Understanding the Cost Drivers of HDI PCBs
To effectively reduce HDI PCB costs, it’s important to first understand the key factors that contribute to their higher price point. Some of the main cost drivers include:
- Smaller via sizes and tighter tolerances
- Increased number of layers
- Use of microvias and buried vias
- Higher-quality materials
- More complex assembly processes
By addressing these areas through smart design choices and manufacturing optimizations, it’s possible to bring down the overall cost of HDI PCBs significantly.
Optimize Your HDI PCB Stack-Up
One of the most impactful ways to reduce HDI PCB costs is by carefully planning and optimizing your PCB stack-up. Here are some specific strategies to consider:
Minimize the Number of Layers
Each additional layer in an HDI PCB increases the complexity and cost of manufacturing. Therefore, it’s crucial to use the minimum number of layers necessary to achieve your design requirements. Work closely with your PCB fabricator to determine the optimal layer count for your specific application.
Use Blind and Buried Vias Judiciously
While blind and buried vias are key enablers of HDI technology, they also add to the cost of manufacturing. Use them only when absolutely necessary, and try to limit their use to the outer layers of the PCB where possible. This can help simplify the fabrication process and reduce costs.
Consider Alternative Materials
The choice of materials used in your HDI PCB can have a significant impact on cost. While high-performance materials like polyimide may be necessary for some applications, there may be lower-cost alternatives that can still meet your requirements. Discuss material options with your PCB fabricator to find the most cost-effective solution.
Design for Manufacturing (DFM)
Another key strategy for reducing HDI PCB costs is to follow best practices for Design for Manufacturing (DFM). By designing your PCB with manufacturability in mind, you can avoid costly redesigns and production issues down the line. Some specific DFM tips include:
Adhere to Your Fabricator’s Design Rules
Each PCB fabricator has their own set of design rules and guidelines based on their specific manufacturing capabilities. By adhering to these rules from the outset, you can ensure that your design is optimized for their processes and avoid costly redesigns later on.
Use Standardized Via Sizes and Pitches
While HDI PCBs often require smaller via sizes and tighter pitches compared to traditional PCBs, it’s still important to use standardized values whenever possible. This can help simplify the manufacturing process and reduce the need for specialized equipment, thereby lowering costs.
Minimize the Use of Microvias
Microvias are a key feature of HDI PCBs, but they also add complexity and cost to the manufacturing process. Use them sparingly and only when necessary to achieve your design requirements. If possible, try to use larger via sizes that can be fabricated using standard drilling processes.
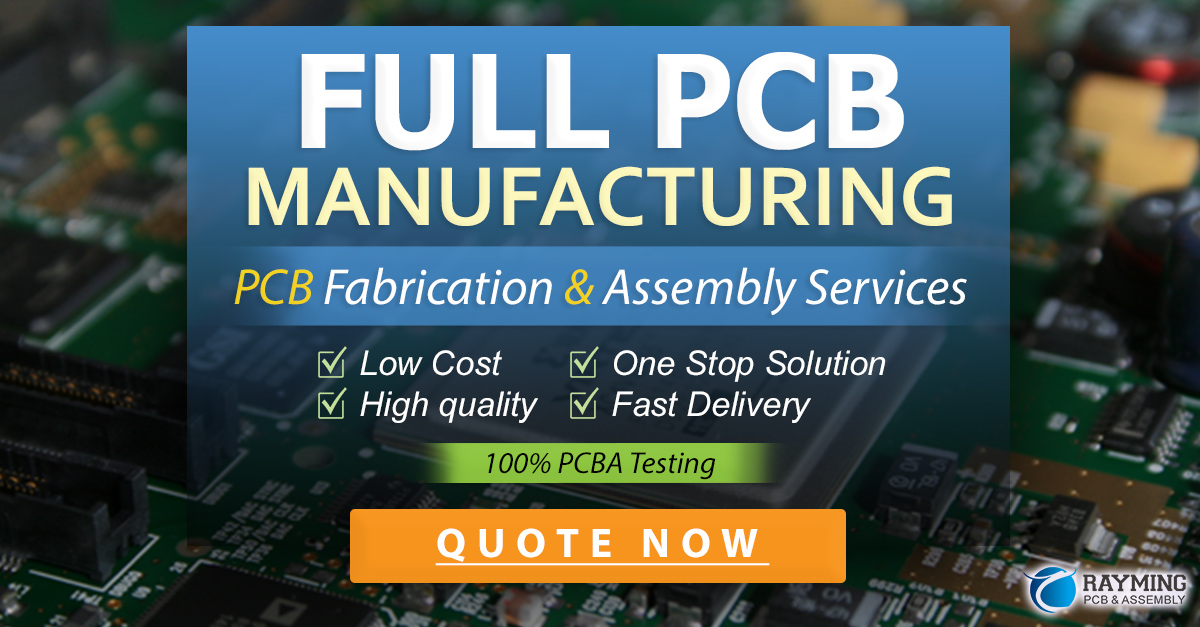
Optimize Your Panelization Strategy
Panelization, or the process of grouping multiple PCBs onto a single panel for production, is another area where cost savings can be realized. Here are some panelization strategies to consider:
Maximize Panel Utilization
Work with your PCB fabricator to determine the optimal panel size and layout for your HDI PCBs. By maximizing the number of boards per panel, you can reduce the overall cost per board and minimize waste.
Consider Stepped Panelization
For HDI PCBs with varying thicknesses or layer counts, stepped panelization can be an effective way to optimize panel utilization. This involves stepping the edges of the panel to accommodate boards of different thicknesses, allowing for more efficient use of the panel space.
Use V-Scoring for Depanelization
Traditional depanelization methods like routing or punching can be problematic for HDI PCBs due to their smaller features and tighter tolerances. V-scoring, which involves cutting a V-shaped groove along the board edges, can be a more cost-effective and reliable method for separating individual boards from the panel.
Leverage Economies of Scale
As with any manufacturing process, HDI PCB production benefits from economies of scale. By increasing your order quantity, you can often negotiate lower prices with your PCB fabricator. However, it’s important to balance this with your inventory management and cash flow needs. Consider the following strategies:
Optimize Your Order Quantity
Work with your PCB fabricator to determine the optimal order quantity for your HDI PCBs based on your specific needs and budget. In general, larger order quantities will result in lower per-unit costs, but this must be balanced against the risk of holding excess inventory.
Consider Long-Term Agreements
If you have a consistent and predictable demand for HDI PCBs, consider entering into a long-term agreement with your PCB fabricator. By committing to a certain volume of business over a period of time, you may be able to negotiate more favorable pricing and terms.
Consolidate Your Supply Chain
Working with multiple suppliers can add complexity and cost to your HDI PCB procurement process. Consider consolidating your supply chain by partnering with a single fabricator that can meet all of your needs. This can help streamline your procurement process and potentially lead to cost savings through volume discounts and reduced transaction costs.
Frequently Asked Questions (FAQ)
Q1: What is the main difference between HDI PCBs and traditional PCBs?
A1: HDI PCBs feature smaller vias, tighter tolerances, and higher layer counts compared to traditional PCBs, allowing for greater functionality in a smaller form factor. However, these features also make HDI PCBs more complex and costly to manufacture.
Q2: Can I use the same design rules for HDI PCBs as I do for traditional PCBs?
A2: No, HDI PCBs often require tighter design rules and tolerances compared to traditional PCBs. It’s important to work closely with your PCB fabricator and adhere to their specific design guidelines to ensure manufacturability and avoid costly redesigns.
Q3: Are there any alternative materials that can be used in HDI PCBs to reduce costs?
A3: Yes, while high-performance materials like polyimide are often used in HDI PCBs, there may be lower-cost alternatives that can still meet your requirements. Discuss material options with your PCB fabricator to find the most cost-effective solution for your specific application.
Q4: How can panelization help reduce HDI PCB costs?
A4: By optimizing your panelization strategy, you can maximize the number of boards per panel and reduce the overall cost per board. Techniques like stepped panelization and V-scoring can also help improve efficiency and reliability in the manufacturing process.
Q5: Is it always better to order larger quantities of HDI PCBs to reduce costs?
A5: While larger order quantities can often lead to lower per-unit costs due to economies of scale, it’s important to balance this with your inventory management and cash flow needs. Work with your PCB fabricator to determine the optimal order quantity based on your specific situation.
Conclusion
Reducing HDI PCB costs without sacrificing quality requires a holistic approach that addresses all aspects of the design and manufacturing process. By optimizing your HDI PCB stack-up, following best practices for Design for Manufacturing (DFM), leveraging economies of scale, and partnering closely with your PCB fabricator, you can significantly reduce costs while still achieving the performance and reliability required for your application.
Remember, the key to success is finding the right balance between cost and quality for your specific needs. By working collaboratively with your PCB fabricator and staying up-to-date with the latest HDI technologies and best practices, you can ensure that your HDI PCBs are optimized for both performance and cost-effectiveness.
No responses yet