The Importance of PCB Prototyping
PCB prototyping is essential for several reasons:
-
Design Validation: Prototyping allows designers to test and validate their PCB designs before committing to mass production. This helps identify any design flaws or issues early in the development process, saving time and money.
-
Functionality Testing: Prototypes enable engineers to test the functionality of the PCB and ensure that it meets the required specifications. This includes testing the board’s electrical characteristics, signal integrity, and overall performance.
-
Manufacturability Assessment: Prototyping helps assess the manufacturability of the PCB design. It allows manufacturers to identify any potential challenges or limitations in the production process and make necessary adjustments.
-
Cost Optimization: By identifying and resolving issues during the prototyping stage, companies can optimize their PCB designs for cost-effectiveness. This includes selecting the right materials, components, and manufacturing processes.
PCB Prototyping Design Flow
The PCB prototyping design flow typically consists of the following stages:
1. Schematic Design
The first stage of PCB prototyping is schematic design. This involves creating a graphical representation of the electronic circuit using specialized software tools. The schematic diagram shows the interconnections between various components, such as resistors, capacitors, integrated circuits (ICs), and connectors.
During this stage, engineers define the functionality of the circuit and select the appropriate components based on their specifications. They also consider factors such as power requirements, signal integrity, and electromagnetic compatibility (EMC).
2. PCB Layout Design
Once the schematic design is complete, the next stage is PCB layout design. This involves translating the schematic into a physical layout of the PCB. The layout design determines the placement of components, routing of traces, and the overall dimensions of the board.
PCB layout designers use specialized CAD (Computer-Aided Design) tools to create the layout. They consider various factors, such as component footprints, trace widths, spacing, and design rules. The goal is to achieve an optimal layout that minimizes signal interference, ensures proper heat dissipation, and meets the required manufacturing tolerances.
3. Design Rule Check (DRC)
After completing the PCB layout design, engineers perform a Design Rule Check (DRC). DRC is an automated process that verifies the layout against a set of predefined design rules. These rules ensure that the PCB design meets the manufacturing guidelines and standards.
DRC checks for various aspects, such as minimum trace widths, spacing between components, drill sizes, and copper pour clearances. Any violations or errors identified during the DRC process must be addressed and corrected before proceeding to the next stage.
4. Gerber File Generation
Once the PCB layout design passes the DRC, the next step is to generate Gerber files. Gerber files are industry-standard file formats used to describe the PCB layout for manufacturing. They contain information about the copper layers, solder mask, silkscreen, and drill holes.
Gerber files are generated using the CAD software and include separate files for each layer of the PCB. These files are then sent to the PCB manufacturer for fabrication.
5. Prototype Fabrication
The PCB manufacturer receives the Gerber files and begins the fabrication process. This involves several steps, including:
-
Copper Etching: The PCB substrate is coated with a layer of copper, and the unwanted copper is etched away based on the Gerber files. This creates the desired circuit pattern on the board.
-
Drilling: Holes are drilled into the PCB substrate to accommodate through-hole components and vias (vertical interconnect access).
-
Solder Mask Application: A solder mask layer is applied to the PCB to protect the copper traces and prevent short circuits. The solder mask also provides insulation and improves the aesthetics of the board.
-
Silkscreen Printing: The silkscreen layer is printed on the PCB to add component labels, logos, and other identifying information.
-
Surface Finish: A surface finish, such as HASL (Hot Air Solder Leveling), ENIG (Electroless Nickel Immersion Gold), or OSP (Organic Solderability Preservative), is applied to the exposed copper areas to protect them from oxidation and enhance solderability.
6. Assembly and Testing
After the PCB Prototype is fabricated, the next stage is assembly and testing. This involves soldering the components onto the PCB according to the schematic design. The assembly process can be done manually for low-volume prototypes or using automated pick-and-place machines for higher volumes.
Once the components are assembled, the prototype undergoes various tests to verify its functionality and performance. These tests may include:
- Continuity Test: Verifies that there are no open circuits or short circuits on the board.
- Functional Test: Checks if the prototype performs the intended functions and meets the design specifications.
- In-Circuit Test (ICT): Verifies the correct placement and value of individual components on the board.
- Boundary Scan Test: Tests the interconnections between ICs and other components using JTAG (Joint Test Action Group) interface.
- Environmental Testing: Subjects the prototype to various environmental conditions, such as temperature, humidity, and vibration, to assess its reliability and durability.
7. Design Iteration and Refinement
Based on the results of the testing phase, engineers may need to iterate and refine the PCB design. This may involve making modifications to the schematic, layout, or component selection to address any issues or improve performance.
The prototyping process may go through multiple iterations until the desired functionality and quality are achieved. Each iteration helps optimize the design and ensures that the final product meets the required specifications.
PCB Prototyping Techniques
There are several techniques used for PCB prototyping, depending on the complexity of the design and the required turnaround time. Some common techniques include:
-
Breadboarding: Breadboarding is a quick and easy way to prototype simple circuits. It involves using a breadboard, which is a reusable plastic board with holes for inserting components and jumper wires. Breadboarding allows designers to quickly test and modify their circuits without the need for soldering.
-
Perfboard Prototyping: Perfboard prototyping involves using a pre-drilled circuit board with a grid of holes. Components are inserted into the holes and soldered together to create the desired circuit. This technique is suitable for simple to moderate complexity designs.
-
Printed Circuit Board (PCB) Prototyping: PCB prototyping involves fabricating a custom-designed PCB based on the schematic and layout files. This technique offers the highest level of design flexibility and is suitable for complex designs with high component density and specific layout requirements.
-
3D Printing: 3D printing technology can be used to create PCB prototypes rapidly. Conductive filaments or inks are used to print the circuit traces directly onto a substrate material. While 3D-printed PCBs may not have the same level of precision and reliability as traditional PCBs, they offer a quick and cost-effective solution for early-stage prototyping.
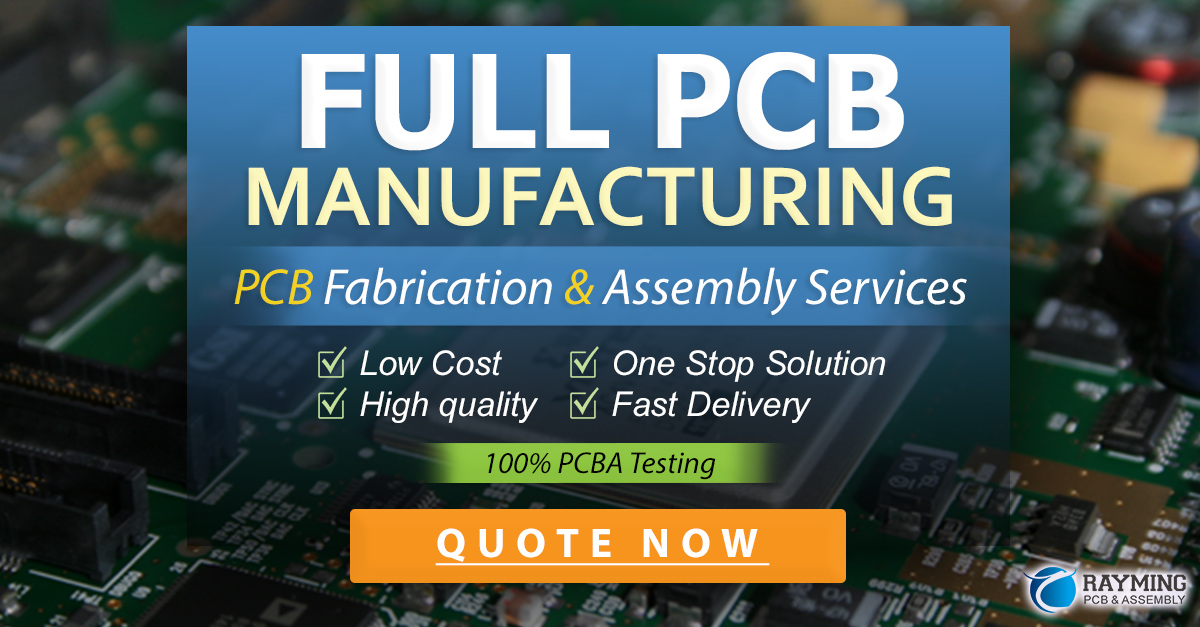
Frequently Asked Questions (FAQ)
-
What is the typical turnaround time for PCB prototyping?
The turnaround time for PCB prototyping varies depending on the complexity of the design and the chosen fabrication technique. Simple designs using perfboard prototyping can be completed in a few hours, while custom PCB fabrication may take several days to a few weeks, depending on the manufacturer’s lead time and the required specifications. -
How much does PCB prototyping cost?
The cost of PCB prototyping depends on factors such as the complexity of the design, the number of layers, the size of the board, and the quantity of prototypes required. Simple designs using perfboard prototyping can cost a few dollars, while custom PCB fabrication may range from a few hundred to several thousand dollars, depending on the specifications and quantity. -
What software tools are used for PCB prototyping?
There are various software tools available for PCB prototyping, including schematic capture and PCB layout design tools. Some popular software options include: - Altium Designer
- Autodesk Eagle
- KiCad
- OrCAD
-
Proteus
-
Can I prototype Multilayer PCBs?
Yes, multilayer PCBs can be prototyped using custom PCB fabrication techniques. Multilayer PCBs consist of multiple layers of conductive traces separated by insulating layers. They offer higher component density and improved signal integrity compared to Single-layer PCBs. However, the complexity and cost of multilayer PCB prototyping are higher compared to single-layer designs. -
What are the benefits of outsourcing PCB prototyping?
Outsourcing PCB prototyping to specialized manufacturers offers several benefits: - Access to advanced manufacturing capabilities and equipment
- Faster turnaround times and higher production capacity
- Expertise in PCB fabrication and assembly processes
- Cost-effectiveness for high-volume production
- Quality assurance and adherence to industry standards
Prototyping Technique | Complexity | Turnaround Time | Cost |
---|---|---|---|
Breadboarding | Low | Hours | Low |
Perfboard Prototyping | Low to Medium | Days | Low to Medium |
Custom PCB Fabrication | High | Days to Weeks | Medium to High |
3D Printing | Low to Medium | Hours to Days | Low to Medium |
Conclusion
PCB prototyping is a critical step in the development of electronic devices. It allows designers to validate their designs, test functionality, assess manufacturability, and optimize cost-effectiveness. The PCB prototyping design flow involves several stages, including schematic design, layout design, design rule check, Gerber file generation, prototype fabrication, assembly, testing, and design iteration.
Various prototyping techniques, such as breadboarding, perfboard prototyping, custom PCB fabrication, and 3D printing, cater to different design complexities and requirements. Choosing the right prototyping technique and leveraging specialized software tools and manufacturing expertise can streamline the prototyping process and ensure the successful development of PCB-based electronic products.
By understanding the PCB prototyping design flow and stages, engineers and designers can effectively navigate the prototyping process, identify and resolve issues early, and bring their innovative ideas to life in a timely and cost-effective manner.
No responses yet