Introduction to OSP PCB Finish
Organic Solderability Preservative (OSP) is a popular surface finish used in the manufacturing of printed circuit boards (PCBs). It is a thin, clear organic coating applied to the copper pads and through-holes of a PCB to protect them from oxidation and enhance solderability. OSP PCB finish has gained popularity due to its cost-effectiveness, environmental friendliness, and compatibility with various soldering processes.
How OSP Works
OSP is typically applied through a dipping process, where the PCB is immersed in an OSP solution. The organic compounds in the solution form a protective layer on the copper surfaces, preventing oxidation and ensuring good solderability. The OSP coating is usually around 0.2 to 0.5 microns thick and does not significantly affect the dimensions of the PCB features.
Composition of OSP
The exact composition of OSP varies among manufacturers, but it generally consists of a blend of organic compounds, such as benzimidazoles, benzotriazoles, and imidazoles. These compounds form a complex with the copper surface, creating a barrier against oxidation while allowing for good wettability during the soldering process.
Advantages of OSP PCB Finish
Cost-effectiveness
One of the primary advantages of OSP is its cost-effectiveness compared to other PCB finishes like ENIG (Electroless Nickel Immersion Gold) or HASL (Hot Air Solder Leveling). The application process for OSP is relatively simple and does not require expensive materials or equipment, making it an attractive option for budget-conscious projects.
Environmental Friendliness
OSP is considered an environmentally friendly PCB finish as it does not contain lead or other harmful substances. The organic compounds used in OSP are biodegradable and do not pose a significant threat to the environment. This makes OSP a good choice for companies looking to reduce their environmental impact and comply with regulations such as RoHS (Restriction of Hazardous Substances).
Good Solderability
OSP provides excellent solderability, ensuring reliable connections between components and the PCB. The organic coating allows for good wetting of the solder, resulting in strong and consistent solder joints. OSP is compatible with various soldering processes, including reflow soldering, wave soldering, and hand soldering.
Flat Surface Finish
Unlike HASL, which can result in uneven surfaces due to the hot air leveling process, OSP provides a flat and uniform surface finish. This is particularly important for fine-pitch components and high-density PCB designs, where a flat surface is crucial for proper component placement and soldering.
Ease of Inspection
OSP is a transparent coating, allowing for easy visual inspection of the PCB. This enables quick identification of any defects or issues on the copper pads and through-holes, facilitating quality control and troubleshooting processes.
Disadvantages of OSP PCB Finish
Limited Shelf Life
One of the main drawbacks of OSP is its limited shelf life compared to other PCB finishes. The organic coating can degrade over time, especially when exposed to high temperatures and humidity. This degradation can lead to reduced solderability and potential reliability issues. Typically, OSP-coated PCBs have a shelf life of 6 to 12 months, depending on the storage conditions and the specific OSP formulation used.
Sensitivity to Handling
OSP-coated PCBs are more sensitive to handling compared to other finishes. The organic coating can be easily contaminated by skin oils, dirt, and other substances, which can negatively impact solderability. Proper handling procedures, such as using gloves and ensuring a clean work environment, are essential to maintain the integrity of the OSP finish.
Limited Rework Capability
Reworking OSP-coated PCBs can be challenging, as the organic coating is removed during the rework process. This exposes the underlying copper, which can quickly oxidize and degrade solderability. Reworking OSP boards often requires reapplying the OSP coating to the affected areas, which can be time-consuming and may not always yield optimal results.
Not Suitable for High-Temperature Applications
OSP may not be the best choice for high-temperature applications, as the organic coating can break down at elevated temperatures. This can lead to reduced protection against oxidation and compromised solderability. In such cases, other PCB finishes like ENIG or immersion silver may be more suitable.
Potential for Copper Leaching
In some cases, OSP-coated PCBs may be susceptible to copper leaching, especially when exposed to harsh environmental conditions or certain chemical processes. Copper leaching can lead to a reduction in the thickness of the copper pads and traces, potentially affecting the electrical performance and reliability of the PCB.
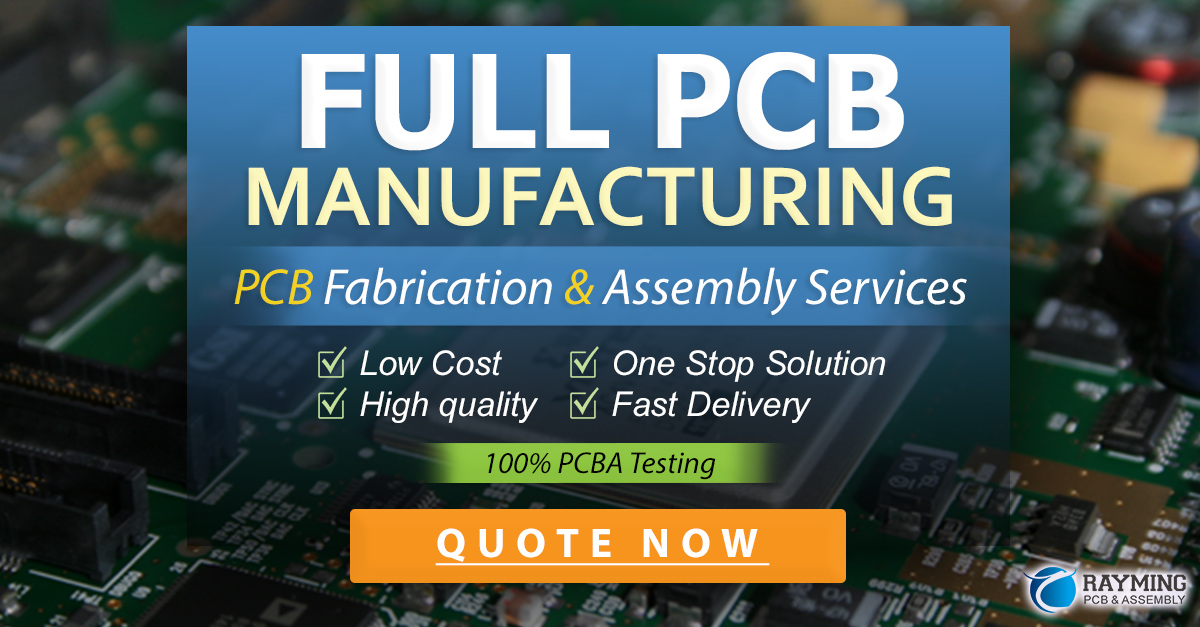
Applications of OSP PCB Finish
OSP is widely used in various electronics applications, particularly those that require cost-effectiveness, good solderability, and environmental friendliness. Some common applications include:
- Consumer electronics
- Automotive electronics
- Industrial control systems
- Medical devices
- Telecommunications equipment
OSP is also suitable for prototyping and low-volume production, as it offers a quick and cost-effective way to protect the copper surfaces of the PCB.
Choosing Between OSP and Other PCB Finishes
When deciding whether to use OSP or another PCB finish, several factors should be considered:
- Cost: OSP is generally more cost-effective than other finishes like ENIG or immersion silver.
- Shelf life: If long shelf life is a priority, ENIG or immersion silver may be better choices.
- Environmental impact: OSP is an environmentally friendly option, while HASL contains lead, and ENIG uses nickel and gold.
- Application requirements: For high-temperature applications or those requiring extended shelf life, OSP may not be the best choice.
- Soldering process: OSP is compatible with most soldering processes, but other finishes may be more suitable for specific soldering techniques.
The table below provides a comparison of OSP with other common PCB finishes:
PCB Finish | Cost | Shelf Life | Environmental Impact | Solderability | Reworkability |
---|---|---|---|---|---|
OSP | Low | Limited (6-12 months) | Low | Good | Limited |
ENIG | High | Extended (12+ months) | Moderate (nickel and gold) | Excellent | Good |
Immersion Silver | Moderate | Extended (12+ months) | Low | Excellent | Good |
HASL | Low | Extended (12+ months) | High (lead content) | Good | Limited |
Proper Handling and Storage of OSP PCBs
To ensure the best performance and reliability of OSP-coated PCBs, proper handling and storage procedures should be followed:
- Handle OSP PCBs with gloves to avoid contamination from skin oils and dirt.
- Store OSP PCBs in a cool, dry environment with a temperature between 20-30°C and relative humidity below 60%.
- Use moisture barrier bags with desiccants for long-term storage to protect against humidity and oxidation.
- Avoid exposing OSP PCBs to direct sunlight or UV light, as this can degrade the organic coating.
- When handling OSP PCBs, use clean tools and work surfaces to minimize the risk of contamination.
By following these guidelines, manufacturers and assemblers can maximize the shelf life and solderability of OSP-coated PCBs.
Frequently Asked Questions (FAQ)
1. What does OSP stand for?
OSP stands for Organic Solderability Preservative. It is a type of surface finish applied to the copper pads and through-holes of a printed circuit board (PCB) to protect against oxidation and enhance solderability.
2. Is OSP environmentally friendly?
Yes, OSP is considered an environmentally friendly PCB finish. It does not contain lead or other harmful substances, and the organic compounds used in OSP are biodegradable.
3. How long does OSP last?
The shelf life of OSP-coated PCBs is typically 6 to 12 months, depending on the storage conditions and the specific OSP formulation used. Proper handling and storage can help maximize the shelf life of OSP PCBs.
4. Can OSP PCBs be reworked?
Reworking OSP-coated PCBs can be challenging, as the organic coating is removed during the rework process. This exposes the underlying copper, which can quickly oxidize and degrade solderability. Reworking OSP boards often requires reapplying the OSP coating to the affected areas.
5. Is OSP suitable for high-temperature applications?
OSP may not be the best choice for high-temperature applications, as the organic coating can break down at elevated temperatures. This can lead to reduced protection against oxidation and compromised solderability. In such cases, other PCB finishes like ENIG or immersion silver may be more suitable.
Conclusion
OSP (Organic Solderability Preservative) is a popular and cost-effective surface finish for printed circuit boards (PCBs). It offers good solderability, environmental friendliness, and a flat surface finish, making it suitable for a wide range of electronics applications. However, OSP has some limitations, such as a limited shelf life, sensitivity to handling, and potential for copper leaching.
When choosing a PCB finish, it is essential to consider the specific requirements of the application, including cost, shelf life, environmental impact, solderability, and reworkability. Proper handling and storage of OSP PCBs are crucial to ensure the best performance and reliability.
As technology advances and environmental regulations evolve, it is likely that OSP and other PCB finishes will continue to be developed and improved. By understanding the advantages and disadvantages of OSP and other finishes, PCB designers and manufacturers can make informed decisions and create high-quality, reliable electronic products.
No responses yet