Introduction to Halogen-Free PCBs
Printed circuit boards (PCBs) are essential components in virtually all modern electronic devices. They provide the foundation upon which electronic components are mounted and interconnected to form functional circuits. Over the years, the manufacturing process of PCBs has evolved to address various concerns, including environmental impact and safety. One significant development in this regard is the introduction of halogen-free PCBs.
Halogen-free PCBs are printed circuit boards that are manufactured without the use of halogenated compounds, such as brominated or chlorinated flame retardants. These compounds have been traditionally used in PCB manufacturing to improve the fire resistance of the boards. However, mounting evidence has shown that these substances can have detrimental effects on human health and the environment.
In this comprehensive guide, we will delve into the world of halogen-free PCBs, exploring their benefits, applications, and the latest trends in the industry. We will also address common questions and concerns regarding halogen-free PCBs to help you make informed decisions when designing and manufacturing your electronic products.
Understanding Halogens and Their Use in PCBs
What are Halogens?
Halogens are a group of elements in the periodic table that include fluorine (F), chlorine (Cl), bromine (Br), iodine (I), and astatine (At). These elements are highly reactive and readily form compounds with other elements. In PCB manufacturing, the most commonly used halogens are bromine and chlorine.
The Role of Halogens in Traditional PCBs
Traditionally, halogens have been used in PCB manufacturing as flame retardants. These compounds are added to the PCB substrate material, typically FR-4, to improve its fire resistance. The presence of halogens helps to inhibit the spread of flames in the event of a fire, thereby reducing the risk of damage to the electronic device and its surroundings.
The most common halogenated flame retardants used in PCBs are:
- Polybrominated diphenyl ethers (PBDEs)
- Tetrabromobisphenol A (TBBPA)
- Decabromodiphenyl ether (DecaBDE)
These compounds have been widely used in the electronics industry due to their effectiveness in improving fire safety and their relatively low cost.
The Problem with Halogenated Compounds
Despite their benefits in terms of fire resistance, halogenated compounds have come under scrutiny in recent years due to their potential negative impacts on human health and the environment.
When exposed to high temperatures or UV radiation, halogenated compounds can break down and release toxic substances, such as dioxins and furans. These substances have been linked to various health issues, including:
- Cancer
- Endocrine disruption
- Developmental and reproductive disorders
- Immune system suppression
Additionally, halogenated compounds are persistent organic pollutants (POPs), meaning they do not readily break down in the environment and can accumulate in the food chain. This can lead to long-term ecological damage and pose risks to wildlife and human health.
In light of these concerns, there has been a growing push to phase out the use of halogenated compounds in PCB manufacturing and move towards safer, more environmentally friendly alternatives.
The Rise of Halogen-Free PCBs
What are Halogen-Free PCBs?
Halogen-free PCBs are printed circuit boards that are manufactured without the use of halogenated flame retardants or other halogenated compounds. Instead, these PCBs rely on alternative materials and technologies to achieve the necessary level of fire resistance and performance.
The primary goal of halogen-free PCBs is to minimize the environmental impact and potential health risks associated with traditional halogenated PCBs while maintaining or even improving their functionality and reliability.
Alternative Flame Retardants Used in Halogen-Free PCBs
To replace halogenated flame retardants, manufacturers have developed a range of alternative materials that can provide comparable fire resistance without the associated health and environmental risks. Some of the most common alternative flame retardants used in halogen-free PCBs include:
- Phosphorus-based compounds
- Organic phosphates
- Inorganic phosphates
-
Red phosphorus
-
Nitrogen-based compounds
- Melamine derivatives
-
Triazines
-
Metal hydroxides
- Aluminum hydroxide (ATH)
- Magnesium hydroxide (MDH)
These alternative flame retardants work by various mechanisms, such as forming protective char layers, releasing water vapor, or diluting combustible gases, to inhibit the spread of flames and improve the overall fire resistance of the PCB.
Benefits of Halogen-Free PCBs
Halogen-free PCBs offer several significant benefits over their traditional halogenated counterparts:
- Reduced environmental impact
-
Halogen-free PCBs do not release toxic substances when exposed to high temperatures or UV radiation, minimizing the risk of ecological damage and long-term pollution.
-
Improved safety for human health
-
By eliminating the use of halogenated compounds, halogen-free PCBs reduce the potential for exposure to harmful substances that can cause various health issues.
-
Compliance with environmental regulations
-
Many countries and regions have implemented stringent regulations on the use of halogenated compounds in electronic products. Using halogen-free PCBs helps manufacturers comply with these regulations and avoid potential legal and financial consequences.
-
Enhanced recyclability and disposal
-
Halogen-free PCBs are easier to recycle and dispose of safely, as they do not contain the harmful substances that can complicate these processes.
-
Improved thermal stability and reliability
- Some alternative flame retardants used in halogen-free PCBs, such as metal hydroxides, can improve the thermal stability and overall reliability of the board, leading to better performance and longer product life.
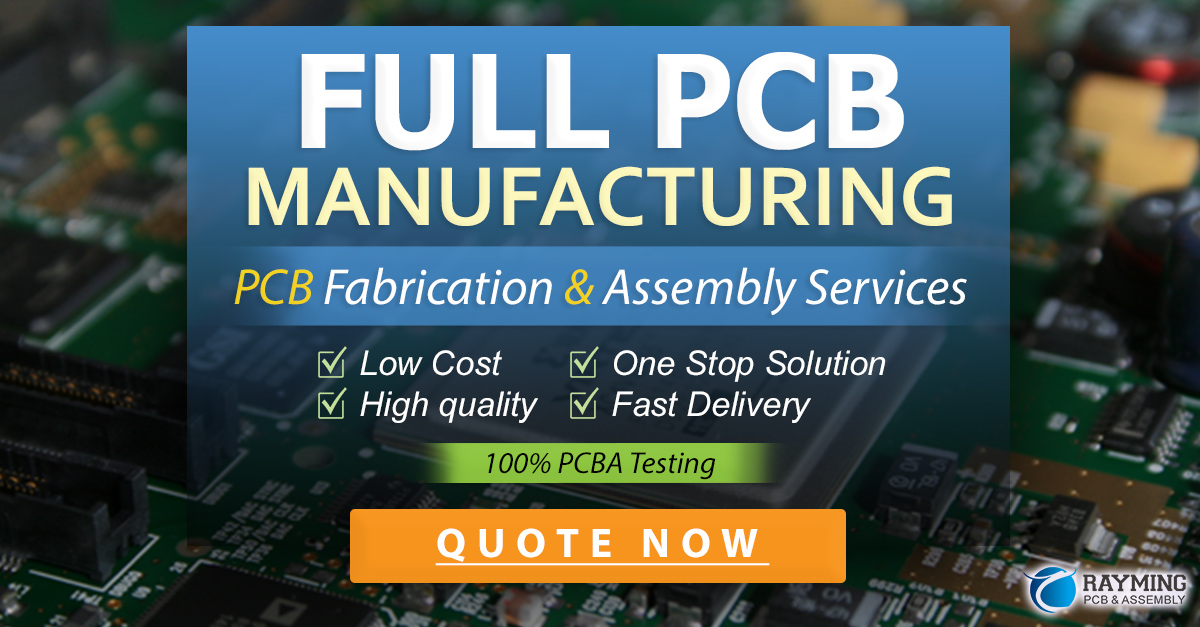
Applications of Halogen-Free PCBs
Halogen-free PCBs have gained widespread adoption across various industries and applications, particularly in sectors where environmental sustainability and human health are of utmost importance. Some of the key areas where halogen-free PCBs are commonly used include:
- Consumer electronics
- Smartphones
- Laptops
- Tablets
-
Wearable devices
-
Automotive electronics
- Engine control units (ECUs)
- Infotainment systems
- Advanced driver assistance systems (ADAS)
-
Electric vehicle (EV) components
-
Medical devices
- Diagnostic equipment
- Monitoring systems
-
Implantable devices
-
Industrial automation and control
- Programmable logic controllers (PLCs)
- Human-machine interfaces (HMIs)
-
Sensors and actuators
-
Aerospace and defense
- Avionics
- Satellite communications
- Military-grade electronics
As awareness of the benefits of halogen-free PCBs continues to grow, it is expected that their adoption will further expand across various sectors, driving innovation and sustainability in the electronics industry.
Challenges and Considerations in Adopting Halogen-Free PCBs
While halogen-free PCBs offer numerous benefits, there are some challenges and considerations that manufacturers and designers must take into account when transitioning from traditional halogenated PCBs:
- Cost implications
-
Alternative flame retardants used in halogen-free PCBs can be more expensive than their halogenated counterparts, which may lead to higher production costs.
-
Material compatibility
-
Some alternative flame retardants may require adjustments to the PCB manufacturing process or may not be compatible with certain substrate materials, necessitating careful selection and testing.
-
Performance and reliability testing
-
Halogen-free PCBs must undergo rigorous testing to ensure they meet the required performance and reliability standards, particularly in applications where high levels of fire resistance are critical.
-
Supply chain management
- Manufacturers must work closely with their suppliers to ensure a consistent and reliable supply of halogen-free materials and components, as the demand for these products continues to grow.
Despite these challenges, the benefits of halogen-free PCBs often outweigh the potential drawbacks, and many manufacturers are successfully navigating these issues to deliver high-quality, environmentally friendly products to their customers.
Latest Trends and Developments in Halogen-Free PCBs
As the electronics industry continues to evolve, so too does the development of halogen-free PCBs. Some of the latest trends and innovations in this field include:
- Advances in alternative flame retardant technologies
-
Researchers and material suppliers are continually working to develop new and improved alternative flame retardants that offer better performance, lower costs, and enhanced environmental sustainability.
-
Increased focus on recycling and circular economy
-
There is a growing emphasis on designing halogen-free PCBs with end-of-life considerations in mind, such as ease of disassembly and material recovery, to support the transition towards a more circular economy.
-
Adoption of bio-based materials
-
Some manufacturers are exploring the use of bio-based materials, such as plant-derived resins and fibers, as a means of further reducing the environmental impact of PCBs.
-
Integration with advanced manufacturing technologies
- The development of halogen-free PCBs is benefiting from advancements in manufacturing technologies, such as 3D printing and additive manufacturing, which offer new opportunities for design innovation and customization.
As these trends continue to shape the future of the electronics industry, it is clear that halogen-free PCBs will play an increasingly important role in delivering sustainable, high-performance solutions for a wide range of applications.
FAQ
- Are halogen-free PCBs more expensive than traditional halogenated PCBs?
-
In general, halogen-free PCBs can be more expensive to manufacture due to the higher cost of alternative flame retardants and potential process adjustments. However, the long-term benefits in terms of environmental sustainability and regulatory compliance often justify the initial investment.
-
Can halogen-free PCBs be used in all applications?
-
Halogen-free PCBs can be used in most applications, but there may be some instances where the specific performance requirements or environmental conditions necessitate the use of traditional halogenated PCBs. It is essential to carefully evaluate the specific needs of each application and consult with experts to determine the most suitable solution.
-
How can I ensure that the PCBs I purchase are truly halogen-free?
-
When sourcing halogen-free PCBs, it is crucial to work with reputable suppliers who can provide detailed material specifications and certifications. Additionally, you can request testing reports or conduct your own independent testing to verify the absence of halogenated compounds in the PCBs.
-
Are there any industry standards or certifications for halogen-free PCBs?
-
Several industry standards and certifications are relevant to halogen-free PCBs, including IEC 61249-2-21, which defines the requirements for halogen-free materials used in electronic assemblies, and UL 94 V-0, which assesses the flammability of plastic materials used in electronic components. Ensuring that your PCBs comply with these standards can provide added assurance of their halogen-free status and fire resistance.
-
How do I dispose of halogen-free PCBs at the end of their life?
- Halogen-free PCBs are generally easier to recycle and dispose of safely compared to their halogenated counterparts. However, it is still important to follow proper disposal procedures and work with certified e-waste recyclers to ensure that the materials are handled responsibly and in compliance with local regulations.
Conclusion
Halogen-free PCBs represent a significant step forward in the development of sustainable and environmentally friendly electronics. By eliminating the use of harmful halogenated compounds, these PCBs offer numerous benefits in terms of reduced environmental impact, improved safety for human health, and enhanced recyclability.
As the demand for halogen-free PCBs continues to grow, driven by increasing environmental awareness and stringent regulations, manufacturers and designers must stay informed about the latest trends, technologies, and best practices in this field. By embracing halogen-free PCBs and working collaboratively to overcome the associated challenges, the electronics industry can play a vital role in building a more sustainable future.
In this comprehensive guide, we have explored the key aspects of halogen-free PCBs, from their basic principles and benefits to their applications and future developments. Armed with this knowledge, you are now well-equipped to make informed decisions about incorporating halogen-free PCBs into your products and contributing to a greener, safer electronics landscape in 2024 and beyond.
No responses yet