What is PCB Manufacturing?
Printed Circuit Board (PCB) manufacturing is the process of creating circuit boards that electrically connect and mechanically support electronic components using conductive pathways, tracks or signal traces etched from copper sheets laminated onto a non-conductive substrate. PCBs are used in virtually all electronic products including computers, smartphones, televisions, digital cameras, and more.
PCB manufacturing involves several key steps:
1. Design: Creating the schematic diagram and PCB layout using EDA software
2. Printing: Printing the circuit pattern on the substrate
3. Etching: Removing unwanted copper to leave behind the desired circuit
4. Drilling: Drilling holes for component leads and vias
5. Plating: Coating exposed copper with solder or other finish to prevent oxidation
6. Silkscreen: Adding silkscreened labels and symbols
7. Testing: Testing the PCB for proper functionality
What Makes 6 Layer PCBs Unique?
A 6 layer PCB contains three double-sided boards sandwiched together with insulating layers in between and vias connecting the different layers. This construction allows for higher component density and more complex circuits compared to simpler double-sided boards. 6 layer PCBs are commonly used in high-speed digital applications, advanced smartphones, servers, telecommunications equipment, and aerospace and military products that require maximum reliability and performance in minimal space.
The typical stack-up of a 6 layer PCB is as follows:
Layer | Description |
---|---|
Top | Components, copper traces, solder mask, silkscreen |
Ground plane | Copper pour connected to ground |
Signal 1 | Copper traces |
Power plane | Copper pour for power distribution |
Signal 2 | Copper traces |
Bottom | Components, copper traces, solder mask, silkscreen |
The dedicated ground and power planes help reduce electromagnetic interference (EMI) and maintain signal integrity. The signal layers are used for routing between components. Blind and buried vias provide connections between internal layers without using space on the outer layers.
6 Layer PCB Manufacturing Process
The manufacturing process for 6 layer PCBs follows the same general steps as other types of PCBs but requires tighter tolerances, more precise alignment, and additional pressing and drilling to create the multilayer structure. Here is an overview of how 6 layer PCBs are made:
Step 1: Inner Layer Printing
The manufacturing process begins with the inner layers. The desired circuit pattern for each inner layer is printed onto a copper clad laminate sheet using a photoresist and high-power UV laser or LDI (laser direct imaging) machine. The photoresist hardens when exposed to UV light, protecting the copper underneath.
Step 2: Inner Layer Etching
The unexposed photoresist is chemically removed and the unprotected copper is etched away using an alkaline or acidic solution, typically ammonium persulfate or cupric chloride. This leaves behind the desired copper traces and pads. The remaining photoresist is then stripped off.
Step 3: Inner Layer AOI
The inner layers undergo automated optical inspection (AOI) to check for any manufacturing defects such as open or short circuits, incorrect trace width or spacing, missing pads, etc. Any defective layers are discarded.
Step 4: Lamination
The four inner layers are sandwiched between sheets of prepreg (pre-impregnated fiberglass) and copper foil in a specific sequence based on the stack-up design. This multilayer structure is aligned using pin holes and then laminated together under high temperature and pressure in a hydraulic press. The heat and pressure cause the prepreg to melt and bond the layers together into a solid board.
Step 5: Drilling
After lamination, a computer-controlled drill machine is used to make holes in the board for plated through holes (PTHs), vias, and any required tooling holes. Smaller via holes may be created using lasers instead of mechanical drills. The holes are then cleaned and deburred.
Step 6: Plating
The drilled board is plated with copper to create conductive barrels connecting the inner layers. Additional copper is electroplated onto the outer layers and in the holes to the desired thickness. The outer layers are then printed and etched similar to the inner layers.
Step 7: Soldermask and Silkscreen
A soldermask coating is applied to the outer layers for insulation and protection, leaving the pads and holes exposed. The soldermask is typically green but other colors are available. A silkscreen layer is then printed on top of the soldermask to add component identifiers, warning symbols, manufacturer markings, and other visual indicators to aid in assembly, testing and troubleshooting.
Step 8: Surface Finish
A surface finish, such as HASL (hot air solder leveling), lead-free HASL, immersion silver, immersion tin, gold plating, or OSP (organic solderability preservative) is applied to the exposed copper to prevent oxidation and facilitate soldering. The choice of finish depends on the intended application, environmental requirements, and cost considerations.
Step 9: Electrical Test
The completed PCB undergoes electrical testing, such as flying probe or bed of nails test, to verify that all connections are correct and there are no unintended short or open circuits. Boundary scan testing may also be performed on boards with high pin-count BGA packages.
Step 10: Final Inspection
The PCBs are given a final visual inspection for any obvious defects before being packaged and shipped to the customer. Microsection analysis and other destructive testing may be performed on a sample basis for quality control purposes.
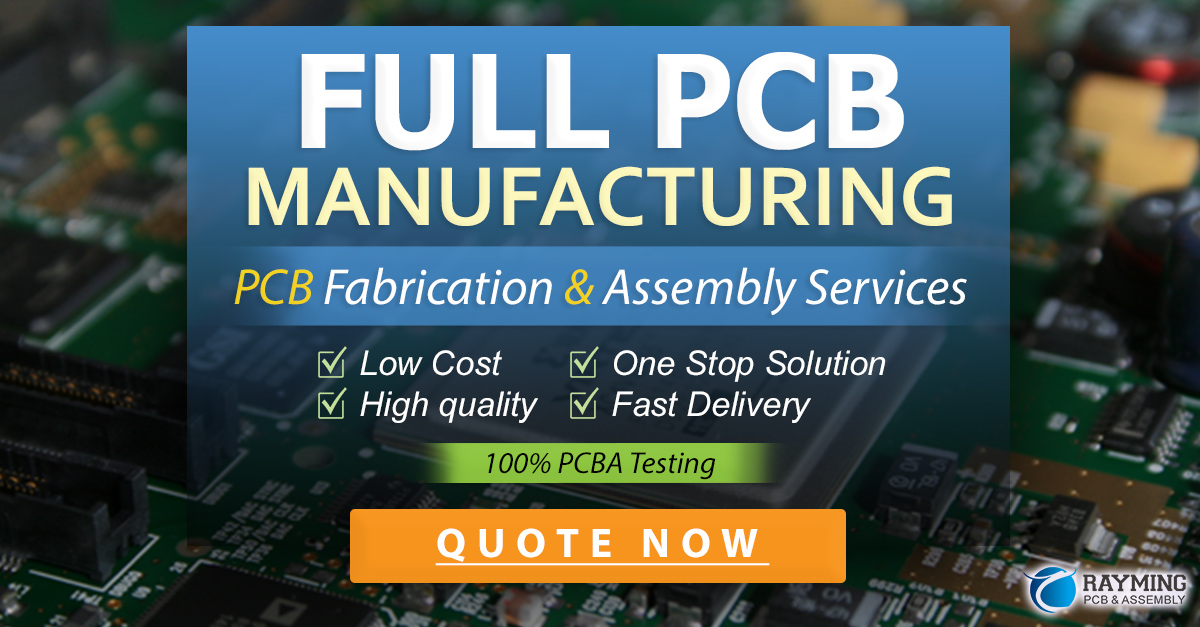
Advantages of 6 Layer PCBs
6 layer PCBs offer several benefits compared to simpler 2 or 4 layer boards:
-
Higher density: The additional layers allow for more routing space, enabling smaller boards with higher component density.
-
Better signal integrity: The dedicated power and ground planes provide a low-impedance path for return currents and help reduce crosstalk and EMI.
-
Improved thermal management: The internal planes can aid in heat dissipation, allowing for higher power handling capability.
-
Greater flexibility: 6 layer boards provide more design options and flexibility in terms of component placement, signal routing, and power distribution.
-
Enhanced reliability: The additional structure and shielding provided by the inner layers make 6 layer PCBs more durable and resistant to mechanical stress and environmental factors.
Disadvantages of 6 Layer PCBs
However, 6 layer PCBs also have some drawbacks:
-
Higher cost: The additional materials, processing steps, and tighter tolerances required make 6 layer boards more expensive than simpler designs.
-
Longer lead times: The more complex manufacturing process also takes longer, so 6 layer boards have longer lead times than 2 or 4 layer boards.
-
Design challenges: Designing 6 layer boards requires more skill and experience to ensure proper signal routing, impedance control, and EMC. Specialized EDA tools and simulation may be needed.
-
Limited repairability: The inner layers are not accessible for rework or repair, so any faults in the internal layers may render the entire board unusable.
FAQ
How much do 6 layer PCBs cost?
The cost of a 6 layer PCB depends on several factors such as size, quantity, materials, surface finish, and turnaround time. As a rough estimate, a 6 layer board might cost 2-3 times as much as a comparable 4 layer board and 4-5 times as much as a 2 layer board. For example, a 100x100mm 6 layer board in a quantity of 100 pieces might cost around $20-30 each, while the same size 4 layer board might be $10-15 each and a 2 layer board $5-8 each.
What are blind and buried vias?
Blind vias are holes that connect an outer layer to one or more inner layers, but do not go through the entire board. Buried vias connect two or more inner layers together without being visible on the outer layers. Both blind and buried vias are used to save space on the outer layers and provide more routing options, but they require additional drilling and plating steps and are therefore more expensive than through-hole vias.
What is the minimum hole size for a 6 layer PCB?
The minimum hole size depends on the thickness of the board and the capabilities of the manufacturer. For a typical 1.6mm thick 6 layer board, the minimum finished hole size is usually around 0.2-0.3mm (8-12mil). Smaller holes down to 0.1mm (4mil) may be possible with laser drilling and special processing, but will add to the cost and complexity of the board.
How long does it take to manufacture a 6 layer PCB?
The lead time for a 6 layer PCB depends on the complexity of the design, the quantity ordered, and the capabilities of the manufacturer. As a rough estimate, a standard 6 layer board might take 2-3 weeks from order to delivery, while an expedited order might be possible in 1-2 weeks. Very complex boards or large quantities may take 4 weeks or longer. It’s always best to check with the specific manufacturer for their current lead times.
Can I mix different copper weights on different layers?
Yes, it is possible to use different copper weights on different layers of a 6 layer PCB. For example, the outer layers might use 1oz (35µm) copper for better heat dissipation and current carrying capacity, while the inner layers might use 0.5oz (18µm) copper to save weight and cost. However, using mixed copper weights can add to the complexity and cost of the board, so it is typically only done when necessary for technical or economic reasons.
Conclusion
6 layer PCBs are a powerful option for designers who need to pack a lot of functionality into a small space while maintaining signal integrity and reliability. By understanding the unique manufacturing process and design considerations involved, you can take full advantage of the benefits of 6 layer construction while minimizing the drawbacks. When in doubt, consult with your PCB manufacturer early in the design process to ensure the best possible outcome for your project.
No responses yet