Introduction to M4 Mounting holes
M4 mounting holes are a common type of threaded fastener used in various applications, from consumer electronics to industrial machinery. These holes are designed to accommodate M4 screws, which have a nominal diameter of 4 mm. Understanding the dimensions and properties of M4 mounting holes is essential for engineers, designers, and manufacturers who work with these fasteners.
What are M4 Screws?
M4 screws are metric threaded fasteners with a nominal diameter of 4 mm. They are part of the ISO metric screw thread system, which is widely used around the world. M4 screws come in various lengths and head styles, such as socket head cap screws, button head screws, and flat head screws. These screws are commonly used in applications that require a small, precise, and strong fastening solution.
Importance of M4 Mounting Holes
M4 mounting holes play a crucial role in the assembly and functionality of many products. They provide a secure and reliable means of fastening components together, ensuring the structural integrity and performance of the final product. Properly designed and manufactured M4 mounting holes can:
- Withstand the forces and stresses applied to the assembly
- Provide a precise and consistent fit for M4 screws
- Facilitate easy assembly and disassembly when necessary
- Contribute to the overall quality and durability of the product
M4 Mounting Hole Dimensions
Basic Dimensions
The basic dimensions of an M4 mounting hole are determined by the nominal diameter of the M4 screw and the pitch of the thread. The nominal diameter is 4 mm, and the standard pitch for M4 screws is 0.7 mm. This means that the distance between the crests of adjacent threads is 0.7 mm.
Dimension | Value |
---|---|
Nominal Diameter | 4 mm |
Pitch | 0.7 mm |
Thread Dimensions
The thread dimensions of an M4 mounting hole are specified by the ISO metric thread standard. The standard defines the profile of the thread, which includes the major diameter, minor diameter, and pitch diameter. These dimensions are critical for ensuring a proper fit between the M4 screw and the mounting hole.
Dimension | Value |
---|---|
Major Diameter | 4.000 mm |
Minor Diameter | 3.242 mm |
Pitch Diameter | 3.545 mm |
Clearance and Tap Drill Sizes
When creating M4 mounting holes, it is essential to use the correct drill sizes for clearance holes and tap holes. Clearance holes are used when the M4 screw needs to pass freely through the hole, while tap holes are used when the hole needs to be threaded to engage with the screw.
Hole Type | Drill Size |
---|---|
Clearance Hole | 4.5 mm |
Tap Drill (50% thread engagement) | 3.3 mm |
Tap Drill (75% thread engagement) | 3.1 mm |
Countersink Dimensions
In some applications, M4 mounting holes may require countersinking to accommodate flat head screws or to create a flush surface. The countersink dimensions depend on the head style and size of the M4 screw being used. Common countersink angles include 82°, 90°, and 100°.
Screw Head Style | Countersink Angle | Countersink Diameter |
---|---|---|
Flat Head | 82° | 7.0 mm |
Flat Head | 90° | 7.5 mm |
Flat Head | 100° | 8.0 mm |
Design Considerations for M4 Mounting Holes
Material Selection
The material of the component containing the M4 mounting hole plays a significant role in determining the hole’s dimensions and properties. Different materials have varying strengths, hardnesses, and machinability, which can affect the performance and durability of the mounting hole. Common materials used in conjunction with M4 mounting holes include:
- Metals (steel, aluminum, brass, etc.)
- Plastics (ABS, polycarbonate, nylon, etc.)
- Composites (carbon fiber, fiberglass, etc.)
When selecting a material, consider factors such as the expected loads, environmental conditions, and manufacturing processes.
Thread Engagement
Thread engagement refers to the length of the M4 screw that is engaged with the threads in the mounting hole. Adequate thread engagement is essential for ensuring a strong and secure connection. The minimum thread engagement required depends on the material and application, but a general rule of thumb is to have at least 1.5 times the nominal diameter of the screw engaged in the hole.
For example, for an M4 screw with a nominal diameter of 4 mm, the minimum thread engagement would be:
Minimum Thread Engagement = 1.5 × 4 mm = 6 mm
Edge Distance and Spacing
When designing components with M4 mounting holes, it is important to consider the edge distance and spacing between holes. Edge distance refers to the distance between the center of the hole and the nearest edge of the component, while spacing refers to the distance between the centers of adjacent holes.
Adequate edge distance and spacing are necessary to prevent the material from cracking or failing under load. The recommended minimum edge distance and spacing depend on the material and application, but a general guideline is to have an edge distance of at least 2 times the nominal diameter of the screw and a spacing of at least 3 times the nominal diameter.
For M4 mounting holes, the recommended minimum edge distance and spacing would be:
Minimum Edge Distance = 2 × 4 mm = 8 mm
Minimum Spacing = 3 × 4 mm = 12 mm
Tolerances
Tolerances are an essential aspect of designing and manufacturing components with M4 mounting holes. Tolerances specify the allowable variation in dimensions, ensuring that the holes will function as intended and that the M4 screws will fit properly. When specifying tolerances for M4 mounting holes, consider factors such as:
- The manufacturing process (e.g., drilling, tapping, casting)
- The material properties and behavior
- The required fit between the screw and the hole (e.g., clearance fit, interference fit)
The ISO 286 standard provides guidelines for tolerances in metric threaded fasteners, including M4 screws and mounting holes.
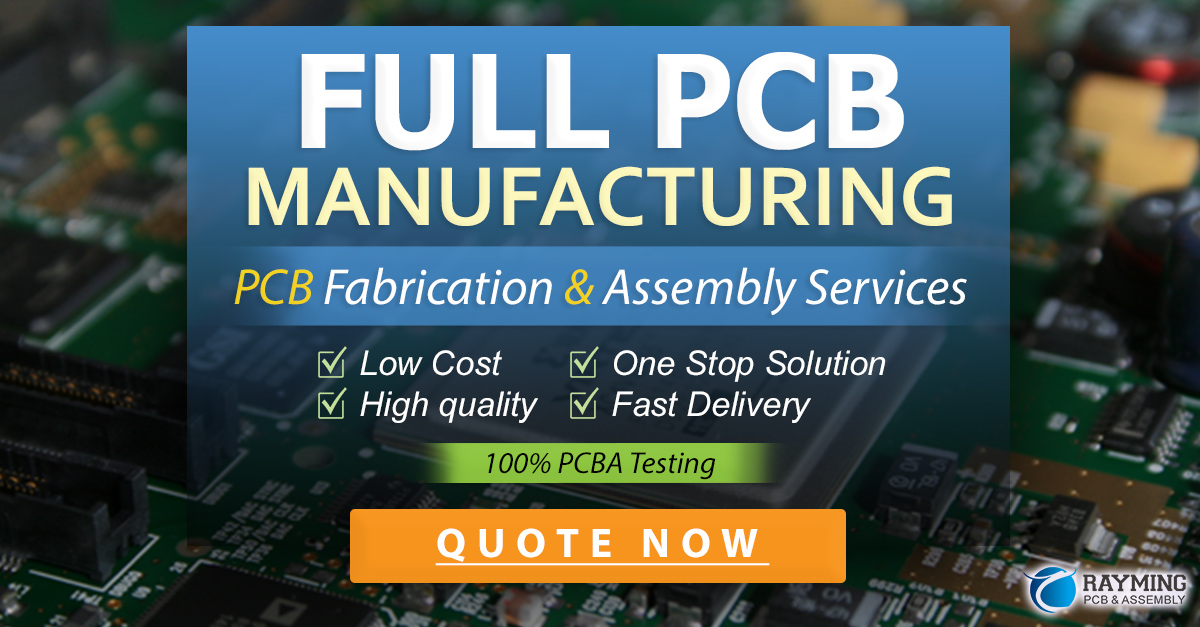
Manufacturing M4 Mounting Holes
Drilling
Drilling is the most common method for creating M4 mounting holes. The process involves using a drill bit to remove material and create a cylindrical hole. When drilling M4 mounting holes, consider the following:
- Use the appropriate drill size for the desired hole type (clearance or tap)
- Ensure proper alignment and perpendicularity of the drill bit
- Use cutting fluids or coolants to reduce heat and improve hole quality
- Control the feed rate and speed to minimize burrs and ensure a clean hole
Tapping
Tapping is the process of creating internal threads in a drilled hole to accommodate an M4 screw. Tapping can be performed by hand using a tap and wrench or by machine using a tapping tool. When tapping M4 mounting holes, keep in mind:
- Use the correct tap drill size for the desired thread engagement
- Ensure proper alignment and perpendicularity of the tap
- Use cutting fluids or lubricants to reduce friction and improve thread quality
- Control the tapping speed and pressure to minimize thread damage and ensure a clean thread
Reaming
Reaming is a finishing process used to improve the dimensional accuracy, surface finish, and cylindricity of a drilled hole. Reaming is often performed after drilling and before tapping to ensure the best possible fit for the M4 screw. When reaming M4 mounting holes, consider:
- Use the appropriate reamer size for the desired hole dimensions
- Ensure proper alignment and perpendicularity of the reamer
- Use cutting fluids or coolants to reduce heat and improve hole quality
- Control the feed rate and speed to minimize burrs and ensure a clean hole
Cast-in-Place Inserts
In some applications, such as plastic components, it may be necessary to use cast-in-place inserts to provide strong and durable M4 mounting holes. Cast-in-place inserts are metal threaded inserts that are molded into the component during the manufacturing process. These inserts provide a robust threaded hole that can withstand repeated use and high loads.
When designing components with cast-in-place inserts for M4 mounting holes, consider:
- The insert material and finish (e.g., brass, stainless steel, coated)
- The insert style and features (e.g., knurled, slotted, flanged)
- The mold design and insert placement to ensure proper alignment and retention
- The assembly process and any post-molding operations required
Fastening Techniques for M4 Mounting Holes
Screws and Bolts
M4 screws and bolts are the most common fasteners used with M4 mounting holes. These fasteners come in various lengths, head styles, and materials to suit different applications. When selecting M4 screws or bolts, consider:
- The required length and thread engagement for a secure connection
- The head style and drive type for ease of installation and aesthetics
- The material and finish for strength, durability, and corrosion resistance
- Any additional features, such as self-locking threads or washers
Threaded Inserts
Threaded inserts are used to provide strong, durable, and reusable threads in materials that may not be suitable for direct threading, such as plastics or thin sheet metals. These inserts are installed into the M4 mounting hole and provide a threaded hole for the M4 screw. Common types of threaded inserts include:
- Helical inserts (e.g., HeliCoil)
- Self-tapping inserts (e.g., Tap-Lok)
- Press-in inserts (e.g., PEM nuts)
- Heat-set inserts (for thermoplastics)
When selecting and installing threaded inserts, consider factors such as the insert material, installation method, and the specific requirements of the application.
Adhesive Bonding
In some cases, M4 mounting holes may be used in conjunction with adhesive bonding to provide a strong and permanent connection between components. Adhesive bonding involves applying a structural adhesive to the mating surfaces and using the M4 screw to clamp the components together while the adhesive cures.
When using adhesive bonding with M4 mounting holes, consider:
- The adhesive type and properties (e.g., epoxy, acrylic, polyurethane)
- The surface preparation and cleaning required for optimal adhesion
- The curing time, temperature, and pressure needed for the adhesive
- The disassembly and repair procedures, if necessary
FAQ
What is the difference between a clearance hole and a tap hole for M4 screws?
A clearance hole is a hole that allows an M4 screw to pass through freely without engaging the threads. The diameter of a clearance hole is typically larger than the major diameter of the M4 screw. A tap hole, on the other hand, is a hole that has been threaded to engage with the threads of the M4 screw. The diameter of a tap hole is smaller than the major diameter of the screw and depends on the desired thread engagement.
Can M4 mounting holes be used in plastic components?
Yes, M4 mounting holes can be used in plastic components. However, the material properties and design considerations may differ from those of metal components. When using M4 mounting holes in plastic components, consider factors such as the material strength, creep resistance, and the use of threaded inserts or self-tapping screws to provide a secure and durable connection.
What is the recommended torque for M4 screws?
The recommended torque for M4 screws depends on factors such as the screw material, the surface finish, the lubrication, and the joint material. As a general guideline, the recommended torque range for M4 screws is between 1.0 and 3.0 Nm (8.85 to 26.55 in-lbs). However, it is essential to consult the screw manufacturer’s specifications or conduct testing to determine the optimal torque for a specific application.
How can I prevent M4 screws from loosening in high-vibration environments?
There are several methods to prevent M4 screws from loosening in high-vibration environments, including:
- Using thread-locking compounds, such as anaerobic adhesives or pre-applied patches
- Employing self-locking nuts or inserts, such as nylon insert lock nuts or deformed thread lock nuts
- Applying mechanical locking methods, such as safety wire, lock washers, or cotter pins
- Designing the joint to minimize vibration and maintain proper preload on the screw
The choice of the appropriate method depends on the specific requirements and constraints of the application.
Can M4 mounting holes be used in high-temperature applications?
M4 mounting holes can be used in high-temperature applications, but the selection of materials and coatings for the screws and the component must be considered. Some materials, such as certain grades of stainless steel or high-temperature alloys, are better suited for elevated temperatures. Additionally, the use of high-temperature lubricants or anti-seize compounds may be necessary to prevent galling and ensure proper functioning of the fasteners.
Conclusion
M4 mounting holes are a versatile and widely used fastening solution in various industries and applications. Understanding the dimensions, design considerations, manufacturing processes, and fastening techniques associated with M4 mounting holes is crucial for engineers, designers, and manufacturers to create robust, reliable, and high-quality products.
By selecting the appropriate materials, specifying the correct hole dimensions, and employing suitable manufacturing and fastening methods, designers can ensure that M4 mounting holes provide a secure and durable connection between components. As with any fastening system, it is essential to consider factors such as the application requirements, environmental conditions, and assembly and maintenance procedures when designing and using M4 mounting holes.
With the information provided in this article, readers should have a comprehensive understanding of M4 mounting hole dimensions and be well-equipped to make informed decisions when working with these fasteners in their projects.
No responses yet