Introduction to PCB Manufacturing
Printed Circuit Board (PCB) manufacturing is a crucial process in the electronics industry. It involves the creation of a board that connects electronic components using conductive tracks, pads, and other features etched from copper sheets laminated onto a non-conductive substrate. PCBs are used in almost all electronic devices, from smartphones and computers to medical equipment and aerospace systems.
In this comprehensive guide, we will dive deep into the world of PCB manufacturing, covering everything from the basics of PCB design to the advanced techniques used in modern PCB fabrication. Whether you are an electronics enthusiast, a professional engineer, or a curious learner, this guide will provide you with the knowledge and insights you need to understand and appreciate the complex process of PCB manufacturing.
The Basics of PCB Design
Before we delve into the manufacturing process, let’s first understand the fundamentals of PCB design. A well-designed PCB is essential for the proper functioning and reliability of an electronic device.
PCB Layers
PCBs can be classified based on the number of layers they contain. The most common types are:
- Single-layer PCB: A single-layer PCB has conductive traces on one side of the substrate.
- Double-layer PCB: A double-layer PCB has conductive traces on both sides of the substrate.
- Multi-layer PCB: A multi-layer PCB has conductive traces on multiple layers, separated by insulating layers.
The choice of PCB layer depends on the complexity of the circuit, the required functionality, and the space constraints of the device.
PCB Material
The base material used for PCBs is typically a non-conductive substrate, such as FR-4, which is a composite material made of woven fiberglass cloth with an epoxy resin binder. Other common PCB materials include:
- Polyimide: A flexible, high-temperature material used in flexible PCBs.
- Ceramic: A high-performance material used in high-frequency and high-temperature applications.
- Aluminum: A metal-based material used for heat dissipation in high-power applications.
The choice of PCB material depends on the electrical, mechanical, and thermal requirements of the device.
PCB Components
A PCB consists of various components that work together to create a functional circuit. The main components of a PCB are:
- Conductive traces: The copper pathways that carry electrical signals between components.
- Pads: The conductive areas where components are soldered onto the board.
- Vias: The conductive holes that allow signals to pass between layers in a multi-layer PCB.
- Solder mask: A protective layer that covers the copper traces, leaving only the pads and vias exposed.
- Silkscreen: A printed layer that provides information about the components and their placement on the board.
The PCB Manufacturing Process
Now that we have a basic understanding of PCB design, let’s explore the manufacturing process in detail.
Step 1: PCB Design and Preparation
The first step in PCB manufacturing is to create a design using specialized software, such as Altium Designer or KiCad. The design includes the schematic diagram, component placement, and routing of the conductive traces. Once the design is complete, it is converted into a set of files, typically Gerber files, that contain all the necessary information for manufacturing.
Step 2: PCB Fabrication
The PCB fabrication process consists of several substeps:
- Copper Cladding: A thin layer of copper is laminated onto the non-conductive substrate, providing a conductive surface for the circuit.
- Drilling: Holes are drilled through the substrate to create vias and mounting holes for components.
- Patterning: The copper layer is patterned using a photolithographic process, which involves applying a photoresist layer, exposing it to UV light through a photomask, and etching away the unwanted copper.
- Plating: The exposed copper is electroplated with additional copper to increase the thickness of the traces and pads.
- Solder Mask Application: A solder mask layer is applied to the board, covering the copper traces but leaving the pads and vias exposed.
- Silkscreen Printing: The silkscreen layer is printed onto the board, providing information about the components and their placement.
Step 3: PCB Assembly
Once the PCB is fabricated, the components need to be assembled onto the board. This process can be done manually or using automated machines, depending on the volume and complexity of the board.
- Solder Paste Application: A solder paste, which is a mixture of tiny solder particles and flux, is applied to the pads using a stencil or a screen-printing process.
- Component Placement: The components are placed onto the board, either manually or using a pick-and-place machine.
- Reflow Soldering: The board is heated in a reflow oven, melting the solder paste and forming a permanent connection between the components and the pads.
Step 4: PCB Testing and Inspection
After assembly, the PCB undergoes a series of tests and inspections to ensure its functionality and reliability.
- Visual Inspection: The board is visually inspected for any defects, such as missing components, solder bridges, or damaged traces.
- Automated Optical Inspection (AOI): An AOI machine uses high-resolution cameras to inspect the board for any defects that may not be visible to the naked eye.
- X-Ray Inspection: For multi-layer PCBs or boards with hidden components, an X-ray inspection may be performed to check for internal defects or voids in the solder joints.
- Electrical Testing: The board is powered up and tested for its electrical functionality, ensuring that all components are working as intended.
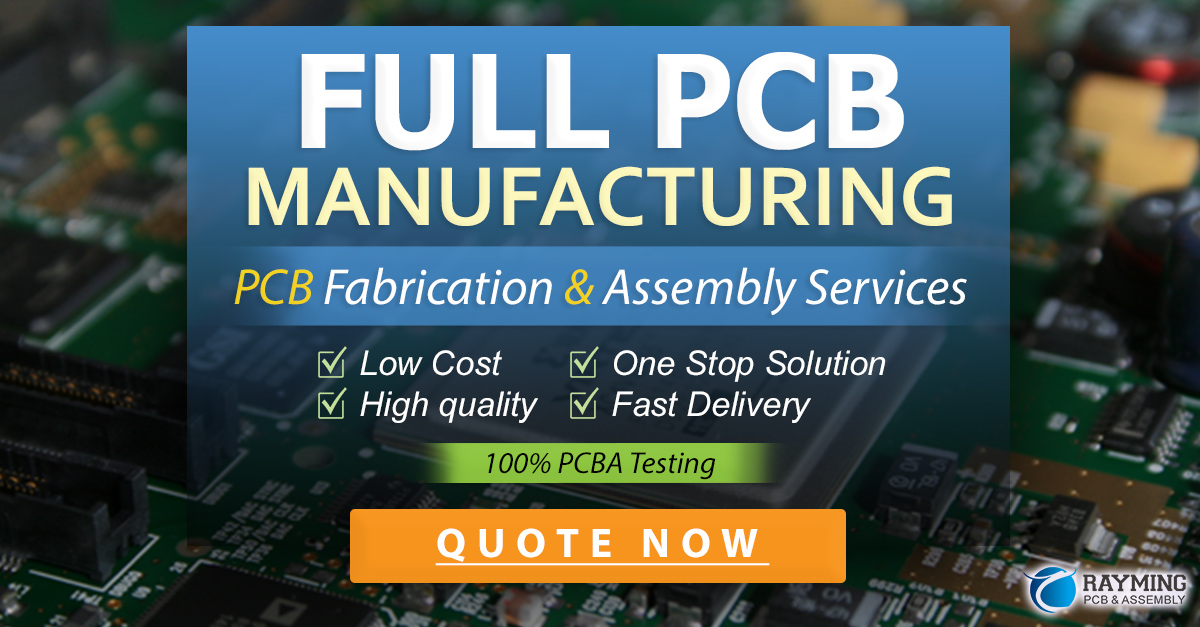
Advanced PCB Manufacturing Techniques
As electronic devices become more complex and compact, PCB manufacturing techniques have evolved to keep pace with the increasing demands. Here are some advanced techniques used in modern PCB manufacturing:
High-Density Interconnect (HDI) PCBs
HDI PCBs are designed to accommodate a high number of components in a small space. They use fine-pitch traces, micro vias, and buried and blind vias to achieve higher density and improved signal integrity.
Flexible PCBs
Flexible PCBs are made of flexible materials, such as polyimide, that allow the board to bend and flex without breaking. They are commonly used in wearable devices, medical equipment, and aerospace applications.
Rigid-Flex PCBs
Rigid-flex PCBs combine the benefits of rigid and flexible PCBs, allowing for a more compact and reliable design. They consist of rigid sections connected by flexible sections, enabling three-dimensional packaging and reducing the need for connectors and cables.
Embedded PCBs
Embedded PCBs have components embedded within the layers of the board, rather than mounted on the surface. This technique allows for a more compact and efficient design, as well as improved thermal management and signal integrity.
PCB Manufacturing Standards and Certifications
To ensure the quality and reliability of PCBs, manufacturers adhere to various industry standards and certifications. Some of the most common standards are:
- IPC-A-600: Acceptability of Printed Boards
- IPC-6012: Qualification and Performance Specification for Rigid Printed Boards
- IPC-6013: Qualification and Performance Specification for Flexible Printed Boards
- UL 94: Standard for Safety of Flammability of Plastic Materials
Manufacturers may also obtain certifications, such as ISO 9001 for quality management systems or AS9100 for aerospace applications, to demonstrate their commitment to quality and reliability.
Frequently Asked Questions (FAQ)
- What is the difference between a PCB and a PCBA?
-
A PCB (Printed Circuit Board) is the bare board without any components assembled onto it. A PCBA (Printed Circuit Board Assembly) is a PCB with all the components soldered onto it, making it a complete functional unit.
-
How long does it take to manufacture a PCB?
-
The lead time for PCB manufacturing varies depending on the complexity of the board, the volume of the order, and the manufacturer’s capacity. Typically, a simple PCB can be manufactured within 1-2 weeks, while a complex, high-volume order may take several weeks or even months.
-
What is the minimum feature size that can be achieved in PCB manufacturing?
-
The minimum feature size depends on the capabilities of the manufacturer and the PCB technology used. For standard PCBs, the minimum trace width and spacing is typically around 4-6 mils (0.1-0.15 mm). For HDI PCBs, the minimum feature size can be as small as 1-2 mils (0.025-0.05 mm).
-
How can I ensure the quality of my PCBs?
-
To ensure the quality of your PCBs, choose a reputable manufacturer that adheres to industry standards and has a proven track record of quality and reliability. Provide clear and detailed design files, and communicate your requirements and expectations to the manufacturer. Perform thorough testing and inspection of the boards before finalizing the production.
-
What is the cost of PCB manufacturing?
- The cost of PCB manufacturing depends on various factors, such as the size and complexity of the board, the material used, the number of layers, the volume of the order, and the location of the manufacturer. As a rough estimate, a simple, single-layer PCB may cost around $0.50-$1 per square inch, while a complex, multi-layer PCB can cost several dollars per square inch.
Conclusion
PCB manufacturing is a complex and fascinating process that plays a crucial role in the electronics industry. From the basics of PCB design to the advanced techniques used in modern fabrication, this comprehensive guide has covered the essential aspects of PCB manufacturing.
As technology continues to evolve, PCB manufacturing will undoubtedly adapt and innovate to meet the growing demands for smaller, faster, and more reliable electronic devices. By understanding the fundamentals of PCB manufacturing and staying up-to-date with the latest trends and techniques, electronics professionals and enthusiasts can contribute to the ongoing advancement of this vital industry.
PCB Type | Layers | Typical Applications |
---|---|---|
Single-layer PCB | 1 | Simple circuits, low-cost devices |
Double-layer PCB | 2 | Most common type, used in a wide range of devices |
Multi-layer PCB | 4, 6, 8, or more | Complex circuits, high-speed devices, compact designs |
Flexible PCB | Varies | Wearable devices, medical equipment, aerospace applications |
Rigid-Flex PCB | Varies | 3D packaging, devices requiring both rigid and flexible sections |
PCB Material | Characteristics | Typical Applications |
---|---|---|
FR-4 | Low-cost, good mechanical and electrical properties | Most common material, used in a wide range of devices |
Polyimide | Flexible, high-temperature resistance | Flexible PCBs, wearable devices, aerospace applications |
Ceramic | High-frequency, high-temperature resistance | RF and microwave circuits, high-power applications |
Aluminum | Excellent thermal conductivity | High-power applications, LED lighting |
No responses yet