Introduction to PCB and CCA
In the world of electronics, two common terms that often come up are PCB (Printed Circuit Board) and CCA (Circuit Card Assembly). While they may sound similar, there are some key differences between the two. In this article, we’ll dive deep into the world of PCBs and CCAs, exploring their definitions, manufacturing processes, applications, and more.
What is a PCB?
Definition and Basics
A Printed Circuit Board, or PCB, is a flat board made of insulating material, such as fiberglass or composite epoxy, with conductive copper traces printed onto its surface. These traces form the electrical connections between various components mounted on the board, such as resistors, capacitors, integrated circuits (ICs), and connectors.
PCBs serve as the foundation for most modern electronic devices, providing a means to mechanically support and electrically connect electronic components using conductive pathways, tracks, or signal traces etched from copper sheets laminated onto a non-conductive substrate.
Types of PCBs
There are several types of PCBs, each with its own unique characteristics and applications:
-
Single-sided PCBs: These boards have conductive traces on only one side of the insulating substrate. They are the simplest and most cost-effective type of PCB, often used in basic electronic devices.
-
Double-sided PCBs: These boards have conductive traces on both sides of the insulating substrate, allowing for more complex circuits and higher component density. The two sides are connected using through-hole technology or vias.
-
Multi-layer PCBs: These boards consist of multiple layers of insulating material and conductive traces, alternating between them. They offer the highest component density and are used in complex electronic devices, such as smartphones, computers, and medical equipment.
-
Flexible PCBs: These boards are made of flexible insulating material, allowing them to bend and conform to various shapes. They are often used in wearable electronics, medical devices, and aerospace applications.
-
Rigid-Flex PCBs: These boards combine the benefits of both rigid and flexible PCBs, featuring rigid sections for mounting components and flexible sections for connecting them. They are used in applications requiring both stability and flexibility, such as automotive electronics and industrial automation.
PCB Manufacturing Process
The PCB manufacturing process involves several steps, each critical to ensuring the quality and functionality of the final product:
-
Design: The PCB design is created using specialized software, such as Altium Designer or Eagle. The design includes the component layout, electrical connections, and any necessary mechanical features.
-
Printing: The design is printed onto a transparent film or photomask, which will be used to transfer the pattern onto the copper-clad board.
-
Etching: The copper-clad board is coated with a photoresist layer and exposed to UV light through the photomask. The exposed areas of the photoresist are then removed, leaving the desired copper traces. The board is then submerged in an etchant solution, which removes the unwanted copper, leaving only the desired traces.
-
Drilling: Holes are drilled into the board to accommodate through-hole components and vias.
-
Plating: The board is plated with a thin layer of copper to improve conductivity and protect the traces from oxidation.
-
Solder Mask Application: A layer of solder mask is applied to the board to protect the copper traces and prevent short circuits.
-
Silkscreen Printing: Text and symbols are printed onto the board using silkscreen printing to aid in component placement and identification.
-
Surface Finishing: The exposed copper areas are coated with a protective layer, such as gold, silver, or tin, to prevent oxidation and improve solderability.
-
Testing: The completed PCB is tested for functionality and quality control.
What is a CCA?
Definition and Basics
A Circuit Card Assembly, or CCA, is a type of PCB that has been populated with electronic components and is ready for use in an electronic device. In other words, a CCA is a fully assembled and functional PCB.
The term “CCA” is often used interchangeably with “PCBA” (Printed Circuit Board Assembly), although some may argue that a CCA specifically refers to a populated PCB used in a larger system, while a PCBA can be a standalone device.
CCA Assembly Process
The CCA assembly process involves several steps, building upon the PCB manufacturing process:
-
Solder Paste Application: Solder paste, a mixture of tiny solder particles and flux, is applied to the PCB’s contact pads using a stencil or syringe.
-
Component Placement: The electronic components are placed onto the PCB, either manually or using automated pick-and-place machinery. Surface mount components are placed directly onto the solder paste, while through-hole components are inserted into the drilled holes.
-
Reflow Soldering: The populated PCB is passed through a reflow oven, which heats the board to a specific temperature profile, melting the solder paste and creating a strong electrical and mechanical bond between the components and the PCB.
-
Inspection: The assembled CCA is visually inspected for any defects, such as misaligned components, solder bridges, or insufficient solder joints. Automated optical inspection (AOI) systems may be used for more precise and consistent inspections.
-
Testing: The CCA undergoes various tests to ensure proper functionality, including in-circuit testing (ICT), functional testing, and boundary scan testing.
-
Conformal Coating (Optional): In some cases, a conformal coating, such as acrylic, silicone, or urethane, is applied to the CCA to protect it from environmental factors, such as moisture, dust, and chemicals.
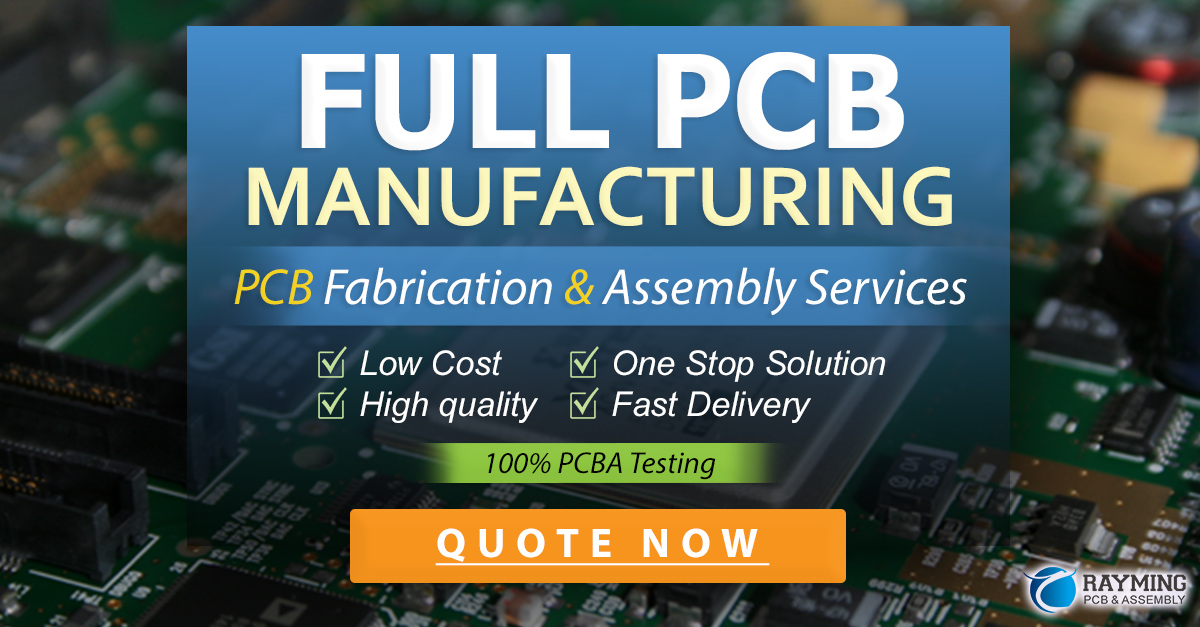
Differences Between PCBs and CCAs
While PCBs and CCAs are closely related, there are some key differences between the two:
Feature | PCB | CCA |
---|---|---|
Definition | A bare board with conductive traces | A fully assembled and functional PCB |
Components | No components mounted | Electronic components mounted and soldered |
Manufacturing | Involves etching, drilling, and plating | Involves component placement and soldering |
Functionality | Not functional on its own | Fully functional and ready for use |
Testing | Limited testing for continuity and shorts | Extensive testing for functionality and quality |
Application | Used as a base for electronic devices | Used as a complete assembly in electronic devices |
Cost | Lower cost due to simpler manufacturing | Higher cost due to additional assembly steps |
Lead Time | Shorter lead times for bare board production | Longer lead times due to assembly process |
Applications of PCBs and CCAs
PCBs and CCAs are used in a wide range of electronic devices and industries, including:
-
Consumer Electronics: Smartphones, laptops, tablets, televisions, gaming consoles, and wearable devices.
-
Automotive: Engine control units, infotainment systems, sensors, and power management systems.
-
Industrial Automation: Programmable logic controllers (PLCs), human-machine interfaces (HMIs), and industrial robots.
-
Medical Devices: Diagnostic equipment, monitoring systems, and implantable devices.
-
Aerospace and Defense: Avionics, communication systems, and missile guidance systems.
-
IoT and Embedded Systems: Smart home devices, wireless sensors, and low-power embedded controllers.
Frequently Asked Questions (FAQ)
-
Q: Can a PCB function without components?
A: No, a PCB is just the bare board with conductive traces. It needs electronic components to be mounted and soldered onto it to function as intended. -
Q: Are all CCAs also PCBs?
A: Yes, a CCA is a type of PCB that has been populated with components. All CCAs start as bare PCBs before the assembly process. -
Q: What is the difference between surface mount and through-hole components?
A: Surface mount components are placed directly onto the solder paste on the PCB, while through-hole components have leads that are inserted into drilled holes in the board. Surface mount technology allows for smaller components and higher density, while through-hole components offer stronger mechanical connections. -
Q: What is the purpose of solder mask on a PCB?
A: Solder mask is a protective layer applied to the PCB that covers the copper traces, leaving only the contact pads exposed. It helps prevent short circuits, protects the traces from oxidation, and provides electrical insulation. -
Q: How are PCBs and CCAs tested for quality and functionality?
A: PCBs undergo limited testing, such as continuity and shorts testing, to ensure the integrity of the conductive traces. CCAs, on the other hand, go through more extensive testing, including in-circuit testing, functional testing, and boundary scan testing, to ensure proper functionality and catch any defects or issues.
Conclusion
In summary, PCBs and CCAs are essential components in the world of electronics, each serving a specific purpose in the design and manufacturing process. PCBs provide the foundation for electronic devices, offering a means to mechanically support and electrically connect components, while CCAs are fully assembled and functional boards ready for use in an electronic device.
Understanding the differences between PCBs and CCAs, as well as their manufacturing processes, applications, and testing methods, is crucial for anyone involved in the electronics industry, from designers and engineers to manufacturers and quality control specialists.
As technology continues to advance, the demand for high-quality, reliable, and compact PCBs and CCAs will only continue to grow, driving innovation and shaping the future of electronic devices across various industries.
No responses yet