Introduction to PCB base Materials
Printed Circuit Boards (PCBs) are essential components in modern electronic devices, serving as the foundation for mounting and interconnecting electronic components. The base material of a PCB plays a crucial role in its performance, durability, and reliability. In this article, we will explore the various materials used as the base for PCBs, their properties, and their applications.
Common PCB Base Materials
The most commonly used PCB base materials include:
- FR-4 (Flame Retardant 4)
- Polyimide
- Ceramic
- Aluminum
- Flexible substrates (e.g., Polyester, Polyimide)
Each of these materials has its unique properties and advantages, making them suitable for different applications and environments.
FR-4: The Most Popular PCB Base Material
FR-4 (Flame Retardant 4) is the most widely used PCB base material, accounting for a significant portion of the PCB market. It is a composite material made of woven fiberglass cloth impregnated with an epoxy resin binder.
Advantages of FR-4
- Excellent electrical insulation properties
- Good mechanical strength and durability
- High resistance to moisture and chemicals
- Flame retardant properties
- Cost-effective solution for most applications
Applications of FR-4 PCBs
FR-4 PCBs are used in a wide range of electronic devices, including:
- Consumer electronics (e.g., smartphones, tablets, laptops)
- Industrial control systems
- Telecommunications equipment
- Automotive electronics
- Medical devices
FR-4 Variants and Their Properties
FR-4 Variant | Description | Tg (°C) | Td (°C) | Dielectric Constant (1 MHz) |
---|---|---|---|---|
Standard | General-purpose FR-4 | 130-140 | 300-320 | 4.2-4.9 |
High Tg | Improved thermal stability and mechanical strength | 170-180 | 340-360 | 4.2-4.9 |
Halogen-free | Environmentally friendly, low-toxicity | 130-140 | 300-320 | 4.2-4.9 |
Tg: Glass transition temperature, Td: Decomposition temperature
Polyimide: High-Temperature PCB Base Material
Polyimide is a high-performance polymer known for its excellent thermal stability, making it an ideal choice for PCBs operating in high-temperature environments.
Advantages of Polyimide
- High thermal stability (up to 260°C)
- Excellent chemical resistance
- Low dielectric constant and dissipation factor
- Good mechanical strength and flexibility
Applications of Polyimide PCBs
Polyimide PCBs are commonly used in:
- Aerospace and defense systems
- High-temperature industrial applications
- Automotive electronics (e.g., under-the-hood components)
- Medical devices (e.g., implantable devices)
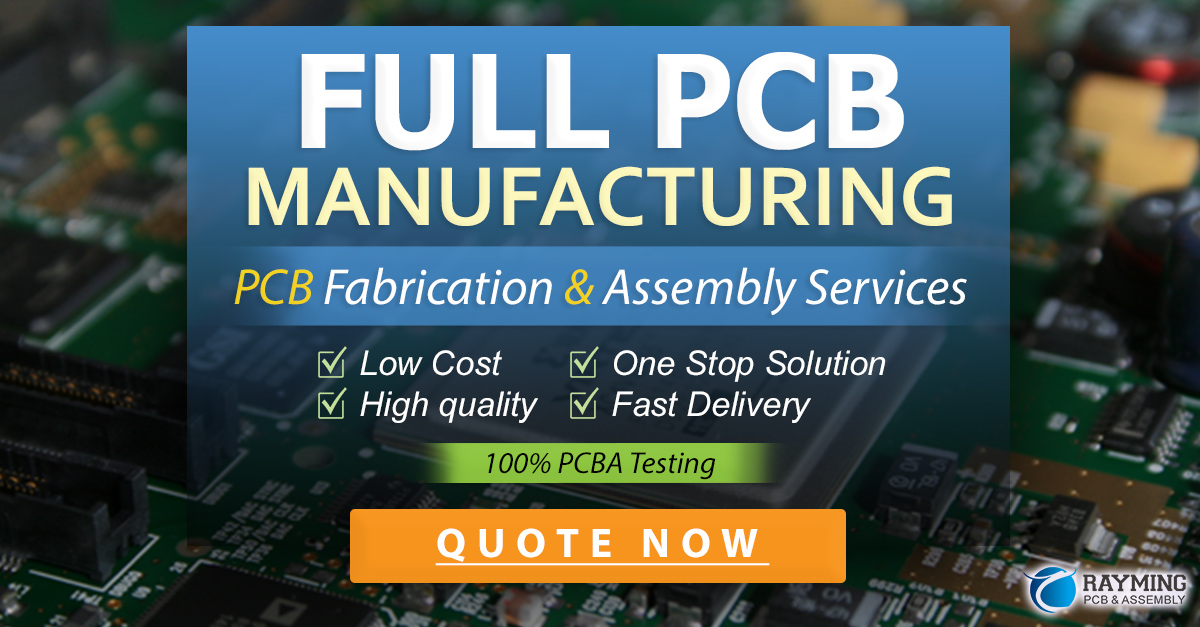
Ceramic: Robust PCB Base Material for Harsh Environments
Ceramic PCBs are made using alumina (Al2O3) or aluminum nitride (AlN) as the base material. They offer exceptional thermal and mechanical properties, making them suitable for demanding applications.
Advantages of Ceramic PCBs
- Excellent thermal conductivity
- High mechanical strength and stiffness
- Low dielectric constant and loss tangent
- Resistance to high temperatures and corrosive environments
Applications of Ceramic PCBs
Ceramic PCBs are used in:
- High-power RF and microwave devices
- LED lighting systems
- Automotive and aerospace electronics
- Medical equipment (e.g., X-ray machines, MRI scanners)
Aluminum: PCB Base Material for Effective Heat Dissipation
Aluminum PCBs consist of an aluminum substrate with a thin layer of dielectric material and copper traces on top. They are designed to efficiently dissipate heat generated by electronic components.
Advantages of Aluminum PCBs
- Excellent thermal conductivity
- Lightweight and durable
- Good mechanical stability
- Cost-effective solution for heat management
Applications of Aluminum PCBs
Aluminum PCBs are commonly found in:
- Power electronics (e.g., motor drives, power supplies)
- LED lighting systems
- Automotive electronics (e.g., headlights, engine control units)
- High-power RF and microwave devices
Flexible PCB Base Materials
Flexible PCBs are made using thin, flexible substrates that allow the PCB to bend and conform to various shapes. The most common flexible PCB base materials are polyester (PET) and polyimide (PI).
Advantages of Flexible PCBs
- Lightweight and thin
- Ability to conform to limited spaces and curved surfaces
- Reduced assembly costs due to fewer interconnections
- Improved mechanical durability and shock resistance
Applications of Flexible PCBs
Flexible PCBs are used in:
- Wearable electronics
- Medical devices (e.g., hearing aids, pacemakers)
- Automotive electronics (e.g., sensor interconnects)
- Consumer electronics (e.g., smartphone displays, camera modules)
Frequently Asked Questions (FAQ)
-
Q: What is the most commonly used PCB base material?
A: FR-4 (Flame Retardant 4) is the most widely used PCB base material, accounting for a significant portion of the PCB market. -
Q: Which PCB base material is best suited for high-temperature applications?
A: Polyimide is an ideal choice for PCBs operating in high-temperature environments due to its excellent thermal stability (up to 260°C). -
Q: Are ceramic PCBs more expensive than FR-4 PCBs?
A: Yes, ceramic PCBs are generally more expensive than FR-4 PCBs due to the higher cost of the base material and the specialized manufacturing processes required. -
Q: What are the advantages of using aluminum as a PCB base material?
A: Aluminum PCBs offer excellent thermal conductivity, making them effective at dissipating heat generated by electronic components. They are also lightweight, durable, and cost-effective. -
Q: Can flexible PCBs be used in medical devices?
A: Yes, flexible PCBs are commonly used in medical devices such as hearing aids, pacemakers, and other implantable devices due to their ability to conform to limited spaces and curved surfaces.
Conclusion
The choice of PCB base material depends on various factors, including the intended application, operating environment, performance requirements, and cost considerations. FR-4 remains the most popular choice for general-purpose PCBs, while polyimide, ceramic, aluminum, and flexible substrates cater to more specialized applications. By understanding the properties and advantages of each material, engineers and designers can select the most appropriate PCB base material to ensure optimal performance and reliability in their electronic devices.
No responses yet