Introduction to Heavy Copper PCB
Heavy copper PCB, also known as thick copper PCB or high current PCB, is a type of printed Circuit board that features thicker copper traces than standard PCBs. These boards are designed to handle higher currents and temperatures, making them ideal for applications that require high power delivery or thermal management.
Key Characteristics of Heavy Copper PCB
- Thicker copper traces (typically 3 oz or more)
- Improved current carrying capacity
- Enhanced thermal dissipation
- Increased durability and reliability
- Suitable for high-power applications
Advantages of Using Heavy Copper PCB
1. Higher Current Carrying Capacity
One of the primary benefits of using heavy copper PCBs is their ability to handle higher currents compared to standard PCBs. The thicker copper traces allow for increased current flow without overheating or causing damage to the board. This is particularly important in power electronics, where high currents are common.
2. Improved Thermal Management
Heavy copper PCBs offer better thermal management than standard PCBs due to their increased Copper thickness. The thicker copper traces act as efficient heat sinks, dissipating heat more effectively and preventing the board from overheating. This is crucial in applications where high temperatures can lead to component failure or reduced performance.
3. Enhanced Durability and Reliability
The thicker copper traces in heavy copper PCBs make them more durable and resistant to mechanical stress and vibrations. This increased robustness translates to improved reliability and longer product life, especially in harsh environments or applications subject to frequent physical stress.
4. Reduced Voltage Drop
In high-current applications, voltage drop can be a significant issue. Heavy copper PCBs help minimize voltage drop by providing lower resistance paths for current flow. This ensures that the required voltage is delivered to components consistently, maintaining optimal performance.
Applications of Heavy Copper PCB
Heavy copper PCBs find applications in various industries and sectors where high power delivery and thermal management are critical. Some common applications include:
- Power electronics
- Automotive electronics
- Industrial control systems
- Telecommunications equipment
- Aerospace and defense systems
- Medical devices
- Renewable energy systems
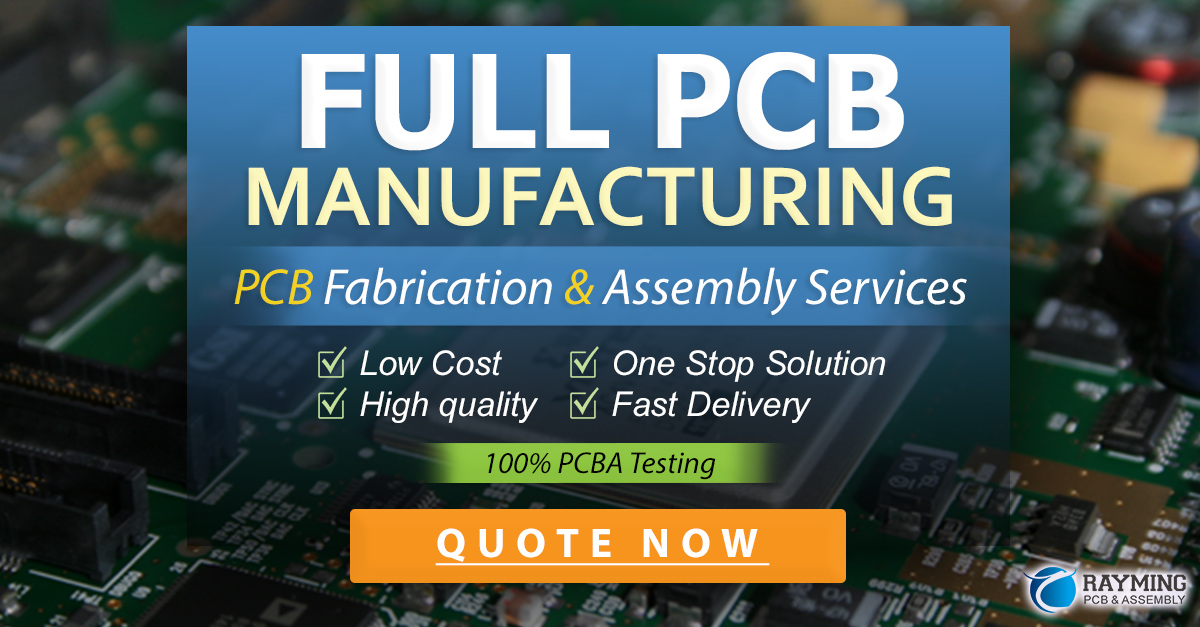
Manufacturing Process of Heavy Copper PCB
The manufacturing process for heavy copper PCBs is similar to that of standard PCBs, with a few key differences to accommodate the thicker copper traces.
1. PCB Design
The PCB design phase is crucial for heavy copper PCBs. Designers must consider the specific requirements of the application, such as current carrying capacity, thermal management, and mechanical durability. They must also ensure that the design is optimized for manufacturability, considering factors like trace width, spacing, and hole sizes.
2. Copper Foil Lamination
In heavy copper PCBs, the copper foil used is thicker than in standard PCBs. The most common copper thicknesses for heavy copper PCBs are 3 oz (105 μm), 4 oz (140 μm), and 6 oz (210 μm). The chosen copper foil is laminated onto the substrate material using heat and pressure.
3. Drilling and Plating
After lamination, holes are drilled into the board for component placement and interconnection. The holes are then plated with copper to create conductive paths between layers. In heavy copper PCBs, the plating process may take longer due to the increased copper thickness.
4. Etching and Solder Mask Application
The unwanted copper is etched away, leaving behind the desired circuit pattern. A solder mask is then applied to protect the copper traces and prevent short circuits. The solder mask also helps to improve the board’s durability and resistance to environmental factors.
5. Surface Finishing
Finally, a surface finish is applied to the exposed copper areas to protect them from oxidation and enhance solderability. Common surface finishes for heavy copper PCBs include HASL (Hot Air Solder Leveling), ENIG (Electroless Nickel Immersion Gold), and OSP (Organic Solderability Preservative).
Design Considerations for Heavy Copper PCB
When designing heavy copper PCBs, several factors must be taken into account to ensure optimal performance and manufacturability.
1. Trace Width and Spacing
The thicker copper traces in heavy copper PCBs require careful consideration of trace width and spacing. Designers must ensure that the traces are wide enough to handle the required current without overheating, while also maintaining sufficient spacing between traces to prevent short circuits and signal interference.
2. Thermal Management
Proper thermal management is essential in heavy copper PCB design. Designers must consider factors such as component placement, copper thickness, and the use of thermal vias to ensure effective heat dissipation. Thermal simulations can help optimize the design for optimal thermal performance.
3. Mechanical Durability
Heavy copper PCBs are often used in applications subject to mechanical stress and vibrations. Designers must consider the board’s mechanical durability, incorporating features such as reinforced Mounting holes, strain relief, and the use of appropriate substrate materials.
4. Manufacturability
Designing for manufacturability is crucial in heavy copper PCBs. Designers must consider factors such as minimum trace width, hole sizes, and copper thickness to ensure that the board can be manufactured reliably and cost-effectively.
Testing and Quality Control of Heavy Copper PCB
To ensure the reliability and performance of heavy copper PCBs, rigorous testing and quality control processes are employed during manufacturing.
1. Electrical Testing
Electrical testing is performed to verify the board’s functionality and ensure that it meets the specified electrical requirements. This includes continuity testing, insulation resistance testing, and high-voltage testing.
2. Thermal Testing
Thermal testing is conducted to assess the board’s ability to dissipate heat effectively and maintain acceptable operating temperatures. This may involve the use of thermal imaging cameras, thermocouples, and temperature-controlled chambers.
3. Mechanical Testing
Mechanical testing is performed to evaluate the board’s durability and resistance to physical stress. This may include vibration testing, shock testing, and bend testing.
4. Visual Inspection
Visual inspection is carried out to identify any surface defects, such as scratches, dents, or discoloration. Automated optical inspection (AOI) systems are often used to detect these defects quickly and accurately.
Challenges and Limitations of Heavy Copper PCB
While heavy copper PCBs offer numerous benefits, they also present some challenges and limitations that must be considered.
1. Higher Manufacturing Costs
The increased copper thickness and specialized manufacturing processes required for heavy copper PCBs result in higher manufacturing costs compared to standard PCBs. This can impact the overall cost of the end product and may not be suitable for all applications.
2. Longer Lead Times
The manufacturing process for heavy copper PCBs is more time-consuming due to the increased copper thickness and additional processing steps. This can result in longer lead times, which may not be feasible for time-sensitive projects.
3. Limited Flexibility
The thicker copper traces in heavy copper PCBs can limit the board’s flexibility, making it more challenging to design for applications that require bendable or flexible PCBs.
4. Increased Weight
The increased copper thickness in heavy copper PCBs results in a higher overall board weight. This may be a concern in weight-sensitive applications, such as aerospace or portable devices.
Future Trends in Heavy Copper PCB Technology
As technology advances and the demand for high-power electronics grows, heavy copper PCB technology is expected to evolve to meet new challenges and requirements.
1. Advanced Materials
The development of advanced substrate materials, such as high-temperature laminates and ceramic substrates, will enable heavy copper PCBs to operate in even more demanding environments and withstand higher temperatures.
2. Improved Manufacturing Processes
Advancements in manufacturing processes, such as laser drilling and selective plating, will help improve the precision and efficiency of heavy copper PCB production, reducing costs and lead times.
3. Integration with Other Technologies
The integration of heavy copper PCBs with other technologies, such as embedded components and 3D printing, will open up new possibilities for high-power electronics design and manufacturing.
4. Increased Adoption in Emerging Industries
As industries such as electric vehicles, renewable energy, and 5G telecommunications continue to grow, the demand for heavy copper PCBs is expected to increase, driving further innovation and development in the field.
Frequently Asked Questions (FAQ)
1. What is the difference between heavy copper PCB and standard PCB?
Heavy copper PCBs have thicker copper traces (typically 3 oz or more) compared to standard PCBs, which usually have 1 oz or 2 oz copper traces. The increased copper thickness allows heavy copper PCBs to handle higher currents and dissipate heat more effectively.
2. What are the most common copper thicknesses used in heavy copper PCBs?
The most common copper thicknesses for heavy copper PCBs are 3 oz (105 μm), 4 oz (140 μm), and 6 oz (210 μm).
3. Can heavy copper PCBs be used in flexible applications?
Heavy copper PCBs are generally less flexible than standard PCBs due to the increased copper thickness. However, some specialized heavy copper PCBs can be designed for flexible applications using specific substrate materials and manufacturing techniques.
4. Are heavy copper PCBs more expensive than standard PCBs?
Yes, heavy copper PCBs are typically more expensive than standard PCBs due to the increased copper thickness and specialized manufacturing processes required.
5. What industries commonly use heavy copper PCBs?
Heavy copper PCBs are commonly used in industries such as power electronics, automotive electronics, industrial control systems, telecommunications, aerospace and defense, medical devices, and renewable energy systems.
Conclusion
Heavy copper PCBs are a crucial technology for applications that require high power delivery and effective thermal management. With their increased copper thickness, these boards offer numerous advantages, including higher current carrying capacity, improved thermal dissipation, enhanced durability, and reduced voltage drop.
As technology continues to advance and the demand for high-power electronics grows, heavy copper PCB technology is expected to evolve, incorporating advanced materials, improved manufacturing processes, and integration with other technologies. By understanding the benefits, applications, and design considerations of heavy copper PCBs, engineers and manufacturers can leverage this technology to create more efficient, reliable, and high-performance electronic systems.
No responses yet