Introduction to High-Frequency PCB Design
High-frequency PCB design is a specialized field that requires careful consideration of various factors to ensure optimal performance and signal integrity. As electronic devices continue to push the boundaries of speed and bandwidth, designing PCBs that can effectively handle high-frequency signals becomes increasingly critical. In this article, we will explore 11 essential design rules that will help you create high-quality, high-frequency PCBs.
What is High-Frequency PCB Design?
High-frequency PCB design refers to the process of designing printed circuit boards that can operate effectively at high frequencies, typically above 100 MHz. At these frequencies, the behavior of signals on the PCB becomes more complex, and factors such as impedance matching, signal reflection, and crosstalk become more pronounced. To mitigate these issues and ensure reliable performance, designers must follow specific guidelines and best practices.
Why is High-Frequency PCB Design Important?
As technology advances, the demand for faster and more efficient electronic devices continues to grow. High-frequency PCB design plays a crucial role in meeting these demands by enabling:
- Faster data transmission rates
- Improved signal integrity
- Reduced electromagnetic interference (EMI)
- Enhanced overall system performance
By designing PCBs that can effectively handle high-frequency signals, engineers can create more advanced and reliable electronic devices across various industries, including telecommunications, automotive, aerospace, and consumer electronics.
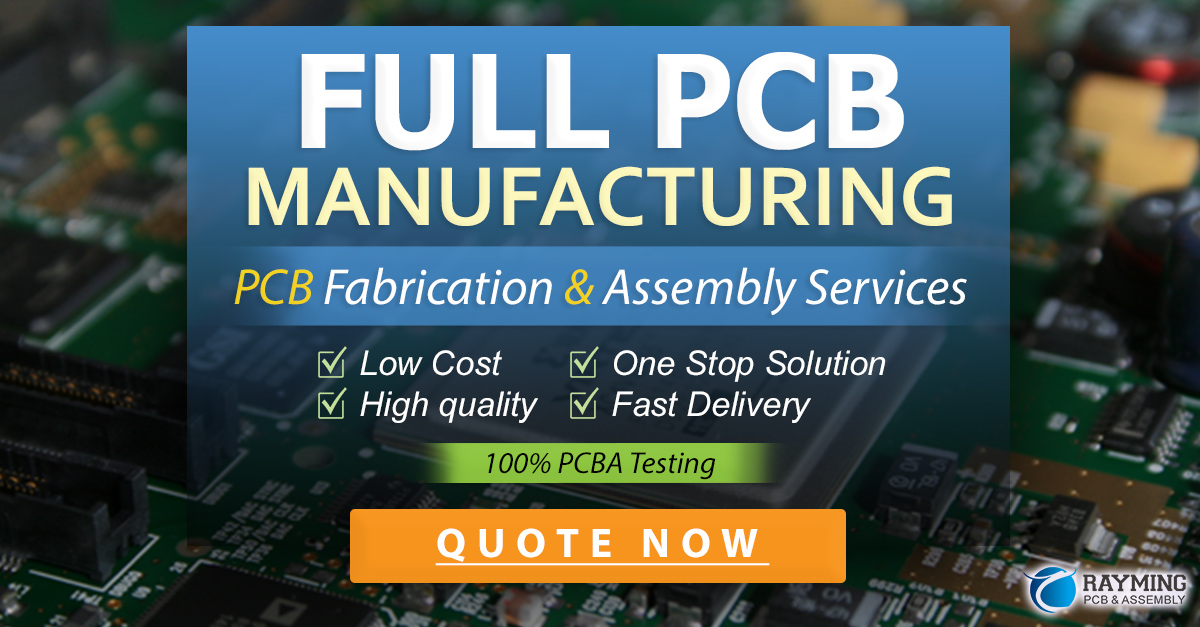
11 Clearest Design Rules for High-Frequency PCBs
To achieve optimal performance and signal integrity in high-frequency PCB design, follow these 11 essential design rules:
1. Minimize Loop Areas
Minimizing loop areas is crucial in high-frequency PCB design to reduce the impact of inductance and electromagnetic interference (EMI). Loop areas are created when a signal trace and its corresponding return path form a closed loop. The larger the loop area, the greater the inductance and the more susceptible the circuit becomes to EMI.
To minimize loop areas:
– Keep signal traces and their return paths as close together as possible
– Use ground planes to provide a low-impedance return path for high-frequency signals
– Avoid routing signal traces over split planes or gaps in the ground plane
Loop Area Size | Inductance | EMI Susceptibility |
---|---|---|
Small | Low | Low |
Medium | Moderate | Moderate |
Large | High | High |
2. Maintain Proper Impedance Matching
Impedance matching is essential in high-frequency PCB design to ensure that signals propagate efficiently and to minimize reflections. When the impedance of a signal trace does not match the impedance of the source or load, a portion of the signal energy is reflected back, leading to signal distortion and degradation.
To maintain proper impedance matching:
– Calculate the required trace width and spacing based on the desired characteristic impedance (typically 50Ω or 75Ω)
– Use controlled impedance design techniques, such as stripline or microstrip, to maintain consistent impedance along the signal path
– Avoid abrupt changes in trace width or layer transitions, as these can cause impedance discontinuities
3. Use Appropriate Decoupling Capacitors
Decoupling capacitors play a vital role in high-frequency PCB design by providing a stable power supply to active components and reducing noise on the power rails. These capacitors act as local energy reservoirs, supplying current during transient demands and filtering out high-frequency noise.
To use decoupling capacitors effectively:
– Place decoupling capacitors as close to the power pins of active components as possible
– Use a combination of capacitor values to target different frequency ranges (e.g., 0.1μF for high frequencies, 1μF for mid-frequencies, and 10μF for low frequencies)
– Minimize the inductance of the capacitor mounting by using short, wide traces and multiple vias
4. Implement Proper Grounding Techniques
Proper grounding is critical in high-frequency PCB design to maintain signal integrity and minimize EMI. A well-designed grounding scheme provides a low-impedance return path for high-frequency signals and helps to contain electromagnetic fields.
To implement proper grounding techniques:
– Use a solid ground plane whenever possible to provide a low-impedance return path
– Avoid splitting the ground plane, as this can create discontinuities and increase EMI
– Use multiple vias to connect ground planes on different layers, minimizing inductance and ensuring a continuous return path
5. Minimize Crosstalk
Crosstalk occurs when signals from one trace couple onto adjacent traces, causing signal distortion and potentially leading to logic errors. In high-frequency PCB design, crosstalk becomes more pronounced due to the increased coupling between traces.
To minimize crosstalk:
– Increase the spacing between adjacent signal traces
– Use guard traces or ground traces between sensitive signal traces to provide shielding
– Route critical signals on different layers, separated by ground planes
– Use differential signaling techniques for high-speed signals, as they are less susceptible to crosstalk
6. Optimize Via Design
Vias are essential for connecting traces on different layers of a PCB, but they can also introduce discontinuities and degrade signal integrity at high frequencies. Optimizing via design is crucial to minimize the impact of vias on signal quality.
To optimize via design:
– Minimize the number of vias in high-speed signal paths
– Use smaller via diameters to reduce capacitance and inductance
– Employ via shielding techniques, such as ground vias or coaxial vias, to contain electromagnetic fields
– Consider using blind or buried vias to reduce the length of the signal path
7. Route High-Speed Signals Carefully
Routing high-speed signals requires careful consideration to maintain signal integrity and minimize reflections. Proper routing techniques help to ensure that signals propagate efficiently and with minimal distortion.
To route high-speed signals effectively:
– Keep high-speed signal traces as short as possible to minimize delay and attenuation
– Avoid sharp corners and use gentle bends (45° or 90° angles) to minimize reflections
– Maintain consistent trace width and spacing to prevent impedance discontinuities
– Use length matching techniques for parallel high-speed traces to ensure synchronous arrival times
8. Implement Electromagnetic Shielding
Electromagnetic shielding is essential in high-frequency PCB design to contain electromagnetic fields and minimize EMI. Shielding helps to prevent the coupling of unwanted signals onto sensitive traces and reduces the emission of electromagnetic energy from the PCB.
To implement electromagnetic shielding:
– Use metal enclosures or conductive coatings to shield the entire PCB
– Incorporate shielding cans or compartments to isolate sensitive components or circuits
– Use shielded connectors and cables for external connections
– Implement proper grounding techniques to ensure the effectiveness of shielding
9. Consider Thermal Management
Thermal management is an important aspect of high-frequency PCB design, as high-speed components often generate significant heat. Proper thermal management helps to ensure the reliability and longevity of the PCB and its components.
To address thermal management:
– Identify heat-generating components and place them strategically to minimize thermal interactions
– Use thermal vias or heat sinks to dissipate heat away from critical components
– Incorporate thermal relief pads for soldered components to prevent thermal stress
– Consider using high-temperature materials, such as ceramics or polyimides, for high-heat applications
10. Perform Signal Integrity Simulations
Signal integrity simulations are valuable tools in high-frequency PCB design, allowing designers to analyze and optimize the performance of the PCB before fabrication. These simulations help to identify potential issues and validate design choices.
To perform signal integrity simulations:
– Use electronic design automation (EDA) tools with built-in signal integrity analysis capabilities
– Create accurate models of the PCB, including trace geometry, material properties, and component characteristics
– Simulate critical signal paths to assess impedance matching, reflections, and crosstalk
– Analyze simulation results and make necessary adjustments to the design to improve performance
11. Collaborate with PCB Manufacturers
Collaborating with experienced PCB manufacturers is essential for successful high-frequency PCB design. These manufacturers have the expertise and capabilities to fabricate high-quality PCBs that meet the stringent requirements of high-frequency applications.
To effectively collaborate with PCB manufacturers:
– Communicate your design requirements and constraints clearly
– Provide comprehensive documentation, including schematics, layout files, and bill of materials
– Discuss any special manufacturing considerations, such as controlled impedance or advanced materials
– Work closely with the manufacturer to resolve any design or fabrication issues that may arise
Frequently Asked Questions (FAQ)
-
What is the difference between high-frequency and low-frequency PCB design?
High-frequency PCB design focuses on managing the complex behavior of signals at frequencies typically above 100 MHz, while low-frequency PCB design deals with signals below this threshold. High-frequency design requires more stringent control of factors such as impedance matching, signal reflection, and crosstalk. -
How do I determine the appropriate trace width and spacing for controlled impedance?
To determine the appropriate trace width and spacing for controlled impedance, you need to consider factors such as the desired characteristic impedance (typically 50Ω or 75Ω), the dielectric constant of the PCB material, and the thickness of the dielectric layer. You can use online calculators or consult with your PCB manufacturer to determine the specific values for your design. -
What are some common materials used in high-frequency PCB design?
Common materials used in high-frequency PCB design include: - FR-4: A cost-effective and widely used material suitable for frequencies up to a few GHz
- Rogers RO4000 series: High-performance materials with low dielectric loss and stable properties at high frequencies
- Isola I-Speed: A low-loss material designed for high-speed digital applications
-
PTFE (Teflon): A low-loss material with excellent thermal and chemical stability, suitable for high-frequency applications
-
How can I minimize the impact of vias on signal integrity?
To minimize the impact of vias on signal integrity, you can: - Minimize the number of vias in high-speed signal paths
- Use smaller via diameters to reduce capacitance and inductance
- Employ via shielding techniques, such as ground vias or coaxial vias, to contain electromagnetic fields
-
Consider using blind or buried vias to reduce the length of the signal path
-
What are some common signal integrity issues in high-frequency PCB design?
Common signal integrity issues in high-frequency PCB design include: - Impedance mismatches, which cause signal reflections and distortion
- Crosstalk, where signals from one trace couple onto adjacent traces
- EMI, which can cause interference with other electronic devices
- Signal attenuation and delay, which can degrade signal quality and timing
Conclusion
Designing high-frequency PCBs requires a deep understanding of the complex behavior of signals at elevated frequencies and adherence to specific design rules and best practices. By following the 11 essential design rules outlined in this article, you can create high-quality, high-frequency PCBs that deliver optimal performance and signal integrity. Remember to minimize loop areas, maintain proper impedance matching, use appropriate decoupling capacitors, implement proper grounding techniques, and collaborate closely with experienced PCB manufacturers. With careful consideration and attention to detail, you can successfully navigate the challenges of high-frequency PCB design and create reliable, high-performance electronic devices.
No responses yet