PCB composition Overview
A PCB is a multi-layered structure composed of conductive and insulating materials. The primary components of a PCB include:
- Substrate
- Copper layers
- Solder mask
- Silkscreen
- Surface finish
Each of these components plays a vital role in the functionality and durability of the PCB. Let’s explore each component in more detail.
Substrate
The substrate is the foundation of the PCB, providing mechanical support and electrical insulation for the conductive layers. The most common substrate materials are:
FR-4
FR-4 (Flame Retardant 4) is the most widely used substrate material for PCBs. It is a composite material made of woven fiberglass cloth impregnated with an epoxy resin binder. FR-4 offers excellent mechanical strength, electrical insulation properties, and resistance to moisture and heat.
High-Frequency Laminates
For applications requiring high-frequency signal transmission, such as RF and microwave circuits, specialized substrate materials are used. These materials, such as Rogers’ RO4000 series or Isola’s I-Tera, offer lower dielectric loss and more consistent dielectric properties over a wide frequency range compared to FR-4.
Flexible Substrates
Flexible PCBs use a different type of substrate material, such as polyimide (Kapton) or polyester (PET). These materials allow the PCB to bend and flex without damaging the conductive layers, making them suitable for applications that require flexibility or space-saving designs.
Copper Layers
The conductive layers of a PCB are made of thin sheets of copper foil laminated onto the substrate. The number of copper layers in a PCB can vary depending on the complexity of the design and the required functionality. PCBs can be categorized based on the number of copper layers:
PCB Type | Number of Copper Layers |
---|---|
Single-sided PCB | 1 |
Double-sided PCB | 2 |
Multi-layer PCB | 3 or more |
The copper layers are etched to create the desired circuit patterns, connecting the various electronic components. The thickness of the copper foil is typically measured in ounces per square foot (oz/ft²), with common thicknesses being 0.5 oz/ft², 1 oz/ft², and 2 oz/ft².
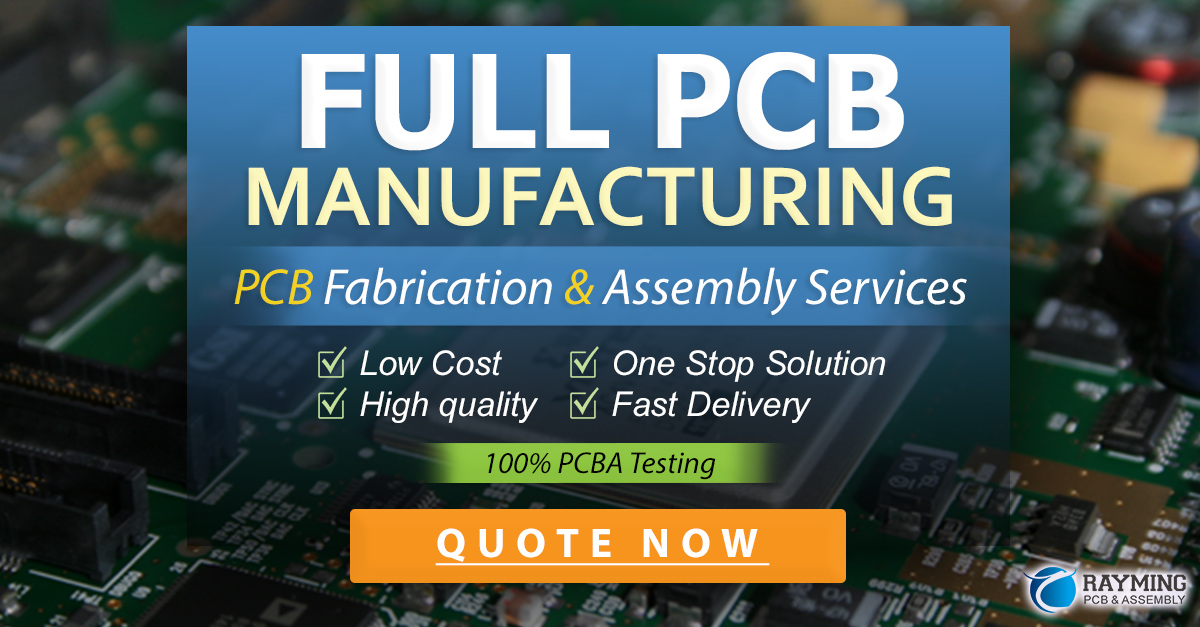
Solder Mask
The solder mask is a thin, protective layer applied over the copper layers of the PCB. Its primary functions are:
- Insulating the copper traces to prevent short circuits
- Protecting the copper from oxidation and corrosion
- Providing a surface for applying solder paste during component assembly
Solder masks are typically made of a photoimageable polymer and are available in various colors, with green being the most common. Other popular colors include red, blue, yellow, and black.
Silkscreen
The silkscreen layer is a non-conductive, textual layer printed on top of the solder mask. It is used to provide information about the PCB, such as:
- Component designators (e.g., R1, C2, U3)
- Polarity indicators
- Test points
- Company logos or product names
The silkscreen is typically printed in white color, but other colors, such as black or yellow, can also be used depending on the color of the solder mask and the desired contrast.
Surface Finish
The surface finish is a protective coating applied to the exposed copper areas of the PCB, such as pads and through-holes. Its primary functions are:
- Protecting the copper from oxidation
- Enhancing solderability
- Improving the shelf life of the PCB
There are several types of surface finishes available, each with its own advantages and disadvantages. The most common surface finishes are:
Hot Air Solder Leveling (HASL)
HASL is a process in which the PCB is dipped into a molten solder bath and then blown with hot air to remove excess solder. This results in a thin, uniform layer of solder on the exposed copper areas. HASL is a cost-effective and widely used surface finish, but it may not be suitable for fine-pitch components due to the possibility of uneven surface.
Electroless Nickel Immersion Gold (ENIG)
ENIG is a two-layer surface finish consisting of a nickel layer plated onto the copper, followed by a thin layer of gold. The nickel layer provides a barrier against copper diffusion, while the gold layer protects the nickel from oxidation and enhances solderability. ENIG offers a flat, uniform surface suitable for fine-pitch components but is more expensive than HASL.
Immersion Silver (IAg)
IAg is a single-layer surface finish that involves the deposition of a thin layer of silver onto the exposed copper areas. It provides good solderability and is a cost-effective alternative to ENIG. However, IAg is prone to tarnishing over time and may have a shorter shelf life compared to ENIG.
Immersion Tin (ISn)
ISn is another single-layer surface finish that deposits a thin layer of tin onto the exposed copper areas. It offers good solderability and is a lead-free alternative to HASL. ISn is less expensive than ENIG and IAg but may be prone to tin whiskers, which can cause short circuits.
Multi-Layer PCB Composition
Multi-layer PCBs are composed of multiple layers of copper and insulating material, allowing for more complex designs and higher component density. The layers are connected through vias, which are conductive holes drilled through the PCB.
A typical 4-layer PCB stack-up might look like this:
Layer | Material |
---|---|
Top Copper | Copper foil |
Prepreg | FR-4 |
Inner Copper 1 | Copper foil |
Core | FR-4 |
Inner Copper 2 | Copper foil |
Prepreg | FR-4 |
Bottom Copper | Copper foil |
The prepreg layers are made of partially cured FR-4 material, which is used to bond the copper layers together during the lamination process. The core layer is a fully cured FR-4 material that provides additional mechanical support.
FAQ
- What is the most common substrate material used in PCBs?
-
FR-4 (Flame Retardant 4) is the most widely used substrate material for PCBs due to its excellent mechanical and electrical properties.
-
What is the purpose of the solder mask on a PCB?
-
The solder mask serves to insulate the copper traces, protect the copper from oxidation and corrosion, and provide a surface for applying solder paste during component assembly.
-
What is the difference between HASL and ENIG surface finishes?
-
HASL is a cost-effective surface finish that involves dipping the PCB in a molten solder bath, while ENIG is a two-layer finish consisting of a nickel layer and a thin gold layer. ENIG provides a flatter, more uniform surface suitable for fine-pitch components but is more expensive than HASL.
-
What are vias in a multi-layer PCB?
-
Vias are conductive holes drilled through the PCB to connect the different copper layers, allowing for more complex designs and higher component density.
-
What are the advantages of using a flexible substrate in PCBs?
- Flexible substrates, such as polyimide or polyester, allow the PCB to bend and flex without damaging the conductive layers. This makes them suitable for applications that require flexibility or space-saving designs, such as wearable electronics or compact devices.
Conclusion
The composition of a PCB board is a critical factor in determining its performance, reliability, and longevity. By understanding the various materials and layers that make up a PCB, engineers and manufacturers can design and produce high-quality boards that meet the specific requirements of their applications. From the substrate and copper layers to the solder mask and surface finish, each component plays a vital role in the overall functionality of the PCB. As technology advances and electronic devices become more complex, the importance of understanding PCB composition will only continue to grow.
No responses yet