Introduction to Plastic PCB
Plastic PCBs, also known as printed circuit boards made from plastic materials, have gained popularity in recent years due to their unique properties and advantages over traditional PCB materials. These boards are manufactured using a variety of plastic polymers, each with its own set of characteristics that make them suitable for specific applications. In this article, we will explore the different types of plastics used in PCB manufacturing, their properties, and their applications.
Types of Plastics Used in PCB Manufacturing
There are several types of plastics commonly used in the production of PCBs. These include:
- Polyimide (PI)
- Polyethylene Terephthalate (PET)
- Polyethylene Naphthalate (PEN)
- Liquid Crystal Polymer (LCP)
- Polycarbonate (PC)
Each of these plastics has its own unique set of properties that make them suitable for different applications. Let’s explore each of these materials in more detail.
Polyimide (PI) PCBs
What is Polyimide?
Polyimide (PI) is a high-performance plastic material known for its excellent thermal stability, chemical resistance, and mechanical strength. It is a popular choice for manufacturing PCBs due to its ability to withstand high temperatures and its low dielectric constant.
Properties of Polyimide PCBs
Property | Value |
---|---|
Glass Transition Temperature (Tg) | 360-410°C |
Dielectric Constant (at 1 MHz) | 3.4-3.5 |
Dissipation Factor (at 1 MHz) | 0.002-0.003 |
Tensile Strength | 150-300 MPa |
Elongation at Break | 10-50% |
Moisture Absorption | 0.5-2.5% |
Polyimide PCBs offer several advantages, including:
- High heat resistance
- Excellent chemical resistance
- Low dielectric constant and dissipation factor
- Good mechanical strength and flexibility
- Low moisture absorption
Applications of Polyimide PCBs
Polyimide PCBs are widely used in various industries, such as:
- Aerospace and defense
- Automotive electronics
- High-speed digital applications
- Flexible electronics
- Medical devices
Polyethylene Terephthalate (PET) PCBs
What is PET?
Polyethylene Terephthalate (PET) is a thermoplastic polymer commonly used in the production of PCBs. It is known for its excellent electrical properties, dimensional stability, and resistance to moisture and chemicals.
Properties of PET PCBs
Property | Value |
---|---|
Glass Transition Temperature (Tg) | 70-80°C |
Dielectric Constant (at 1 MHz) | 3.0-3.2 |
Dissipation Factor (at 1 MHz) | 0.002-0.003 |
Tensile Strength | 50-70 MPa |
Elongation at Break | 50-300% |
Moisture Absorption | 0.1-0.3% |
PET PCBs offer several advantages, including:
- Good electrical insulation properties
- High dimensional stability
- Excellent resistance to moisture and chemicals
- Good mechanical strength and flexibility
- Low cost compared to other plastic PCB materials
Applications of PET PCBs
PET PCBs are commonly used in various applications, such as:
- Consumer electronics
- Telecommunications
- Automotive electronics
- Medical devices
- RFID tags and smart cards
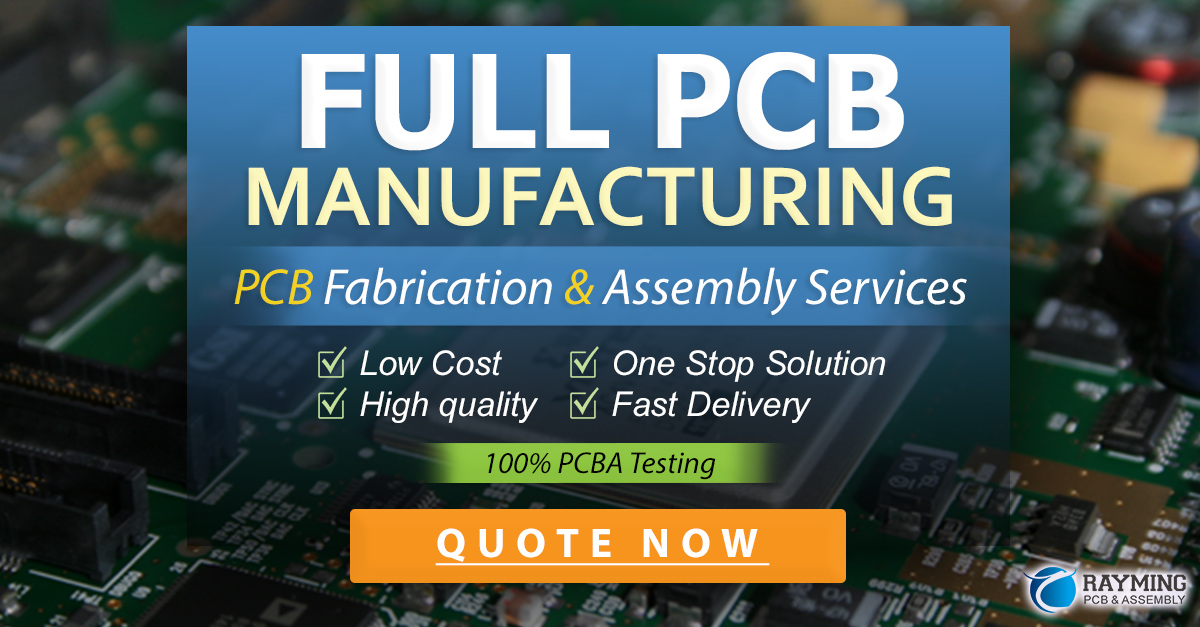
Polyethylene Naphthalate (PEN) PCBs
What is PEN?
Polyethylene Naphthalate (PEN) is a high-performance plastic material similar to PET but with improved thermal and mechanical properties. It is known for its high glass transition temperature, excellent dimensional stability, and low moisture absorption.
Properties of PEN PCBs
Property | Value |
---|---|
Glass Transition Temperature (Tg) | 120-130°C |
Dielectric Constant (at 1 MHz) | 3.0-3.2 |
Dissipation Factor (at 1 MHz) | 0.002-0.003 |
Tensile Strength | 70-100 MPa |
Elongation at Break | 50-100% |
Moisture Absorption | 0.1-0.3% |
PEN PCBs offer several advantages, including:
- Higher glass transition temperature compared to PET
- Excellent dimensional stability
- Low moisture absorption
- Good mechanical strength and flexibility
- Improved chemical resistance
Applications of PEN PCBs
PEN PCBs are used in various applications that require higher thermal stability and improved performance compared to PET PCBs, such as:
- Automotive electronics
- High-temperature applications
- Flexible displays
- Solar cells
- High-frequency applications
Liquid Crystal Polymer (LCP) PCBs
What is LCP?
Liquid Crystal Polymer (LCP) is a high-performance thermoplastic material known for its exceptional electrical properties, low moisture absorption, and excellent dimensional stability. It is a popular choice for high-frequency and high-speed applications due to its low dielectric constant and dissipation factor.
Properties of LCP PCBs
Property | Value |
---|---|
Glass Transition Temperature (Tg) | 280-350°C |
Dielectric Constant (at 1 MHz) | 2.9-3.1 |
Dissipation Factor (at 1 MHz) | 0.002-0.004 |
Tensile Strength | 150-200 MPa |
Elongation at Break | 1-3% |
Moisture Absorption | 0.02-0.10% |
LCP PCBs offer several advantages, including:
- Excellent electrical properties
- Low dielectric constant and dissipation factor
- Extremely low moisture absorption
- High dimensional stability
- Good thermal and chemical resistance
Applications of LCP PCBs
LCP PCBs are widely used in high-frequency and high-speed applications, such as:
- 5G telecommunications
- Automotive radar systems
- Aerospace and defense
- High-speed digital applications
- Medical devices
Polycarbonate (PC) PCBs
What is Polycarbonate?
Polycarbonate (PC) is a thermoplastic polymer known for its high impact resistance, transparency, and good electrical insulation properties. It is commonly used in the production of PCBs for applications that require durability and resistance to mechanical stress.
Properties of PC PCBs
Property | Value |
---|---|
Glass Transition Temperature (Tg) | 145-150°C |
Dielectric Constant (at 1 MHz) | 2.8-3.0 |
Dissipation Factor (at 1 MHz) | 0.005-0.010 |
Tensile Strength | 60-70 MPa |
Elongation at Break | 100-150% |
Moisture Absorption | 0.1-0.3% |
PC PCBs offer several advantages, including:
- High impact resistance
- Good electrical insulation properties
- Transparency (for optical applications)
- Good heat resistance
- Excellent dimensional stability
Applications of PC PCBs
PC PCBs are used in various applications that require durability and resistance to mechanical stress, such as:
- Automotive electronics
- Industrial control systems
- Medical devices
- Aerospace and defense
- Consumer electronics
Frequently Asked Questions (FAQ)
-
Q: What are the main advantages of using plastic PCBs over traditional PCB materials?
A: Plastic PCBs offer several advantages, including excellent electrical properties, low moisture absorption, high dimensional stability, and good thermal and chemical resistance. They are also lightweight and flexible, making them suitable for a wide range of applications. -
Q: Which plastic PCB material is best for high-frequency applications?
A: Liquid Crystal Polymer (LCP) PCBs are the best choice for high-frequency applications due to their low dielectric constant and dissipation factor, excellent electrical properties, and extremely low moisture absorption. -
Q: Are plastic PCBs suitable for high-temperature applications?
A: Some plastic PCB materials, such as Polyimide (PI) and Polyethylene Naphthalate (PEN), have high glass transition temperatures and can withstand elevated temperatures. However, for extreme high-temperature applications, other materials like ceramic or metal-based PCBs may be more suitable. -
Q: How do the costs of plastic PCBs compare to traditional PCB materials?
A: The cost of plastic PCBs varies depending on the specific material used. Some materials, like PET, are relatively low-cost compared to other plastic PCB materials. However, high-performance plastics like PI and LCP may be more expensive than traditional PCB materials like FR-4. -
Q: Can plastic PCBs be used in flexible electronics applications?
A: Yes, many plastic PCB materials, such as Polyimide (PI) and Polyethylene Terephthalate (PET), are suitable for flexible electronics applications due to their good mechanical strength and flexibility.
Conclusion
Plastic PCBs have gained significant popularity in recent years due to their unique properties and advantages over traditional PCB materials. The various types of plastics used in PCB manufacturing, such as Polyimide, PET, PEN, LCP, and Polycarbonate, each offer distinct characteristics that make them suitable for specific applications.
When selecting a plastic PCB material, it is essential to consider factors such as the intended application, required electrical properties, thermal stability, and mechanical requirements. By understanding the properties and advantages of each plastic material, designers and engineers can make informed decisions to ensure the best performance and reliability of their electronic devices.
As technology continues to advance, the demand for high-performance, lightweight, and flexible PCBs will likely increase. Plastic PCBs are well-positioned to meet these challenges and will play a crucial role in shaping the future of the electronics industry.
No responses yet