Understanding the PCB Assembly Process
Before diving into the preparation phase, it is important to grasp the fundamentals of the PCB assembly process. PCB assembly involves several stages, including:
- PCB Design and Layout
- PCB Fabrication
- Component Sourcing and Procurement
- PCB Assembly (SMT and THT)
- Testing and Quality Control
Each stage plays a vital role in the overall success of your PCB assembly project. By understanding these stages, you can better plan and prepare for the challenges that may arise during the process.
PCB Design and Layout Considerations
The first step in preparing for PCB assembly is to ensure that your PCB design and layout are optimized for manufacturability. Here are some key considerations to keep in mind:
Choosing the Right PCB Size and Shape
When designing your PCB, consider the size and shape that best suits your application. Common PCB sizes and shapes include:
PCB Size | Dimensions (mm) |
---|---|
Small | 25 x 25 |
Medium | 50 x 50 |
Large | 100 x 100 |
Extra Large | 200 x 200 |
Choose a size that accommodates all your components while minimizing excess space to reduce manufacturing costs.
Designing for Manufacturing (DFM)
Designing for Manufacturing (DFM) is a crucial aspect of PCB design. DFM involves adhering to certain guidelines and best practices to ensure that your PCB can be manufactured efficiently and reliably. Some key DFM considerations include:
- Maintaining appropriate trace widths and spacings
- Avoiding sharp angles and using curved traces
- Providing sufficient clearance between components
- Using standard component sizes and footprints
- Minimizing the number of layers to reduce complexity and cost
By following DFM guidelines, you can minimize the risk of manufacturing defects and delays, ultimately saving time and money in the long run.
Creating a Bill of Materials (BOM)
A Bill of Materials (BOM) is a comprehensive list of all the components required for your PCB assembly. It includes information such as part numbers, quantities, and specifications. Creating an accurate BOM is essential for ensuring that you have all the necessary components on hand before starting the assembly process.
When creating your BOM, consider the following:
- Use consistent part numbering and naming conventions
- Specify the manufacturer and supplier for each component
- Include detailed specifications, such as component values and tolerances
- Double-check the quantities to avoid shortages or excess inventory
An accurate and well-organized BOM will streamline your component sourcing and procurement process, saving you time and reducing the risk of errors.
Component Sourcing and Procurement
Once you have finalized your PCB design and created a comprehensive BOM, the next step is to source and procure the necessary components. Here are some key considerations for component sourcing and procurement:
Choosing Reliable Suppliers
Selecting reliable suppliers is crucial for ensuring the quality and availability of your components. When choosing suppliers, consider the following factors:
- Reputation and track record
- Quality control processes
- Lead times and availability
- Pricing and minimum order quantities (MOQs)
- Customer support and technical assistance
Building relationships with trusted suppliers can help you secure high-quality components at competitive prices while minimizing the risk of supply chain disruptions.
Verifying Component Compatibility
Before purchasing components, it is essential to verify their compatibility with your PCB design and manufacturing process. Some key factors to consider include:
- Package type and footprint
- Electrical specifications and tolerances
- Temperature ratings and operating conditions
- RoHS compliance and environmental regulations
Double-checking component compatibility can help you avoid costly rework and delays due to incompatible or substandard components.
Managing Inventory and Lead Times
Effective inventory management is crucial for ensuring a smooth and efficient PCB assembly process. When managing your component inventory, consider the following:
- Establish minimum and maximum stock levels based on your production needs
- Monitor lead times and plan your orders accordingly
- Use inventory management software to track stock levels and reorder points
- Implement a first-in, first-out (FIFO) system to minimize the risk of component obsolescence
By proactively managing your inventory and lead times, you can avoid production delays and minimize the risk of component shortages or excess inventory.
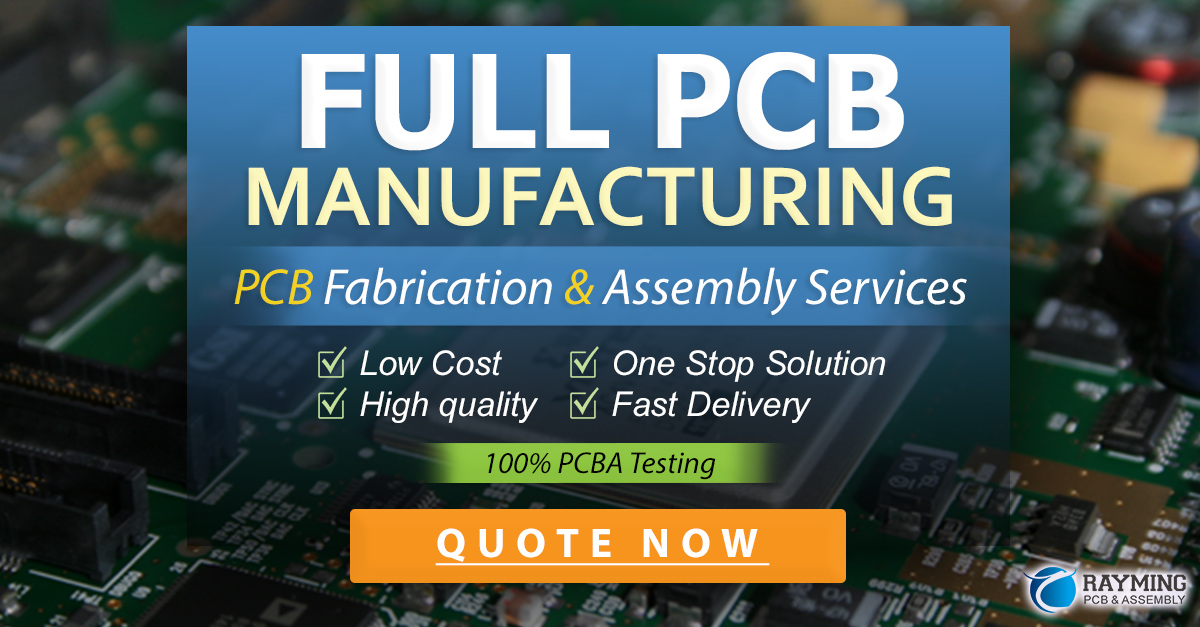
PCB Assembly Preparation
With your components sourced and procured, it’s time to prepare for the actual PCB assembly process. Here are some key steps to ensure a smooth and successful assembly:
Preparing the Assembly Workspace
A clean and organized workspace is essential for efficient and accurate PCB assembly. When preparing your assembly workspace, consider the following:
- Ensure adequate lighting and ventilation
- Provide a stable and ESD-safe work surface
- Organize tools and equipment for easy access
- Implement proper ESD protection measures, such as grounding straps and mats
A well-prepared workspace will enhance your productivity and minimize the risk of assembly errors and damage to your components.
Inspecting and Kitting Components
Before starting the assembly process, it is crucial to inspect and kit your components. This involves:
- Visually inspecting components for damage or defects
- Verifying component values and specifications against your BOM
- Sorting and organizing components by type and value
- Creating kits for each PCB assembly, including all necessary components
Thorough inspection and kitting of components can help you identify any issues early on and ensure a more efficient and accurate assembly process.
Preparing Solder Paste and Stencils
If your PCB assembly involves surface mount technology (SMT), you will need to prepare solder paste and stencils. Here are some key considerations:
- Choose a solder paste with the appropriate alloy composition and particle size
- Ensure that your solder paste is within its shelf life and has been stored properly
- Design and fabricate a high-quality stencil with the correct aperture sizes and shapes
- Perform regular maintenance on your solder paste printer to ensure consistent deposits
Proper preparation of solder paste and stencils is essential for achieving reliable and high-quality solder joints during the SMT assembly process.
Testing and Quality Control
After completing the PCB assembly process, it is crucial to perform thorough testing and quality control to ensure that your board functions as intended. Here are some key steps in the testing and quality control process:
Visual Inspection
The first step in testing and quality control is a visual inspection of the assembled PCB. This involves:
- Checking for proper component placement and orientation
- Inspecting solder joints for any defects, such as bridges or insufficient solder
- Verifying that all components are present and accounted for
- Looking for any signs of physical damage or contamination
A thorough visual inspection can help you identify any obvious assembly issues that may impact the functionality or reliability of your PCB.
Electrical Testing
After visual inspection, electrical testing is performed to verify that your PCB functions as designed. This may include:
- Continuity testing to ensure proper electrical connections
- Resistance testing to verify component values
- Power-on testing to check for proper voltage levels and current draw
- Functional testing to validate that the PCB performs its intended functions
Electrical testing helps to identify any issues related to component functionality, circuit design, or assembly quality.
Automated Optical Inspection (AOI)
For larger production runs or more complex PCBs, Automated Optical Inspection (AOI) can be used to streamline the quality control process. AOI systems use high-resolution cameras and advanced algorithms to detect assembly defects, such as:
- Component placement errors
- Solder joint defects
- Missing or incorrect components
- Polarity issues
AOI can quickly and accurately identify assembly issues, reducing the need for manual inspection and improving overall quality control efficiency.
Burn-In and Stress Testing
In some cases, it may be necessary to perform additional testing to ensure the long-term reliability of your PCBs. This can include:
- Burn-in testing, where PCBs are subjected to elevated temperatures and operating conditions to identify early failures
- Stress testing, where PCBs are exposed to various environmental factors, such as vibration, shock, or humidity, to verify their durability
Burn-in and stress testing can help you identify potential reliability issues and ensure that your PCBs can withstand the rigors of their intended operating environment.
Frequently Asked Questions (FAQ)
- What is the difference between SMT and THT assembly?
-
SMT (Surface Mount Technology) involves placing components directly onto the surface of the PCB, while THT (Through-Hole Technology) involves inserting component leads through holes in the PCB and soldering them on the opposite side.
-
How do I choose the right solder paste for my PCB assembly?
-
When selecting a solder paste, consider factors such as the alloy composition (e.g., lead-free or leaded), particle size, and melting temperature. Consult with your PCB assembly provider or solder paste manufacturer for guidance based on your specific requirements.
-
What are some common PCB assembly defects to watch out for?
-
Common PCB assembly defects include solder bridges, insufficient or excessive solder, component misalignment, tombstoning (components standing on end), and damaged or missing components. Thorough inspection and testing can help identify these issues.
-
How can I minimize the risk of ESD damage during PCB assembly?
-
To minimize the risk of ESD (Electrostatic Discharge) damage, implement proper ESD protection measures, such as using grounded wrist straps, ESD-safe mats and flooring, and ESD-safe packaging for components. Train personnel in ESD safety practices and maintain a clean, organized workspace.
-
What should I do if I encounter issues during the PCB assembly process?
- If you encounter issues during PCB assembly, first, document the problem and gather as much information as possible. Consult with experienced colleagues or your PCB assembly provider for guidance. Implement corrective actions, such as rework or redesign, as necessary, and incorporate lessons learned into future projects to prevent similar issues from recurring.
By understanding and preparing for each stage of the PCB assembly process, you can minimize the risk of errors, delays, and quality issues, ultimately leading to a successful and reliable end product.
No responses yet