Introduction to Teflon (PTFE)
Teflon, the trademark name for PTFE, was accidentally discovered by Roy Plunkett, a chemist working for DuPont, in 1938. Since then, it has become a household name and an essential material in numerous applications. PTFE is a fluorocarbon solid, consisting of carbon and fluorine atoms arranged in a linear chain. Its chemical formula is (C2F4)n, where n represents the number of monomer units in the polymer chain.
Properties of Teflon (PTFE)
Teflon possesses a unique combination of properties that make it stand out from other materials:
-
Low friction coefficient: Teflon has one of the lowest friction coefficients of any solid material, ranging from 0.05 to 0.10. This means that it is highly slippery and resistant to sticking.
-
Chemical inertness: Teflon is chemically inert and resistant to most acids, bases, and solvents. It does not react with other substances, making it suitable for use in corrosive environments.
-
Thermal stability: Teflon can withstand temperatures ranging from -270°C to 260°C (-454°F to 500°F) without degrading or losing its properties.
-
Electrical insulation: Teflon is an excellent electrical insulator, with a dielectric constant of 2.1 and a dielectric strength of 60 kV/mm.
-
Non-wetting: Teflon has a low surface energy, which means that liquids and other substances do not adhere to its surface easily.
Advantages of Teflon (PTFE)
1. Non-stick Properties
One of the most well-known advantages of Teflon is its non-stick properties. Teflon-coated cookware has revolutionized the food industry by making cooking and cleaning easier and more convenient. The low friction coefficient of Teflon prevents food from sticking to the surface, reducing the need for oil or butter during cooking. This not only makes the cooking process more efficient but also promotes healthier cooking by reducing the amount of fat required.
Additionally, the non-stick properties of Teflon make cleaning cookware much simpler. Food particles and residues do not adhere to the surface, allowing for easy removal with minimal scrubbing. This saves time and effort in the kitchen and prolongs the life of the cookware.
2. Chemical Resistance
Teflon’s chemical inertness makes it an ideal material for applications where chemical resistance is crucial. It can withstand exposure to a wide range of chemicals, including acids, bases, and solvents, without degrading or losing its properties. This advantage makes Teflon suitable for use in various industries, such as:
-
Chemical processing: Teflon-lined pipes, valves, and reactors are used in chemical manufacturing to handle corrosive substances and prevent contamination.
-
Pharmaceutical industry: Teflon is used in the production and packaging of drugs and medical devices due to its chemical stability and non-reactivity.
-
Automotive industry: Teflon-coated components, such as seals and gaskets, are used in fuel systems and other automotive applications to resist chemical degradation.
3. Thermal Stability
Teflon’s ability to maintain its properties over a wide temperature range makes it suitable for applications involving extreme temperatures. It can withstand temperatures as low as -270°C (-454°F) and as high as 260°C (500°F) without degrading or losing its non-stick and chemical resistance properties.
This thermal stability is particularly advantageous in industries such as:
-
Aerospace: Teflon is used in the production of aircraft components, such as wire and cable insulation, due to its ability to withstand extreme temperature fluctuations.
-
Electronics: Teflon is used as an insulating material in electronic components, such as printed circuit boards and connectors, because of its thermal stability and excellent dielectric properties.
-
Industrial processing: Teflon-coated equipment, such as heat exchangers and drying belts, is used in high-temperature industrial processes to prevent sticking and ensure smooth operation.
4. Electrical Insulation
Teflon’s excellent dielectric properties make it an ideal material for electrical insulation applications. It has a low dielectric constant of 2.1 and a high dielectric strength of 60 kV/mm, which means that it can withstand high voltages without breaking down or conducting electricity.
This advantage is particularly useful in the following applications:
-
Wire and cable insulation: Teflon is used to insulate wires and cables in high-voltage applications, such as power transmission and distribution systems.
-
Printed circuit boards: Teflon-based laminates are used in the production of high-frequency printed circuit boards due to their low dielectric loss and stable dielectric constant.
-
Semiconductor manufacturing: Teflon is used in the production of semiconductor devices as an insulating material to prevent electrical leakage and ensure reliable performance.
5. Low Friction and Wear Resistance
Teflon’s low friction coefficient and wear resistance make it an excellent material for applications involving moving parts and surfaces. The slippery nature of Teflon reduces friction between components, minimizing wear and tear and extending the lifespan of the equipment.
This advantage is particularly beneficial in the following applications:
-
Bearings and seals: Teflon-coated bearings and seals are used in various machinery and equipment to reduce friction, prevent leakage, and extend service life.
-
Conveyor belts: Teflon-coated conveyor belts are used in food processing, packaging, and other industries to ensure smooth and efficient material handling.
-
Medical devices: Teflon is used in the production of medical devices, such as catheters and guidewires, to reduce friction and improve patient comfort during procedures.
Teflon (PTFE) Application Examples
Teflon’s unique combination of properties has led to its widespread use in various industries. The following table provides a summary of some common Teflon (PTFE) applications:
Industry | Application | Benefit |
---|---|---|
Food | Non-stick cookware | Easy cooking and cleaning |
Chemical Processing | Pipes, valves, and reactors | Chemical resistance and contamination prevention |
Automotive | Seals and gaskets | Chemical resistance and durability |
Aerospace | Wire and cable insulation | Thermal stability and electrical insulation |
Electronics | Printed circuit boards and connectors | Thermal stability and excellent dielectric properties |
Medical | Catheters and guidewires | Low friction and patient comfort |
Textile | Fabric coating | Water and stain resistance |
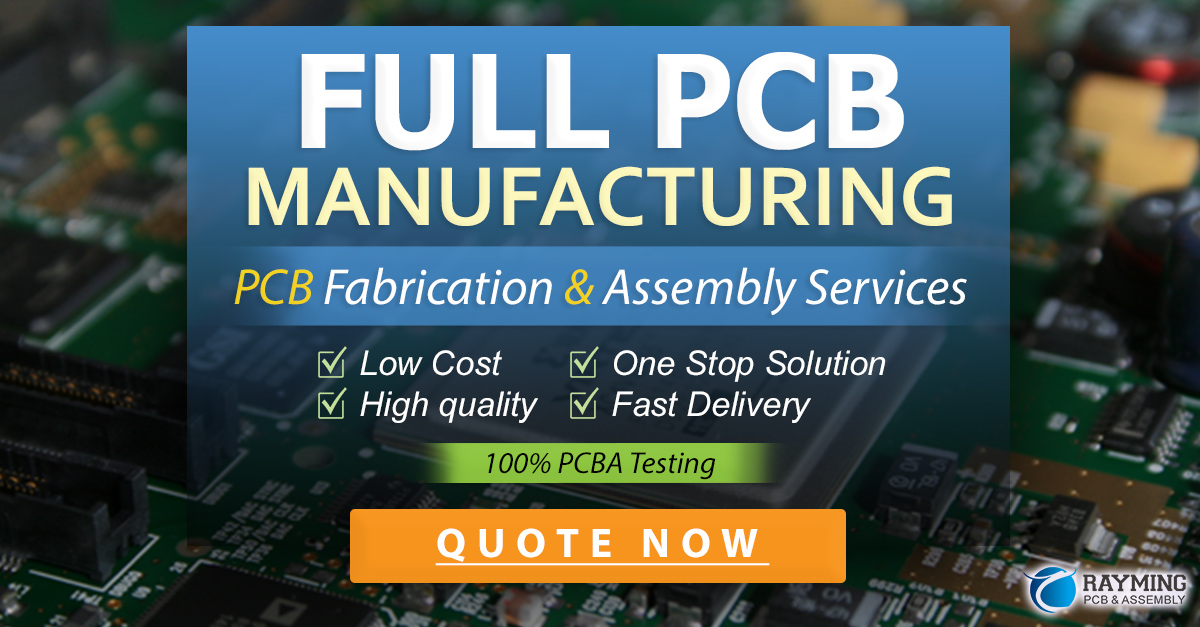
Frequently Asked Questions (FAQ)
1. Is Teflon safe for cooking?
Teflon-coated cookware is generally considered safe for cooking when used as intended. However, it is important to follow proper usage guidelines to ensure safety:
- Avoid overheating Teflon-coated pans, as temperatures above 260°C (500°F) can cause the coating to break down and release harmful fumes.
- Use low to medium heat settings when cooking with Teflon-coated cookware.
- Replace Teflon-coated pans if the coating becomes scratched or damaged.
2. Is Teflon environmentally friendly?
Teflon itself is chemically inert and does not pose a direct threat to the environment. However, the production of Teflon has historically involved the use of perfluorooctanoic acid (PFOA), which is a persistent organic pollutant. In recent years, major manufacturers have phased out the use of PFOA in Teflon production, and efforts are being made to develop more environmentally friendly alternatives.
3. Can Teflon be recycled?
Teflon is not commonly recycled due to the difficulty in separating it from other materials and the limited market for recycled Teflon. However, some specialized recycling facilities may accept Teflon-coated products, such as cookware, for recycling. It is best to check with local recycling centers for specific guidelines on disposing of Teflon-containing items.
4. Are there any alternatives to Teflon?
While Teflon remains a popular choice for many applications, there are some alternatives available:
-
Ceramic coatings: Non-stick ceramic coatings are used in cookware as an alternative to Teflon. These coatings are made from natural materials and are free from PFOA and PTFE.
-
Silicone: Silicone is used as a non-stick material in bakeware and kitchen utensils. It is heat-resistant, flexible, and easy to clean.
-
Stainless steel: For applications where non-stick properties are not critical, stainless steel can be used as a durable and chemically resistant alternative to Teflon.
5. How long does Teflon last?
The lifespan of Teflon-coated products depends on various factors, such as usage, care, and maintenance. In general, Teflon-coated cookware can last between 3 to 5 years with proper use and care. Industrial applications of Teflon may have longer lifespans, depending on the specific conditions and requirements of the application.
Conclusion
Teflon, or PTFE, is a remarkable material that has transformed various industries with its unique combination of properties. Its non-stick characteristics, chemical resistance, thermal stability, electrical insulation, and low friction coefficient have made it an essential component in numerous applications, ranging from cookware to aerospace engineering.
While Teflon has faced some concerns regarding its production process and environmental impact, manufacturers have taken steps to address these issues and develop more sustainable alternatives. Despite these challenges, the advantages of Teflon continue to make it a valuable material in many sectors.
As technology advances and new materials emerge, it is likely that Teflon will continue to evolve and find new applications. Its versatility and unparalleled properties ensure that it will remain an important material in shaping our world for years to come.
No responses yet