Introduction to High-TG PCB
High-Tg PCB, also known as High Glass Transition Temperature PCB, is a type of printed circuit board that offers superior thermal stability and mechanical properties compared to standard PCBs. The term “Tg” refers to the glass transition temperature, which is the temperature at which the polymer substrate of the PCB transitions from a rigid, glassy state to a more flexible, rubbery state. High-Tg PCBs are designed to withstand higher temperatures and maintain their structural integrity under harsh environmental conditions.
What Makes High-Tg PCB Different?
The primary difference between High-Tg PCBs and standard PCBs lies in the materials used for the substrate. High-Tg PCBs utilize advanced polymer materials, such as polyimide or high-performance epoxy resins, which have a higher glass transition temperature compared to the traditional FR-4 substrate used in standard PCBs. These materials provide several advantages, including:
- Enhanced thermal stability
- Improved mechanical strength
- Lower thermal expansion
- Better electrical performance
- Increased resistance to moisture and chemicals
Applications of High-Tg PCB
High-Tg PCBs find applications in various industries where electronic devices are subjected to extreme temperatures, harsh environments, or high-reliability requirements. Some common applications include:
- Automotive electronics
- Aerospace and defense systems
- Industrial control and automation
- Medical devices
- Telecommunications equipment
- Power electronics
- Oil and gas exploration
- Renewable energy systems
Benefits of Using High-Tg PCB
Thermal Stability
One of the primary benefits of using High-Tg PCBs is their exceptional thermal stability. The advanced polymer materials used in High-Tg PCBs can withstand higher operating temperatures without deteriorating or losing their mechanical properties. This thermal stability is crucial for electronic devices that operate in high-temperature environments, such as automotive engine compartments, industrial machinery, or aerospace applications.
The table below compares the glass transition temperatures (Tg) of common PCB substrate materials:
Material | Glass Transition Temperature (Tg) |
---|---|
Standard FR-4 | 130°C – 140°C |
High-Tg FR-4 | 170°C – 180°C |
Polyimide | 250°C – 300°C |
High-Performance Epoxy | 180°C – 220°C |
As evident from the table, High-Tg PCB materials have significantly higher glass transition temperatures compared to standard FR-4, enabling them to maintain their structural integrity and performance at elevated temperatures.
Mechanical Strength and Durability
High-Tg PCBs exhibit superior mechanical strength and durability compared to standard PCBs. The advanced polymer materials used in High-Tg PCBs provide better resistance to vibration, shock, and physical stress. This enhanced mechanical stability is particularly important for electronic devices that are subjected to harsh environmental conditions or frequent handling.
Moreover, High-Tg PCBs have lower thermal expansion coefficients compared to standard PCBs. This means that they experience less dimensional change when exposed to temperature fluctuations, reducing the risk of warpage, delamination, or cracking of the PCB. The improved mechanical properties of High-Tg PCBs contribute to the overall reliability and longevity of electronic devices.
Electrical Performance
High-Tg PCBs offer excellent electrical performance, making them suitable for high-speed and high-frequency applications. The advanced polymer materials used in High-Tg PCBs have lower dielectric constants and lower dissipation factors compared to standard FR-4. This translates to reduced signal loss, improved signal integrity, and better high-frequency performance.
The table below compares the electrical properties of common PCB substrate materials:
Material | Dielectric Constant (at 1 GHz) | Dissipation Factor (at 1 GHz) |
---|---|---|
Standard FR-4 | 4.2 – 4.5 | 0.02 – 0.03 |
High-Tg FR-4 | 4.0 – 4.3 | 0.01 – 0.02 |
Polyimide | 3.2 – 3.5 | 0.002 – 0.005 |
High-Performance Epoxy | 3.8 – 4.2 | 0.008 – 0.015 |
As shown in the table, High-Tg PCB materials have lower dielectric constants and dissipation factors, which contribute to better electrical performance. This makes High-Tg PCBs suitable for applications that require high-speed data transmission, low signal distortion, and minimal power loss.
Environmental Resistance
High-Tg PCBs exhibit excellent resistance to moisture, chemicals, and other environmental factors. The advanced polymer materials used in High-Tg PCBs have low moisture absorption rates, which helps prevent the degradation of the PCB’s electrical and mechanical properties when exposed to humid environments.
Furthermore, High-Tg PCBs are more resistant to chemical attack compared to standard PCBs. They can withstand exposure to various chemicals, solvents, and oils without suffering from degradation or delamination. This chemical resistance is particularly important for electronic devices used in industrial settings or harsh environments where exposure to aggressive chemicals is common.
Manufacturing Considerations for High-Tg PCB
Material Selection
When designing and manufacturing High-Tg PCBs, material selection is a critical factor. The choice of substrate material depends on the specific requirements of the application, such as the operating temperature range, mechanical stress, and electrical performance needs.
Some common High-Tg PCB substrate materials include:
- High-Tg FR-4: An enhanced version of the standard FR-4 material with a higher glass transition temperature.
- Polyimide: A high-performance polymer material with excellent thermal stability and mechanical properties.
- High-Performance Epoxy: An advanced epoxy resin material with improved thermal and electrical properties.
The selection of the appropriate substrate material should be based on a thorough analysis of the application’s requirements and the trade-offs between cost, performance, and manufacturability.
Fabrication Process
The fabrication process for High-Tg PCBs is similar to that of standard PCBs, but with some additional considerations. Due to the higher thermal stability and mechanical strength of High-Tg PCB materials, the manufacturing process may require adjustments to ensure proper lamination, drilling, and plating.
Some key aspects of the High-Tg PCB fabrication process include:
- Lamination: The lamination process for High-Tg PCBs typically requires higher temperatures and pressures compared to standard PCBs to ensure proper bonding of the layers.
- Drilling: High-Tg PCB materials may be more difficult to drill due to their increased hardness and mechanical strength. Specialized drills and optimized drilling parameters may be necessary to achieve clean and accurate hole formation.
- Plating: The plating process for High-Tg PCBs may require adjustments to accommodate the different thermal expansion properties of the substrate material. Proper control of the plating parameters is essential to ensure good adhesion and conductivity of the copper traces.
Design Considerations
When designing High-Tg PCBs, several factors should be taken into account to ensure optimal performance and reliability. Some key design considerations include:
- Thermal Management: High-Tg PCBs are often used in high-temperature environments, so proper thermal management is crucial. Designers should consider the placement of components, the use of thermal vias, and the selection of appropriate heat dissipation techniques to ensure effective heat transfer and prevent overheating.
- Mechanical Stress: High-Tg PCBs are subjected to mechanical stress during assembly and operation. Designers should consider the placement of components, the use of reinforcement techniques, and the selection of appropriate mounting methods to minimize mechanical stress and prevent damage to the PCB.
- Signal Integrity: High-Tg PCBs are suitable for high-speed and high-frequency applications, so signal integrity is a critical consideration. Designers should carefully route the traces, minimize crosstalk and electromagnetic interference, and use appropriate impedance matching techniques to ensure good signal quality and minimize signal distortion.
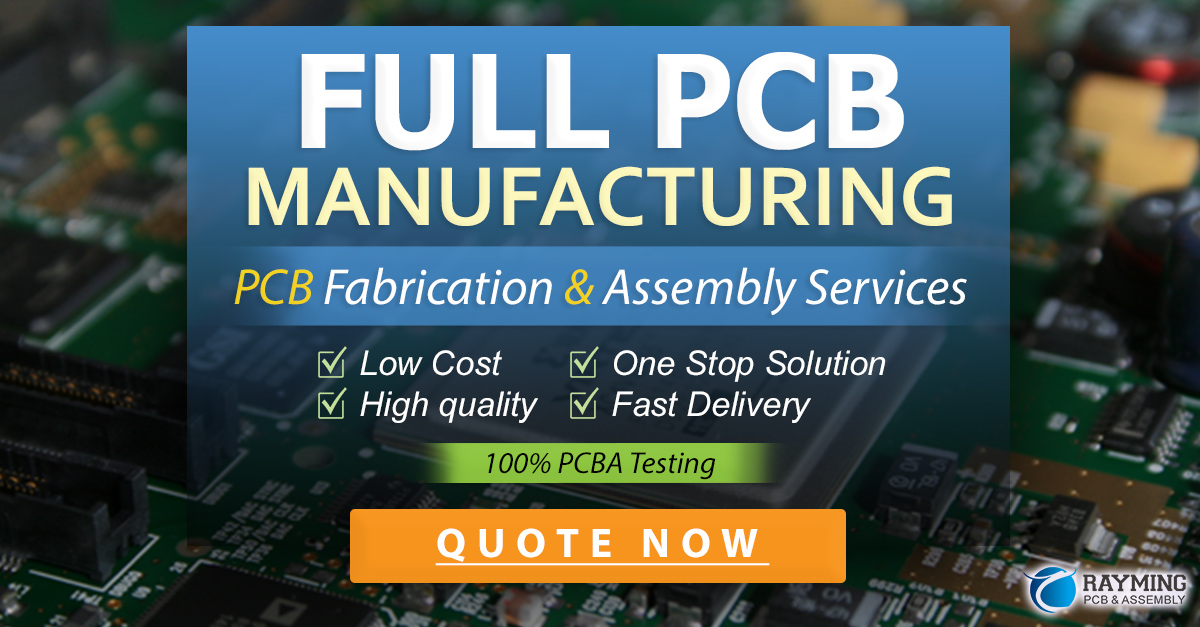
Frequently Asked Questions (FAQ)
- What is the difference between High-Tg PCB and standard PCB?
-
High-Tg PCBs use advanced polymer materials with higher glass transition temperatures compared to standard PCBs, providing better thermal stability, mechanical strength, and electrical performance.
-
What are the common applications of High-Tg PCB?
-
High-Tg PCBs are commonly used in automotive electronics, aerospace and defense systems, industrial control and automation, medical devices, telecommunications equipment, power electronics, oil and gas exploration, and renewable energy systems.
-
What are the benefits of using High-Tg PCB?
-
The benefits of using High-Tg PCBs include enhanced thermal stability, improved mechanical strength and durability, better electrical performance, and increased resistance to moisture and chemicals.
-
What are the key considerations when manufacturing High-Tg PCB?
-
The key considerations when manufacturing High-Tg PCBs include material selection, fabrication process adjustments (such as lamination, drilling, and plating), and design considerations (such as thermal management, mechanical stress, and signal integrity).
-
How do I choose the right High-Tg PCB material for my application?
- The selection of the appropriate High-Tg PCB material depends on the specific requirements of your application, such as the operating temperature range, mechanical stress, and electrical performance needs. It is recommended to consult with a PCB manufacturer or materials expert to determine the most suitable material for your specific application.
Conclusion
High-Tg PCBs offer superior thermal stability, mechanical strength, and electrical performance compared to standard PCBs, making them an ideal choice for electronic devices operating in harsh environments or demanding applications. By utilizing advanced polymer materials with higher glass transition temperatures, High-Tg PCBs can withstand extreme temperatures, mechanical stress, and chemical exposure while maintaining their structural integrity and performance.
When designing and manufacturing High-Tg PCBs, careful consideration should be given to material selection, fabrication process adjustments, and design optimization to ensure optimal performance and reliability. By leveraging the benefits of High-Tg PCBs, engineers and manufacturers can develop electronic devices that can operate reliably in challenging conditions and meet the ever-increasing demands of modern technology.
As the electronics industry continues to evolve and push the boundaries of performance and reliability, High-Tg PCBs will play an increasingly important role in enabling the development of advanced electronic systems. With their exceptional properties and versatile applications, High-Tg PCBs are poised to revolutionize the way we design and manufacture electronic devices for a wide range of industries.
No responses yet