Introduction to Teflon and Rubber
Teflon and rubber are two distinct materials that are often used in various applications due to their unique properties. While they may share some similarities, such as being non-stick or flexible, they are fundamentally different in terms of their chemical composition, manufacturing process, and specific characteristics. In this article, we will explore the differences between Teflon and rubber, their properties, and their common uses.
What is Teflon?
Teflon, also known as polytetrafluoroethylene (PTFE), is a synthetic fluoropolymer of tetrafluoroethylene. It was accidentally discovered by Roy Plunkett, a chemist at DuPont, in 1938. Teflon is known for its exceptional properties, including:
- Non-stick surface
- High thermal stability
- Chemical inertness
- Low friction coefficient
- Electrical insulation
Chemical Composition of Teflon
Teflon is composed of carbon and fluorine atoms arranged in a linear chain. The chemical formula for Teflon is (C2F4)n, where n represents the number of repeating units in the polymer chain. The strong carbon-fluorine bonds give Teflon its unique properties, such as high thermal stability and chemical resistance.
Manufacturing Process of Teflon
The manufacturing process of Teflon involves the polymerization of tetrafluoroethylene (TFE) under high pressure and temperature conditions. The process can be summarized in the following steps:
- TFE monomer is introduced into a reactor along with water and a catalyst.
- The mixture is heated to a temperature between 100°C and 150°C and pressurized to 10-100 atmospheres.
- The catalyst initiates the polymerization reaction, forming PTFE particles.
- The PTFE particles are separated from the water and dried.
- The dried PTFE powder is processed into various forms, such as sheets, rods, or coatings, depending on the intended application.
Properties of Teflon
Teflon possesses several unique properties that make it suitable for various applications:
Property | Description |
---|---|
Non-stick | Teflon has a low surface energy, which prevents substances from adhering to its surface. |
High thermal stability | Teflon remains stable at temperatures up to 260°C (500°F) and has a melting point of 327°C (620°F). |
Chemical inertness | Teflon is resistant to most chemicals, including acids, bases, and solvents. |
Low friction coefficient | Teflon has one of the lowest friction coefficients of any solid material, making it ideal for reducing wear and tear in moving parts. |
Electrical insulation | Teflon is an excellent electrical insulator, with a high dielectric strength and low dielectric constant. |
Common Uses of Teflon
Teflon finds applications in various industries due to its unique properties:
- Non-stick cookware
- Chemical processing equipment
- Automotive components (e.g., bearings, seals)
- Electrical insulation for wires and cables
- Medical devices (e.g., catheters, surgical instruments)
- Textile coatings for stain and water resistance
What is Rubber?
Rubber is a natural or synthetic elastomer that possesses the ability to deform under stress and return to its original shape when the stress is removed. Natural rubber is obtained from the latex of certain plants, primarily the Hevea brasiliensis tree, while synthetic rubber is manufactured from petrochemicals.
Types of Rubber
There are two main types of rubber:
-
Natural Rubber: Natural rubber is derived from the latex of the Hevea brasiliensis tree. It consists of polyisoprene, a polymer of isoprene (C5H8) units. Natural rubber is known for its high elasticity, tensile strength, and resistance to abrasion.
-
Synthetic Rubber: Synthetic rubber is artificially produced from petrochemicals. There are various types of synthetic rubber, each with unique properties suited for specific applications. Some common types of synthetic rubber include:
-
Styrene-butadiene rubber (SBR)
- Nitrile rubber (NBR)
- Neoprene (polychloroprene)
- Ethylene propylene diene monomer (EPDM) rubber
- Silicone rubber
Manufacturing Process of Rubber
The manufacturing process of rubber varies depending on the type of rubber and the desired end product. However, the general steps involved in rubber production are as follows:
-
Latex Collection (for natural rubber): The latex is collected from rubber trees by making incisions in the bark and allowing the latex to flow into containers.
-
Compounding: The raw rubber (natural or synthetic) is mixed with various additives, such as vulcanizing agents, fillers, plasticizers, and antioxidants, to achieve the desired properties.
-
Shaping: The compounded rubber is then shaped into the desired form using methods such as extrusion, molding, or calendering.
-
Vulcanization: The shaped rubber is subjected to heat and pressure in the presence of a vulcanizing agent (usually sulfur) to form cross-links between the polymer chains. This process improves the rubber’s strength, elasticity, and durability.
-
Finishing: The vulcanized rubber product may undergo additional finishing processes, such as trimming, painting, or coating, depending on the specific application.
Properties of Rubber
Rubber possesses several unique properties that make it suitable for various applications:
Property | Description |
---|---|
Elasticity | Rubber can deform under stress and return to its original shape when the stress is removed. |
High tensile strength | Rubber can withstand high levels of stress before breaking. |
Abrasion resistance | Rubber is resistant to wear and tear caused by friction. |
Electrical insulation | Some types of rubber, such as silicone rubber, are excellent electrical insulators. |
Chemical resistance | Certain types of rubber, such as nitrile rubber, are resistant to oils, fuels, and other chemicals. |
Common Uses of Rubber
Rubber finds applications in various industries due to its unique properties:
- Tires for vehicles
- Seals and gaskets
- Conveyor belts
- Hoses and tubing
- Electrical insulation
- Footwear and clothing
- Medical devices (e.g., gloves, tubing)
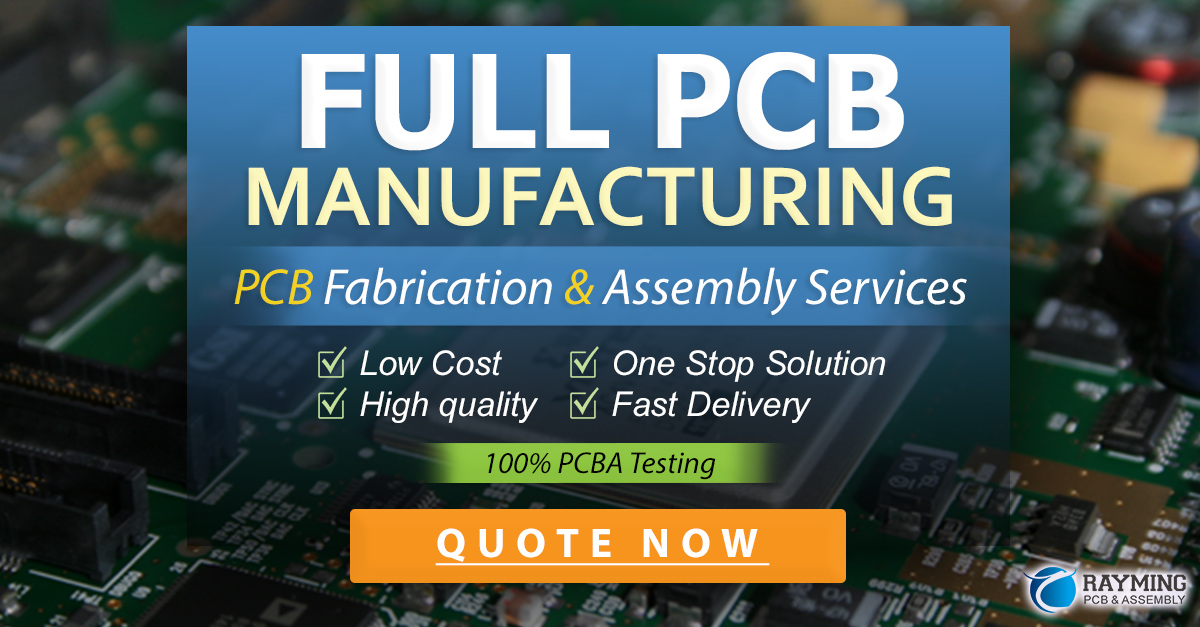
Differences between Teflon and Rubber
Although Teflon and rubber may share some similarities, such as being non-stick or flexible, they have several key differences:
- Chemical Composition:
- Teflon is a synthetic fluoropolymer composed of carbon and fluorine atoms.
-
Rubber is a natural or synthetic elastomer composed of various monomers, such as isoprene or styrene and butadiene.
-
Manufacturing Process:
- Teflon is produced by polymerizing tetrafluoroethylene under high pressure and temperature conditions.
-
Rubber is manufactured by compounding raw rubber with additives, shaping, vulcanizing, and finishing.
-
Properties:
- Teflon has a non-stick surface, high thermal stability, chemical inertness, low friction coefficient, and excellent electrical insulation properties.
-
Rubber is known for its elasticity, high tensile strength, abrasion resistance, and, in some cases, chemical resistance and electrical insulation properties.
-
Applications:
- Teflon is commonly used in non-stick cookware, chemical processing equipment, automotive components, electrical insulation, medical devices, and textile coatings.
- Rubber is used in tires, seals, gaskets, conveyor belts, hoses, electrical insulation, footwear, clothing, and medical devices.
Frequently Asked Questions (FAQ)
- Can Teflon be used in high-temperature applications?
-
Yes, Teflon remains stable at temperatures up to 260°C (500°F) and has a melting point of 327°C (620°F), making it suitable for high-temperature applications.
-
Is rubber biodegradable?
-
Natural rubber is biodegradable, as it is derived from plant sources. However, the biodegradability of synthetic rubber varies depending on its composition and the presence of additives.
-
Can Teflon be recycled?
-
Teflon can be recycled, but the process is complex and not widely available. It involves decomposing the Teflon into its constituent monomers, which can then be used to produce new Teflon products.
-
What is the difference between vulcanized and unvulcanized rubber?
-
Vulcanized rubber has undergone the vulcanization process, which involves the formation of cross-links between the polymer chains, improving its strength, elasticity, and durability. Unvulcanized rubber lacks these cross-links and has lower strength and durability.
-
Is Teflon safe for use in cookware?
- Teflon is generally considered safe for use in cookware when used as intended. However, when Teflon is heated to temperatures above 260°C (500°F), it can start to decompose and release toxic fumes. It is essential to use Teflon-coated cookware according to the manufacturer’s instructions and avoid overheating.
Conclusion
In conclusion, Teflon and rubber are two distinct materials with unique properties and applications. While they may share some similarities, such as being non-stick or flexible, they differ in their chemical composition, manufacturing process, and specific characteristics. Teflon is a synthetic fluoropolymer known for its non-stick surface, high thermal stability, chemical inertness, low friction coefficient, and excellent electrical insulation properties. On the other hand, rubber is a natural or synthetic elastomer known for its elasticity, high tensile strength, abrasion resistance, and, in some cases, chemical resistance and electrical insulation properties.
Understanding the differences between Teflon and rubber is crucial when selecting materials for specific applications. By considering factors such as the intended use, operating conditions, and required properties, engineers and manufacturers can choose the most suitable material to ensure optimal performance, durability, and safety.
As technology advances and new materials are developed, it is essential to stay informed about the properties and potential applications of various materials, including Teflon and rubber. Ongoing research and development efforts aim to improve the performance, sustainability, and versatility of these materials, opening up new possibilities for innovation across industries.
No responses yet