Introduction to Ceramic PCB
Ceramic PCBs, also known as ceramic printed circuit boards, are a type of high-performance substrate material used in the manufacturing of electronic circuits. Unlike traditional PCBs that use fiberglass or other organic materials as the base substrate, ceramic PCBs utilize ceramic materials, offering unique properties and advantages in specific applications.
What is a Ceramic PCB?
A ceramic PCB is a printed circuit board that uses ceramic materials as the base substrate instead of the more commonly used fiberglass or other organic materials. The ceramic material is typically composed of alumina (aluminum oxide) or other ceramic compounds. The conductive traces and components are then printed or deposited onto the ceramic substrate to create the desired electronic circuit.
Advantages of Ceramic PCBs
Ceramic PCBs offer several advantages over traditional PCBs:
-
High thermal conductivity: Ceramic materials have excellent thermal conductivity, allowing for efficient heat dissipation from electronic components. This property makes ceramic PCBs suitable for high-power and high-temperature applications.
-
Low dielectric constant: Ceramics have a low dielectric constant, which reduces signal loss and improves signal integrity. This characteristic is particularly beneficial for high-frequency applications, such as radio frequency (RF) and microwave circuits.
-
Dimensional stability: Ceramic materials have a low coefficient of thermal expansion (CTE), which means they maintain their dimensions and shape even under extreme temperature variations. This stability is crucial for maintaining the integrity of the electronic circuit.
-
High strength and rigidity: Ceramic substrates are inherently strong and rigid, providing excellent mechanical support for the electronic components. This strength also allows for the creation of thinner and more compact PCBs.
-
Chemical resistance: Ceramic materials are resistant to various chemicals and solvents, making them suitable for use in harsh environments where traditional PCBs may degrade or fail.
Materials Used in Ceramic PCBs
Alumina (Al2O3)
Alumina, or aluminum oxide, is the most commonly used ceramic material in the production of ceramic PCBs. It is known for its excellent electrical insulation properties, high thermal conductivity, and good mechanical strength. Alumina substrates are available in various purity grades, with higher purity levels offering better performance characteristics.
Aluminum Nitride (AlN)
Aluminum nitride is another ceramic material used in the manufacturing of ceramic PCBs. It offers even higher thermal conductivity compared to alumina, making it an ideal choice for applications that require efficient heat dissipation. AlN also has a low dielectric constant, making it suitable for high-frequency applications.
Beryllium Oxide (BeO)
Beryllium oxide is a ceramic material known for its exceptional thermal conductivity, surpassing that of both alumina and aluminum nitride. However, due to the toxic nature of beryllium and the associated health risks, the use of BeO in ceramic PCBs is limited and requires strict safety precautions during manufacturing and handling.
Types of Ceramic PCBs
Single-Layer Ceramic PCBs
Single-layer ceramic PCBs consist of a single layer of ceramic substrate with conductive traces and components on one side. These PCBs are relatively simple to manufacture and are suitable for low-complexity circuits. Single-layer ceramic PCBs are commonly used in power electronics, LED lighting, and high-temperature applications.
Multilayer Ceramic PCBs
Multilayer ceramic PCBs are constructed by stacking multiple layers of ceramic substrates with conductive traces and interconnects between the layers. This configuration allows for more complex circuit designs and higher component density compared to single-layer PCBs. Multilayer ceramic PCBs are used in applications that require high reliability, such as aerospace, military, and medical devices.
Co-fired Ceramic PCBs
Co-fired ceramic PCBs involve the simultaneous firing of the ceramic substrate and the conductive traces in a single process. There are two main types of co-fired ceramic PCBs:
-
Low Temperature Co-fired Ceramic (LTCC): LTCC PCBs are fabricated using ceramic materials that can be fired at relatively low temperatures (below 1000°C). This allows for the use of low-resistance conductors like silver and gold, enabling high-frequency applications.
-
High Temperature Co-fired Ceramic (HTCC): HTCC PCBs are manufactured using ceramic materials that require higher firing temperatures (above 1000°C). These PCBs offer excellent thermal stability and are suitable for high-temperature applications.
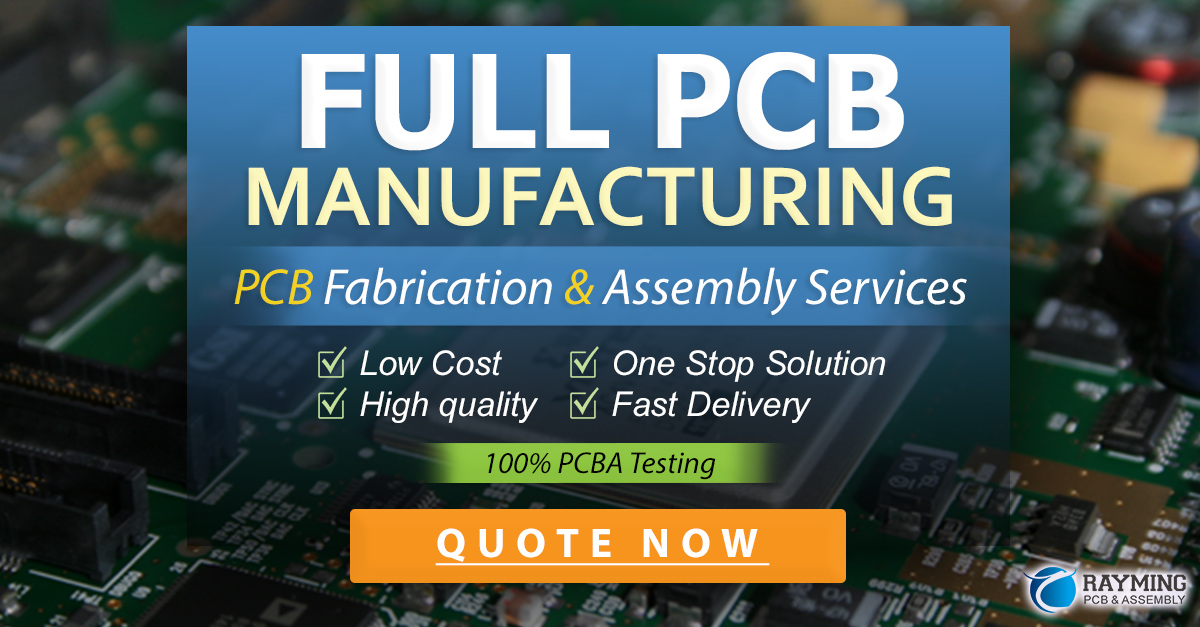
Ceramic PCB Manufacturing Process
The manufacturing process for ceramic PCBs involves several steps:
-
Substrate Preparation: The ceramic substrate material is prepared by mixing ceramic powders with binders and solvents to form a slurry. The slurry is then cast or molded into the desired shape and thickness.
-
Via Formation: Holes or vias are drilled or punched into the ceramic substrate to allow for interconnections between layers in multilayer PCBs.
-
Metallization: Conductive traces and pads are deposited onto the ceramic substrate using techniques such as screen printing, thin-film deposition, or thick-film deposition. The choice of metallization technique depends on the required circuit resolution and performance.
-
Layering and Lamination (for multilayer PCBs): Multiple layers of metallized ceramic substrates are stacked and aligned, with conductive pastes or adhesives used to bond the layers together.
-
Firing: The assembled ceramic PCB is fired in a high-temperature furnace to sinter the ceramic material and form a dense, solid substrate. The firing process also fuses the conductive traces and interconnects to the ceramic substrate.
-
Post-firing Processing: After firing, additional processing steps may be performed, such as surface finishing, component assembly, and testing.
Applications of Ceramic PCBs
Ceramic PCBs find applications in various industries and sectors where high performance, reliability, and durability are critical:
-
Aerospace and Defense: Ceramic PCBs are used in avionics, radar systems, satellite communications, and military electronics due to their ability to withstand extreme temperatures and harsh environments.
-
Automotive: In the automotive industry, ceramic PCBs are used in engine control units, power electronics, and sensors, where they provide reliable performance under high-temperature conditions.
-
Medical Devices: Ceramic PCBs are utilized in medical implants, surgical instruments, and diagnostic equipment, where their biocompatibility and reliability are essential.
-
Industrial Electronics: Ceramic PCBs are employed in industrial control systems, power converters, and high-temperature sensors, where they offer robustness and long-term stability.
-
RF and Microwave Applications: The low dielectric constant and low loss properties of ceramic PCBs make them suitable for high-frequency applications, such as satellite communications, radar systems, and wireless infrastructure.
Frequently Asked Questions (FAQ)
1. What is the difference between ceramic PCBs and traditional PCBs?
Ceramic PCBs use ceramic materials, such as alumina or aluminum nitride, as the base substrate, while traditional PCBs use organic materials like fiberglass. Ceramic PCBs offer better thermal conductivity, lower dielectric constant, and higher strength compared to traditional PCBs.
2. Are ceramic PCBs more expensive than traditional PCBs?
Yes, ceramic PCBs are generally more expensive than traditional PCBs due to the higher cost of ceramic materials and the specialized manufacturing processes involved. However, the improved performance and reliability of ceramic PCBs justify the added cost in certain applications.
3. Can ceramic PCBs be used for high-frequency applications?
Yes, ceramic PCBs are well-suited for high-frequency applications due to their low dielectric constant and low loss properties. They are commonly used in RF and microwave circuits, where signal integrity is crucial.
4. What are the common materials used in ceramic PCBs?
The most common materials used in ceramic PCBs are alumina (Al2O3), aluminum nitride (AlN), and beryllium oxide (BeO). Each material has its own unique properties and advantages, such as high thermal conductivity or low dielectric constant.
5. How are ceramic PCBs manufactured?
The manufacturing process for ceramic PCBs involves substrate preparation, via formation, metallization, layering and lamination (for multilayer PCBs), firing, and post-firing processing. The process requires specialized equipment and techniques to achieve the desired performance and reliability.
Conclusion
Ceramic PCBs offer a high-performance alternative to traditional PCBs, providing excellent thermal conductivity, low dielectric constant, dimensional stability, and high strength. These properties make ceramic PCBs suitable for a wide range of applications, including aerospace, automotive, medical devices, industrial electronics, and RF and microwave circuits.
The choice of ceramic material, such as alumina, aluminum nitride, or beryllium oxide, depends on the specific requirements of the application. Ceramic PCBs can be manufactured as single-layer or multilayer boards, with co-fired ceramic technologies like LTCC and HTCC offering additional advantages.
While ceramic PCBs are more expensive than traditional PCBs, their superior performance and reliability justify the added cost in demanding applications. As technology continues to advance, ceramic PCBs are expected to play an increasingly important role in enabling the development of high-performance electronic systems.
Property | Ceramic PCBs | Traditional PCBs |
---|---|---|
Substrate Material | Ceramic (e.g., alumina, aluminum nitride) | Organic (e.g., fiberglass) |
Thermal Conductivity | High | Low |
Dielectric Constant | Low | Higher |
Strength and Rigidity | High | Moderate |
Dimensional Stability | High | Moderate |
Chemical Resistance | High | Moderate |
Cost | Higher | Lower |
Table: Comparison of properties between ceramic PCBs and traditional PCBs
No responses yet