Introduction to PCB Signal Conditioners
PCB Piezotronics, a leading manufacturer of sensors and instrumentation, has recently introduced a new signal conditioner designed specifically for DC sensors. This innovative product is set to revolutionize the way engineers and technicians process and analyze data from various DC sensors, including pressure transducers, load cells, and displacement sensors.
What is a Signal Conditioner?
A signal conditioner is an electronic device that converts the raw output signal from a sensor into a standardized, usable format for data acquisition systems or other devices. It performs functions such as amplification, filtering, isolation, and linearization to ensure that the signal is accurate, stable, and compatible with the connected equipment.
The Importance of Signal Conditioning
Signal conditioning is crucial in many applications, as it helps to:
- Improve signal quality by reducing noise and interference
- Protect sensitive equipment from high voltages or currents
- Convert the sensor’s output into a format suitable for the connected devices
- Compensate for environmental factors such as temperature changes
Features and Benefits of the PCB Signal Conditioner
Versatile Input Compatibility
The PCB signal conditioner is designed to work with a wide range of DC sensors, including:
- Pressure transducers
- Load cells
- Displacement sensors
- Accelerometers
- Strain gauges
This versatility allows engineers to use a single signal conditioner for multiple sensor types, simplifying their setup and reducing costs.
Adjustable Gain and Excitation
The signal conditioner features adjustable gain and excitation settings, enabling users to optimize the device for their specific sensor and application. This flexibility ensures that the signal is amplified and conditioned appropriately, resulting in accurate and reliable measurements.
Gain Range | Excitation Range |
---|---|
1 to 1000 | 1 to 15 VDC |
Filtering Options
To minimize noise and interference, the PCB signal conditioner offers various filtering options:
- Low-pass filters
- High-pass filters
- Band-pass filters
- Notch filters
These filters can be easily configured to suit the specific requirements of the application, ensuring a clean and stable output signal.
Isolation and Protection
The signal conditioner provides galvanic isolation between the input and output, protecting both the sensor and the connected equipment from potential damage caused by ground loops, high voltages, or electrical noise. This isolation also helps to prevent signal degradation and ensures the integrity of the measurement data.
Compact and Rugged Design
PCB Piezotronics has designed this signal conditioner to be compact and rugged, making it suitable for use in a variety of environments, including:
- Industrial plants
- Automotive testing facilities
- Aerospace and defense applications
- Research laboratories
The device’s sturdy enclosure and robust connectors ensure reliable operation even in harsh conditions.
Applications of the PCB Signal Conditioner
Industrial Process Control
In industrial process control, accurate and reliable sensor data is essential for optimizing production, minimizing waste, and ensuring product quality. The PCB signal conditioner can be used with pressure transducers, load cells, and displacement sensors to monitor and control various processes, such as:
- Fluid flow
- Tank level measurement
- Conveyor belt tension
- Valve positioning
By providing clean, conditioned signals to the control system, the signal conditioner helps to improve process efficiency and consistency.
Automotive Testing
Automotive engineers rely on a wide range of sensors to evaluate vehicle performance, safety, and durability. The PCB signal conditioner can be used in conjunction with sensors such as:
- Accelerometers for vibration analysis
- Pressure transducers for engine and hydraulic system monitoring
- Load cells for suspension and brake testing
The signal conditioner’s adjustable gain and filtering options allow engineers to optimize the sensor signals for their specific testing requirements, ensuring accurate and meaningful data.
Aerospace and Defense
In the aerospace and defense industries, sensor data is critical for monitoring the performance and health of aircraft, missiles, and other systems. The PCB signal conditioner can be used with sensors such as:
- Accelerometers for structural health monitoring
- Pressure transducers for engine and hydraulic system monitoring
- Strain gauges for stress analysis
The device’s rugged design and isolation capabilities make it well-suited for the demanding environments encountered in these applications.
Research and Development
Researchers and scientists in various fields, such as materials science, biomechanics, and geophysics, use DC sensors to gather data for their studies. The PCB signal conditioner can help to improve the quality and reliability of their measurements by providing clean, conditioned signals from sensors such as:
- Load cells for material testing
- Pressure transducers for fluid dynamics studies
- Displacement sensors for motion analysis
The signal conditioner’s versatility and adjustable settings enable researchers to adapt the device to their specific experimental setups, ensuring optimal results.
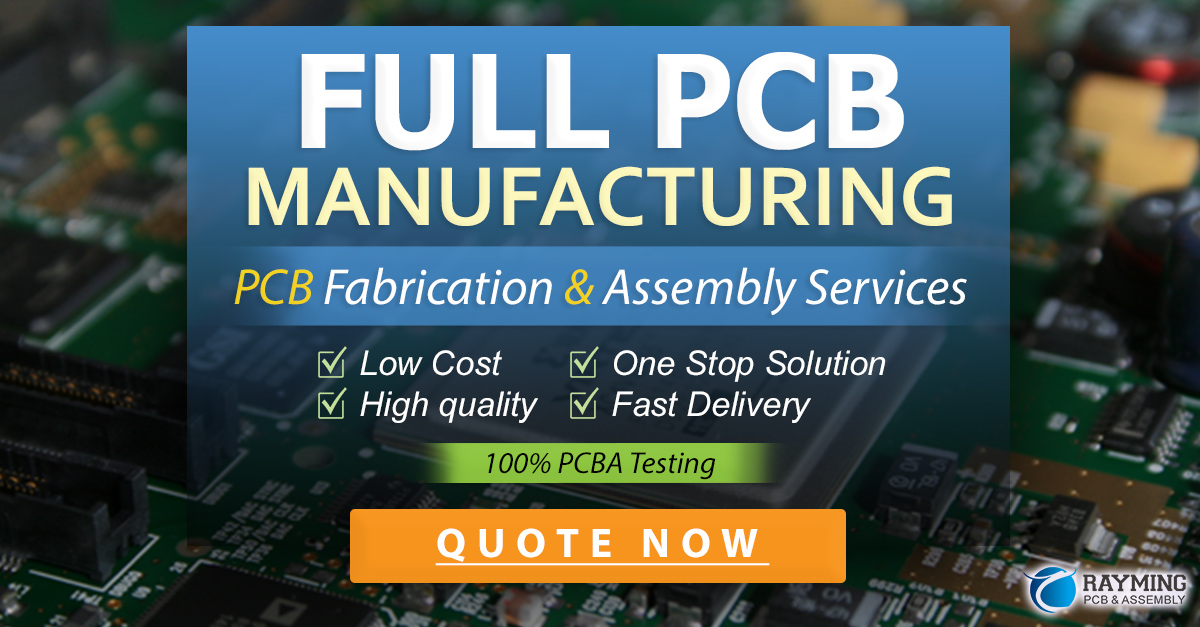
Setting Up and Using the PCB Signal Conditioner
Installation and Wiring
Installing the PCB signal conditioner is a straightforward process:
- Mount the device in a suitable location, ensuring adequate ventilation and protection from environmental hazards.
- Connect the sensor to the input terminals, following the manufacturer’s wiring guidelines.
- Connect the output terminals to the data acquisition system or other connected equipment.
- Power the device using the appropriate supply voltage.
Proper wiring is essential for accurate and reliable operation. Always follow the provided instructions and use high-quality, shielded cables to minimize noise and interference.
Configuration and Calibration
Before using the PCB signal conditioner, users must configure the device settings to match their specific sensor and application requirements. This process typically involves:
- Setting the gain and excitation levels
- Selecting the appropriate filtering options
- Configuring any additional features, such as offset adjustment or shunt calibration
The signal conditioner may also require calibration to ensure accurate measurements. This can be done by applying known input signals and adjusting the device settings to achieve the desired output values.
Maintenance and Troubleshooting
To ensure optimal performance and longevity, regular maintenance of the PCB signal conditioner is recommended. This may include:
- Cleaning the device and connectors
- Checking for loose or damaged wiring
- Verifying the accuracy of the output signal
If issues arise, troubleshooting steps may include:
- Checking the power supply and wiring connections
- Verifying the sensor’s functionality and compatibility
- Adjusting the device settings and recalibrating if necessary
- Consulting the manufacturer’s support resources or contacting their technical support team
Conclusion
The PCB signal conditioner for DC sensors is a versatile and reliable tool for engineers, researchers, and technicians across various industries. By providing clean, conditioned signals from a wide range of sensors, this device helps to improve the accuracy, reliability, and efficiency of data acquisition and control systems.
With its adjustable gain and excitation settings, flexible filtering options, and rugged design, the PCB signal conditioner is well-suited for applications in industrial process control, automotive testing, aerospace and defense, and research and development.
As technology continues to advance, the importance of accurate and reliable sensor data will only continue to grow. The PCB signal conditioner is poised to play a crucial role in enabling engineers and scientists to gather the high-quality data they need to drive innovation and progress in their respective fields.
Frequently Asked Questions (FAQ)
-
Q: Can the PCB signal conditioner be used with sensors from other manufacturers?
A: Yes, the PCB signal conditioner is designed to work with a wide range of DC sensors, regardless of the manufacturer. However, it is essential to ensure that the sensor’s specifications, such as output type and range, are compatible with the signal conditioner’s input requirements. -
Q: What is the maximum cable length between the sensor and the signal conditioner?
A: The maximum cable length depends on factors such as the sensor type, output signal level, and environmental conditions. In general, it is recommended to keep the cable length as short as possible to minimize noise and signal degradation. Consult the manufacturer’s guidelines or contact their technical support for specific recommendations. -
Q: Can the PCB signal conditioner be used in hazardous environments?
A: The PCB signal conditioner is designed for use in a variety of industrial environments. However, for use in hazardous locations, such as those with explosive atmospheres, it is essential to select a device with the appropriate certifications and ratings, such as intrinsic safety or explosion-proof enclosures. Always consult the manufacturer’s specifications and local regulations to ensure compliance. -
Q: How often should the PCB signal conditioner be calibrated?
A: The calibration frequency depends on factors such as the application requirements, environmental conditions, and the stability of the sensor and signal conditioner. Some applications may require daily or weekly calibration, while others may only need annual or bi-annual calibration. Establishing a calibration schedule based on the specific needs of the application and the recommendations of the manufacturer is crucial. -
Q: What should I do if the output signal from the PCB signal conditioner is unstable or noisy?
A: If the output signal is unstable or noisy, first check the wiring connections and ensure that the cables are properly shielded and grounded. Verify that the sensor is functioning correctly and that the signal conditioner’s settings, such as gain and filtering, are appropriate for the application. If the issue persists, try adjusting the filtering options or consult the manufacturer’s troubleshooting guide for further assistance.
No responses yet