Understanding SMD Components
Before diving into the assembly process, it’s essential to understand what SMD components are and how they differ from through-hole components. SMD components are designed to be soldered directly onto the surface of a printed circuit board (PCB), whereas through-hole components have leads that are inserted into holes drilled in the PCB.
SMD components come in various sizes and packages, such as:
- Resistors
- Capacitors
- Inductors
- Diodes
- Transistors
- Integrated circuits (ICs)
The size of an SMD component is typically expressed in a metric code, such as 0402, 0603, 0805, 1206, and so on. The first two digits represent the length, and the last two digits represent the width of the component in hundredths of an inch. For example, a 0402 component measures 0.04 inches by 0.02 inches (1.0mm x 0.5mm).
Tools and Equipment for SMD Assembly
To successfully assemble SMD components, you’ll need the following tools and equipment:
- Soldering iron with a fine tip (0.2mm to 0.5mm)
- Solder wire (lead-free, diameter: 0.5mm to 0.8mm)
- Tweezers (ESD-safe, preferably with a fine tip)
- Flux (no-clean or water-soluble)
- Isopropyl alcohol and cleaning swabs
- Magnifying glass or microscope
- ESD-safe work mat and wrist strap
- Solder wick or desoldering braid
- Hot air rework station (optional)
- Solder paste and stencil (for reflow soldering, optional)
Preparing the Workspace
Before starting the SMD assembly process, it’s crucial to set up a clean, organized, and ESD-safe workspace. Follow these steps:
- Clean your work surface thoroughly with isopropyl alcohol to remove any dirt, dust, or grease.
- Place an ESD-safe mat on your work surface to protect your components and PCB from electrostatic discharge.
- Wear an ESD-safe wrist strap and connect it to a grounded point or the ESD mat.
- Organize your tools and components within easy reach to streamline the assembly process.
- Ensure adequate lighting and ventilation in your workspace.
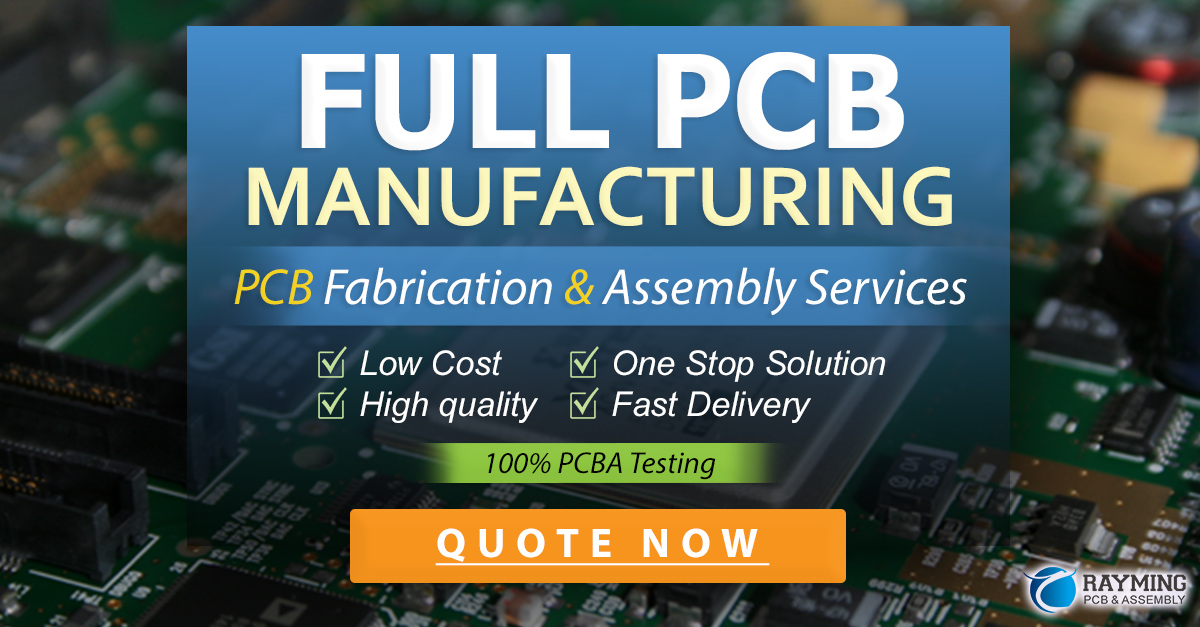
SMD Assembly Techniques
There are two primary techniques for assembling SMD components: hand soldering and reflow soldering.
Hand Soldering
Hand soldering is the most common method for small-scale projects and prototypes. Follow these steps:
- Apply a small amount of flux to the pads on the PCB where the SMD component will be placed.
- Using tweezers, carefully place the SMD component on the pads, ensuring that it is aligned correctly.
- Hold the component in place with the tweezers while applying heat to one of the pads with your soldering iron.
- Feed a small amount of solder wire to the pad, allowing it to melt and form a joint between the pad and the component lead.
- Remove the soldering iron and let the joint cool for a few seconds.
- Repeat steps 3-5 for the other pad(s) of the component.
- Clean any excess flux from the PCB using isopropyl alcohol and a cleaning swab.
Reflow Soldering
Reflow soldering is a more advanced technique that involves applying solder paste to the pads, placing the components, and then heating the entire PCB to melt the solder and form the joints. This method is more suitable for larger-scale production and complex boards.
- Apply solder paste to the pads on the PCB using a stencil or dispensing syringe.
- Place the SMD components on the pads, ensuring that they are aligned correctly.
- Preheat the PCB to activate the flux in the solder paste and remove any moisture.
- Place the PCB in a reflow oven or use a hot air rework station to melt the solder paste and form the joints.
- Allow the PCB to cool gradually to prevent thermal stress on the components.
- Clean any excess flux from the PCB using isopropyl alcohol and a cleaning swab.
Checking SMD Components
After assembling the SMD components, it’s essential to check their placement, alignment, and solder joint quality to ensure the reliability and functionality of your electronic device.
Visual Inspection
Perform a visual inspection of the assembled PCB using a magnifying glass or microscope. Look for the following:
- Proper alignment and orientation of components
- Solder bridges or short circuits between pads
- Insufficient or excessive solder on the joints
- Damaged or missing components
- Flux residue or contaminants on the PCB
Continuity and Resistance Tests
Use a multimeter to perform continuity and resistance tests on the assembled PCB:
- Set your multimeter to the continuity test mode.
- Place one probe on a pad and the other probe on the corresponding lead of the component.
- The multimeter should beep, indicating a continuous connection. If there is no beep, there may be an open circuit or a poor solder joint.
- For resistors, set your multimeter to the resistance mode and measure the resistance between the pads. Compare the measured value with the expected value based on the resistor’s color code or markings.
Functional Testing
After verifying the assembly’s integrity, perform a functional test of your electronic device:
- Power on the device and check for any signs of malfunction, such as overheating, unusual noises, or odors.
- Use an oscilloscope or logic analyzer to verify the proper functioning of the circuit.
- Compare the device’s performance with the expected specifications and requirements.
Rework and Repair Techniques
If you detect any issues during the inspection or functional testing, you may need to rework or repair the assembled PCB. Common rework and repair techniques include:
- Desoldering: Use a desoldering braid or solder sucker to remove the solder from the joint and then remove the component with tweezers.
- Solder joint repair: Apply flux to the joint and reheat it with your soldering iron, adding or removing solder as needed to create a proper joint.
- Component replacement: If a component is damaged or non-functional, desolder it and replace it with a new one, following the assembly techniques described earlier.
Best Practices for SMD Assembly
To ensure successful SMD assembly and minimize the risk of errors or damage, follow these best practices:
- Always handle SMD components with ESD-safe tweezers to prevent electrostatic discharge damage.
- Use the appropriate soldering iron tip size and temperature for the component and PCB.
- Apply the right amount of solder to create a proper joint – not too little or too much.
- Keep your workspace clean and organized to prevent contamination and lost components.
- Practice proper soldering techniques, such as maintaining a steady hand and applying heat for the appropriate duration.
- Regularly maintain and calibrate your tools and equipment to ensure optimal performance.
Troubleshooting Common SMD Assembly Issues
Despite following best practices, you may still encounter issues during SMD assembly. Here are some common problems and their solutions:
- Tombstoning: This occurs when one end of a component lifts off the pad during soldering. To prevent this, ensure equal heating of both pads and use the appropriate amount of solder.
- Solder bridges: These are unintended connections between two or more pads. To remove a solder bridge, use a desoldering braid or solder sucker and then reapply solder to the individual pads.
- Cold solder joints: These are dull, rough, or cracked joints that result from insufficient heat or poor soldering technique. Reheat the joint and apply fresh solder to create a proper connection.
- Damaged components: If a component is damaged during assembly, replace it with a new one and take extra care during the soldering process to prevent further damage.
FAQ
- What is the difference between SMD and through-hole components?
-
SMD components are designed to be soldered directly onto the surface of a PCB, while through-hole components have leads that are inserted into holes drilled in the PCB.
-
What tools do I need for SMD assembly?
-
Essential tools for SMD assembly include a soldering iron with a fine tip, solder wire, tweezers, flux, isopropyl alcohol, cleaning swabs, a magnifying glass or microscope, and an ESD-safe work mat and wrist strap.
-
How do I choose the right soldering iron tip size and temperature for SMD assembly?
-
The soldering iron tip size should be appropriate for the size of the SMD component and the PCB pads. A tip size between 0.2mm and 0.5mm is suitable for most SMD work. The temperature should be set according to the solder wire and component specifications, typically between 300°C and 400°C.
-
What is the difference between no-clean and water-soluble flux?
-
No-clean flux does not require cleaning after soldering, as it leaves minimal residue. Water-soluble flux requires cleaning with water or isopropyl alcohol after soldering to remove the residue, which can be corrosive if left on the PCB.
-
How can I prevent electrostatic discharge (ESD) damage to SMD components?
- To prevent ESD damage, always handle SMD components with ESD-safe tweezers, wear an ESD-safe wrist strap connected to a grounded point or ESD mat, and work on an ESD-safe surface. Store components in ESD-safe bags or containers when not in use.
Conclusion
SMD assembly is a critical process in the production of modern electronic devices. By understanding the components, tools, techniques, and best practices involved in SMD assembly, you can create reliable and efficient electronic projects. Remember to always prioritize safety, organization, and attention to detail throughout the assembly process, and don’t hesitate to seek guidance or resources when faced with challenges. With practice and perseverance, you’ll master the art of SMD assembly and unlock a world of possibilities in electronics design and fabrication.
No responses yet