Introduction to PCB Comparison
Printed circuit boards (PCBs) are essential components in modern electronic devices. They provide the foundation for electrical connections and mechanical support for various components. Over the years, different materials have been used to manufacture PCBs, each with its own set of advantages and disadvantages. In this article, we will compare two types of PCBs: carbon nanotube PCBs and aluminum PCBs. We will discuss their properties, manufacturing processes, applications, and performance to help you make an informed decision when selecting a PCB for your project.
What is a Carbon Nanotube PCB?
Definition and Properties
Carbon nanotube PCBs are a relatively new type of PCB that utilize carbon nanotubes as the conductive material. Carbon nanotubes are cylindrical molecules made of carbon atoms arranged in a hexagonal lattice. They possess unique properties, such as high electrical conductivity, high thermal conductivity, and exceptional mechanical strength. When incorporated into PCBs, carbon nanotubes offer several advantages over traditional copper-based PCBs.
Manufacturing Process
The manufacturing process for carbon nanotube PCBs involves several steps:
-
Substrate preparation: A substrate, typically made of glass-reinforced epoxy (FR-4), is cleaned and prepared for the application of carbon nanotubes.
-
Carbon nanotube deposition: Carbon nanotubes are deposited onto the substrate using various methods, such as chemical vapor deposition (CVD), spray coating, or ink-jet printing. The nanotubes are aligned and patterned to form the desired circuit layout.
-
Insulation and protection: An insulating layer, such as a polymer or resin, is applied over the carbon nanotube layer to provide electrical insulation and protection from environmental factors.
-
Drilling and plating: Holes are drilled through the substrate and conductive layers to allow for the connection of components. The holes are then plated with a conductive material, such as copper, to ensure reliable electrical connections.
-
Surface finishing: The PCB undergoes surface finishing processes, such as solder mask application and silkscreen printing, to improve its durability and aesthetics.
Advantages of Carbon Nanotube PCBs
Carbon nanotube PCBs offer several advantages over traditional PCBs:
-
High electrical conductivity: Carbon nanotubes have a higher electrical conductivity than copper, allowing for faster signal transmission and lower resistance.
-
High thermal conductivity: Carbon nanotubes can dissipate heat more efficiently than copper, reducing the risk of thermal damage to components.
-
Lightweight: Carbon nanotube PCBs are lighter than copper-based PCBs, making them suitable for applications where weight reduction is crucial, such as aerospace and automotive industries.
-
High mechanical strength: Carbon nanotubes have exceptional mechanical strength, providing enhanced durability and resistance to vibration and shock.
-
Flexibility: Carbon nanotube PCBs can be made flexible, allowing for their use in wearable electronics and other applications where flexibility is required.
Applications of Carbon Nanotube PCBs
Carbon nanotube PCBs find applications in various industries, including:
-
Aerospace: The lightweight and high-performance characteristics of carbon nanotube PCBs make them suitable for use in aerospace systems, such as satellites and aircraft.
-
Automotive: Carbon nanotube PCBs can be used in automotive electronics, such as engine control units and infotainment systems, where high reliability and thermal management are essential.
-
High-speed electronics: The high electrical conductivity of carbon nanotubes enables the development of high-speed electronic devices, such as high-frequency communication systems and high-performance computing.
-
Wearable electronics: The flexibility and lightweight nature of carbon nanotube PCBs make them ideal for use in wearable devices, such as smartwatches and fitness trackers.
What is an Aluminum PCB?
Definition and Properties
Aluminum PCBs are a type of PCB that use aluminum as the base material instead of the more commonly used FR-4 substrate. Aluminum PCBs offer several advantages over traditional PCBs, particularly in terms of thermal management and mechanical stability. They consist of an aluminum substrate with a thin layer of dielectric material, typically a polymer or ceramic, and a conductive layer, usually copper, for the circuit traces.
Manufacturing Process
The manufacturing process for aluminum PCBs involves the following steps:
-
Substrate preparation: An aluminum substrate is cleaned and prepared for the application of the dielectric layer.
-
Dielectric layer application: A thin layer of dielectric material, such as a polymer or ceramic, is applied onto the aluminum substrate using methods like lamination, screen printing, or vapor deposition.
-
Circuit patterning: The conductive layer, typically copper, is applied onto the dielectric layer and patterned to form the desired circuit layout using processes such as photolithography and etching.
-
Drilling and plating: Holes are drilled through the aluminum substrate and conductive layers for component connections. The holes are then plated with a conductive material to ensure reliable electrical connections.
-
Surface finishing: The PCB undergoes surface finishing processes, such as solder mask application and silkscreen printing, to improve its durability and aesthetics.
Advantages of Aluminum PCBs
Aluminum PCBs offer several advantages over traditional FR-4 PCBs:
-
Excellent thermal management: Aluminum has a high thermal conductivity, allowing for efficient heat dissipation from components. This makes aluminum PCBs suitable for applications with high power densities or temperature-sensitive components.
-
Mechanical stability: Aluminum provides a rigid and stable base for the PCB, reducing the risk of warping or deformation under mechanical stress or temperature fluctuations.
-
Lightweight: Aluminum PCBs are lighter than copper-based PCBs of similar size, making them attractive for weight-sensitive applications.
-
Cost-effective: Aluminum is generally less expensive than other high-performance PCB materials, such as ceramic or polyimide, making aluminum PCBs a cost-effective solution for many applications.
-
Electromagnetic shielding: Aluminum PCBs can provide inherent electromagnetic shielding, reducing the impact of electromagnetic interference (EMI) on the circuit.
Applications of Aluminum PCBs
Aluminum PCBs find applications in various industries, including:
-
Power electronics: The excellent thermal management properties of aluminum PCBs make them suitable for use in power electronic applications, such as motor drives, inverters, and power supplies.
-
Automotive: Aluminum PCBs can be used in automotive electronics, particularly in high-temperature environments like engine control units and lighting systems.
-
LED lighting: The efficient heat dissipation provided by aluminum PCBs makes them ideal for use in high-power LED lighting applications.
-
Industrial control systems: Aluminum PCBs can withstand the harsh environmental conditions often encountered in industrial control systems, such as vibration, shock, and temperature extremes.
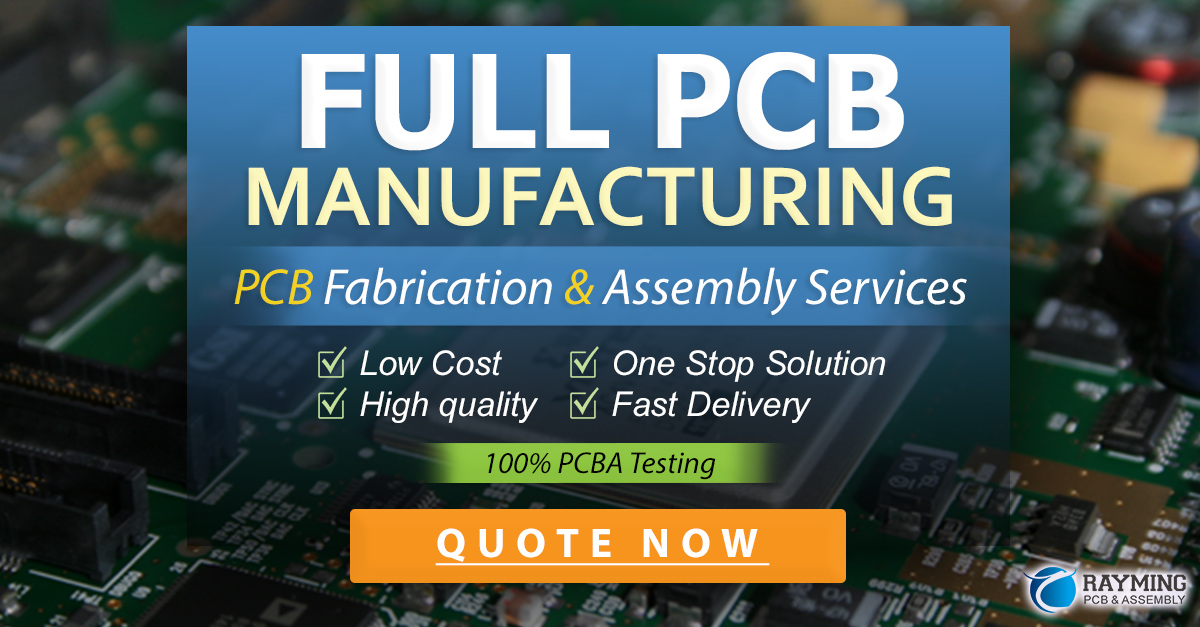
Comparison of Carbon Nanotube PCBs and Aluminum PCBs
Electrical Properties
Property | Carbon Nanotube PCB | Aluminum PCB |
---|---|---|
Electrical Conductivity | High | Moderate |
Signal Integrity | Excellent | Good |
Resistance to EMI | High | Moderate |
Carbon nanotube PCBs exhibit higher electrical conductivity compared to aluminum PCBs, allowing for faster signal transmission and lower resistance. They also offer excellent signal integrity and high resistance to electromagnetic interference (EMI). Aluminum PCBs, while not as conductive as carbon nanotube PCBs, still provide good electrical performance and moderate resistance to EMI.
Thermal Properties
Property | Carbon Nanotube PCB | Aluminum PCB |
---|---|---|
Thermal Conductivity | High | High |
Heat Dissipation | Excellent | Excellent |
Thermal Stability | High | High |
Both carbon nanotube PCBs and aluminum PCBs excel in thermal management. Carbon nanotubes have high thermal conductivity, allowing for efficient heat dissipation from components. Similarly, aluminum PCBs provide excellent thermal conductivity and heat dissipation capabilities. Both types of PCBs offer high thermal stability, making them suitable for applications with high power densities or temperature-sensitive components.
Mechanical Properties
Property | Carbon Nanotube PCB | Aluminum PCB |
---|---|---|
Strength | High | Moderate |
Flexibility | High | Low |
Vibration Resistance | High | Moderate |
Weight | Low | Moderate |
Carbon nanotube PCBs exhibit exceptional mechanical strength and flexibility, making them highly resistant to vibration and suitable for applications where flexibility is required. They are also lightweight, which is advantageous in weight-sensitive applications. Aluminum PCBs, while not as strong or flexible as carbon nanotube PCBs, provide moderate strength and vibration resistance. They are lightweight compared to traditional FR-4 PCBs but heavier than carbon nanotube PCBs.
Cost Comparison
Property | Carbon Nanotube PCB | Aluminum PCB |
---|---|---|
Material Cost | High | Moderate |
Manufacturing Cost | High | Moderate |
Overall Cost | High | Moderate |
Carbon nanotube PCBs are currently more expensive than aluminum PCBs due to the higher cost of carbon nanotube materials and the specialized manufacturing processes required. Aluminum PCBs, on the other hand, are more cost-effective, as aluminum is less expensive than other high-performance PCB materials, and the manufacturing processes are well-established.
Application Suitability
Application | Carbon Nanotube PCB | Aluminum PCB |
---|---|---|
High-speed electronics | Excellent | Good |
Power electronics | Good | Excellent |
Wearable electronics | Excellent | Poor |
Automotive | Good | Excellent |
Aerospace | Excellent | Good |
Industrial control systems | Good | Excellent |
Carbon nanotube PCBs are particularly well-suited for high-speed electronics and wearable electronics due to their high electrical conductivity, flexibility, and lightweight nature. They are also excellent for aerospace applications where weight reduction is crucial. Aluminum PCBs, on the other hand, excel in power electronics, automotive, and industrial control systems, where their excellent thermal management and mechanical stability are advantageous.
Frequently Asked Questions (FAQ)
-
Q: Are carbon nanotube PCBs commercially available?
A: While carbon nanotube PCBs are not yet widely commercially available, several companies and research institutions are actively developing and testing this technology. As manufacturing processes improve and costs decrease, it is expected that carbon nanotube PCBs will become more accessible in the future. -
Q: Can aluminum PCBs be used in high-frequency applications?
A: Aluminum PCBs can be used in high-frequency applications, but their performance may be limited compared to carbon nanotube PCBs or other specialized high-frequency materials. The choice of dielectric material and the design of the circuit layout play a crucial role in determining the high-frequency performance of aluminum PCBs. -
Q: Are carbon nanotube PCBs more environmentally friendly than traditional PCBs?
A: Carbon nanotube PCBs have the potential to be more environmentally friendly than traditional PCBs due to their lightweight nature and the possibility of using fewer environmentally harmful chemicals in their manufacturing process. However, the environmental impact of carbon nanotube production and disposal must also be considered. -
Q: How do aluminum PCBs compare to ceramic PCBs in terms of thermal management?
A: Both aluminum PCBs and ceramic PCBs offer excellent thermal management properties. Ceramic PCBs have higher thermal conductivity than aluminum PCBs, but they are also more expensive and brittle. Aluminum PCBs provide a good balance between thermal performance, cost, and mechanical stability. -
Q: Can carbon nanotube PCBs and aluminum PCBs be combined in a single design?
A: Yes, it is possible to combine carbon nanotube PCBs and aluminum PCBs in a single design, leveraging the strengths of each material. For example, a carbon nanotube PCB could be used for high-speed signal routing, while an aluminum PCB could be used for power management and thermal dissipation. However, the design and manufacturing process for such a hybrid PCB would be more complex and costly.
Conclusion
In conclusion, carbon nanotube PCBs and aluminum PCBs are two distinct types of PCBs with their own unique properties and advantages. Carbon nanotube PCBs excel in electrical performance, flexibility, and lightweight design, making them suitable for high-speed electronics, wearable devices, and aerospace applications. Aluminum PCBs, on the other hand, offer excellent thermal management, mechanical stability, and cost-effectiveness, making them ideal for power electronics, automotive, and industrial control systems.
When selecting between carbon nanotube PCBs and aluminum PCBs, it is essential to consider the specific requirements of your application, such as electrical performance, thermal management, mechanical stability, and cost. By understanding the strengths and limitations of each type of PCB, you can make an informed decision that best suits your project’s needs.
As technology advances, it is likely that we will see further developments in both carbon nanotube PCBs and aluminum PCBs, as well as the emergence of new PCB materials and manufacturing processes. Staying informed about these advancements will help you stay ahead of the curve and select the most appropriate PCB technology for your future projects.
No responses yet