What is Solder Paste?
Solder paste is a thick, paste-like material consisting of fine solder powder particles mixed with a flux vehicle. The solder alloy is typically tin-lead (SnPb) or lead-free, such as tin-silver-copper (SAC). The flux helps remove surface oxides, prevents re-oxidation, and promotes solder wetting during reflow. Solder paste is sticky and can be dispensed or printed onto PCB pads using a stencil.
Solder Paste Composition
Solder paste has four main ingredients:
-
Solder powder – Tiny spherical particles of solder alloy, typically ranging from 25-45 microns in diameter (Type 3-6). The size and shape of the particles affect printing and reflow properties.
-
Flux – Made of rosins, activators, solvents, and additives. Flux removes oxides from metals to aid solder wetting and flow. Solder paste flux is thicker and slower-drying compared to liquid flux.
-
Solvents – Added to give solder paste the right viscosity for printing. Solvents evaporate during preheat, so solder paste must be used quickly after opening.
-
Thickeners and additives – Control the rheology (flow behavior) of the paste for optimal printing, storage stability, tack strength, and reflow.
The ratio of solder powder to flux/vehicle in the paste is called the metal load, expressed as a percentage by weight. Typical metal loads range from 85-90%.
Types of Solder Paste
Solder pastes are categorized by the solder alloy composition, particle size, and flux type.
Solder Alloys
The most common solder paste alloys are:
- Tin-lead (SnPb) – Traditional eutectic Sn63/Pb37 or near-eutectic Sn62/Pb36/Ag2. Melts at 183°C.
- Lead-free (Pb-free) – Tin-silver-copper (SAC) alloys like SAC305 (Sn96.5/Ag3.0/Cu0.5) are most popular. Higher melting point around 217°C.
Other alloys may contain indium, bismuth, antimony, etc. for specialized applications.
Solder Powder Particle Size
Solder powder size is classified by mesh size ranging from Type 2 to Type 6. Larger numbers have smaller particles:
Type | Mesh Size (microns) |
---|---|
2 | 75-45 |
3 | 45-25 |
4 | 38-20 |
5 | 25-15 |
6 | 15-5 |
Smaller particles are used for fine-pitch components, while larger particles work for bigger components and connectors. Type 3 and 4 are most common.
Flux Types
Solder paste flux comes in three main types:
-
Rosin (RO) – Mildly activated, leaves clear residue. Suitable for most applications.
-
Rosin Mildly Activated (RMA) – Higher activity than RO. May require cleaning.
-
No-Clean (NC) – Low residue and ionics. Designed to be left on board after assembly.
Water-soluble (OA) fluxes also exist but are less common in solder paste.
How to Choose Solder Paste
Selecting the right solder paste involves considering multiple factors:
-
Solder alloy – Tin-lead or lead-free depending on application requirements, regulations, and process compatibility. SAC305 is the most common lead-free alloy.
-
Powder size – Type 3 or 4 works for most SMT assembly. Use Type 5 or 6 for fine-pitch and ultra-fine pitch components (<0.5mm pitch).
-
Flux type – No-clean flux is recommend for most production lines. Use water-soluble or rosin flux if cleaning is required or corrosion is a concern.
-
Metal load – Higher metal loads (88-90%) provide better deposition volume and bead shape. Lower metal load pastes (85-87%) may improve fine feature printing.
-
Printing performance – Evaluate key solder paste properties like viscosity, slump, and tack strength to ensure compatibility with your stencil printing process.
-
Reflow profile – Ensure the paste’s flux chemistry and alloy melting properties match your reflow oven profile and peak temperature requirements.
-
Reliability – Consider electrical, mechanical, and thermal reliability requirements. Some applications may need enhanced properties like vibration resistance or thermal cycling endurance.
It’s best to consult with solder paste suppliers to select products that fit your specific assembly process and reliability needs. Many suppliers offer solder paste guides and technical support to assist with product selection and optimization.
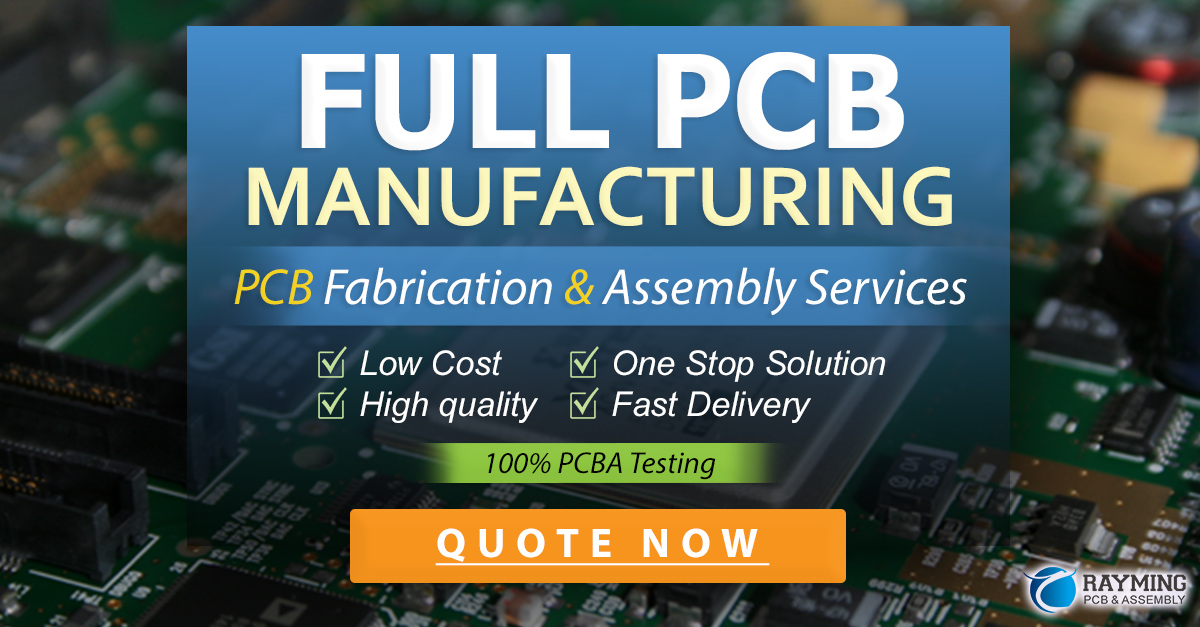
Solder Paste Storage
Proper storage and handling of solder paste is essential to maintain its printing and reflow characteristics. Solder paste has a limited shelf life that varies by alloy and flux chemistry.
Storage Conditions
- Temperature – Store solder paste in a refrigerator between 32-50°F (0-10°C) to maximize shelf life. Never freeze solder paste.
- Humidity – Keep solder paste in a humidity-controlled environment below 60% RH. High humidity can cause paste to dry out or absorb moisture.
- Upright position – Store solder paste jars and syringes upright to prevent flux separation and air entrapment.
Shelf Life
Solder paste shelf life depends on the alloy and flux type, ranging from 3 to 12 months. Consult the supplier for specific storage time limits.
- Unopened – Factory-sealed paste can be stored in a refrigerator for the full shelf life. Allow cold paste to reach room temperature naturally before opening.
- Opened – Once opened, solder paste must be used within a shorter period, typically 1-3 months. Refer to supplier guidelines for opened jar/cartridge shelf life.
Handling Tips
- Warming – Let refrigerated solder paste warm to room temperature for at least 4 hours before use. Never force-warm paste.
- Stirring – Gently stir the paste for 1-2 minutes with a spatula to ensure even flux distribution. Do not introduce air bubbles.
- Keep covered – When not in use, always keep the solder paste jar/cartridge covered to prevent drying and contamination.
- Scoop – Use a clean plastic spatula to scoop paste from the jar. Avoid metal tools that could contaminate or scratch the jar.
How to Use Solder Paste
Using solder paste involves three main steps: printing, component placement, and reflow soldering.
Step 1: Printing
Solder paste is printed onto the PCB pads using a laser-cut stainless steel stencil and squeegee blade. The stencil has apertures that match the size and shape of the pads.
- Align stencil – Carefully align the stencil to the PCB using fiducials or tooling pins. Secure the stencil flat against the board.
- Apply paste – Dispense a bead of solder paste along one edge of the stencil. Use enough paste to cover the print area.
- Squeegee – Slowly drag the metal squeegee blade across the stencil at a 45° angle, forcing paste through the apertures and onto the pads. Maintain even pressure and speed.
- Inspect – After printing, lift the PCB straight up off the stencil. Visually inspect the paste deposits for consistent volume, shape, and alignment.
- Clean stencil – Wipe the bottom side of the stencil clean with lint-free cloth and solvent. Periodically remove and clean the stencil entirely to prevent clogging.
Common solder paste printing defects include:
- Bridging – Too much paste causing shorts between pads or leads
- Insufficients – Not enough paste on pads for proper bonding
- Scooping – Paste stuck to stencil aperture walls creating divots
- Smearing – Excess paste on top of stencil or squeegee
- Skipping – Some pads missing paste due to poor release from stencil
Optimize your squeegee pressure/speed, stencil thickness, and separation speed to minimize print defects.
Step 2: Pick-and-Place
After printing, SMD components are placed onto the solder paste deposits using automated pick-and-place machines or sometimes by hand. The placement pressure should be just enough to push components into the paste without disturbing or flattening the deposits too much. Most pick-and-place systems have vision alignment to accurately center the component leads on the pads.
Step 3: Reflow
Finally, the PCB is heated in a multi-zone convection reflow oven to melt the solder paste and permanently attach the components. The reflow profile must be carefully tailored to the solder paste characteristics for optimal results.
- Preheat – The PCB is slowly heated to 150-170°C to dry the solder paste, activate the flux, and warm the board/components. Heating too fast can cause slumping or tombstoning.
- Thermal soak – Temperature is stabilized for 60-90 seconds to remove any remaining solvent and ensure all areas reach an even temperature.
- Reflow spike – The oven temperature is quickly spiked to 20-40°C above the solder alloy’s melting point. In this liquidus stage, the alloy melts, wets the surfaces, and forms solder joints.
- Cooling – The PCB is cooled at a controlled rate to solidify the solder joints without cracking or unwanted intermetallic growth. Fans speed cooling back to room temperature.
Reflow soldering requires precise profile control and real-time oven monitoring to ensure the paste reaches the right temperatures for the right durations. Incorrect reflow parameters can cause defects like:
- Cold joints – Gray, porous appearance from insufficient heat
- Tombstoning – Components lifting up on one end due to uneven heating
- Bridging – Solder shorts from excessive heat or paste volume
- Solder balling – Small solder balls due to poor wetting and flux exhaustion
- Voiding – Hollow air bubbles within the solder joint
Post-reflow, the solder joints should be smooth, shiny, and slightly concave in shape. X-ray inspection may be used to detect subsurface voids or cracks.
Solder Paste FAQs
What is the shelf life of solder paste?
Unopened solder paste can last 6-12 months when stored in a refrigerator. Opened jars should be used within 1-3 months. Always check the paste’s born-on date and follow the manufacturer’s storage guidelines.
How long can solder paste be left out at room temperature?
Ideally, solder paste should be used immediately after warming to room temperature. However, paste can sit out for up to 8 hours during a work shift if kept sealed and prevented from drying out. Avoid exposing paste to excessive heat or humidity.
Can you reuse solder paste?
It’s best not to return unused solder paste from the stencil back into the original jar to avoid contamination. Only reuse paste if it’s still fresh, clean, and has not started to dry out. When in doubt, discard the paste.
What happens if you use expired solder paste?
Expired or improperly stored solder paste can suffer from flux separation, dry-out, or degraded rheology. This can cause printing and reflow issues like poor release, slumping, solder balling, graping, or joint weakness. Always use the freshest paste possible.
How do you dispose of solder paste?
Solder paste contains metals and chemicals that require special disposal. Never pour paste down the drain. Check with your local waste authority for approved solder paste disposal methods. Most manufacturers offer take-back recycling services for their spent paste.
Conclusion
Solder paste is the foundation of a robust SMT assembly process. By understanding solder paste composition, types, storage needs, and proper usage, you can optimize your solder paste printing and reflow results. Always use fresh, high-quality solder paste from a trusted supplier and follow their technical guidelines. Investing the time to select and master the right solder paste will pay dividends in higher yields, greater reliability, and lower assembly costs.
No responses yet