Introduction to EMC and PCB Design
Electromagnetic Compatibility (EMC) is a critical aspect of Printed Circuit Board (PCB) design that ensures electronic devices function properly in their intended electromagnetic environment without causing or being susceptible to electromagnetic interference (EMI). EMC PCB design involves implementing various techniques and adhering to EMC standards to minimize EMI and ensure the device’s compliance with regulatory requirements.
In this comprehensive guide, we will delve into the fundamentals of EMC, its importance in PCB design, and the key EMC standards that designers must follow to create robust and compliant electronic products.
Understanding Electromagnetic Compatibility (EMC)
EMC refers to an electronic device’s ability to operate satisfactorily in its electromagnetic environment without introducing intolerable EMI to other devices in the same environment. There are two main aspects of EMC:
- Emission: The electromagnetic energy generated by the device that can potentially interfere with other devices.
- Immunity: The device’s ability to function correctly in the presence of EMI from other sources.
To achieve good EMC, designers must consider both emission and immunity while designing PCBs and electronic systems.
Importance of EMC in PCB Design
Proper EMC PCB design is crucial for several reasons:
- Regulatory compliance: Electronic devices must meet EMC standards set by regulatory bodies to be sold in various markets.
- Reliability: EMI can cause devices to malfunction or fail, leading to poor performance and user experience.
- Safety: In some cases, EMI can pose safety risks, such as in medical or automotive applications.
- Cost reduction: Addressing EMC issues early in the design process can save significant costs associated with redesigns and product recalls.
By prioritizing EMC in PCB design, designers can create products that are more reliable, safe, and compliant with regulations.
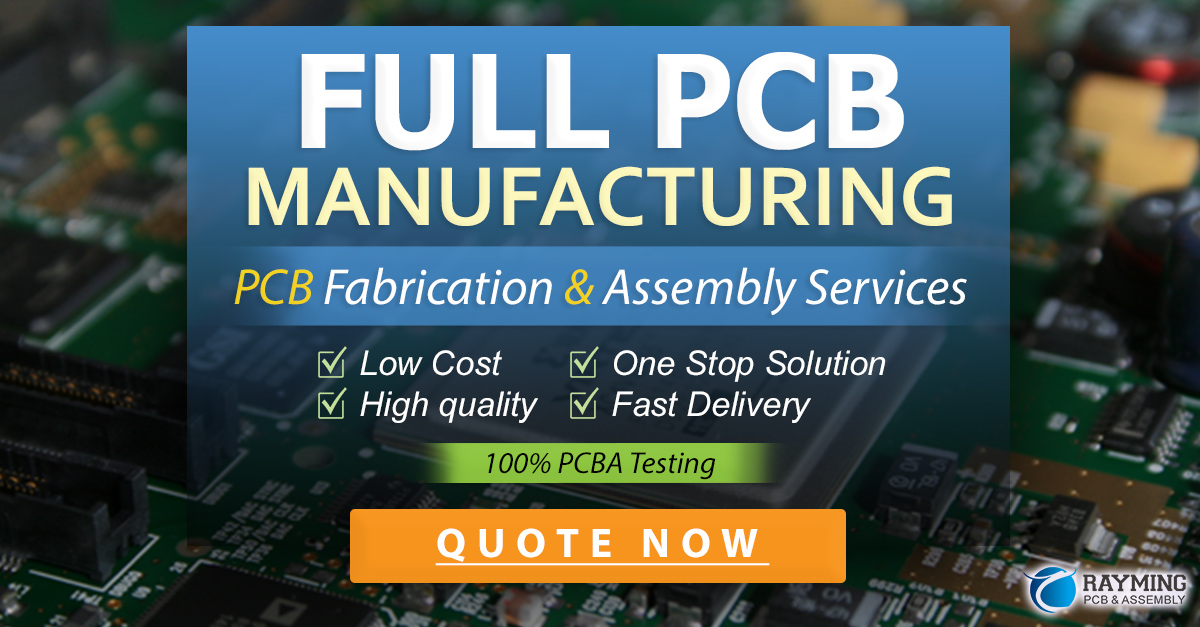
Key EMC Standards for PCB Design
Several EMC standards guide designers in creating compliant PCBs. Some of the most important standards include:
FCC Part 15 (USA)
The Federal Communications Commission (FCC) regulates EMI emissions from electronic devices in the United States. FCC Part 15 sets limits for both intentional and unintentional radiators.
Device Class | Frequency Range | Electric Field Strength Limit |
---|---|---|
Class A | 30-88 MHz | 90 µV/m at 10 meters |
Class A | 88-216 MHz | 150 µV/m at 10 meters |
Class A | 216-960 MHz | 210 µV/m at 10 meters |
Class B | 30-88 MHz | 100 µV/m at 3 meters |
Class B | 88-216 MHz | 150 µV/m at 3 meters |
Class B | 216-960 MHz | 200 µV/m at 3 meters |
CISPR 22 and CISPR 32 (Europe)
The International Special Committee on Radio Interference (CISPR) develops EMC standards adopted by many countries, particularly in Europe. CISPR 22 and CISPR 32 set limits for EMI emissions from information technology equipment (ITE) and multimedia equipment (MME), respectively.
IEC 61000-4 Series (Immunity Standards)
The International Electrotechnical Commission (IEC) 61000-4 series standards define immunity requirements for electronic devices. Some key standards include:
- IEC 61000-4-2: Electrostatic Discharge (ESD) Immunity
- IEC 61000-4-3: Radiated, Radio-Frequency, Electromagnetic Field Immunity
- IEC 61000-4-4: Electrical Fast Transient (EFT) / Burst Immunity
- IEC 61000-4-5: Surge Immunity
- IEC 61000-4-6: Immunity to Conducted Disturbances, Induced by Radio-Frequency Fields
Designers must understand and apply these standards to ensure their PCBs meet the required EMC performance criteria.
EMC PCB Design Techniques
To achieve good EMC performance, designers can employ various techniques during PCB design:
Grounding and Shielding
Proper grounding and shielding are essential for minimizing EMI. Techniques include:
- Using a solid ground plane to provide a low-impedance return path for high-frequency currents.
- Implementing a single-point grounding scheme to avoid ground loops.
- Using shielded cables and connectors to reduce EMI coupling.
- Applying shielding materials, such as conductive coatings or metal enclosures, to contain EMI.
PCB Layer Stackup
An optimal PCB layer stackup can help reduce EMI and improve signal integrity. Guidelines include:
- Placing high-speed signals on inner layers between ground planes to minimize radiation.
- Using ground planes to separate noisy and sensitive signal layers.
- Maintaining symmetry in the stackup to balance capacitance and reduce common-mode noise.
Signal Routing and Termination
Careful signal routing and proper termination can minimize EMI generation and susceptibility. Techniques include:
- Keeping high-speed traces as short as possible and avoiding unnecessary bends.
- Using controlled impedance traces and matching terminations to minimize reflections.
- Separating high-speed and low-speed signals to avoid crosstalk.
- Implementing differential signaling for noise immunity.
Filtering and Suppression
Filters and suppression components can help attenuate EMI at the source or prevent its propagation. Methods include:
- Using power supply filters to reduce conducted EMI.
- Placing decoupling capacitors close to ICs to suppress high-frequency noise.
- Implementing ferrite beads or common-mode chokes to attenuate common-mode currents.
- Applying transient voltage suppressors (TVS) or varistors to protect against voltage spikes.
EMC Testing and Compliance
To ensure PCBs meet EMC standards, designers must perform appropriate testing and maintain documentation. Key aspects include:
- Pre-compliance testing: In-house testing to identify and resolve EMC issues early in the design process.
- Compliance testing: Formal testing at an accredited EMC laboratory to certify the product’s compliance with relevant standards.
- Documentation: Maintaining design records, test reports, and declarations of conformity to demonstrate compliance.
By incorporating EMC considerations throughout the design process and conducting thorough testing, designers can create PCBs that meet EMC standards and perform reliably in their intended electromagnetic environments.
Frequently Asked Questions (FAQ)
- What is the difference between EMI and EMC?
-
EMI (Electromagnetic Interference) refers to the unwanted electromagnetic energy that can disrupt the functioning of electronic devices. EMC (Electromagnetic Compatibility) is the ability of a device to operate properly in its electromagnetic environment without causing or being susceptible to EMI.
-
Why is EMC important in PCB design?
-
EMC is crucial in PCB design to ensure that the device functions reliably, meets regulatory requirements, and does not interfere with other electronic devices in its environment. Proper EMC design helps to minimize EMI, improve signal integrity, and avoid costly redesigns or product recalls.
-
What are some common EMC standards that PCB designers must follow?
-
Some common EMC standards include FCC Part 15 (USA), CISPR 22 and CISPR 32 (Europe), and the IEC 61000-4 series for immunity requirements. Designers must understand and apply these standards based on the intended market and application of their products.
-
How can grounding and shielding techniques help with EMC in PCB design?
-
Proper grounding and shielding techniques, such as using a solid ground plane, implementing a single-point grounding scheme, and applying shielding materials, can help minimize EMI by providing low-impedance return paths and containing electromagnetic energy within the device.
-
What is the purpose of EMC testing, and when should it be performed?
- EMC testing is performed to ensure that a device meets the relevant EMC standards and can function properly in its intended electromagnetic environment. Pre-compliance testing should be done early in the design process to identify and resolve EMC issues, while formal compliance testing is required to certify the product’s compliance before it can be sold in the market.
Conclusion
EMC PCB design is a critical aspect of creating reliable, safe, and compliant electronic devices. By understanding the fundamentals of EMC, applying appropriate design techniques, and adhering to relevant EMC standards, designers can minimize EMI and ensure their products perform well in their intended electromagnetic environments.
This comprehensive guide has covered the importance of EMC in PCB design, key EMC standards, design techniques for grounding, shielding, PCB layer stackup, signal routing, and filtering, as well as the role of EMC testing and compliance. By following these guidelines and best practices, PCB designers can create robust and compliant products that meet the increasingly stringent EMC requirements in today’s electronic landscape.
No responses yet