What is BGA?
BGA is a surface-mount packaging used for integrated circuits. The bottom of the BGA package has an array of solder balls that are used to conduct electrical signals from the integrated circuit to the Printed circuit board (PCB). BGA packages can have anywhere from a few dozen to over a thousand solder balls, with pitches ranging from 1.27mm down to 0.3mm or less.
Advantages of BGA Packages
BGA packages offer several advantages over other surface mount packages, such as quad flat packs (QFPs) and thin small outline packages (TSOPs):
- Higher pin counts: BGAs can have hundreds or even thousands of pins, allowing for more complex designs.
- Smaller footprint: For a given number of pins, BGAs have a smaller footprint than other packages, allowing for denser PCB layouts.
- Better thermal performance: The large number of solder balls in a BGA provides a low-resistance thermal path away from the integrated circuit.
- Better electrical performance: The short leads and low inductance of BGA packages provide superior electrical performance, especially at high frequencies.
Challenges of BGA Assembly
While BGA packages offer many advantages, they also present challenges for assembly:
- Placement accuracy: The small size and tight pitch of BGA packages require high-precision placement equipment.
- Reflow Soldering: Achieving proper solder joint formation requires careful control of the reflow profile.
- Inspection: Inspecting BGA solder joints requires the use of X-ray equipment.
- Rework: Reworking BGA packages is difficult and requires specialized equipment and training.
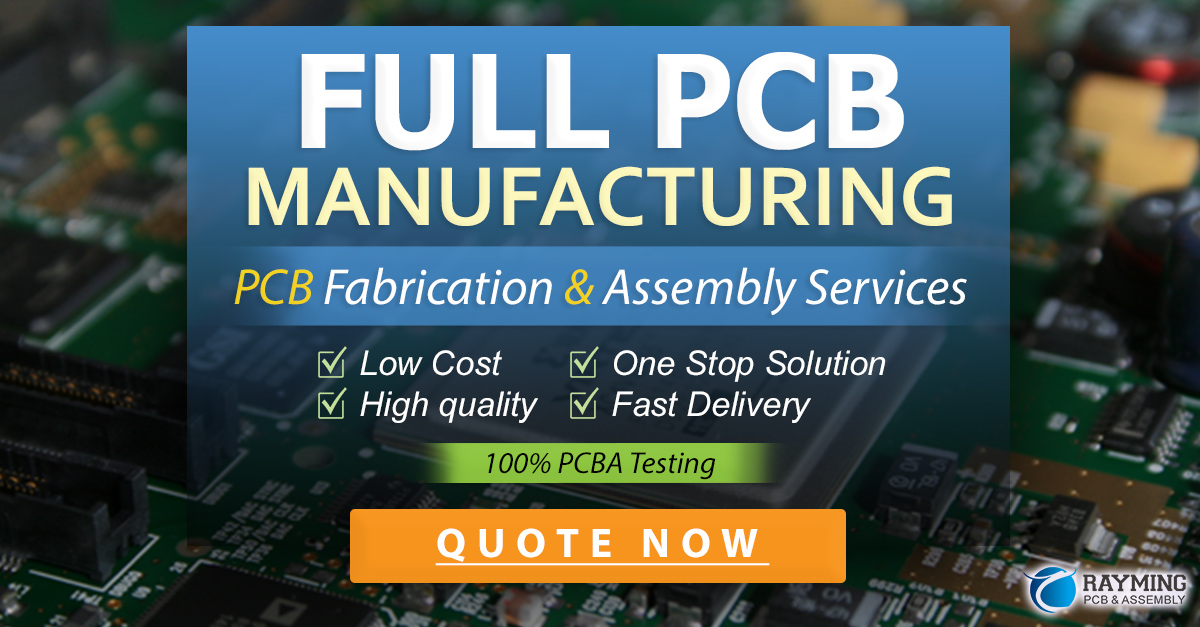
BGA Assembly Process
The BGA assembly process typically involves the following steps:
-
Solder Paste Printing: Solder paste is applied to the PCB using a stencil printer. The stencil has apertures that match the solder ball locations on the BGA package.
-
BGA placement: The BGA package is placed onto the PCB using a high-precision Pick-and-Place machine. Placement accuracy is critical to ensure proper solder joint formation.
-
Reflow soldering: The PCB is run through a reflow oven, which melts the solder paste and forms the solder joints between the BGA package and the PCB. The reflow profile must be carefully controlled to achieve proper solder joint formation without damaging the components.
-
Inspection: After reflow, the solder joints are inspected using X-ray equipment to ensure proper formation and check for defects such as shorts, opens, and voids.
-
Rework (if necessary): If defects are found during inspection, the BGA package may need to be reworked. This involves removing the package, cleaning the site, and reassembling the package.
Equipment Required for BGA Assembly
To properly assemble BGA packages, several pieces of specialized equipment are required:
-
Stencil printer: Used to apply solder paste to the PCB. Must have high precision and repeatability.
-
Pick-and-place machine: Used to place the BGA package onto the PCB. Must have high placement accuracy, typically +/-0.025mm or better.
-
Reflow oven: Used to melt the solder paste and form the solder joints. Must have good temperature uniformity and be able to follow a precise reflow profile.
-
X-ray Inspection system: Used to inspect the solder joints after reflow. Allows for inspection of hidden joints that cannot be seen optically.
-
Rework station: Used to remove and replace defective BGA packages. Typically includes a hot air pencil, vacuum pick-up tool, and specialized nozzles for different package sizes.
Solder Paste Selection
Selecting the right solder paste is critical for successful BGA assembly. The solder paste must have the right particle size, flux activity, and rheology for the specific application. Some factors to consider when selecting a solder paste include:
- Powder particle size: Smaller particle sizes are better for fine-pitch BGAs, but may be more difficult to print.
- Flux activity: Higher flux activity is better for wetting and reducing voiding, but may be more difficult to clean after reflow.
- Rheology: The paste must have good printability and release from the stencil apertures, while also maintaining its shape after printing.
Example solder pastes for BGA assembly:
Paste | Powder Size | Flux Type | Rheology |
---|---|---|---|
Alpha OM-338 | Type 4 (20-38µm) | No-clean, halide-free | Excellent printability and release |
Indium 8.9HF | Type 4 (20-38µm) | No-clean, halogen-free | Good wetting and low voiding |
Kester NP505-HR | Type 4.5 (15-25µm) | No-clean, halogen-free | Fine-pitch printing capability |
Reflow Profile Optimization
Achieving a good reflow profile is essential for proper solder joint formation and reducing defects. The reflow profile should be optimized for the specific solder paste and BGA package being used. Some key factors to consider when optimizing the reflow profile include:
- Peak temperature: The peak temperature must be high enough to fully melt the solder and allow for good wetting, but not so high as to damage the components.
- Time above liquidus (TAL): The TAL should be long enough to allow for complete solder melting and wetting, but not so long as to cause intermetallic growth or damage to the components.
- Ramp rate: The ramp rate should be fast enough to minimize the time spent in the critical temperature range where intermetallic growth occurs, but not so fast as to cause thermal shock to the components.
Example reflow profile for a lead-free solder paste:
Zone | Temperature | Time |
---|---|---|
Preheat | 150-180°C | 60-120 sec |
Soak | 180-200°C | 60-120 sec |
Reflow | 235-250°C | 30-60 sec |
Peak | 245-260°C | 10-30 sec |
Cooling | <6°C/sec | – |
X-Ray Inspection
X-ray inspection is essential for verifying the quality of BGA solder joints, as the joints are hidden under the package and cannot be inspected optically. X-ray systems used for BGA inspection typically use either 2D or 3D imaging techniques.
2D X-ray systems provide a top-down view of the solder joints, allowing for inspection of solder bridges, voids, and other defects. However, 2D systems cannot measure the height or volume of the solder joints, which can be important for assessing joint quality.
3D X-ray systems use computed tomography (CT) techniques to create a 3D image of the solder joints. This allows for measurement of joint height and volume, as well as detection of more subtle defects such as cracks and head-in-pillow (HIP) defects.
Example X-ray images of BGA solder joints:
Image Type | Description |
---|---|
2D X-ray image showing a void in a BGA solder joint | |
3D X-ray image showing head-in-pillow defects in BGA solder joints |
BGA Rework
Even with the best assembly processes, defects can still occur that require rework of the BGA package. BGA rework typically involves the following steps:
- Removal of the defective package using a hot air pencil or rework station.
- Cleaning of the PCB pads to remove any residual solder or flux.
- Placement of a new package using a pick-and-place machine or manual placement tool.
- Reflow soldering of the new package using a localized heating method such as hot air or infrared.
- Inspection of the new solder joints using X-ray.
Successful BGA rework requires skilled operators and specialized equipment. Improper rework techniques can damage the PCB or components, leading to further reliability issues.
Conclusion
BGA assembly presents many challenges, but with the right equipment, processes, and expertise, it is possible to achieve high-quality, reliable solder joints. Careful selection of solder paste, optimization of the reflow profile, and thorough inspection using X-ray are all critical for success. When defects do occur, proper rework techniques can salvage the board and prevent further damage.
As BGAs continue to shrink in size and increase in complexity, the importance of having strong BGA assembly capabilities will only continue to grow. By investing in the right equipment and training, electronics manufacturers can position themselves for success in this demanding field.
FAQ
- What is the smallest BGA pitch that can be assembled?
-
With the right equipment and processes, BGA pitches down to 0.3mm or even smaller can be successfully assembled. However, as the pitch gets smaller, the challenges of printing, placement, and inspection increase.
-
What is the most common defect in BGA assembly?
-
One of the most common defects in BGA assembly is voiding, where there are gaps or air pockets in the solder joint. Voiding can be caused by a variety of factors, including poor paste deposition, insufficient flux activity, or improper reflow profile.
-
Can BGAs be reworked multiple times?
-
While it is possible to rework BGAs multiple times, each rework cycle introduces additional stress on the PCB and components, increasing the risk of damage. It is generally best to minimize the number of rework cycles whenever possible.
-
What is the difference between a collapsible and non-collapsible BGA?
-
Collapsible BGAs have solder balls that are designed to collapse and flatten out during reflow, while non-collapsible BGAs have solder balls that maintain their shape. Collapsible BGAs are more forgiving of placement and reflow variations, but non-collapsible BGAs may be preferred for applications where solder joint height is critical.
-
How can head-in-pillow defects be prevented?
- Head-in-pillow (HIP) defects occur when the solder ball on the BGA does not fully collapse and wet to the PCB pad, resulting in an open or high-resistance connection. HIP defects can be prevented by ensuring proper paste deposition, using a sufficiently active flux, and optimizing the reflow profile to achieve complete solder melting and wetting.
No responses yet