1. Solder Bridges and Short Circuits
Solder bridges occur when excess solder accidentally connects two or more component leads or PCB traces that should not be connected. This can lead to short circuits and cause the circuit to malfunction or even damage components.
Solutions:
- Use a soldering iron with a fine tip to precisely control the amount of solder applied
- Employ proper soldering techniques, such as using the correct temperature and applying solder in moderation
- Inspect the PCB closely after soldering to identify and remove any solder bridges
- Consider using solder masks or insulating materials to prevent accidental bridging
2. Cold Solder Joints
Cold solder joints happen when the solder does not melt and flow properly, resulting in a weak and unreliable connection. This can be caused by insufficient heat, improper soldering technique, or contaminated surfaces.
Solutions:
- Ensure the soldering iron is set to the appropriate temperature for the solder being used
- Clean the component leads and PCB pads before soldering to remove any oxidation or contamination
- Apply heat to both the component lead and the PCB pad simultaneously for proper solder flow
- Use flux to improve solder wetting and remove oxides
3. Lifted or Misaligned Components
Components can sometimes lift or become misaligned during the soldering process, especially if they are subjected to excessive heat or mechanical stress. This can lead to poor connections and reduced reliability.
Solutions:
- Use a soldering iron with temperature control to avoid overheating components
- Secure components in place before soldering, using tape or specialized adhesives
- Employ proper placement techniques, such as using pick-and-place machines for precise positioning
- Inspectcomponents after soldering to ensure proper alignment and make necessary adjustments
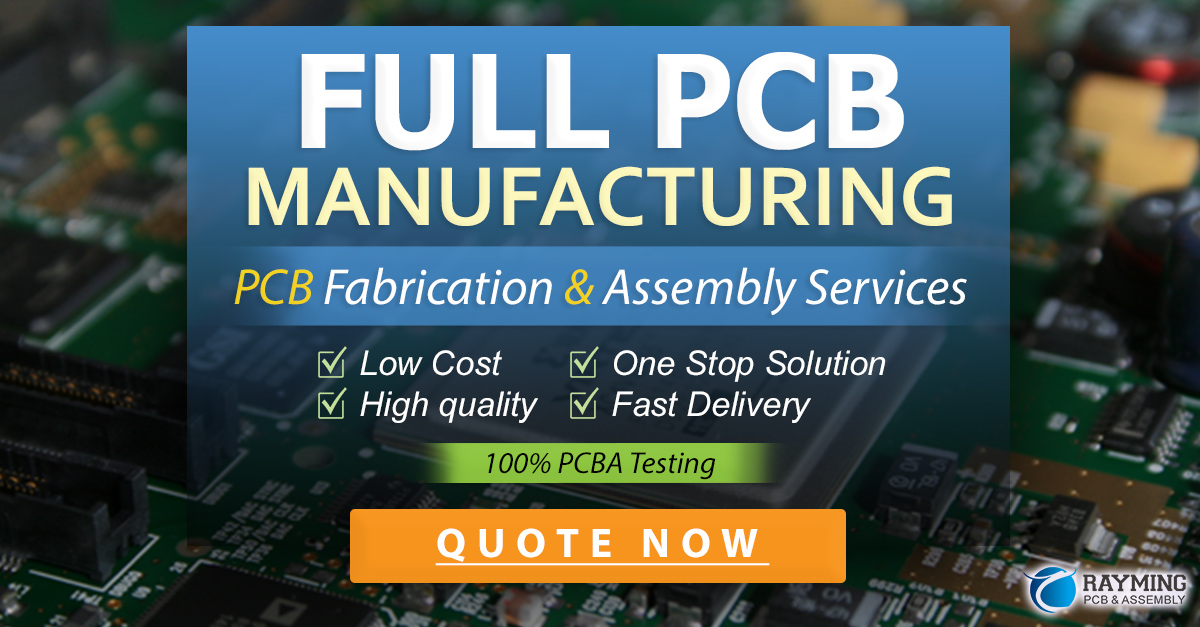
4. Trace Damage and Discontinuity
PCB traces can be damaged due to physical stress, excessive heat, or improper handling. Damaged traces can cause signal interruptions, short circuits, or open circuits, leading to circuit malfunction.
Solutions:
- Handle PCBs with care, avoiding excessive bending or twisting
- Use ESD (Electrostatic Discharge) protection measures when handling PCBs to prevent damage from static electricity
- Employ adequate strain relief for connectors and cables to minimize stress on the PCB
- Consider using thicker copper traces or reinforced PCB materials for high-stress applications
5. Incorrect Component Placement
Placing components in the wrong orientation or location on the PCB can result in circuit malfunction or even damage to the components themselves.
Solutions:
- Double-check component placement before soldering, referring to the PCB layout diagram and component datasheets
- Use clear and unambiguous markings on the PCB to indicate component orientation (e.g., silkscreen, polarity marks)
- Implement a thorough visual inspection process to catch placement errors before powering up the circuit
- Consider using automated inspection systems, such as machine vision, for high-volume production
6. Insufficient or Excessive Solder
Applying too little solder can result in weak connections and reduced reliability, while excessive solder can cause bridging, short circuits, and difficulty in rework.
Solutions:
- Use the appropriate solder wire diameter and tip size for the specific component and PCB pad
- Apply solder in moderation, ensuring sufficient coverage without overflowing
- Employ proper soldering techniques, such as preheating and using the correct iron temperature
- Consider using solder paste and reflow soldering for surface-mount components to ensure consistent solder volume
7. Improper Grounding and Shielding
Inadequate grounding and shielding can lead to signal integrity issues, electromagnetic interference (EMI), and reduced circuit performance.
Solutions:
- Design the PCB with proper grounding techniques, such as using ground planes and minimizing ground loops
- Employ shielding materials, such as metal enclosures or conductive coatings, to reduce EMI
- Use decoupling capacitors and ferrite beads to suppress high-frequency noise and stabilize power supply
- Consider using differential signaling for sensitive signals to reduce susceptibility to noise
8. Manufacturing Defects
Manufacturing defects, such as etching errors, drill misalignment, or incorrect layer registration, can cause various issues with PCB functionality and reliability.
Solutions:
- Work with reputable PCB manufacturers that adhere to strict quality control standards
- Provide clear and accurate design files, including Gerber files and drill data
- Specify appropriate tolerances and design rules for the specific manufacturing process
- Perform thorough electrical testing and visual inspection of the manufactured PCBs to identify and address any defects
9. Environmental Factors
Environmental factors, such as temperature, humidity, and vibration, can affect PCB performance and long-term reliability.
Solutions:
- Design the PCB with consideration for the expected operating environment, including temperature range and humidity levels
- Use appropriate PCB materials and coatings that can withstand the environmental conditions
- Employ thermal management techniques, such as using heatsinks or thermal vias, to dissipate heat effectively
- Consider using conformal coatings or potting compounds to protect the PCB from moisture and contaminants
- Use vibration-dampening mounting techniques or specialized PCB materials for high-vibration environments
FAQ
Q1: What are the most common causes of solder bridges?
A1: Solder bridges are often caused by applying excessive solder, using a soldering iron with a tip that is too large, or not properly cleaning the PCB and component leads before soldering.
Q2: How can I prevent lifted components during the soldering process?
A2: To prevent lifted components, use a soldering iron with temperature control to avoid overheating, secure components in place before soldering, and employ proper placement techniques, such as using pick-and-place machines for precise positioning.
Q3: What are the consequences of improper grounding and shielding in PCBs?
A3: Improper grounding and shielding can lead to signal integrity issues, electromagnetic interference (EMI), and reduced circuit performance. This can cause the circuit to malfunction or be susceptible to external noise and interference.
Q4: How can I ensure the quality of manufactured PCBs?
A4: To ensure the quality of manufactured PCBs, work with reputable PCB manufacturers that adhere to strict quality control standards, provide clear and accurate design files, specify appropriate tolerances and design rules, and perform thorough electrical testing and visual inspection of the manufactured PCBs.
Q5: What environmental factors should I consider when designing a PCB?
A5: When designing a PCB, consider the expected operating environment, including temperature range, humidity levels, and vibration. Use appropriate PCB materials and coatings that can withstand the environmental conditions, and employ thermal management techniques, conformal coatings, or potting compounds as needed.
Problem | Cause | Solution |
---|---|---|
Solder Bridges and Short Circuits | Excess solder, improper soldering technique | Use fine-tipped soldering iron, apply solder in moderation, inspect for bridges |
Cold Solder Joints | Insufficient heat, improper technique, contamination | Use appropriate soldering iron temperature, clean surfaces, apply heat evenly, use flux |
Lifted or Misaligned Components | Excessive heat or mechanical stress | Use temperature-controlled soldering iron, secure components, employ proper placement techniques |
Trace Damage and Discontinuity | Physical stress, excessive heat, improper handling | Handle PCBs with care, use ESD protection, employ strain relief, consider thicker traces or reinforced materials |
Incorrect Component Placement | Human error, ambiguous markings | Double-check placement, use clear markings, implement visual inspection, consider automated inspection systems |
In conclusion, addressing the various problems associated with PCBs requires a combination of proper design techniques, manufacturing processes, and handling procedures. By understanding the common issues and implementing the appropriate solutions, designers and manufacturers can ensure the reliability, performance, and longevity of their PCBs. Regular inspection, testing, and adherence to industry standards and best practices are essential for identifying and resolving PCB Issues effectively.
No responses yet