What is PCB soldering?
PCB soldering is the process of attaching electronic components to a printed Circuit Board using a molten metal alloy called solder. The solder creates an electrical and mechanical connection between the component leads and the copper pads on the PCB. This connection allows electrical current to flow through the circuit, enabling the device to function as intended.
Tools and Materials Needed for PCB Soldering
Before you begin soldering your PCB, it’s important to gather all the necessary tools and materials. Here’s a list of what you’ll need:
- Soldering iron with adjustable temperature control
- Soldering iron tip (chisel or conical shape, appropriately sized for your components)
- Solder wire (lead-free, rosin-core, 0.5-0.8mm diameter)
- Soldering iron stand
- Brass or stainless steel sponge for cleaning the soldering iron tip
- Solder wick or desoldering pump for removing excess solder
- Flux pen or flux paste (optional, but recommended for better solder flow)
- Tweezers for handling small components
- Wire cutters for trimming component leads
- Magnifying glass or microscope for inspecting solder joints
- Isopropyl alcohol and cotton swabs for cleaning the PCB
- ESD (electrostatic discharge) protection, such as an ESD mat or wrist strap
Preparing Your Workspace for PCB Soldering
Creating a clean, organized, and safe workspace is crucial for successful PCB soldering. Follow these steps to prepare your workspace:
- Choose a well-ventilated area with good lighting and a stable, heat-resistant work surface.
- Ensure your work area is free from clutter and has enough space for your tools, materials, and PCB.
- Set up your soldering iron stand and make sure your soldering iron is clean and in good condition.
- If using ESD-sensitive components, set up your ESD protection, such as an ESD mat or wrist strap.
- Organize your components and tools for easy access during the soldering process.
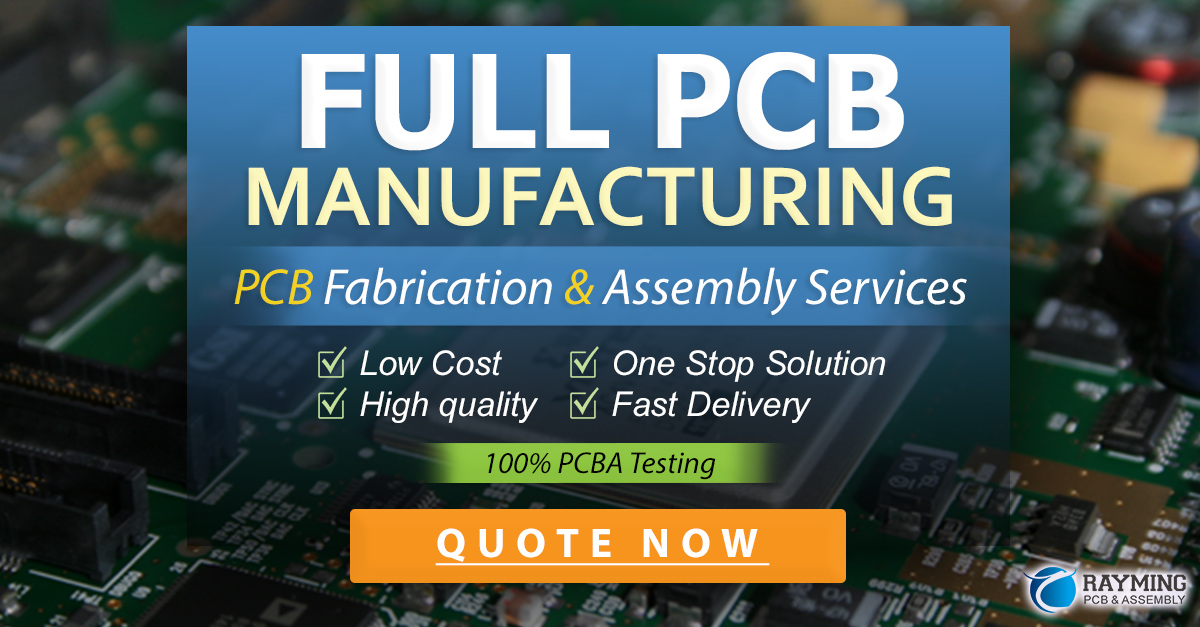
PCB Soldering Techniques
Through-Hole Soldering
Through-hole soldering involves attaching components with leads that pass through holes in the PCB. Here’s how to solder through-hole components:
- Insert the component leads through the designated holes in the PCB.
- Bend the leads slightly outward on the opposite side of the PCB to hold the component in place.
- Heat your soldering iron to the appropriate temperature (typically 300-400°C or 572-752°F).
- Apply a small amount of solder to the tip of the iron to improve heat transfer.
- Place the soldering iron tip against the component lead and the PCB pad simultaneously.
- Feed solder into the joint where the lead, pad, and iron meet. The solder should melt and flow around the lead and pad, creating a shiny, concave fillet.
- Remove the solder wire and the iron, keeping the iron in place for an additional 1-2 seconds to allow the joint to cool and solidify.
- Trim the excess lead length with wire cutters, leaving about 1-2mm of lead above the solder joint.
Surface Mount Soldering
Surface mount soldering involves attaching components directly to the surface of the PCB without passing leads through holes. SMD (Surface Mount Device) components are smaller and require more precision to solder. Here’s how to solder SMD components:
- Apply a small amount of Solder Paste or flux to the PCB pads where the component will be placed.
- Using tweezers, carefully position the SMD component on the PCB pads, aligning the leads with the pads.
- Heat your soldering iron to the appropriate temperature (typically 300-350°C or 572-662°F).
- Place the soldering iron tip against the component lead and the PCB pad simultaneously.
- Feed a small amount of solder into the joint where the lead, pad, and iron meet. The solder should melt and flow around the lead and pad, creating a shiny, concave fillet.
- Remove the solder wire and the iron, keeping the iron in place for an additional 1-2 seconds to allow the joint to cool and solidify.
- Repeat the process for the remaining leads on the component.
Inspecting and Cleaning Solder Joints
After soldering your components, it’s essential to inspect the solder joints for quality and cleanliness. Here’s how to inspect and clean your solder joints:
- Use a magnifying glass or microscope to visually inspect each solder joint for the following characteristics:
- Shiny, concave appearance
- Smooth transition from the component lead to the PCB pad
- No excess solder or solder bridges between adjacent pads
- No cold joints (dull, lumpy, or cracked appearance)
- If you notice any imperfections, reheat the joint with your soldering iron and apply more solder or remove excess solder as needed.
- Clean the PCB with isopropyl alcohol and a cotton swab to remove any flux residue or debris.
Common PCB Soldering Issues and Troubleshooting
Despite your best efforts, you may encounter some common issues during PCB soldering. Here are a few problems and their solutions:
- Cold joints: These occur when the solder doesn’t melt completely or when the joint moves before the solder solidifies. To fix a cold joint, reheat the joint with your soldering iron and apply fresh solder.
- Solder bridges: These occur when excess solder connects adjacent pads or leads. To remove a solder bridge, use solder wick or a desoldering pump to remove the excess solder.
- Insufficient solder: If a joint appears dull or lacks a proper fillet, reheat the joint and apply more solder.
- Overheated components: If you apply too much heat for too long, you may damage the component or the PCB. To avoid this, use the lowest effective temperature and minimize the time the iron is in contact with the joint.
Tips for Successful PCB Soldering
To ensure the best results when soldering your PCB, keep these tips in mind:
- Keep your soldering iron tip clean and tinned with fresh solder.
- Use the appropriate solder wire diameter and composition for your project.
- Apply heat to the joint, not the solder wire.
- Work quickly and efficiently to minimize heat exposure to components and the PCB.
- Practice on scrap PCBs or practice kits to improve your technique before working on a real project.
Frequently Asked Questions (FAQ)
- What type of solder should I use for PCB soldering?
-
For most PCB soldering projects, use a lead-free, rosin-core solder wire with a diameter between 0.5-0.8mm. Lead-free solder is preferred due to environmental and health concerns, while rosin-core solder contains a flux that helps the solder flow and adhere to the joint.
-
How do I choose the right soldering iron tip for my project?
-
The soldering iron tip size and shape should be appropriate for the size of the components and pads you’ll be soldering. For through-hole components, a chisel tip around 2-3mm wide is suitable. For SMD components, a finer conical or chisel tip around 0.5-1mm wide is recommended.
-
What temperature should I set my soldering iron to?
-
For lead-free solder, a temperature between 300-400°C (572-752°F) is typically appropriate. The exact temperature depends on the specific solder alloy and the size of the components and pads. Consult your solder wire manufacturer’s recommendations and start at the lower end of the range, increasing the temperature if needed.
-
How do I prevent ESD damage to sensitive components?
-
To prevent electrostatic discharge (ESD) damage, use ESD protection such as an ESD mat or wrist strap when handling sensitive components. Additionally, avoid touching component leads or PCB pads directly, and always ground yourself before working on the PCB.
-
Can I reuse solder wick or desoldering braid?
- While it’s possible to reuse solder wick or desoldering braid, it’s generally not recommended. The wick or braid becomes less effective at absorbing solder after each use, and it may introduce contamination to your solder joints. It’s best to use a fresh piece of wick or braid for each desoldering task.
Conclusion
Soldering a PCB may seem daunting at first, but with the right tools, techniques, and practice, you can create reliable and professional-looking solder joints. Remember to work in a clean, organized, and safe environment, and always inspect your solder joints for quality and cleanliness. With time and experience, you’ll develop the skills and confidence needed to tackle more complex PCB soldering projects.
Soldering Iron Temperature | Solder Wire Diameter | Tip Size (Through-Hole) | Tip Size (SMD) |
---|---|---|---|
300-400°C (572-752°F) | 0.5-0.8mm | 2-3mm chisel | 0.5-1mm conical or chisel |
By following this guide and referring to the information provided in the table, you’ll be well on your way to mastering the art of PCB soldering. Happy soldering!
No responses yet