Introduction to PCB Manufacturing
Printed Circuit Board (PCB) manufacturing is a complex process that involves various steps and technologies to create high-quality electronic circuits. PCBs are essential components in almost all modern electronic devices, from smartphones and computers to industrial equipment and medical devices. In this article, we will explore the manufacturing capabilities of PCB and PCB assembly, focusing on the key aspects of the process and the technologies involved.
What is a PCB?
A PCB is a flat board made of insulating material, such as fiberglass or plastic, with conductive pathways etched or printed on its surface. These pathways, also known as traces, connect various electronic components, such as resistors, capacitors, and integrated circuits (ICs), to form a functional electronic circuit. PCBs provide a stable and reliable platform for electronic components, ensuring proper connectivity and minimizing signal interference.
Types of PCBs
There are several types of PCBs, each designed to meet specific requirements and applications. The most common types include:
-
Single-sided PCBs: These PCBs have conductive traces on only one side of the board. They are the simplest and most cost-effective type of PCB, suitable for basic electronic applications.
-
Double-sided PCBs: These PCBs have conductive traces on both sides of the board, allowing for more complex circuits and higher component density. The two sides are connected using through-hole technology or vias.
-
Multi-layer PCBs: These PCBs consist of multiple layers of conductive traces separated by insulating layers. They offer the highest component density and are used in advanced electronic applications, such as high-speed digital circuits and RF systems.
-
Flexible PCBs: These PCBs are made of flexible materials, such as polyimide or polyester, allowing them to bend and conform to various shapes. They are commonly used in wearable devices, medical equipment, and aerospace applications.
-
Rigid-Flex PCBs: These PCBs combine the benefits of rigid and flexible PCBs, featuring both rigid and flexible sections. They are used in applications that require both stability and flexibility, such as folding smartphones and automotive electronics.
PCB Manufacturing Process
The PCB manufacturing process involves several key steps, each contributing to the quality and functionality of the final product. The main steps include:
1. PCB Design and Layout
The first step in PCB manufacturing is designing the circuit and creating the PCB layout. This process involves using specialized software, such as Altium Designer or KiCad, to create a digital representation of the circuit schematic and the physical layout of the PCB. The layout determines the placement of components, the routing of traces, and the overall dimensions of the board.
2. PCB Fabrication
Once the PCB design is finalized, the fabrication process begins. The main steps in PCB fabrication include:
a. Substrate Preparation: The PCB substrate, typically a fiberglass-reinforced epoxy laminate, is cut to the required size and shape.
b. Copper Cladding: A thin layer of copper is bonded to one or both sides of the substrate using heat and pressure.
c. Drilling: Holes are drilled through the substrate to accommodate through-hole components and vias.
d. Patterning: The desired circuit pattern is transferred onto the copper layer using a photoresist and exposure to UV light. The unexposed areas are then etched away, leaving only the desired conductive traces.
e. Plating: The exposed copper traces and holes are plated with a thin layer of copper, followed by a layer of tin-lead alloy (solder) or other protective coatings.
f. Solder Mask Application: A protective solder mask is applied to the PCB surface, leaving only the exposed pads and holes for component assembly.
g. Silkscreen Printing: The component labels, logos, and other markings are printed onto the PCB surface using a silkscreen process.
3. PCB Assembly
After the PCB fabrication is complete, the electronic components are assembled onto the board. The main steps in PCB assembly include:
a. Solder Paste Application: A precise amount of solder paste is applied to the component pads using a stencil or syringe.
b. Component Placement: The electronic components are placed onto the PCB using automated pick-and-place machines or manual placement for smaller batches.
c. Reflow Soldering: The PCB with the placed components is passed through a reflow oven, which melts the solder paste and forms a permanent electrical and mechanical connection between the components and the PCB.
d. Inspection and Testing: The assembled PCB is visually inspected and tested for functionality, ensuring that all components are correctly placed and the circuit performs as intended.
PCB Manufacturing Technologies
Several advanced technologies are employed in PCB manufacturing to achieve higher precision, reliability, and performance. Some of these technologies include:
1. High-Density Interconnect (HDI) PCBs
HDI PCBs feature finer trace widths, smaller vias, and higher component density compared to traditional PCBs. They are manufactured using advanced processes, such as laser drilling, microvias, and sequential lamination. HDI PCBs are commonly used in smartphones, wearables, and other compact electronic devices.
2. Embedded Component PCBs
Embedded component PCBs have electronic components, such as resistors and capacitors, embedded within the layers of the PCB substrate. This technology allows for higher component density, improved signal integrity, and reduced board size. Embedded component PCBs are used in applications that require high performance and miniaturization, such as medical implants and aerospace systems.
3. 3D Printed PCBs
3D printing technology is being explored for PCB manufacturing, enabling the creation of complex, three-dimensional circuit structures. 3D printed PCBs can incorporate conductive and insulating materials in a single print, allowing for novel designs and improved functionality. While still in the early stages of development, 3D printed PCBs have the potential to revolutionize electronics manufacturing.
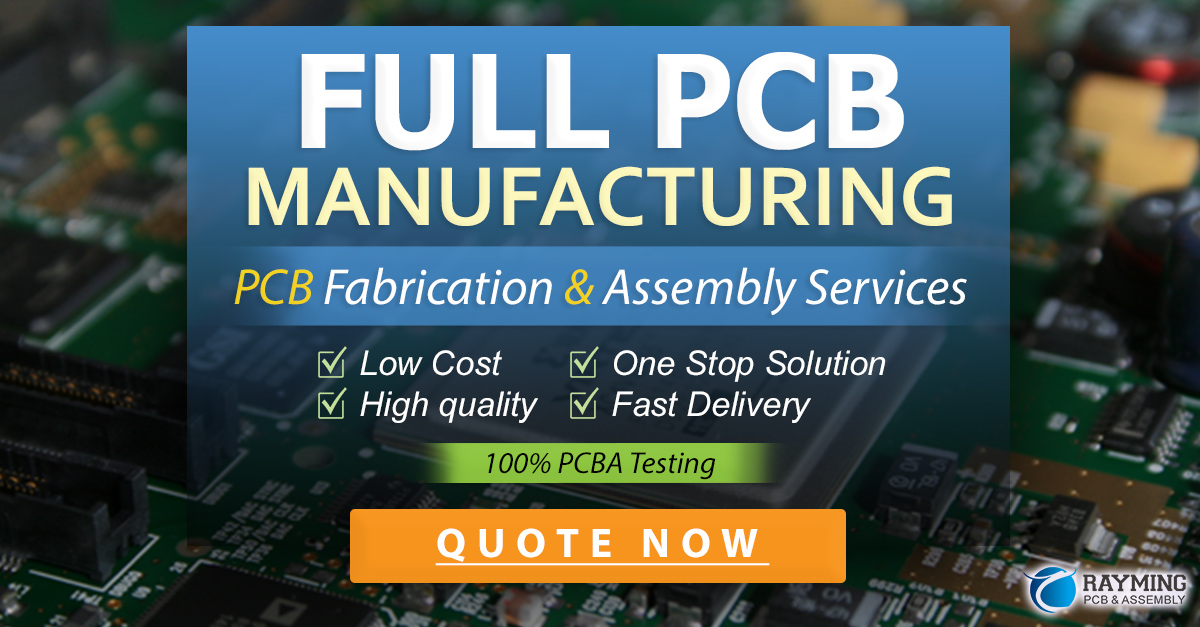
PCB Assembly Techniques
PCB assembly techniques can be broadly categorized into two main types: through-hole assembly and surface mount assembly.
1. Through-Hole Assembly
Through-hole assembly involves inserting component leads through drilled holes in the PCB and soldering them to pads on the opposite side. This technique is suitable for larger components and provides a strong mechanical connection. However, it requires more board space and is generally slower than surface mount assembly.
2. Surface Mount Assembly
Surface mount assembly involves placing components directly onto pads on the PCB surface and soldering them in place. This technique enables higher component density, faster assembly, and improved high-frequency performance. Surface mount assembly is the most common method used in modern PCB manufacturing.
Quality Control and Testing
Ensuring the quality and reliability of PCBs is crucial for the performance and longevity of electronic devices. Several quality control and testing methods are employed throughout the PCB manufacturing process, including:
-
Visual Inspection: PCBs are visually inspected for defects, such as misaligned components, solder bridges, or damaged traces.
-
Automated Optical Inspection (AOI): AOI systems use high-resolution cameras and image processing algorithms to detect assembly defects, such as missing or misplaced components.
-
X-Ray Inspection: X-ray imaging is used to inspect solder joints and internal structures of the PCB, particularly for multi-layer boards and BGAs (Ball Grid Arrays).
-
In-Circuit Testing (ICT): ICT involves using a bed-of-nails fixture to make electrical contact with specific points on the PCB and test the functionality of individual components and circuits.
-
Functional Testing: The assembled PCB is tested under real-world operating conditions to ensure that it performs as intended and meets the specified requirements.
PCB Manufacturing Capabilities
PCB manufacturers offer a wide range of capabilities to meet the diverse needs of electronic product development. Some key capabilities include:
-
Quick-Turn Prototyping: Many PCB manufacturers offer rapid prototyping services, providing fast turnaround times for small batches of PCBs, enabling product development teams to test and iterate their designs quickly.
-
High-Volume Production: PCB manufacturers with advanced facilities and automation can handle high-volume production, ensuring consistent quality and timely delivery for large-scale projects.
-
Customization and Special Requirements: PCB manufacturers can accommodate special requirements, such as unique materials, finishes, or tolerances, to meet the specific needs of a project.
-
Design Support and Consultation: Many PCB manufacturers offer design support and consultation services, assisting customers in optimizing their PCB designs for manufacturability, reliability, and cost-effectiveness.
Future Trends in PCB Manufacturing
As electronic devices continue to evolve and become more complex, PCB manufacturing technologies and capabilities must adapt to meet new challenges. Some future trends in PCB manufacturing include:
-
Miniaturization: The demand for smaller, more compact electronic devices will drive the development of advanced PCB manufacturing techniques, such as ultra-fine pitch components and 3D packaging.
-
High-Speed and High-Frequency: As data rates and signal frequencies continue to increase, PCB manufacturers will need to develop new materials and design techniques to maintain signal integrity and minimize electromagnetic interference.
-
Sustainability and Green Manufacturing: There is a growing focus on environmentally friendly PCB manufacturing processes, such as lead-free soldering, halogen-free materials, and recycling of waste materials.
-
Industry 4.0 and Automation: The adoption of Industry 4.0 technologies, such as AI, machine learning, and robotics, will enable more efficient, flexible, and data-driven PCB manufacturing processes.
Frequently Asked Questions (FAQ)
-
What is the difference between a PCB and a PCBA?
A PCB (Printed Circuit Board) is the bare board with etched copper traces, while a PCBA (Printed Circuit Board Assembly) is a PCB with electronic components assembled onto it. -
How long does it take to manufacture a PCB?
The lead time for PCB manufacturing varies depending on the complexity of the design, the manufacturing process, and the quantity ordered. Quick-turn prototyping can take as little as 24 hours, while high-volume production may require several weeks. -
What is the minimum feature size achievable in PCB manufacturing?
The minimum feature size depends on the PCB manufacturing technology used. For standard PCBs, the minimum trace width and spacing are typically around 0.15mm (6 mil). High-density PCBs can achieve trace widths and spacing as small as 0.05mm (2 mil) or less. -
What is the difference between rigid and flexible PCBs?
Rigid PCBs are made of a solid substrate material, such as FR-4, and are designed to maintain a fixed shape. Flexible PCBs are made of a flexible substrate, such as polyimide, and can bend and conform to various shapes. -
How can I ensure the quality and reliability of my PCBs?
To ensure the quality and reliability of your PCBs, work with a reputable PCB manufacturer that follows industry standards and best practices. Provide clear and accurate design files, communicate your requirements effectively, and consider implementing quality control measures, such as testing and inspection, throughout the manufacturing process.
Conclusion
PCB manufacturing is a critical aspect of electronic product development, enabling the creation of high-quality, reliable, and innovative electronic devices. By understanding the manufacturing capabilities, processes, and technologies involved in PCB and PCB assembly, product development teams can make informed decisions and collaborate effectively with PCB manufacturers to bring their designs to life.
As the electronics industry continues to evolve, PCB manufacturing will face new challenges and opportunities. By staying at the forefront of technological advancements and adopting best practices in design, fabrication, and assembly, PCB manufacturers can support the development of the next generation of electronic products.
PCB Manufacturing Process | Key Steps |
---|---|
PCB Design and Layout | – Circuit design – PCB layout – Component placement – Trace routing |
PCB Fabrication | – Substrate preparation – Copper cladding – Drilling – Patterning – Plating – Solder mask application – Silkscreen printing |
PCB Assembly | – Solder paste application – Component placement – Reflow soldering – Inspection and testing |
PCB Assembly Techniques | Description |
---|---|
Through-Hole Assembly | – Components inserted through drilled holes – Soldered to pads on the opposite side – Suitable for larger components – Stronger mechanical connection |
Surface Mount Assembly | – Components placed directly onto pads on the PCB surface – Soldered in place – Higher component density – Faster assembly – Improved high-frequency performance |
By leveraging advanced manufacturing capabilities and following best practices in PCB design and assembly, electronic product development teams can create innovative, reliable, and high-performance products that meet the evolving needs of the market.
No responses yet