Introduction to Flexible Aluminum PCBs
A flexible aluminum PCB, also known as an aluminum-based flexible circuit board, is a type of printed circuit board that combines the flexibility of a traditional flexible PCB with the thermal management properties of aluminum. Unlike standard flexible PCBs (FPCs) which use a polymer substrate, flexible aluminum PCBs have a thin aluminum layer as the base material.
Flexible aluminum PCBs offer several advantages over traditional FPCs and rigid PCBs:
- Excellent thermal conductivity for heat dissipation
- Lightweight and flexible for space-constrained applications
- High mechanical strength and durability
- Shielding against electromagnetic interference (EMI)
These unique properties make flexible aluminum PCBs well-suited for applications in industries such as automotive, aerospace, LED lighting, and consumer electronics where thermal management, flexibility, and reliability are critical.
Structure and Composition of Flexible Aluminum PCBs
A flexible aluminum PCB typically consists of the following layers:
- Protective cover layer (optional)
- Conductive copper traces
- Insulating dielectric layer
- Aluminum substrate
- Adhesive layer
- Protective bottom layer (optional)
The aluminum substrate serves as the base material and provides the PCB with its thermal management properties and mechanical strength. The thickness of the aluminum layer can vary depending on the specific application requirements, but it is typically between 0.2mm and 0.5mm.
The insulating dielectric layer is laminated onto the aluminum substrate using an adhesive. This layer electrically isolates the conductive copper traces from the aluminum base. Common dielectric materials used in flexible aluminum PCBs include polyimide, polyester, and epoxy.
The conductive copper traces are etched onto the dielectric layer to create the desired circuit pattern. The copper thickness can range from 0.5 oz to 3 oz, depending on the current carrying requirements of the application.
Optional protective layers can be added to the top and bottom of the PCB to provide additional insulation and protection against environmental factors such as moisture, dust, and abrasion.
Thermal Management Properties
One of the key benefits of using a flexible aluminum PCB is its excellent thermal conductivity. Aluminum has a thermal conductivity of approximately 200 W/mK, which is significantly higher than the thermal conductivity of traditional PCB materials like FR-4 (0.3 W/mK) and polyimide (0.2 W/mK).
This high thermal conductivity allows flexible aluminum PCBs to efficiently dissipate heat generated by electronic components, preventing overheating and ensuring stable performance. The aluminum substrate acts as a built-in heat sink, conducting heat away from hot spots and distributing it evenly across the PCB.
The thermal management properties of flexible aluminum PCBs can be further enhanced by incorporating additional features such as thermal vias, which are conductive holes drilled through the PCB to transfer heat from the top layer to the aluminum substrate. Other techniques like using thicker copper traces or adding dedicated heat sinks can also improve the thermal performance of the PCB.
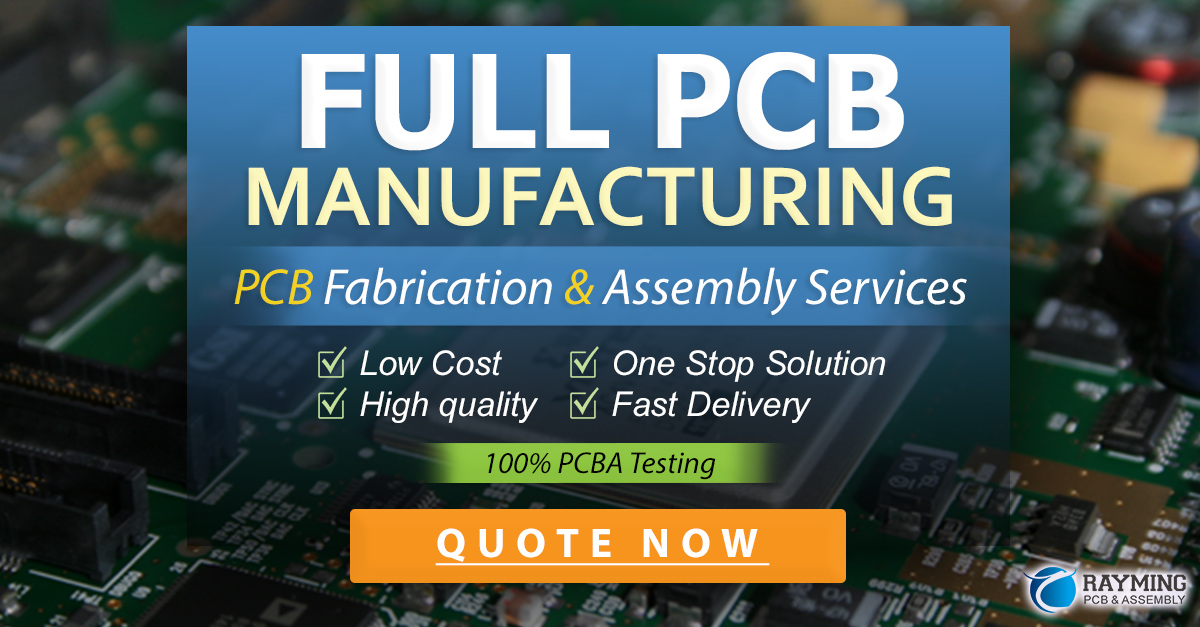
Flexible and Lightweight Design
Flexible aluminum PCBs combine the flexibility of traditional FPCs with the strength and thermal management properties of aluminum. This unique combination makes them ideal for applications where space is limited, and the PCB needs to conform to the shape of the enclosure or components.
The aluminum substrate provides the PCB with a high degree of mechanical strength and durability, allowing it to withstand repeated bending and flexing without damage. The flexibility of the dielectric layer and copper traces enables the PCB to be bent, rolled, or folded to fit into tight spaces or wrapped around components.
In addition to their flexibility, aluminum-based PCBs are also lightweight compared to traditional rigid PCBs. This weight reduction is particularly beneficial in applications where every gram counts, such as in aerospace and portable electronic devices.
EMI Shielding Properties
Another advantage of using a flexible aluminum PCB is its inherent shielding against electromagnetic interference (EMI). EMI can cause unwanted noise, signal degradation, and malfunctions in electronic systems, particularly in high-frequency applications.
The aluminum substrate in a flexible aluminum PCB acts as a natural EMI shield, reflecting and absorbing electromagnetic waves. This shielding property helps to minimize the impact of EMI on the circuit, ensuring cleaner signals and more reliable performance.
By using a flexible aluminum PCB, designers can often eliminate the need for additional EMI shielding components like metal enclosures or shielding gaskets, saving space, weight, and cost in the overall system design.
Applications of Flexible Aluminum PCBs
Flexible aluminum PCBs are used in a wide range of industries and applications where thermal management, flexibility, and reliability are essential. Some common applications include:
- Automotive electronics
- Engine control units (ECUs)
- Power inverters and converters
- LED lighting systems
-
Sensors and actuators
-
Aerospace and defense
- Avionics systems
- Radar and communication equipment
- Satellite components
-
Military wearables
-
LED lighting
- High-power LED modules
- Flexible LED strips
- Automotive LED headlights
-
Stage and entertainment lighting
-
Consumer electronics
- Smartphones and tablets
- Wearable devices
- Gaming consoles
-
Virtual reality (VR) and augmented reality (AR) headsets
-
Medical devices
- Implantable electronics
- Wearable health monitors
- Diagnostic imaging equipment
- Surgical instruments
Comparison with Traditional FPCs and Rigid PCBs
To better understand the benefits of flexible aluminum PCBs, it’s helpful to compare them with traditional flexible PCBs (FPCs) and rigid PCBs. The following table summarizes the key differences between these three types of PCBs:
Property | Flexible Aluminum PCB | Traditional FPC | Rigid PCB |
---|---|---|---|
Substrate Material | Aluminum | Polymer | FR-4 |
Thermal Conductivity | High | Low | Low |
Mechanical Strength | High | Low | High |
Flexibility | High | High | Low |
Weight | Lightweight | Lightweight | Heavy |
EMI Shielding | Excellent | Poor | Moderate |
Cost | Moderate to High | Low to Moderate | Low |
Common Thickness Range | 0.2mm – 0.5mm | 0.05mm – 0.3mm | 0.8mm – 3.2mm |
As shown in the table, flexible aluminum PCBs offer a unique combination of properties that set them apart from traditional FPCs and rigid PCBs. While they may have a higher cost compared to other options, their superior thermal management, mechanical strength, and EMI shielding make them the preferred choice for many demanding applications.
Design Considerations for Flexible Aluminum PCBs
When designing a flexible aluminum PCB, there are several key factors to consider to ensure optimal performance and reliability:
-
Bend radius: The minimum bend radius of the PCB should be carefully calculated based on the thickness of the aluminum substrate, dielectric layer, and copper traces. Exceeding the minimum bend radius can cause stress and damage to the PCB.
-
Thermal management: While the aluminum substrate provides excellent thermal conductivity, proper thermal design is still essential. This includes optimizing the placement of components, using thermal vias, and considering additional heat sinking methods if necessary.
-
Adhesive selection: The choice of adhesive used to bond the dielectric layer to the aluminum substrate is critical for the long-term reliability of the PCB. The adhesive must be compatible with the materials used and able to withstand the expected environmental conditions and mechanical stresses.
-
Copper trace design: The layout and geometry of the copper traces should be optimized to minimize resistance and ensure adequate current carrying capacity. The use of thicker copper traces or multiple layers can help to improve the electrical performance of the PCB.
-
Connector and component selection: When choosing connectors and components for a flexible aluminum PCB, it’s important to consider their compatibility with the flexible substrate and their ability to withstand the expected mechanical stresses and environmental conditions.
By carefully considering these design factors and working closely with experienced PCB manufacturers, designers can create high-performance flexible aluminum PCBs that meet the specific requirements of their applications.
Manufacturing Process for Flexible Aluminum PCBs
The manufacturing process for flexible aluminum PCBs involves several key steps:
-
Substrate preparation: The aluminum substrate is cleaned and treated to improve adhesion with the dielectric layer.
-
Lamination: The dielectric layer is laminated onto the aluminum substrate using a high-temperature and pressure process. The adhesive layer is typically pre-applied to the dielectric material.
-
Drilling and patterning: Holes are drilled through the laminated substrate for vias and component mounting. The copper layer is then patterned using photolithography and etching processes to create the desired circuit layout.
-
Surface finish: A surface finish, such as ENIG (Electroless Nickel Immersion Gold) or OSP (Organic Solderability Preservative), is applied to the copper traces to protect them from oxidation and improve solderability.
-
Cutting and forming: The PCB panel is cut into individual circuits using a laser or mechanical cutting process. If required, the circuits can be formed into the desired shape using specialized tooling.
-
Assembly and testing: Components are soldered onto the PCB using SMT (Surface Mount Technology) or through-hole assembly processes. The assembled PCB is then tested to ensure proper functionality and performance.
Throughout the manufacturing process, strict quality control measures are implemented to ensure the consistency and reliability of the final product. This includes inspections at various stages, such as visual inspections, electrical testing, and environmental testing.
Frequently Asked Questions (FAQ)
- What is the difference between a flexible aluminum PCB and a traditional flexible PCB (FPC)?
-
A flexible aluminum PCB uses an aluminum substrate as the base material, providing better thermal conductivity and mechanical strength compared to traditional FPCs, which use a polymer substrate. Flexible aluminum PCBs also offer better EMI shielding properties.
-
Can flexible aluminum PCBs be used in high-temperature applications?
-
Yes, flexible aluminum PCBs are well-suited for high-temperature applications due to their excellent thermal conductivity. The aluminum substrate helps to dissipate heat efficiently, preventing overheating and ensuring stable performance.
-
How does the cost of a flexible aluminum PCB compare to other types of PCBs?
-
Flexible aluminum PCBs tend to have a higher cost compared to traditional FPCs and rigid PCBs due to the specialized materials and manufacturing processes involved. However, the superior thermal management, mechanical strength, and EMI shielding properties of flexible aluminum PCBs can often justify the higher cost in demanding applications.
-
Are flexible aluminum PCBs suitable for high-frequency applications?
-
Yes, flexible aluminum PCBs are a good choice for high-frequency applications due to their inherent EMI shielding properties. The aluminum substrate helps to minimize the impact of electromagnetic interference on the circuit, ensuring cleaner signals and more reliable performance.
-
Can flexible aluminum PCBs be customized to meet specific application requirements?
- Yes, flexible aluminum PCBs can be customized in terms of thickness, size, shape, and layer stack-up to meet the specific requirements of an application. Designers can work closely with PCB manufacturers to optimize the design for their particular needs.
Conclusion
Flexible aluminum PCBs offer a unique combination of thermal management, flexibility, and mechanical strength, making them an attractive option for a wide range of demanding applications. By combining the benefits of traditional flexible PCBs with the superior properties of aluminum, these PCBs enable designers to create high-performance, reliable, and space-efficient electronic systems.
As technology continues to advance and the demand for more compact, lightweight, and thermally efficient electronics grows, flexible aluminum PCBs are poised to play an increasingly important role in industries such as automotive, aerospace, LED lighting, and consumer electronics.
By understanding the key properties, design considerations, and manufacturing processes involved in creating flexible aluminum PCBs, designers can leverage this innovative technology to push the boundaries of electronic design and develop products that meet the evolving needs of the market.
No responses yet