PCB composition: An Overview
PCB chips are composed of several layers of materials, each serving a specific purpose in the overall functioning of the circuit board. The primary components of a PCB chip include:
- Substrate
- Copper foil
- Solder mask
- Silkscreen
- Surface finish
Let’s explore each of these components in detail.
Substrate: The Foundation of PCB Chips
The substrate is the base material upon which the other layers of the PCB chip are built. It provides the necessary insulation and mechanical support for the electronic components. The most common substrate materials used in PCB manufacturing are:
-
FR-4 (Flame Retardant 4): A composite material made of woven fiberglass cloth impregnated with an epoxy resin. FR-4 is the most widely used substrate due to its excellent electrical insulation properties, mechanical strength, and thermal stability.
-
CEM-1 (Composite Epoxy Material 1): A composite material consisting of a cellulose paper core with woven fiberglass reinforcement, impregnated with an epoxy resin. CEM-1 is a more cost-effective alternative to FR-4 but offers lower performance and reliability.
-
Polyimide: A high-performance polymer known for its exceptional thermal stability, chemical resistance, and mechanical strength. Polyimide substrates are commonly used in applications that require high temperature tolerance or flexibility, such as aerospace and military electronics.
-
PTFE (Polytetrafluoroethylene): A synthetic fluoropolymer with excellent dielectric properties, low dissipation factor, and high thermal stability. PTFE substrates are often used in high-frequency applications, such as radar and satellite communication systems.
Substrate Material | Dielectric Constant | Dissipation Factor | Thermal Stability | Typical Applications |
---|---|---|---|---|
FR-4 | 4.5 | 0.02 | Good | General-purpose PCBs |
CEM-1 | 4.7 | 0.03 | Fair | Low-cost consumer electronics |
Polyimide | 3.5 | 0.002 | Excellent | High-temperature and flexible PCBs |
PTFE | 2.1 | 0.0002 | Excellent | High-frequency PCBs |
Copper Foil: The Conductive Layer
Copper foil is the conductive layer that forms the electrical connections between components on the PCB chip. It is typically laminated onto the substrate using heat and pressure. The thickness of the copper foil is measured in ounces per square foot (oz/ft²), with common thicknesses ranging from 0.5 oz/ft² to 2 oz/ft².
The copper foil is patterned using a photolithographic process to create the desired circuit layout. This process involves:
- Applying a photoresist layer on top of the copper foil
- Exposing the photoresist to UV light through a photomask containing the circuit pattern
- Developing the photoresist to remove the exposed areas
- Etching away the unwanted copper using a chemical etchant
- Stripping off the remaining photoresist
Solder Mask: Protecting the Copper Traces
The solder mask is a thin, protective layer applied over the copper traces on the PCB chip. Its primary functions are to:
- Prevent accidental short circuits by providing insulation between adjacent copper traces
- Protect the copper from oxidation and environmental damage
- Provide a surface for applying the silkscreen layer
Solder masks are typically made of a liquid photoimageable polymer that is applied, exposed, and developed in a similar manner to the photoresist used for patterning the copper foil. The most common colors for solder masks are green, red, and blue, although other colors are available for specific applications or aesthetic purposes.
Silkscreen: Labeling and Identification
The silkscreen layer is a non-conductive, ink-based layer that is applied on top of the solder mask. Its primary purpose is to provide labeling and identification for the components and connectors on the PCB chip. The silkscreen layer typically includes:
- Component outlines and reference designators
- Polarity markers for polarized components (e.g., electrolytic capacitors, diodes)
- Test points and fiducial markers for automated assembly and testing
- Company logos, part numbers, and revision information
The silkscreen is usually applied using a screen printing process, where the ink is forced through a fine mesh screen onto the PCB surface. The most common color for silkscreen is white, as it provides good contrast against the darker solder mask colors.
Surface Finish: Protecting and Enhancing Solderability
The surface finish is a thin, metallic coating applied to the exposed copper pads on the PCB chip. Its primary functions are to:
- Protect the copper from oxidation and corrosion
- Enhance the solderability of the pads for component assembly
- Provide a better electrical contact between the PCB and the components
There are several types of surface finishes used in PCB manufacturing, each with its own advantages and disadvantages:
-
HASL (Hot Air Solder Leveling): A tin-lead alloy is applied to the copper pads and then leveled using hot air. HASL is the most common and cost-effective surface finish but can result in uneven pad surfaces.
-
ENIG (Electroless Nickel Immersion Gold): A layer of nickel is first deposited on the copper pads, followed by a thin layer of gold. ENIG provides excellent solderability and shelf life but is more expensive than HASL.
-
OSP (Organic Solderability Preservative): A thin, organic coating is applied to the copper pads to protect them from oxidation. OSP is a cost-effective and environmentally friendly option but has a limited shelf life.
-
Immersion Silver: A thin layer of silver is deposited on the copper pads. Immersion silver offers good solderability and electrical conductivity but can tarnish over time.
Surface Finish | Thickness (μm) | Shelf Life | Solderability | Typical Applications |
---|---|---|---|---|
HASL | 1-20 | 6-12 months | Good | General-purpose PCBs |
ENIG | 3-7 (Ni), 0.05-0.2 (Au) | 12+ months | Excellent | High-reliability PCBs |
OSP | 0.2-0.5 | 3-6 months | Good | Low-cost, lead-free PCBs |
Immersion Silver | 0.1-0.3 | 6-12 months | Very Good | High-frequency and RF PCBs |
PCB Fabrication Process
The fabrication of PCB chips involves several steps, from designing the circuit layout to the final assembly and testing. The main stages in the PCB fabrication process are:
-
Design: The circuit schematic and layout are created using Electronic Design Automation (EDA) software. The design is then checked for errors and optimized for manufacturability.
-
Substrate Preparation: The substrate material is cut to the required size and thickness, and any necessary holes are drilled.
-
Copper Foil Lamination: The copper foil is laminated onto the substrate using heat and pressure.
-
Photolithography: The copper foil is patterned using the photolithographic process described earlier.
-
Etching: The unwanted copper is removed using a chemical etchant, leaving the desired circuit pattern.
-
Solder Mask Application: The solder mask is applied, exposed, and developed to protect the copper traces.
-
Silkscreen Printing: The silkscreen layer is applied using the screen printing process.
-
Surface Finish Application: The chosen surface finish is applied to the exposed copper pads.
-
Electrical Testing: The PCB is tested for continuity, short circuits, and other electrical properties to ensure functionality.
-
Assembly and Final Testing: The electronic components are soldered onto the PCB, and the final assembly is tested for performance and reliability.
Advantages of PCB Chips
PCB chips offer several advantages over other methods of connecting and supporting electronic components:
-
Compact Size: PCB chips allow for the miniaturization of electronic devices by providing a dense, compact platform for mounting components.
-
Reliability: The robust construction and protective layers of PCB chips ensure reliable performance, even in harsh environments.
-
Cost-Effectiveness: Mass production of PCB chips using automated processes makes them a cost-effective solution for electronic manufacturing.
-
Customization: PCB chips can be easily customized to meet specific design requirements, such as unique shapes, sizes, and component layouts.
-
Improved Signal Integrity: The careful design and layout of PCB chips can minimize signal interference and improve overall system performance.
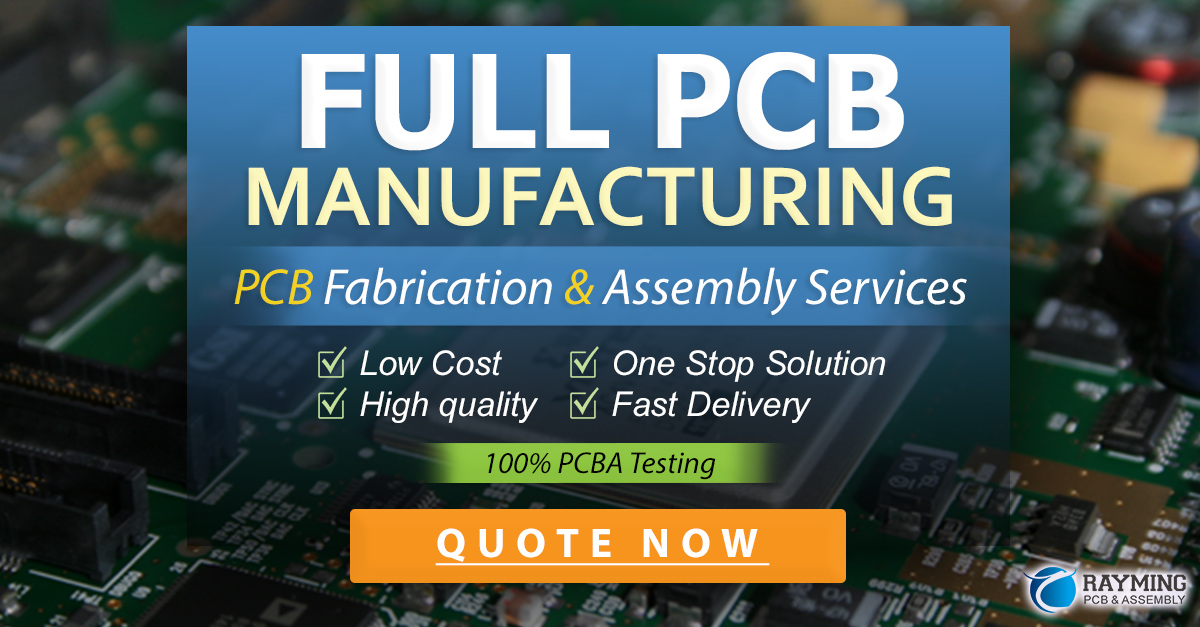
Applications of PCB Chips
PCB chips find applications in a wide range of industries and products, including:
-
Consumer Electronics: Smartphones, tablets, laptops, and wearable devices
-
Automotive Electronics: Engine control units, infotainment systems, and sensor modules
-
Medical Devices: Diagnostic equipment, implantable devices, and patient monitoring systems
-
Industrial Automation: Process control systems, robotics, and data acquisition devices
-
Aerospace and Defense: Avionics, satellite communication systems, and military equipment
-
Internet of Things (IoT): Smart home devices, remote sensing nodes, and connected appliances
-
Power Electronics: Switchmode power supplies, motor drives, and renewable energy systems
As technology continues to advance, the demand for more complex and high-performance PCB chips will only increase, driving innovation in materials, manufacturing processes, and design methodologies.
Frequently Asked Questions (FAQ)
-
What is the difference between a PCB and a PCB chip?
A PCB (Printed Circuit Board) is the entire board that contains the electronic components and the interconnections between them. A PCB chip, on the other hand, refers to the specific area on the PCB where a single integrated circuit (IC) or chip is mounted. -
Can PCB chips be repaired if damaged?
In most cases, damaged PCB chips cannot be repaired and need to be replaced entirely. However, if the damage is limited to the surface finish or solder mask, it may be possible to repair the affected area using specialized techniques. -
How long do PCB chips typically last?
The lifespan of a PCB chip depends on various factors, such as the quality of the materials used, the manufacturing process, and the environmental conditions in which it operates. Generally, well-designed and manufactured PCB chips can last for several years or even decades, depending on the application. -
Are PCB chips recyclable?
Yes, PCB chips can be recycled to recover valuable materials such as copper, gold, and silver. However, the recycling process is complex and requires specialized facilities to ensure proper handling and disposal of hazardous substances. -
What are the environmental concerns associated with PCB manufacturing?
The PCB manufacturing process involves the use of various chemicals and materials that can have negative environmental impacts if not properly managed. These concerns include the release of volatile organic compounds (VOCs), the generation of hazardous waste, and the potential for water and soil contamination. Responsible manufacturers employ strict environmental controls and adhere to regulations to minimize these risks.
In conclusion, PCB chips are essential components in modern electronics, providing a reliable and efficient means of connecting and supporting various electronic components. Understanding the composition, fabrication process, and advantages of PCB chips is crucial for engineers, manufacturers, and enthusiasts to design, develop, and produce high-quality electronic devices. As technology advances, the importance of PCB chips will only continue to grow, driving innovation and shaping the future of the electronics industry.
No responses yet