What is PTFE?
PTFE is a synthetic fluoropolymer discovered in 1938 by Roy J. Plunkett, a chemist working for DuPont. It is composed of carbon and fluorine atoms arranged in a repeating pattern of –CF2-CF2–. The strong carbon-fluorine bonds give PTFE its unique properties, including:
- Low friction coefficient
- High melting point (327°C or 620°F)
- Excellent chemical resistance
- Non-stick properties
- Electrical insulation
These properties make PTFE suitable for various applications, such as non-stick cookware, automotive parts, medical devices, and industrial coatings.
What are PFAS?
PFAS are a group of man-made chemicals that contain fluorine and carbon atoms. They are characterized by their strong carbon-fluorine bonds, which make them highly stable and resistant to degradation. PFAS have been used in various industries since the 1940s due to their unique properties, such as:
- Water and oil repellency
- Stain resistance
- Heat resistance
- Surfactant properties
There are thousands of PFAS compounds, with the most well-known being perfluorooctanoic acid (PFOA) and perfluorooctanesulfonic acid (PFOS). These two compounds have been phased out in many countries due to their potential health and environmental concerns.
The Relationship Between PTFE and PFAS
PTFE is a type of PFAS, as it contains fluorine and carbon atoms. However, not all PFAS are PTFE. The relationship between PTFE and PFAS can be summarized as follows:
- PTFE is a specific type of PFAS
- Not all PFAS are PTFE
- PTFE can be manufactured with or without the use of other PFAS compounds
Historically, PFOA was used as a processing aid in the manufacture of PTFE. However, due to health and environmental concerns, many manufacturers have phased out the use of PFOA and other long-chain PFAS in the production of PTFE.
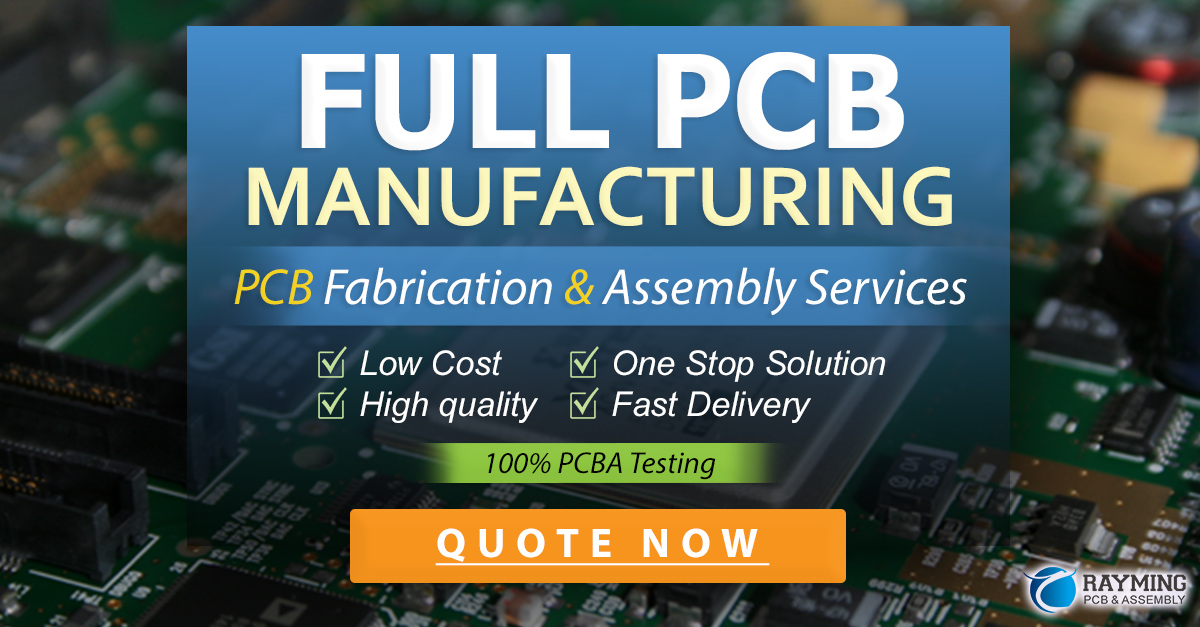
PTFE Manufacturing Processes
There are two main methods for manufacturing PTFE:
- Suspension polymerization
- Emulsion polymerization
Suspension Polymerization
In suspension polymerization, tetrafluoroethylene (TFE) monomer is dispersed in water and polymerized using a free-radical initiator. This process does not require the use of PFOA or other PFAS compounds. The resulting PTFE resin is then processed into various forms, such as granules, fine powders, or dispersions.
Emulsion Polymerization
In emulsion polymerization, TFE monomer is emulsified in water using a surfactant, typically a PFAS compound like PFOA. The polymerization is initiated using a free-radical initiator, and the resulting PTFE dispersion is then processed into various forms. Many manufacturers have replaced PFOA with alternative surfactants, such as short-chain PFAS or non-fluorinated alternatives.
PFOA-free PTFE
Due to health and environmental concerns associated with PFOA, many manufacturers have developed PFOA-free PTFE products. These products are made using alternative manufacturing processes or surfactants that do not involve the use of PFOA or other long-chain PFAS compounds.
Some examples of PFOA-free PTFE products include:
- GenX: Developed by DuPont (now Chemours), GenX is a short-chain PFAS used as a replacement for PFOA in the manufacture of PTFE.
- Dyneon TFM: Developed by 3M, Dyneon TFM is a PTFE produced using a modified emulsion polymerization process that does not require the use of PFOA.
- Hyflon AD: Developed by Solvay, Hyflon AD is a PTFE produced using a suspension polymerization process that does not involve the use of PFOA or other PFAS compounds.
It is important to note that while these products are PFOA-free, they may still contain other types of PFAS compounds. The long-term health and environmental impacts of these alternative PFAS compounds are still being studied.
Regulatory Landscape
The use of PFAS, particularly long-chain PFAS like PFOA and PFOS, has come under increased scrutiny from regulatory agencies worldwide. Many countries have implemented regulations to phase out or restrict the use of these compounds in various applications, including the manufacture of PTFE.
Some notable regulatory actions include:
- United States: In 2006, the U.S. Environmental Protection Agency (EPA) launched the PFOA Stewardship Program, which aimed to eliminate the use of PFOA in the manufacture of PTFE and other fluoropolymers by 2015. The EPA has also proposed a rule to designate PFOA and PFOS as hazardous substances under the Comprehensive Environmental Response, Compensation, and Liability Act (CERCLA).
- European Union: In 2020, the European Union (EU) banned the use of PFOA in the manufacture of PTFE and other products, with limited exceptions. The EU has also proposed a broader restriction on the use of PFAS in various applications.
- China: In 2019, China announced a plan to phase out the production and use of PFOA by 2025.
These regulatory actions have driven the development of PFOA-free PTFE and alternative manufacturing processes that do not rely on the use of long-chain PFAS compounds.
Frequently Asked Questions (FAQ)
1. Is all PTFE made with PFOA?
No, not all PTFE is made with PFOA. While PFOA was historically used as a processing aid in the manufacture of PTFE, many manufacturers have phased out its use due to health and environmental concerns. PTFE can be produced using alternative manufacturing processes or surfactants that do not involve the use of PFOA.
2. Is PTFE safe to use?
PTFE itself is generally considered safe to use when used as intended. It is inert, non-toxic, and does not react with most chemicals. However, concerns have been raised about the potential release of PFAS compounds during the manufacture or degradation of PTFE products. When PTFE is heated to temperatures above 260°C (500°F), it can release fumes that may cause flu-like symptoms known as “polymer fume fever.”
3. Can PTFE be recycled?
PTFE can be recycled, but the process is more complicated than recycling other plastics. PTFE has a high melting point and is not easily dissolved, making it difficult to recycle using traditional methods. However, some specialized recycling facilities can process PTFE waste into new products, such as fillers or coatings.
4. Are there alternatives to PTFE?
Yes, there are alternatives to PTFE for various applications. Some examples include:
- Silicone: Silicone coatings can provide non-stick properties similar to PTFE and are suitable for use in food-contact applications.
- Ceramic: Ceramic coatings can offer high heat resistance and non-stick properties, making them a suitable alternative for cookware.
- Stainless steel: For some industrial applications, stainless steel can provide similar chemical resistance and durability to PTFE.
5. How can I tell if a product contains PFAS?
It can be difficult for consumers to determine if a product contains PFAS, as manufacturers are not always required to disclose the presence of these compounds. Some steps you can take to minimize your exposure to PFAS include:
- Looking for products labeled as “PFOA-free” or “PFAS-free”
- Avoiding non-stick cookware and food packaging made with PTFE or other fluorinated coatings
- Checking with manufacturers about the use of PFAS in their products
- Supporting regulations that require greater transparency in the use of PFAS in consumer products
Conclusion
In conclusion, while all PTFE is a type of PFAS, not all PTFE contains PFOA or other long-chain PFAS compounds. The relationship between PTFE and PFAS is complex, and the presence of PFAS in PTFE products depends on the specific manufacturing process and materials used.
As concerns about the health and environmental impacts of PFAS continue to grow, manufacturers are developing alternative manufacturing processes and materials that do not rely on the use of long-chain PFAS compounds. Consumers can take steps to minimize their exposure to PFAS by seeking out PFOA-free or PFAS-free products and supporting regulations that require greater transparency in the use of these compounds.
While the long-term impacts of PFAS exposure are still being studied, it is clear that a more sustainable and health-conscious approach to the manufacture and use of PTFE and other fluoropolymers is needed. By working together, manufacturers, regulators, and consumers can help to ensure a safer and more sustainable future for all.
PTFE Manufacturing Process | PFOA Use | Alternative Surfactants |
---|---|---|
Suspension Polymerization | Not Required | None needed |
Emulsion Polymerization (Historical) | Required | None used |
Emulsion Polymerization (Modern) | Not Required | GenX, other short-chain PFAS, or non-fluorinated alternatives |
Example PFOA-free PTFE Products | Manufacturer | Manufacturing Process |
---|---|---|
GenX | Chemours (formerly DuPont) | Emulsion polymerization with short-chain PFAS |
Dyneon TFM | 3M | Modified emulsion polymerization |
Hyflon AD | Solvay | Suspension polymerization |
In summary, while PTFE is a type of PFAS, not all PTFE contains PFOA or other long-chain PFAS compounds. Manufacturers have developed alternative manufacturing processes and materials to produce PFOA-free PTFE, but the long-term impacts of these alternative compounds are still being studied. Consumers can take steps to minimize their exposure to PFAS by seeking out PFOA-free or PFAS-free products and supporting regulations that require greater transparency in the use of these compounds.
No responses yet