Types of LED PCB Boards
1. Single Layer LED PCB
Single layer LED PCBs are the most basic type of LED circuit board. They consist of a single conductive layer, usually made of copper, laminated onto an insulating substrate. The components, including LEDs and resistors, are mounted on one side of the board, while the copper traces on the other side connect the components.
Advantages:
- Cost-effective due to simple design and manufacturing process
- Suitable for low-complexity LED applications
- Easy to design and prototype
Applications:
- Simple LED indicators
- Low-power LED lighting systems
- DIY projects and hobbyist applications
2. Double Layer LED PCB
Double layer LED PCBs feature two conductive layers, one on each side of the insulating substrate. The layers are connected through conductive vias, allowing for more complex circuit designs and improved power distribution compared to single layer boards.
Advantages:
- Increased design flexibility and circuit density
- Better power distribution and heat dissipation
- Suitable for medium-complexity LED applications
Applications:
- LED displays and signage
- LED lighting fixtures
- Automotive LED lighting systems
3. Multi-Layer LED PCB
Multi-layer LED PCBs consist of three or more conductive layers separated by insulating layers. These boards offer the highest level of design complexity and circuit density, enabling the integration of numerous components and features.
Advantages:
- High design complexity and circuit density
- Excellent power distribution and signal integrity
- Suitable for advanced LED applications
Applications:
- High-power LED lighting systems
- LED video walls and large displays
- Industrial and commercial LED lighting solutions
4. Flexible LED PCB
Flexible LED PCBs are manufactured using a flexible insulating substrate, such as polyimide or polyester. These boards can bend and conform to various shapes, making them ideal for applications where traditional rigid PCBs are not suitable.
Advantages:
- Conformable and adaptable to different shapes and surfaces
- Lightweight and thin profile
- Resistant to vibration and shock
Applications:
- Wearable LED devices
- Automotive interior LED lighting
- Flexible LED displays and signage
5. Metal Core LED PCB (MCPCB)
Metal Core LED PCBs feature a metal substrate, typically aluminum, which acts as a heat sink. The metal core is covered with a thin layer of dielectric material, followed by a copper circuit layer. MCPCBs are designed to efficiently dissipate heat generated by high-power LEDs, ensuring optimal performance and longevity.
Advantages:
- Excellent thermal management and heat dissipation
- Improved LED performance and lifespan
- Suitable for high-power LED applications
Applications:
- High-power LED lighting fixtures
- LED street lights and floodlights
- LED grow lights for horticulture
6. Rigid-Flex LED PCB
Rigid-flex LED PCBs combine the benefits of both rigid and flexible PCBs. These boards consist of rigid sections connected by flexible sections, allowing for three-dimensional design and improved reliability in applications with limited space or moving parts.
Advantages:
- 3D design capabilities and space savings
- Reduced connectors and improved reliability
- Suitable for applications with limited space or moving components
Applications:
- LED lighting in smart devices and wearables
- Automotive LED lighting systems
- Medical LED devices
LED PCB Materials
The choice of materials for LED PCBs is crucial to ensure optimal performance, reliability, and longevity. Some common materials used in LED PCB manufacturing include:
Material | Description |
---|---|
FR-4 | A popular and cost-effective PCB substrate made from woven fiberglass and epoxy resin. Suitable for most LED applications. |
Aluminum | Used as a substrate in Metal Core PCBs for excellent thermal conductivity and heat dissipation. Ideal for high-power LED applications. |
Polyimide | A flexible and heat-resistant material used in flexible LED PCBs. Offers high durability and conformability. |
Copper | The primary conductive material used for circuit traces and pads on LED PCBs. Offers excellent electrical conductivity. |
LED PCB Design Considerations
When designing LED PCBs, several factors must be taken into account to ensure optimal performance and reliability:
-
Thermal Management: Proper thermal management is essential to prevent overheating and ensure the longevity of LEDs. The PCB design should incorporate adequate heat dissipation techniques, such as the use of metal core substrates, thermal vias, and heat sinks.
-
Power Distribution: LED PCBs must be designed to provide uniform power distribution to all LEDs, minimizing voltage drops and ensuring consistent brightness. This can be achieved through proper trace sizing, copper thicknesses, and the use of power and ground planes.
-
Signal Integrity: Maintaining signal integrity is crucial for LED PCBs, especially in applications with high-speed control signals or dimming functionalities. Proper trace routing, impedance control, and the use of decoupling capacitors can help minimize signal distortion and ensure reliable operation.
-
Component Placement: The placement of LEDs and other components on the PCB should be optimized for thermal management, signal integrity, and ease of assembly. Adequate spacing between components and the use of thermal relief patterns can help improve heat dissipation and manufacturability.
-
Color Consistency: For applications requiring precise color rendering, such as LED displays or architectural lighting, the PCB design must take into account the color consistency of LEDs. This can be achieved through binning techniques, where LEDs with similar color characteristics are grouped together, and through the use of color mixing optics.
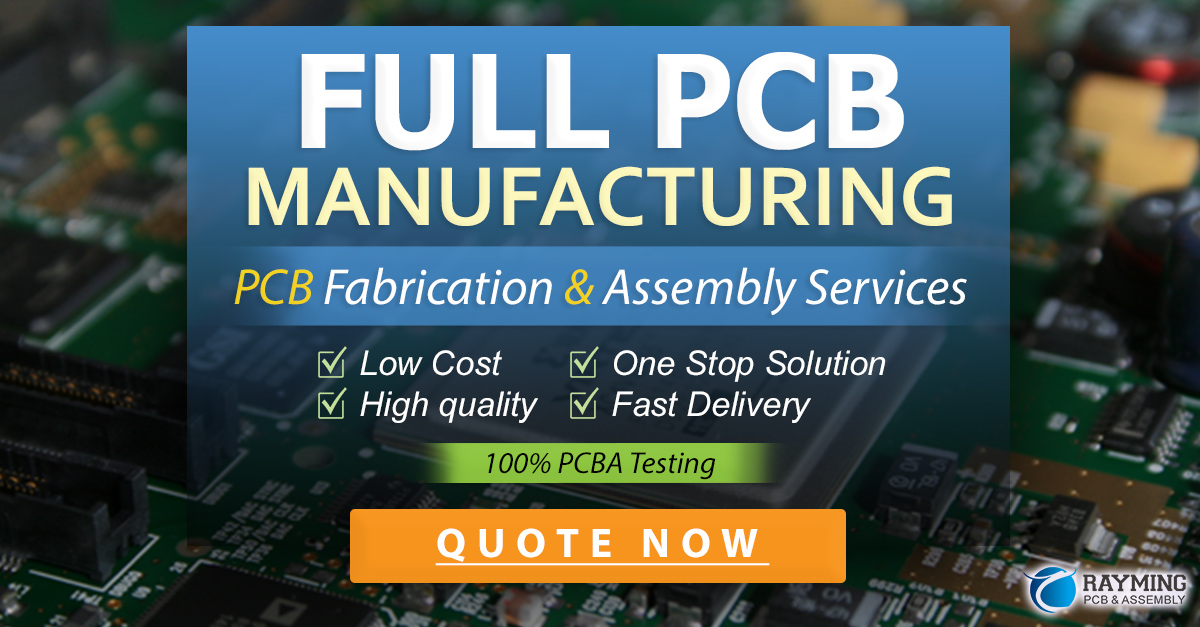
FAQ
-
Q: What is the difference between a single layer and a double layer LED PCB?
A: Single layer LED PCBs have a single conductive layer, while double layer PCBs have two conductive layers, one on each side of the insulating substrate. Double layer PCBs offer increased design flexibility and better power distribution compared to single layer boards. -
Q: What are the advantages of using a metal core LED PCB?
A: Metal core LED PCBs offer excellent thermal management and heat dissipation, thanks to their aluminum substrate. This improves LED performance and lifespan, making metal core PCBs ideal for high-power LED applications. -
Q: Can flexible LED PCBs be used in automotive applications?
A: Yes, flexible LED PCBs are well-suited for automotive applications, particularly for interior lighting and conformable exterior lighting. Their ability to bend and adapt to different shapes makes them ideal for integration into various automotive components. -
Q: What is the role of copper in LED PCBs?
A: Copper is the primary conductive material used for circuit traces and pads on LED PCBs. It offers excellent electrical conductivity, allowing for efficient power distribution and signal transmission. -
Q: Why is thermal management important in LED PCB design?
A: Proper thermal management is crucial in LED PCB design to prevent overheating and ensure the longevity of LEDs. Overheating can lead to reduced performance, color shifts, and premature failure of LEDs. Effective thermal management techniques, such as the use of metal core substrates and heat sinks, help dissipate heat and maintain optimal LED performance.
Conclusion
LED PCBs are essential components in a wide range of LED lighting applications, from simple indicators to complex illumination systems. The six types of LED PCBs discussed in this article – single layer, double layer, multi-layer, flexible, metal core, and rigid-flex – each offer unique features and benefits tailored to specific application requirements.
When designing LED PCBs, careful consideration must be given to thermal management, power distribution, signal integrity, component placement, and color consistency. By understanding the characteristics and advantages of different LED PCB Types and following best design practices, engineers and manufacturers can create high-performance, reliable, and efficient LED lighting solutions for various industries and applications.
As LED technology continues to advance, the development of innovative LED PCB designs and materials will play a crucial role in enabling new possibilities in energy-efficient lighting, display technology, and beyond.
No responses yet