What is Solder Mask?
Solder mask is a polymer-based ink that is applied to the copper traces of a PCB. Its primary purpose is to insulate the copper traces from accidental contact with other conductive materials, such as solder, during the assembly process. The solder mask also provides protection against oxidation and other environmental factors that can degrade the performance of the PCB over time.
Composition of Solder Mask
Solder mask is typically composed of epoxy or acrylic-based polymers, along with various additives such as fillers, pigments, and photoinitiators. These additives help to improve the physical and chemical properties of the solder mask, such as its adhesion to the copper, its resistance to chemicals and high temperatures, and its color stability.
Properties of Solder Mask
A high-quality solder mask should possess the following properties:
- High electrical insulation resistance
- Good adhesion to the copper surface
- Excellent chemical and thermal resistance
- Smooth and even surface finish
- Consistent color and appearance
- Compatibility with various solderable finishes, such as HASL, ENIG, and OSP
Solder Mask Application Process
The application of solder mask to a PCB involves several steps, each of which is critical to ensuring a high-quality finish. The process typically includes the following stages:
1. Surface Preparation
Before applying the solder mask, the PCB surface must be thoroughly cleaned to remove any contaminants, such as dirt, grease, or oxidation. This is typically done using a combination of chemical cleaning agents and mechanical abrasion.
2. Solder Mask Application
The solder mask is applied to the PCB surface using one of several methods, such as screen printing, curtain coating, or spray coating. The choice of application method depends on factors such as the size and complexity of the PCB, the desired thickness of the solder mask, and the production volume.
3. Curing
After application, the solder mask must be cured to achieve its final properties. This is typically done using UV light or heat, depending on the type of solder mask used. The curing process helps to crosslink the polymers in the solder mask, making it harder and more resistant to chemicals and high temperatures.
4. Inspection
Once the solder mask has been cured, the PCB is inspected to ensure that the mask has been applied evenly and without any defects, such as pinholes, bubbles, or cracks. Any defects must be repaired before the PCB can be used in the assembly process.
Types of Solder Mask
There are several types of solder mask available, each with its own unique properties and advantages. Some of the most common types include:
Liquid Photoimageable Solder Mask (LPISM)
LPISM is a type of solder mask that is applied as a liquid and then cured using UV light. It offers high resolution and excellent adhesion to the copper surface, making it ideal for fine-pitch PCBs and high-density designs.
Dry Film Solder Mask (DFSM)
DFSM is a type of solder mask that is applied as a thin, dry film and then laminated onto the PCB surface. It offers good chemical and thermal resistance, as well as excellent adhesion to the copper. However, it may not be suitable for very fine-pitch designs due to its thickness.
Peelable Solder Mask (PSM)
PSM is a temporary solder mask that is applied to the PCB surface during the assembly process and then peeled off after soldering. It is used to protect specific areas of the PCB from solder, such as test points or connector pads.
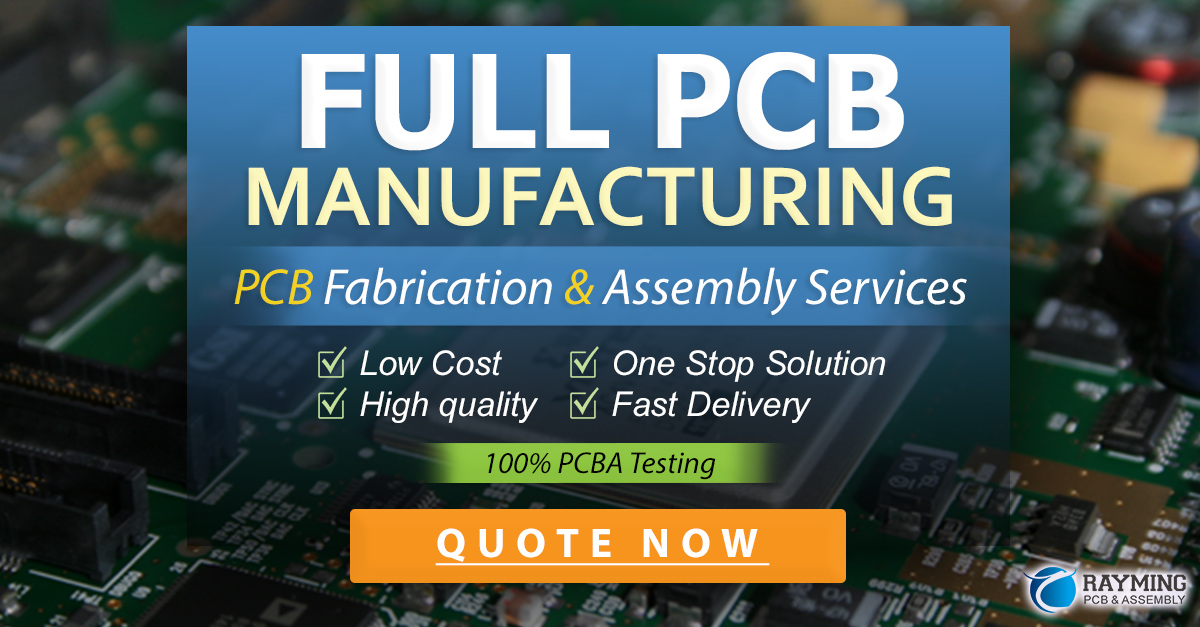
Solder Mask Colors
Solder mask is available in a variety of colors, with green being the most common. Other popular colors include blue, red, yellow, black, and white. The choice of color depends on factors such as the intended use of the PCB, the desired appearance, and the compatibility with the solderable finish.
Color | Advantages | Disadvantages |
---|---|---|
Green | – Most common color – Good contrast with copper – Provides good protection against oxidation |
– May not be suitable for certain applications – Can be difficult to see certain components |
Blue | – Good contrast with copper – Aesthetically pleasing |
– Less common than green – May be more expensive |
Red | – High visibility – Often used for power planes |
– May not provide good contrast with certain components |
Yellow | – High visibility – Often used for warning or danger areas |
– May not provide good contrast with certain components |
Black | – Provides good protection against oxidation – High contrast with copper |
– Can make it difficult to see certain components |
White | – High visibility – Often used for silkscreen applications |
– May not provide good protection against oxidation |
Solder Mask and Solderable Finishes
The choice of solderable finish can have a significant impact on the performance of the solder mask. Some finishes, such as Hot Air Solder Leveling (HASL) and Electroless Nickel Immersion Gold (ENIG), require a thicker solder mask to provide adequate protection against the high temperatures and chemicals used in the finishing process.
Other finishes, such as Organic Solderability Preservative (OSP) and Immersion Silver (IAg), are more compatible with thinner solder masks and can provide a flatter, more even surface for component placement.
Benefits of Solder Mask
The use of solder mask offers several benefits in the manufacture of PCBs, including:
-
Protection against short circuits: Solder mask prevents accidental contact between the copper traces and other conductive materials, reducing the risk of short circuits and other defects.
-
Improved reliability: Solder mask provides protection against oxidation and other environmental factors that can degrade the performance of the PCB over time, improving its reliability and longevity.
-
Enhanced aesthetics: Solder mask can be used to improve the appearance of the PCB, with different colors and finishes available to suit different applications and preferences.
-
Better solderability: Solder mask can help to improve the solderability of the PCB by providing a flat, even surface for component placement and by preventing solder from flowing onto unwanted areas.
-
Reduced assembly time: Solder mask can help to reduce the assembly time of the PCB by providing clear markings and guides for component placement, as well as by preventing solder from flowing onto unwanted areas.
Frequently Asked Questions (FAQ)
1. What is the difference between solder mask and silkscreen?
Solder mask and silkscreen are both used in the manufacture of PCBs, but they serve different purposes. Solder mask is used to protect the copper traces and prevent short circuits, while silkscreen is used to add text, logos, and other markings to the PCB surface for identification and assembly purposes.
2. Can solder mask be removed from a PCB?
In most cases, solder mask cannot be easily removed from a PCB without damaging the copper traces or other components. However, some types of solder mask, such as peelable solder mask (PSM), are designed to be temporarily applied and then removed after soldering.
3. What is the typical thickness of solder mask?
The typical thickness of solder mask ranges from 0.5 to 2.0 mils (0.0127 to 0.0508 mm), depending on the type of solder mask and the application method used. Thicker solder masks may be required for certain solderable finishes or for high-voltage applications.
4. Can solder mask be applied to both sides of a PCB?
Yes, solder mask can be applied to both sides of a PCB, depending on the design requirements and the intended use of the board. Double-sided solder mask is commonly used in applications where both sides of the PCB need to be protected against short circuits and environmental factors.
5. How does solder mask affect the impedance of a PCB?
Solder mask can have a significant impact on the impedance of a PCB, particularly in high-frequency applications. The Dielectric constant of the solder mask material, as well as its thickness and uniformity, can all affect the impedance of the PCB traces. Designers must take these factors into account when selecting a solder mask and designing the PCB layout to ensure optimal performance.
Conclusion
Solder mask is a critical component in the manufacture of PCBs, providing essential protection against short circuits, oxidation, and other environmental factors. With its ability to improve reliability, enhance aesthetics, and reduce assembly time, solder mask plays a vital role in ensuring the quality and performance of electronic devices.
As PCB Designs continue to become more complex and demanding, the importance of selecting the right solder mask and application process will only continue to grow. By understanding the properties, types, and benefits of solder mask, designers and manufacturers can make informed decisions that will help to ensure the success of their projects and the satisfaction of their customers.
No responses yet