What is a PCB?
Before we dive into the tutorial, let’s briefly discuss what a PCB is and why it’s essential in electronics. A PCB is a flat board made of insulating material, such as fiberglass or plastic, with conductive copper traces printed on its surface. These traces connect various electronic components, such as resistors, capacitors, and integrated circuits, to form a complete electronic circuit.
PCBs offer several advantages over traditional point-to-point wiring:
- Compact design
- Increased reliability
- Easier mass production
- Reduced electromagnetic interference (EMI)
Why Use AutoDesk Eagle for PCB Design?
AutoDesk Eagle is a powerful, yet user-friendly, PCB design software that offers a wide range of features for both beginners and experienced designers. Some of the key benefits of using Eagle include:
- Cross-platform compatibility (Windows, Mac, and Linux)
- Extensive component libraries
- Schematic and board layout editors
- Design rule checking (DRC) and electrical rule checking (ERC)
- Gerber file generation for manufacturing
Getting Started with AutoDesk Eagle
Installation and Setup
- Download AutoDesk Eagle from the official website (https://www.autodesk.com/products/eagle/overview).
- Install the software following the on-screen instructions.
- Launch Eagle and create a new account or sign in with your existing AutoDesk account.
User Interface Overview
Eagle’s user interface consists of several main components:
- Control Panel: Manages files, libraries, and settings
- Schematic Editor: Creates and edits schematic diagrams
- Board Editor: Designs the physical layout of the PCB
- Library Editor: Creates and modifies component libraries
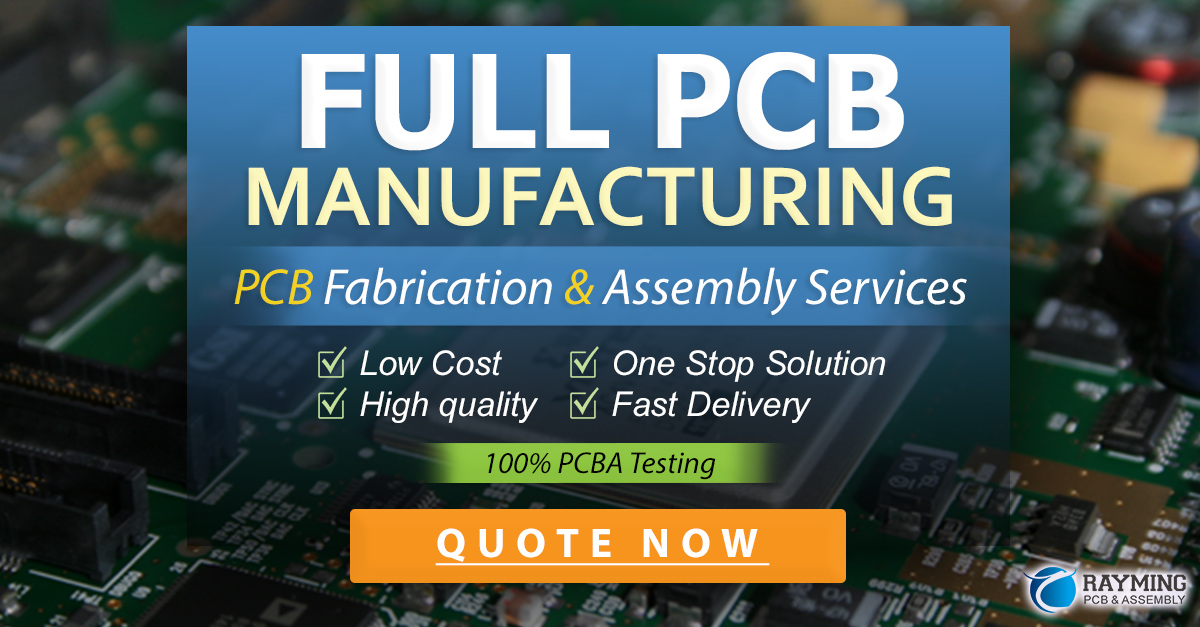
Designing Your PCB
Step 1: Create a New Project
- In the Control Panel, click on “File” > “New” > “Project”.
- Choose a location to save your project and give it a name.
- Right-click on your project in the Control Panel and select “New” > “Schematic”.
Step 2: Create a Schematic Diagram
- Add components to your schematic by clicking on the “Add” tool and searching for the desired component in the libraries.
- Place the components on the schematic canvas and arrange them logically.
- Use the “Net” tool to connect the components according to your circuit design.
- Assign unique names to your components and nets using the “Name” tool.
Step 3: Perform Electrical Rule Checking (ERC)
- Click on the “ERC” button in the Schematic Editor to run an electrical rule check.
- Address any warnings or errors flagged by the ERC.
Step 4: Create a Board from the Schematic
- Click on the “Board” button in the Schematic Editor to generate a board layout from your schematic.
- A new Board Editor window will open with your components placed on the board.
Step 5: Design the Board Layout
- Arrange the components on the board for optimal placement and routing.
- Define the board outline using the “Rectangle” tool.
- Use the “Route” tool to manually route the traces between components, following the connections defined in your schematic.
- Adjust trace widths and clearances as needed to meet your design requirements.
Step 6: Perform Design Rule Checking (DRC)
- Click on the “DRC” button in the Board Editor to run a design rule check.
- Modify your board layout to resolve any DRC errors or warnings.
Step 7: Generate Gerber Files
- In the Board Editor, click on “File” > “CAM Processor”.
- Select the “Gerber RS-274X” output device and click “Process Job”.
- Save the generated Gerber files, which will be used by the PCB manufacturer.
PCB Manufacturing and Assembly
Once you have generated the Gerber files, you can send them to a PCB manufacturer for fabrication. Many online PCB manufacturing services, such as JLCPCB or PCBWay, offer affordable and quick turnaround times.
After receiving your manufactured PCBs, you can proceed with the assembly process:
- Gather the necessary components and tools (soldering iron, solder, tweezers, etc.).
- Place the components on the PCB according to the designators on the silk screen layer.
- Solder the components to the PCB, ensuring proper connections and avoiding solder bridges.
- Inspect the assembled board for any defects or errors.
Tips and Best Practices
- Keep your schematic organized and well-labeled to simplify the board layout process.
- Use a consistent naming convention for your components and nets.
- Follow recommended design rules for trace width, clearance, and hole sizes to ensure manufacturability.
- Consider using ground planes to reduce EMI and improve signal integrity.
- Test your assembled PCB thoroughly before putting it into use.
Frequently Asked Questions (FAQ)
-
Q: Can I use AutoDesk Eagle for commercial projects?
A: Yes, AutoDesk Eagle offers a subscription-based license that allows commercial use. However, make sure to review the licensing terms and conditions before using Eagle for commercial purposes. -
Q: How do I add custom components to Eagle’s libraries?
A: You can create custom components using the Library Editor in Eagle. Start by creating a new library, then use the available tools to define the component’s schematic symbol, package, and device. -
Q: What are the minimum trace width and clearance values I should use for my PCB?
A: The minimum trace width and clearance values depend on factors such as the PCB manufacturing process, copper weight, and voltage requirements. Consult with your PCB manufacturer for their recommended values. -
Q: Can I import designs from other software into AutoDesk Eagle?
A: Yes, Eagle supports importing design files from various formats, such as DXF, BXL, and Gerber. However, some manual adjustments may be required to ensure compatibility. -
Q: How can I troubleshoot common issues encountered during PCB design and assembly?
A: Common issues include incorrect component placement, solder bridges, and poor connections. To troubleshoot, carefully inspect your PCB for visible defects, use a multimeter to test continuity, and refer to your schematic and board layout for proper component placement and orientation.
Conclusion
Designing and manufacturing PCBs using AutoDesk Eagle is a rewarding and educational experience for anyone interested in electronics. By following this step-by-step tutorial and adhering to best practices, you’ll be well on your way to creating professional-quality PCBs for your projects. Remember to continually refine your skills, explore advanced features, and engage with the Eagle community for further learning and inspiration.
Task | Time Estimate |
---|---|
Installation and Setup | 30 minutes |
Schematic Design | 2-4 hours |
Board Layout | 4-8 hours |
Manufacturing Preparation | 1-2 hours |
Assembly and Testing | 2-4 hours |
Note: Time estimates may vary depending on project complexity and designer experience level.
Happy PCB designing!
No responses yet