Types of PCB Soldering Defects
1. Bridging
Bridging occurs when solder accidentally connects two or more points on the PCB that should not be connected. This can happen when too much solder is applied, or when the solder is not properly controlled during the soldering process. Bridging can cause short circuits and other electrical issues.
2. Cold Joint
A cold joint occurs when the solder does not properly melt and flow, resulting in a weak and unreliable connection. This can happen when the soldering iron is not hot enough, or when the solder is not applied correctly. Cold joints can cause intermittent electrical issues and can eventually lead to complete failure of the joint.
3. Insufficient Solder
Insufficient solder occurs when not enough solder is applied to the joint, resulting in a weak and unreliable connection. This can happen when the soldering iron is not properly loaded with solder, or when the soldering process is rushed. Insufficient solder can cause intermittent electrical issues and can eventually lead to complete failure of the joint.
4. Excess Solder
Excess solder occurs when too much solder is applied to the joint, resulting in a bulky and uneven connection. This can happen when the soldering iron is overloaded with solder, or when the solder is not properly controlled during the soldering process. Excess solder can cause short circuits and other electrical issues.
5. Solder Balls
Solder balls are small spheres of solder that can form on the PCB during the soldering process. They can occur when the solder is not properly controlled, or when the PCB is not properly cleaned before soldering. Solder balls can cause short circuits and other electrical issues.
6. Tombstoning
Tombstoning occurs when a component lifts up and stands on end during the soldering process. This can happen when the solder on one side of the component melts before the other, causing the component to tilt and lift up. Tombstoning can cause the component to be misaligned or not properly connected to the PCB.
7. Pad Lifting
Pad lifting occurs when the copper pad on the PCB separates from the board during the soldering process. This can happen when the PCB is exposed to excessive heat or stress, or when the copper pad is not properly bonded to the board. Pad lifting can cause the component to be misaligned or not properly connected to the PCB.
8. Solder Wicking
Solder wicking occurs when the solder is drawn up into the component lead or the PCB hole during the soldering process. This can happen when the soldering iron is applied for too long, or when the hole is not properly cleaned before soldering. Solder wicking can cause insufficient solder on the joint and a weak connection.
9. Solder Flags
Solder flags are thin, ribbon-like extensions of solder that can form on the joint during the soldering process. They can occur when the solder is not properly controlled, or when the soldering iron is moved too quickly. Solder flags can cause short circuits and other electrical issues.
10. Solder Spikes
Solder spikes are sharp, pointed extensions of solder that can form on the joint during the soldering process. They can occur when the solder is not properly controlled, or when the soldering iron is applied with too much pressure. Solder spikes can cause short circuits and other electrical issues.
11. Dewetting
Dewetting occurs when the solder does not properly adhere to the surface of the PCB or the component lead. This can happen when the surface is not properly cleaned or prepared before soldering, or when the solder alloy is not compatible with the surface. Dewetting can cause a weak and unreliable connection.
12. Graping
Graping occurs when the solder forms a rough, grainy texture on the surface of the joint. This can happen when the solder is contaminated with impurities, or when the soldering process is not properly controlled. Graping can cause a weak and unreliable connection.
13. Disturbed Joint
A disturbed joint occurs when the solder joint is accidentally touched or moved while it is still molten. This can happen when the PCB is handled too soon after soldering, or when the soldering iron is accidentally touched to the joint. A disturbed joint can cause a weak and unreliable connection.
Tips for Preventing PCB Soldering Defects
Tip | Description |
---|---|
Use the right tools | Use a high-quality soldering iron with adjustable temperature control, and use the appropriate tip size for the job. |
Keep the soldering iron clean | Regularly clean the soldering iron tip with a damp sponge or brass wool to remove oxide buildup and ensure good heat transfer. |
Use the right solder | Use a solder alloy that is appropriate for the job, and make sure it is compatible with the surfaces being soldered. |
Apply the right amount of solder | Apply just enough solder to create a strong and reliable joint, but not so much that it causes bridging or excess solder. |
Control the soldering process | Use a steady hand and a consistent speed when applying the solder, and avoid moving the PCB or the component until the joint has cooled. |
Clean the surfaces before soldering | Make sure the PCB and component leads are clean and free of dirt, grease, and oxide before soldering. |
Preheat the PCB and components | Preheat the PCB and components to the appropriate temperature before soldering to ensure good solder flow and adhesion. |
Inspect the joints after soldering | Carefully inspect each solder joint after soldering to ensure it is strong, reliable, and free of defects. |
FAQ
1. What causes PCB soldering defects?
PCB soldering defects can be caused by a variety of factors, including:
– Incorrect soldering technique
– Incorrect solder alloy or flux
– Contaminated or oxidized surfaces
– Incorrect soldering iron temperature
– Inadequate preheating of the PCB and components
– Handling the PCB or components too soon after soldering
2. How can I prevent PCB soldering defects?
To prevent PCB soldering defects, follow these tips:
– Use the right tools and materials for the job
– Keep the soldering iron clean and at the appropriate temperature
– Apply the right amount of solder and flux
– Clean and prepare the surfaces before soldering
– Preheat the PCB and components to the appropriate temperature
– Control the soldering process with a steady hand and consistent speed
– Inspect the joints after soldering to ensure they are strong and reliable
3. What are the most common PCB soldering defects?
The most common PCB soldering defects include:
– Bridging
– Cold joints
– Insufficient or excess solder
– Solder balls
– Tombstoning
– Pad lifting
4. How can I fix PCB soldering defects?
To fix PCB soldering defects, follow these steps:
– Identify the type of defect and its cause
– Clean the affected area with a soldering iron and solder wick or a desoldering pump
– Reapply solder and flux as needed, using the appropriate technique and amount
– Inspect the joint to ensure it is strong and reliable
– If the defect cannot be fixed, consider replacing the affected component or PCB
5. Can PCB soldering defects be prevented entirely?
While it is not possible to prevent PCB soldering defects entirely, following best practices and using the right tools and techniques can greatly reduce the likelihood of defects occurring. Regular inspection and quality control measures can also help catch and correct defects before they cause more serious problems down the line.
By being aware of the different types of PCB soldering defects and taking steps to prevent them, manufacturers can ensure the reliability and performance of their electronic products.
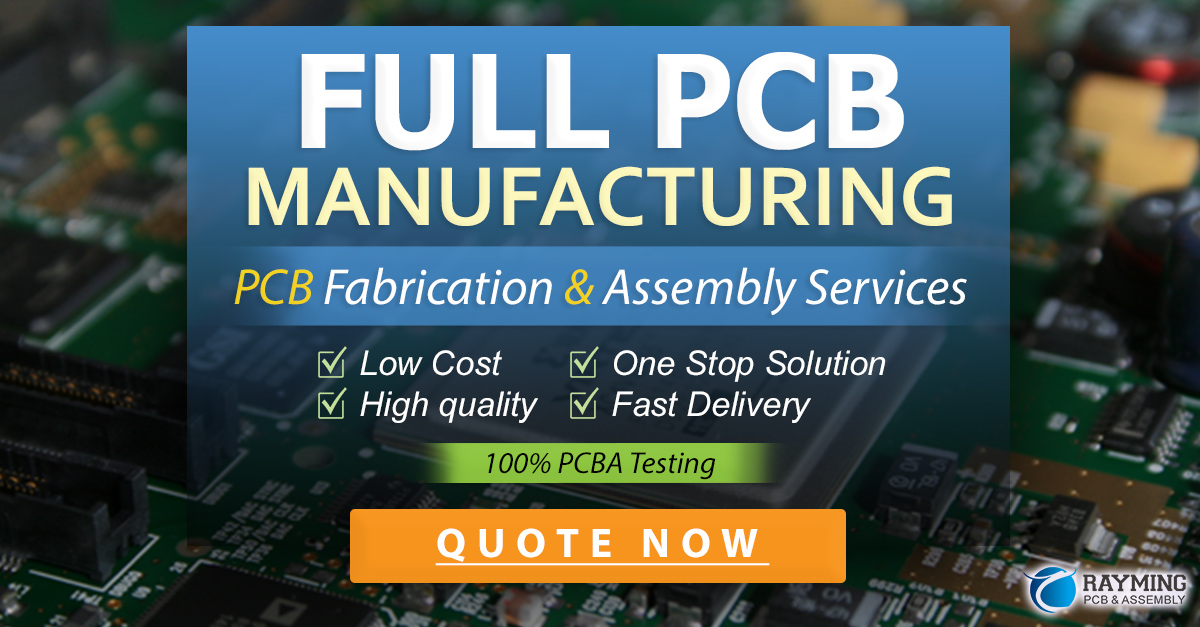
No responses yet