Understanding PCB Trace Width and Current
When designing a printed circuit board (PCB), one of the crucial factors to consider is the trace width and current-carrying capacity. PCB traces are the conductive paths that carry electrical signals and power between components on the board. Determining the appropriate trace width is essential to ensure reliable performance, minimize power loss, and prevent overheating or damage to the PCB.
Factors Affecting PCB Trace Width
Several factors influence the determination of PCB trace width:
-
Current: The amount of current flowing through the trace is a primary factor. Higher currents require wider traces to handle the increased power without excessive heating.
-
Temperature Rise: The acceptable temperature rise of the trace above the ambient temperature affects the trace width. Higher temperature rises allow for narrower traces, while lower temperature rises necessitate wider traces.
-
Trace Thickness: The thickness of the copper trace also impacts its current-carrying capacity. Thicker traces can handle more current than thinner traces of the same width.
-
Ambient Temperature: The surrounding temperature of the PCB environment affects the trace width calculation. Higher ambient temperatures require wider traces to dissipate heat effectively.
-
Trace Length: The length of the trace influences voltage drop and power loss. Longer traces may require wider widths to minimize these effects.
Calculating PCB Trace Width
To determine the appropriate PCB trace width, you can use various methods, including mathematical calculations, online calculators, or PCB design software. Here’s a step-by-step guide to calculating trace width using the IPC-2152 standard.
Step 1: Determine the Required Current
First, identify the maximum current that will flow through the trace. This information is typically provided in the circuit design or component specifications. Let’s denote the current as “I” in amperes (A).
Step 2: Choose the Appropriate Temperature Rise
Select the maximum allowable temperature rise above the ambient temperature for the trace. The temperature rise depends on factors such as the PCB material, component specifications, and operating environment. Common temperature rises range from 10°C to 30°C. Let’s denote the temperature rise as “ΔT” in degrees Celsius (°C).
Step 3: Determine the Trace Thickness
Specify the thickness of the copper trace. PCB copper thickness is typically expressed in ounces per square foot (oz/ft²). Common thicknesses are 0.5 oz/ft², 1 oz/ft², and 2 oz/ft². Convert the thickness to mils (thousandths of an inch) using the following conversion:
– 0.5 oz/ft² ≈ 0.7 mils
– 1 oz/ft² ≈ 1.4 mils
– 2 oz/ft² ≈ 2.8 mils
Let’s denote the trace thickness as “t” in mils.
Step 4: Apply the IPC-2152 Formula
The IPC-2152 standard provides a formula to calculate the minimum trace width based on the current, temperature rise, and trace thickness. The formula is as follows:
W = (I / (k * ΔT^b))^(1/c)
Where:
– W = Trace width in mils
– I = Current in amps
– ΔT = Temperature rise in °C
– k, b, c = Constants based on trace thickness (see table below)
Trace Thickness (oz/ft²) | k | b | c |
---|---|---|---|
0.5 | 0.024 | 0.44 | 0.72 |
1 | 0.048 | 0.44 | 0.72 |
2 | 0.095 | 0.44 | 0.72 |
Substitute the values for I, ΔT, and the constants based on the trace thickness into the formula and calculate the minimum trace width.
Step 5: Round Up the Trace Width
After obtaining the minimum trace width from the calculation, round up the value to the nearest available trace width in your PCB design software or manufacturing capabilities. It’s always better to err on the side of caution and choose a slightly wider trace than the minimum requirement.
Example Calculation
Let’s work through an example to illustrate the PCB trace width calculation process.
Given:
– Current (I) = 1.5 A
– Temperature Rise (ΔT) = 20°C
– Trace Thickness = 1 oz/ft² (1.4 mils)
Step 1: Determine the constants based on the trace thickness.
From the table, for 1 oz/ft² trace thickness:
– k = 0.048
– b = 0.44
– c = 0.72
Step 2: Apply the IPC-2152 formula.
W = (1.5 / (0.048 * 20^0.44))^(1/0.72)
W = (1.5 / 0.1915)^1.389
W = 7.83^1.389
W = 20.16 mils
Step 3: Round up the trace width.
The calculated minimum trace width is 20.16 mils. Round up to the nearest available trace width, such as 21 mils or 22 mils, depending on your design constraints.
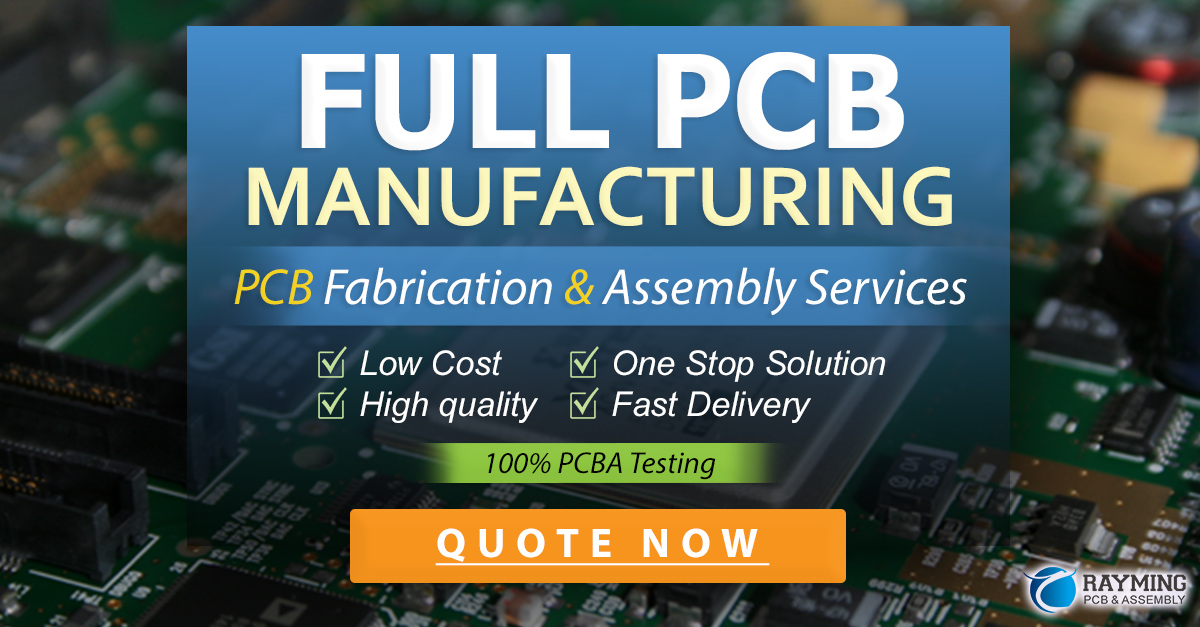
PCB Trace Current Capacity Tables
To simplify the trace width determination process, you can refer to pre-calculated current capacity tables. These tables provide the maximum current-carrying capacity for various trace widths, thicknesses, and temperature rises. Here’s an example table for 1 oz/ft² copper thickness and a 10°C temperature rise:
Trace Width (mils) | Maximum Current (A) |
---|---|
5 | 0.5 |
10 | 1.0 |
20 | 2.0 |
30 | 3.0 |
40 | 4.0 |
50 | 5.0 |
Remember that these tables are based on specific assumptions and may not cover all scenarios. It’s essential to consider the specific requirements of your PCB design and consult the relevant standards and guidelines.
Frequently Asked Questions (FAQs)
-
What happens if the PCB trace width is too narrow?
If the PCB trace width is too narrow for the required current, it can lead to several problems. The trace may overheat, causing damage to the PCB or connected components. Excessive heating can also lead to increased resistance, resulting in voltage drops and power loss. In severe cases, the trace may even melt or break, causing circuit failure. -
Can I use different trace widths for different sections of the same trace?
Yes, you can use different trace widths for different sections of the same trace. This technique is called necking down or tapering. It involves gradually reducing the trace width in areas where the current is expected to be lower. However, it’s important to ensure that the narrower sections can still handle the required current without exceeding the temperature rise limits. -
What is the relationship between trace width and resistance?
The resistance of a PCB trace is inversely proportional to its width. In other words, wider traces have lower resistance, while narrower traces have higher resistance. This relationship is important because higher resistance leads to increased power loss and voltage drop along the trace. By using wider traces, you can minimize these effects and improve the overall efficiency of your PCB design. -
How does the PCB material affect trace width calculations?
The PCB material can affect trace width calculations in several ways. Different materials have varying thermal conductivity and heat dissipation properties. For example, FR-4, a common PCB material, has a lower thermal conductivity compared to metal-core PCBs or high-performance substrates. Materials with better thermal conductivity allow for narrower traces, as they can dissipate heat more effectively. Additionally, the dielectric constant and thickness of the PCB material influence the trace impedance and signal integrity, which may require adjustments to trace widths. -
Are there any online tools or calculators for determining PCB trace width?
Yes, there are numerous online tools and calculators available for determining PCB trace width. These tools often provide a user-friendly interface where you can input parameters such as current, temperature rise, copper thickness, and PCB material. They then calculate the minimum trace width based on industry standards or specific formulas. Some popular online calculators include the Saturn PCB Toolkit,7PCB Trace Width Calculator, and EEWeb PCB Trace Width Calculator. However, it’s always a good practice to verify the results and consult the relevant standards and guidelines for your specific PCB design requirements.
Conclusion
Determining the appropriate PCB trace width is crucial for ensuring reliable performance, minimizing power loss, and preventing overheating or damage to the PCB. By understanding the factors that influence trace width, such as current, temperature rise, trace thickness, and ambient temperature, you can make informed decisions during the PCB design process.
The IPC-2152 standard provides a formula for calculating the minimum trace width based on these parameters. Additionally, pre-calculated current capacity tables offer a quick reference for determining trace widths based on specific requirements.
When designing your PCB, consider the specific needs of your circuit, consult the relevant standards and guidelines, and use appropriate tools and calculators to assist in trace width determination. By following best practices and carefully considering trace width and current-carrying capacity, you can create robust and reliable PCB designs that meet your performance and reliability goals.
No responses yet