Understanding FR4 and its composition
FR4 is a composite material made of woven fiberglass cloth impregnated with an epoxy resin binder. The “FR” in its name stands for “Flame Retardant,” indicating its inherent resistance to fire and high temperatures. The number “4” denotes the specific grade of the material, which is determined by the type of epoxy resin used and the manufacturing process employed.
The composition of FR4 typically includes:
– Fiberglass cloth (50-60% by weight)
– Epoxy resin (40-50% by weight)
– Flame retardant additives (usually brominated or phosphorus-based compounds)
– Other additives (such as fillers, colorants, and adhesion promoters)
The fiberglass cloth provides mechanical strength and dimensional stability to the laminate, while the epoxy resin acts as a binder and insulator. The flame retardant additives enhance the material’s resistance to ignition and fire propagation.
Thermal properties of FR4
Glass transition temperature (Tg)
One of the most important thermal properties of FR4 is its glass transition temperature (Tg). The Tg is the temperature at which the epoxy resin in the laminate transitions from a hard, glassy state to a soft, rubbery state. This transition is accompanied by a significant decrease in the material’s mechanical properties, such as stiffness and strength.
The Tg of FR4 typically ranges from 130°C to 180°C (266°F to 356°F), depending on the specific formulation of the epoxy resin used. Some high-performance FR4 laminates may have a Tg as high as 200°C (392°F).
Coefficient of thermal expansion (CTE)
Another important thermal property of FR4 is its coefficient of thermal expansion (CTE). The CTE is a measure of how much the material expands or contracts with changes in temperature. A low CTE is desirable for PCBs, as it minimizes the risk of thermal stress and warpage during manufacturing and operation.
FR4 has a relatively low CTE compared to other PCB materials, typically ranging from 12 to 16 ppm/°C (parts per million per degree Celsius) in the X and Y directions (in-plane) and 50 to 70 ppm/°C in the Z direction (through-thickness).
Thermal conductivity
Thermal conductivity is a measure of a material’s ability to conduct heat. A higher thermal conductivity allows for better heat dissipation, which is important for PCBs with high-power components or those operating in high-temperature environments.
FR4 has a relatively low thermal conductivity, typically ranging from 0.3 to 0.4 W/m·K (watts per meter-kelvin). This means that FR4 is not an ideal choice for applications that require rapid heat dissipation, such as high-power LED lighting or power electronics.
Factors affecting the Thermal stability of FR4
Several factors can influence the thermal stability of FR4, including:
-
Epoxy resin formulation: The type and composition of the epoxy resin used in the laminate can significantly affect its thermal properties. High-performance epoxy resins, such as those based on dicyandiamide (DICY) or phenol novolac, generally offer better thermal stability than standard epoxy resins.
-
Fiberglass content and weave style: The amount and type of fiberglass used in the laminate can also impact its thermal stability. Higher fiberglass content generally improves the material’s mechanical properties and dimensional stability at elevated temperatures. The weave style of the fiberglass cloth (e.g., plain, twill, or satin) can also affect the laminate’s thermal performance.
-
Manufacturing process: The manufacturing process used to produce the FR4 laminate can influence its thermal stability. Factors such as the curing temperature, pressure, and duration can affect the crosslink density of the epoxy resin, which in turn affects the material’s thermal properties.
-
Exposure to thermal stress: Prolonged exposure to high temperatures or thermal cycling can degrade the thermal stability of FR4 over time. This can lead to a reduction in the material’s mechanical properties, increased warpage, or even delamination of the PCB.
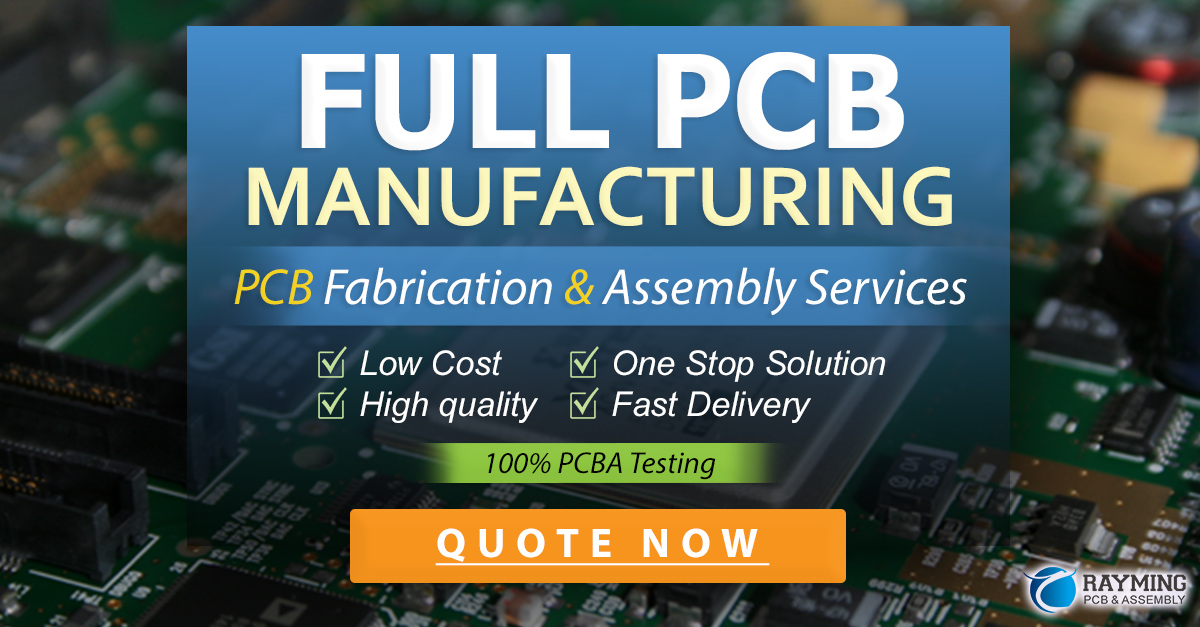
Testing the thermal stability of FR4
Several standardized test methods are used to evaluate the thermal stability of FR4 laminates. These tests help manufacturers and users determine the material’s suitability for specific applications and ensure consistent quality control.
Thermal stress testing
Thermal stress testing involves subjecting the FR4 laminate to elevated temperatures or thermal cycling to assess its ability to withstand thermal stress without degradation. Common thermal stress tests include:
-
Solder float test (IPC-TM-650 2.4.13): This test evaluates the laminate’s resistance to delamination and blistering when exposed to molten solder at 288°C (550°F) for a specified duration.
-
Thermal shock test (IPC-TM-650 2.6.7.1): This test subjects the laminate to alternating cycles of high and low temperatures (typically -65°C to 125°C or -85°F to 257°F) to assess its resistance to thermal stress and strain.
Thermal decomposition testing
Thermal decomposition testing is used to determine the temperature at which the FR4 laminate begins to break down and lose its structural integrity. Common thermal decomposition tests include:
-
Thermogravimetric analysis (TGA): This test measures the weight loss of the laminate as a function of temperature, providing information on the onset of thermal decomposition and the material’s residual weight at high temperatures.
-
Differential scanning calorimetry (DSC): This test measures the heat flow into or out of the laminate as a function of temperature, providing information on the material’s glass transition temperature, curing behavior, and other thermal events.
Flammability testing
Flammability testing is used to evaluate the FR4 laminate’s resistance to ignition and fire propagation. Common flammability tests include:
-
Underwriters Laboratories (UL) 94: This test assesses the laminate’s flammability by subjecting it to a small flame and measuring the time required for the flame to extinguish and the extent of burning.
-
IPC-TM-650 2.3.10: This test evaluates the laminate’s resistance to ignition and fire propagation when subjected to a high-temperature heat source.
Applications and limitations of FR4
FR4 is widely used in the electronics industry for the production of PCBs due to its good balance of mechanical, electrical, and thermal properties. Some common applications of FR4 include:
- Consumer electronics (smartphones, laptops, televisions)
- Automotive electronics (engine control units, infotainment systems)
- Industrial equipment (control panels, sensors, automation systems)
- Medical devices (patient monitors, diagnostic equipment)
- Aerospace and defense (avionics, communication systems)
However, FR4 also has some limitations that should be considered when selecting a PCB material for a specific application. These limitations include:
-
Limited thermal conductivity: FR4’s low thermal conductivity can limit its use in applications that require rapid heat dissipation, such as high-power electronics or LED lighting.
-
Reduced performance at high frequencies: FR4’s dielectric properties can degrade at high frequencies (above 1 GHz), making it less suitable for high-speed digital or RF applications.
-
Susceptibility to moisture absorption: FR4 can absorb moisture from the environment, which can lead to changes in its dielectric properties and reduce its thermal stability over time.
Frequently Asked Questions (FAQ)
- What is the typical glass transition temperature (Tg) of FR4?
-
The typical glass transition temperature (Tg) of FR4 ranges from 130°C to 180°C (266°F to 356°F), depending on the specific formulation of the epoxy resin used. Some high-performance FR4 laminates may have a Tg as high as 200°C (392°F).
-
How does the thermal stability of FR4 compare to other PCB materials?
-
FR4 has a good balance of thermal stability, mechanical strength, and electrical properties compared to other common PCB materials, such as CEM-1 or CEM-3. However, some high-performance materials, such as polyimide or PTFE-based laminates, offer better thermal stability and performance at high temperatures.
-
Can FR4 be used in high-temperature applications?
-
FR4 can be used in applications with operating temperatures up to its glass transition temperature (Tg), which typically ranges from 130°C to 180°C (266°F to 356°F). For applications with higher temperature requirements, high-performance FR4 laminates with a higher Tg or alternative PCB materials may be necessary.
-
What factors can affect the thermal stability of FR4 during PCB manufacturing?
-
Several factors can affect the thermal stability of FR4 during PCB manufacturing, including the lamination temperature and pressure, the drilling and routing processes, and the soldering temperature and duration. Proper control of these factors is essential to ensure the material’s thermal stability and prevent issues such as delamination or warpage.
-
How can I test the thermal stability of FR4 for my specific application?
- To test the thermal stability of FR4 for a specific application, you can use standardized test methods such as the solder float test (IPC-TM-650 2.4.13), thermal shock test (IPC-TM-650 2.6.7.1), or thermogravimetric analysis (TGA). These tests can help evaluate the material’s resistance to thermal stress, decomposition, and other thermal events under conditions relevant to your application.
Conclusion
The thermal stability of FR4 is a critical factor in determining its suitability for various PCB applications. With a glass transition temperature (Tg) typically ranging from 130°C to 180°C (266°F to 356°F) and a relatively low coefficient of thermal expansion (CTE), FR4 offers a good balance of thermal stability, mechanical strength, and electrical properties for many consumer, industrial, and automotive electronics applications.
However, it is essential to consider the specific requirements of each application and the factors that can influence the thermal stability of FR4, such as the epoxy resin formulation, fiberglass content, and manufacturing process. Standardized testing methods, such as thermal stress testing, thermal decomposition testing, and flammability testing, can help evaluate the material’s performance and ensure its suitability for a given application.
By understanding the thermal stability of FR4 and its limitations, PCB designers and manufacturers can make informed decisions when selecting materials and processes to ensure the reliability and longevity of their products.
Property | Typical Value Range |
---|---|
Glass Transition Temperature (Tg) | 130°C to 180°C (266°F to 356°F) |
Coefficient of Thermal Expansion (CTE) – X,Y | 12 to 16 ppm/°C |
Coefficient of Thermal Expansion (CTE) – Z | 50 to 70 ppm/°C |
Thermal Conductivity | 0.3 to 0.4 W/m·K |
Table 1: Typical thermal properties of FR4 laminates.
No responses yet