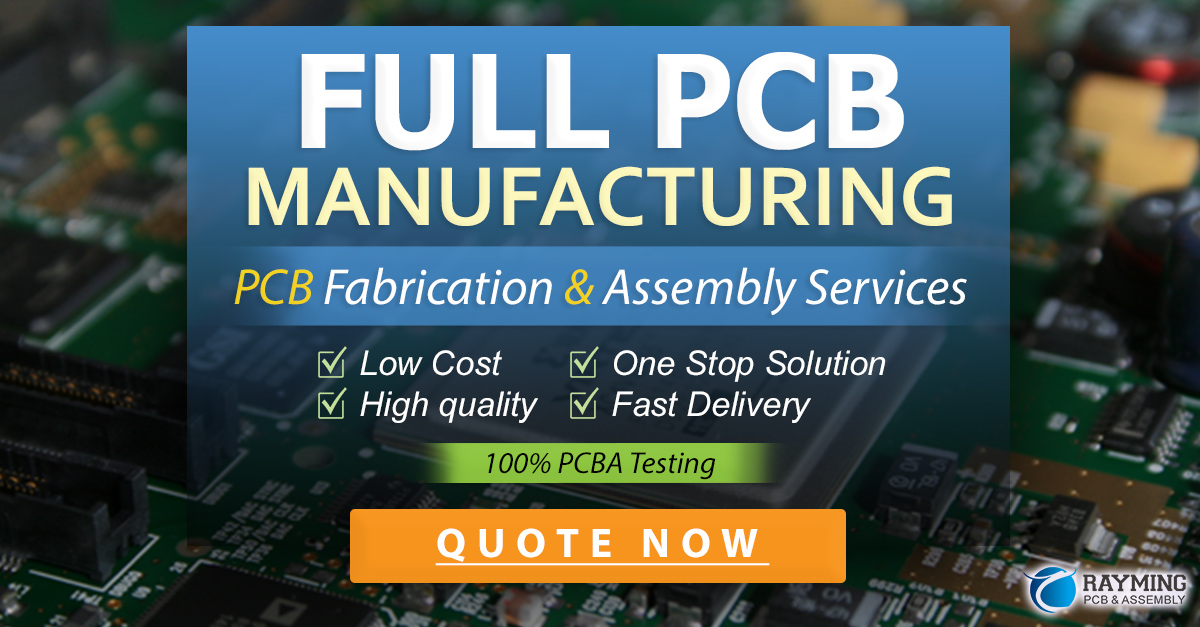
Stencil Aperture Design
The design of the stencil apertures is critical for achieving the desired solder paste deposit and ensuring a reliable solder joint. Factors to consider when designing stencil apertures include:
- Aperture size: Should be slightly larger than the PCB pad to allow for proper gasketing and paste release.
- Aperture shape: Can be circular, square, or rectangular, depending on the pad shape and component type.
- Aperture wall angle: Typically 5-15 degrees to facilitate paste release and prevent clogging.
Specialized software tools are used to create optimal stencil aperture designs based on the PCB layout and component requirements.
Stencil Printing Process
The SMT stencil printing process involves the following steps:
- Stencil alignment: The stencil is aligned with the PCB using fiducial marks or vision systems.
- Solder paste application: Solder paste is dispensed onto the stencil and spread across the apertures using a squeegee.
- Paste deposition: The squeegee is moved across the stencil, forcing the solder paste through the apertures and onto the PCB pads.
- Stencil separation: The stencil is lifted away from the PCB, leaving the solder paste deposits on the pads.
- Inspection: The printed PCB is inspected for defects such as insufficient or excessive solder paste, bridging, or misalignment.
Proper control of printing parameters, such as squeegee pressure, speed, and angle, is essential for achieving consistent and high-quality solder paste deposits.
Stencil Maintenance and Cleaning
Regular maintenance and cleaning of SMT stencils are essential for ensuring consistent print quality and extending the stencil’s life. Common maintenance and cleaning practices include:
- Wiping the stencil with a lint-free cloth between prints to remove excess solder paste.
- Using specialized stencil cleaning solutions and ultrasonic cleaners for periodic deep cleaning.
- Inspecting the stencil for damage, wear, or clogging, and repairing or replacing it as needed.
Proper storage of stencils, such as hanging them vertically or storing them in protective cases, helps prevent damage and contamination.
Frequently Asked Questions (FAQ)
1. What is the difference between a framed and frameless SMT stencil?
A framed stencil has a thin metal foil stretched and glued onto a rigid aluminum frame, while a frameless stencil is made of a thin metal foil without a supporting frame. Framed stencils are more durable and easier to handle, while frameless stencils offer lower cost and faster changeover times.
2. How do I choose the right stencil thickness for my PCB assembly?
The choice of stencil thickness depends on factors such as component pitch, pad size, and solder paste type. Generally, thinner stencils (0.100-0.125 mm) are used for standard and fine-pitch components, while thicker stencils (0.150-0.200 mm) are used for ultra-fine pitch components or power components and connectors.
3. What is a step-up stencil, and when is it used?
A step-up stencil, also called a multi-level or 3D stencil, has different thicknesses in specific areas to accommodate components with varying heights or to improve solder paste deposition for fine-pitch components. They are used when assembling PCBs with components of different heights or when fine-pitch components require more precise solder paste deposition.
4. How often should I clean my SMT stencil?
The frequency of stencil cleaning depends on factors such as the solder paste type, print volume, and environmental conditions. Generally, it is recommended to wipe the stencil with a lint-free cloth between prints and perform a deep cleaning using specialized solutions and ultrasonic cleaners every few prints or as needed based on print quality and stencil condition.
5. Can I use the same SMT stencil for different PCB designs?
In most cases, each PCB design requires a unique SMT stencil that matches its specific pad layout and component requirements. However, in some situations, such as when assembling similar PCBs with minor variations, a single stencil with multiple aperture designs can be used to accommodate the different layouts. This approach can help reduce stencil costs and changeover times in low-volume production scenarios.
Conclusion
SMT stencils are an essential tool in the PCB assembly process, enabling precise and consistent solder paste deposition for successful component mounting. Understanding the different types of stencils – framed, frameless, and step-up – along with their characteristics, advantages, and applications, is crucial for selecting the right stencil for a given PCB design and assembly requirements.
By considering factors such as stencil material, thickness, aperture design, and maintenance practices, manufacturers can optimize their SMT stencil printing process and achieve high-quality, reliable solder joints. As PCB designs continue to evolve with smaller components and finer pitches, the importance of SMT stencils in ensuring successful assembly will only continue to grow.
No responses yet