The Chemical Formula and Structure of PTFE
The chemical formula for PTFE is (C2F4)n, where n is the number of repeating tetrafluoroethylene monomers that make up the polymer chain. PTFE has a very simple chemical structure:
[F-CF2-CF2]n
In this structure, the carbon atoms are surrounded by fluorine atoms, forming very strong carbon-fluorine bonds. A single PTFE macromolecule can contain tens of thousands of –CF2– repeating units, resulting in a high molecular weight.
Here are some key facts about PTFE’s chemical structure and properties:
-
PTFE is a linear polymer, meaning the –CF2– units are arranged in a straight chain without branching or crosslinking between chains.
-
The carbon-fluorine bonds in PTFE are extremely strong, with a bond dissociation energy of about 552 kJ/mol. For comparison, a carbon-carbon single bond has a dissociation energy of about 347 kJ/mol.
-
The high strength of the C-F bonds, combined with the shielding effect of the fluorine atoms, makes PTFE very resistant to chemical attack. PTFE is inert to most chemicals, including strong acids and bases.
-
The fluorine atoms are also responsible for PTFE’s low surface energy and non-stick properties. Fluorine is highly electronegative, meaning it strongly attracts electrons. This causes the electron density around the carbon backbone to be pulled toward the fluorines, resulting in a non-polar, low-energy surface that repels other substances.
-
PTFE has a very high melting point around 327°C (620°F) due to the strength of the C-F bonds. However, PTFE degrades before reaching its theoretical melting point, undergoing depolymerization at temperatures above 350°C (662°F).
Polymerization of Tetrafluoroethylene
PTFE is made by polymerizing tetrafluoroethylene (TFE) monomers. TFE is a colorless, odorless, flammable gas at room temperature with the formula F2C=CF2. Here is an overview of the PTFE polymerization process:
- TFE monomer is synthesized by pyrolysis of chlorodifluoromethane at 600-800°C. The reaction is:
CHClF2 → CF2=CF2 + HCl
-
The TFE gas is then pressurized and fed into a stirred aqueous reaction vessel along with a small amount of initiator, such as ammonium persulfate.
-
Free-radical polymerization of the TFE occurs, building the PTFE polymer chains:
n F2C=CF2 → [-CF2-CF2-]n
-
The resulting PTFE dispersion is filtered, washed, and dried into a white, free-flowing powder.
-
The PTFE powder can then be further processed into various forms, such as sheets, rods, tubes, films, fibers, or applied as a coating.
The table below summarizes the typical composition of PTFE:
Component | Amount |
---|---|
Tetrafluoroethylene | > 99% |
Perfluoropropylvinylether (PPVE) | 0 – 0.5% |
Initiator and surfactant residues | < 0.1% |
PPVE is a co-monomer that can be incorporated in small amounts to modify PTFE’s properties, such as increasing its resistance to high temperatures and radiation. The initiators and surfactants used in the polymerization process remain in trace amounts in the final PTFE resin.
Fillers and Additives in PTFE
While pure PTFE has many desirable properties, it also has some limitations. PTFE has poor abrasion resistance, high thermal expansion, and a tendency to creep under load. To improve its mechanical properties and performance for certain applications, various fillers can be incorporated into PTFE. Some common PTFE fillers include:
-
Glass fibers: Adding chopped glass fibers to PTFE improves its dimensional stability, creep resistance, and compressive strength. Typical glass fiber content is 5-40% by weight.
-
Carbon/graphite: Carbon or graphite powder can be added to PTFE to increase its thermal and electrical conductivity while maintaining low friction and wear. Typical carbon content is 5-30% by weight.
-
Bronze: Bronze powder is used as a filler in PTFE for bearings and bushings. The bronze improves PTFE’s compressive strength and wear resistance. Typical bronze content is 40-60% by weight.
-
Molybdenum disulfide: MoS2 is used as a filler in PTFE to further enhance its lubricity and lower its friction coefficient, especially in dry or vacuum conditions. Typical MoS2 content is 2-10% by weight.
Here is a table comparing some properties of filled and unfilled PTFE:
Property | Unfilled PTFE | 25% Glass-Filled PTFE | 60% Bronze-Filled PTFE |
---|---|---|---|
Specific Gravity | 2.16 | 2.30 | 3.80 |
Tensile Strength (MPa) | 20-35 | 14 | 8 |
Elongation at Break (%) | 350-550 | 150-300 | 130-260 |
Coefficient of Friction | 0.05-0.10 | 0.12-0.25 | 0.07-0.12 |
Continuous Service Temp (°C) | 260 | 260 | 260 |
Thermal Conductivity (W/m·K) | 0.25 | 0.42 | 0.70 |
As the table shows, fillers generally increase PTFE’s density and reduce its tensile strength and elongation compared to virgin PTFE. However, they can significantly improve properties like wear resistance, creep resistance, and thermal conductivity for specific applications.
In addition to fillers, small amounts of other additives may be compounded into PTFE, such as pigments for coloring, antioxidants, or UV stabilizers. The type and amount of fillers and additives used depends on the end-use requirements.
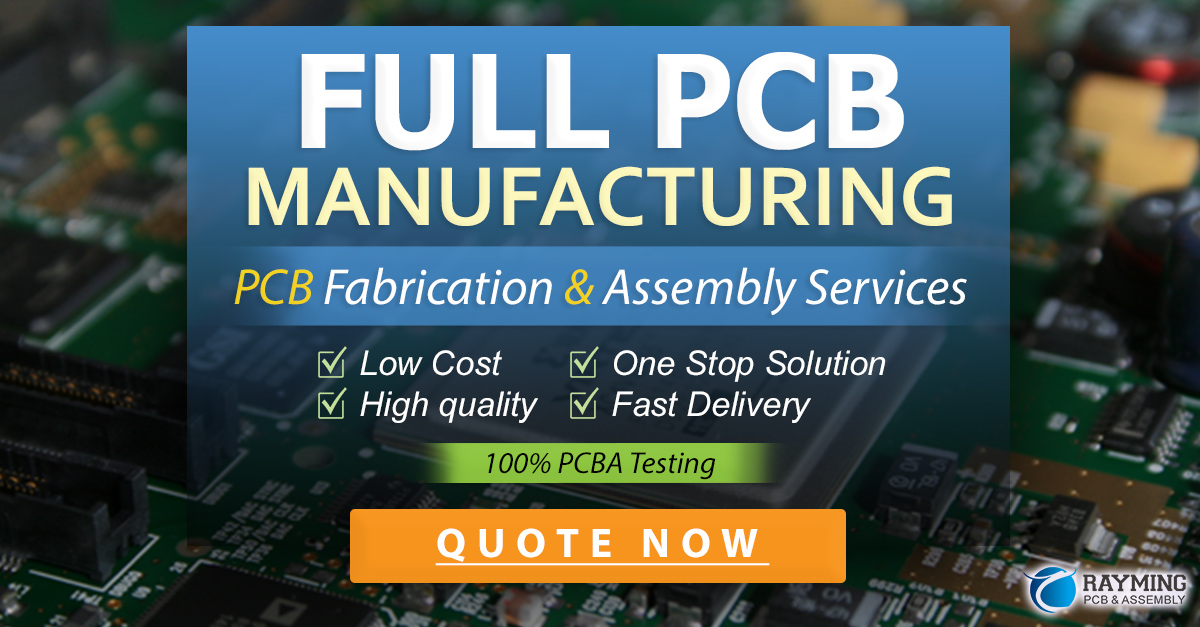
Safety and Environmental Concerns with PTFE
PTFE is generally considered a safe and inert material. It is non-toxic, biologically inert, and is even used in medical implants. However, there are some safety and environmental concerns associated with PTFE and its processing:
PFOA in PTFE Manufacturing
Historically, the polymerization of TFE into PTFE was carried out using a surfactant called perfluorooctanoic acid (PFOA) as a processing aid. PFOA is a type of perfluorinated compound (PFC) that has been linked to various health and environmental concerns.
Studies have shown that PFOA is persistent in the environment, bioaccumulative in wildlife and humans, and toxic at very low concentrations. It has been associated with kidney and testicular cancer, thyroid disease, high cholesterol, and developmental problems.
Due to these concerns, major PTFE manufacturers phased out the use of PFOA in their production by 2015. Today, PTFE is manufactured using alternative surfactants that have better environmental and toxicological profiles, such as GenX. Modern PTFE products are considered PFOA-free, with PFOA levels below detectable limits.
Thermal Decomposition of PTFE
While PTFE is very stable and heat-resistant under normal conditions, it can start to decompose if heated above its service temperature of 260°C (500°F). The thermal decomposition of PTFE releases toxic gases, primarily carbonyl fluoride and ultra-fine particulates.
Inhalation of PTFE decomposition products can cause polymer fume fever, a temporary flu-like illness. Symptoms include chills, headache, fever, and chest tightness. The condition is also known as “Teflon flu” when caused by overheated PTFE cookware.
To prevent exposure to PTFE decomposition products:
-
Never heat PTFE above 260°C. Avoid using Teflon-coated cookware on high heat or under broilers.
-
Ensure proper ventilation when processing PTFE at high temperatures.
-
Do not use PTFE in applications where it may be exposed to fire or flames.
-
Avoid smoking tobacco products around PTFE, as the hot ash can cause decomposition.
When used within its recommended temperature range and with proper precautions, PTFE is safe and does not off-gas or leach harmful compounds.
PTFE Waste and Recyclability
Like most plastics, PTFE is not biodegradable and can persist in the environment for a long time if not properly disposed of. PTFE waste, such as scrap or used products, should be recycled or incinerated at high temperatures in an authorized facility to prevent environmental release.
PTFE is not easily recycled due to its resistance to high temperatures and chemicals, which makes it difficult to melt and reform. However, some PTFE recycling methods have been developed, such as:
-
Cryogenic grinding: Cooling PTFE waste with liquid nitrogen, then grinding it into a fine powder that can be used as a filler or additive in other materials.
-
Pyrolysis: Heating PTFE waste in the absence of oxygen to break it down into smaller fluorinated compounds that can be recovered and reused.
-
Sintering: Compressing PTFE powder waste under high pressure and temperature to form new solid shapes.
Recycling PTFE is still not widely done and most PTFE waste ends up in landfills or incinerators. Continuing research into effective PTFE recycling methods is important for reducing the environmental impact of this prevalent material.
Frequently Asked Questions
1. Is Teflon safe to use for cooking?
Yes, Teflon (PTFE) coated cookware is safe to use under normal cooking conditions. Modern Teflon pans are PFOA-free and do not leach or off-gas harmful compounds during normal use. However, Teflon can start to break down and release toxic fumes if heated above 500°F (260°C). To use Teflon safely, use low to medium heat, don’t preheat empty pans, and discard pans that are scratched or flaking.
2. Is Teflon microwave-safe?
Yes, Teflon is generally microwave-safe. PTFE is transparent to microwaves and does not absorb microwave energy. It will not break down or release fumes under normal microwave use. However, make sure the item is labeled as microwave-safe by the manufacturer, as some Teflon-coated items may have metal components or reinforcements that can cause arcing in the microwave.
3. Does Teflon cause cancer?
No, there is no evidence that Teflon (PTFE) itself causes cancer. PTFE is biologically inert and not metabolized by the body. However, PFOA, a chemical formerly used in Teflon manufacturing, has been linked to increased cancer risk. PFOA was phased out by 2015, and modern Teflon products are considered PFOA-free and safe to use.
4. How long does Teflon last?
The lifespan of a Teflon coating depends on factors such as usage, cleaning, and storage. With proper care, a Teflon non-stick pan can last 3-5 years on average. Signs that it’s time to replace your Teflon pan include:
- Scratches or chips in the coating
- Flaking or peeling of the coating
- Food starting to stick or burn onto the surface
To prolong the life of your Teflon cookware, avoid using metal utensils, don’t soak in water, and handwash with non-abrasive sponges.
5. Can Teflon be recycled?
Teflon (PTFE) is difficult to recycle because of its resistance to high temperatures and chemicals, which makes it challenging to melt down and reform. Most PTFE waste ends up in landfills or incinerators. However, some specialized recycling methods for PTFE have been developed, such as cryogenic grinding, pyrolysis, and sintering. Continuing research is being done to find more effective and scalable ways to recycle PTFE and reduce its environmental impact.
No responses yet