Introduction to PCB quality
Printed Circuit boards (PCBs) are the backbone of modern electronics. They provide the foundation upon which electronic components are mounted and interconnected to form a functional circuit. The quality of a PCB directly impacts the performance, reliability, and longevity of the end product. In this article, we will focus on the quality issues related to gold plated PCBs, specifically those manufactured by Goldfinger, and discuss the measures that can be taken to address these issues.
What is a Gold Plated PCB?
Gold plated PCBs are circuit boards that have a layer of gold deposited on the surface of the copper traces and pads. The gold plating provides several advantages over bare copper, including:
- Improved corrosion resistance
- Enhanced electrical conductivity
- Better solderability
- Increased durability
These properties make gold plated PCBs ideal for applications that demand high reliability, such as in the aerospace, military, and medical industries.
Goldfinger PCB manufacturing Process
Goldfinger is a well-known manufacturer of gold plated PCBs. Their manufacturing process involves the following steps:
-
Substrate preparation: The PCB substrate, typically made of FR-4 or other high-quality materials, is cleaned and prepared for the subsequent processes.
-
Copper plating: A layer of copper is electroplated onto the substrate to form the conductive traces and pads.
-
Nickel plating: A layer of nickel is electroplated onto the copper layer to provide a barrier between the copper and the gold layer, preventing diffusion and improving adhesion.
-
Gold plating: Finally, a layer of gold is electroplated onto the nickel layer. The thickness of the gold layer varies depending on the application and customer requirements, but typically ranges from 0.05 to 2.54 microns (2 to 100 microinches).
Common Quality Issues in Goldfinger Gold Plated PCBs
Despite the stringent manufacturing processes and quality control measures employed by Goldfinger, quality issues can still arise in their gold plated PCBs. Some of the most common issues include:
1. Inadequate Gold Thickness
One of the most critical factors in determining the quality of a gold plated PCB is the thickness of the gold layer. If the gold layer is too thin, it may not provide sufficient protection against corrosion and wear. On the other hand, if the gold layer is too thick, it can lead to issues such as embrittlement and poor adhesion.
The table below shows the recommended gold thickness for various applications:
Application | Recommended Gold Thickness (microns) |
---|---|
Connectors | 0.76 – 1.27 |
Edge connectors | 1.27 – 2.54 |
Wire bonding pads | 0.76 – 1.27 |
Soldering pads | 0.05 – 0.25 |
To ensure adequate gold thickness, Goldfinger employs strict process controls and regularly monitors the plating baths. However, variations in the plating process can still lead to inconsistencies in the gold thickness across a single PCB or between different batches.
2. Poor Adhesion
Another common issue with gold plated PCBs is poor adhesion between the gold layer and the underlying nickel layer. Poor adhesion can lead to delamination, where the gold layer separates from the nickel layer, exposing the copper traces to corrosion and oxidation.
Several factors can contribute to poor adhesion, including:
- Contamination of the nickel surface prior to gold plating
- Incorrect plating parameters, such as current density and bath composition
- Stresses introduced during the plating process
To mitigate adhesion issues, Goldfinger follows strict cleaning and surface preparation protocols, and closely monitors the plating process parameters. They also employ various quality control techniques, such as tape tests and cross-section analysis, to assess the adhesion of the gold layer.
3. Pinholes and Porosity
Pinholes and porosity are small defects in the gold layer that can expose the underlying nickel and copper layers to the environment, leading to corrosion and reduced product life.
Pinholes can occur due to a variety of reasons, including:
- Contamination of the plating bath
- Incorrect plating parameters
- Mechanical damage during handling
Porosity, on the other hand, is often a result of the inherent structure of the electroplated gold layer. The gold atoms are deposited in a columnar structure, with small gaps between the columns that can allow moisture and contaminants to penetrate the gold layer.
To minimize pinholes and porosity, Goldfinger employs several measures, such as:
- Maintaining strict cleanliness in the plating area
- Regularly monitoring and adjusting the plating bath composition
- Using pulse plating techniques to produce a denser, less porous gold layer
4. Connectors’ Mating Issues
Gold plated connectors are often used in high-reliability applications, such as in aerospace and military equipment. However, mating issues can arise if the gold layer on the connector is too thick or too soft.
If the gold layer is too thick, it can lead to increased insertion forces and reduced contact area, resulting in poor electrical performance. On the other hand, if the gold layer is too soft, it can lead to excessive wear and debris generation during mating and unmating cycles.
To address these issues, Goldfinger works closely with connector manufacturers to optimize the gold plating process for specific connector designs. They also employ various test methods, such as insertion force testing and durability testing, to ensure the connectors meet the required performance specifications.
Measures to Improve Goldfinger Gold Plated PCB Quality
1. Continuous Process Improvement
Goldfinger continuously strives to improve its manufacturing processes to deliver the highest quality gold plated PCBs. This involves:
- Regular audits and assessments of the manufacturing process
- Implementation of statistical process control (SPC) techniques
- Investment in state-of-the-art equipment and technology
- Training and development of the workforce
By continuously monitoring and improving their processes, Goldfinger can identify and address potential quality issues before they impact the end product.
2. Strict Raw Material Control
The quality of the raw materials used in the manufacturing process directly impacts the quality of the final product. Goldfinger employs strict raw material control measures to ensure consistency and quality, including:
- Supplier qualification and audits
- Incoming material inspections
- Material traceability throughout the manufacturing process
- Regular testing and validation of material properties
3. Advanced Quality Control Techniques
Goldfinger utilizes a range of advanced quality control techniques to assess the quality of their gold plated PCBs, such as:
- X-ray fluorescence (XRF) analysis for measuring gold thickness
- Scanning electron microscopy (SEM) for detecting surface defects and analyzing the gold layer structure
- Cross-section analysis for evaluating the adhesion and interfaces between the different layers
- Electrical testing for assessing the conductivity and performance of the PCB
By employing these techniques, Goldfinger can identify and address quality issues quickly and effectively, ensuring that only products that meet the highest quality standards are delivered to their customers.
4. Customer Collaboration and Support
Goldfinger works closely with their customers to understand their specific requirements and provide tailored solutions. This involves:
- Early engagement in the product design phase to optimize the PCB layout and specifications
- Regular communication and updates throughout the manufacturing process
- Comprehensive technical support and troubleshooting services
- Flexibility to accommodate customer-specific testing and inspection requirements
By fostering a strong partnership with their customers, Goldfinger can ensure that the delivered products meet the exact needs and expectations of each customer.
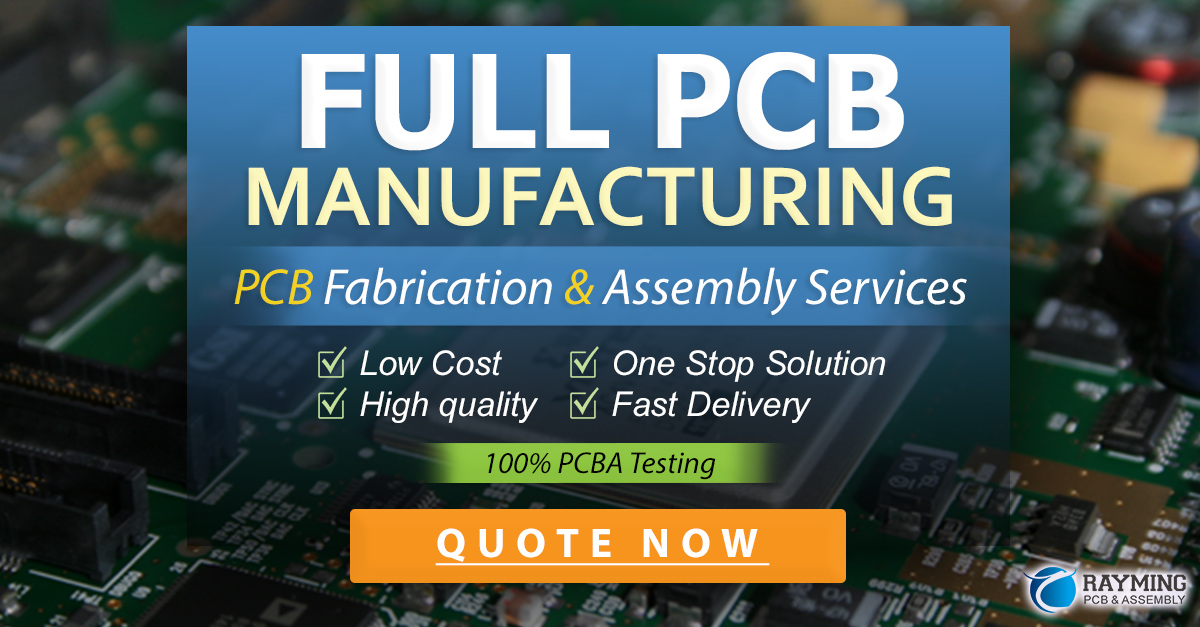
Frequently Asked Questions (FAQ)
-
Q: What is the typical gold thickness used in Goldfinger’s gold plated PCBs?
A: The gold thickness used by Goldfinger varies depending on the application and customer requirements. Typical thicknesses range from 0.05 to 2.54 microns (2 to 100 microinches). -
Q: How does Goldfinger ensure the adhesion of the gold layer to the underlying nickel layer?
A: Goldfinger employs strict cleaning and surface preparation protocols, closely monitors the plating process parameters, and uses quality control techniques such as tape tests and cross-section analysis to assess the adhesion of the gold layer. -
Q: Can Goldfinger accommodate customer-specific testing and inspection requirements?
A: Yes, Goldfinger is flexible and can accommodate customer-specific testing and inspection requirements. They work closely with their customers to understand their specific needs and provide tailored solutions. -
Q: What measures does Goldfinger take to minimize pinholes and porosity in the gold layer?
A: Goldfinger maintains strict cleanliness in the plating area, regularly monitors and adjusts the plating bath composition, and uses pulse plating techniques to produce a denser, less porous gold layer. -
Q: How does Goldfinger support customers in optimizing their PCB Designs?
A: Goldfinger engages with customers early in the product design phase to provide guidance and recommendations on optimizing the PCB layout and specifications for manufacturability and quality.
Conclusion
The quality of gold plated PCBs is crucial for ensuring the performance, reliability, and longevity of electronic products. Goldfinger, as a leading manufacturer of gold plated PCBs, is committed to delivering the highest quality products to their customers.
By continuously improving their manufacturing processes, maintaining strict raw material controls, employing advanced quality control techniques, and fostering strong partnerships with their customers, Goldfinger addresses the common quality issues associated with gold plated PCBs and ensures that their products meet the most stringent quality requirements.
As the demand for high-reliability electronics continues to grow, particularly in industries such as aerospace, military, and medical, the importance of gold plated PCB quality will only increase. Goldfinger is well-positioned to meet this demand and support their customers in developing and manufacturing cutting-edge electronic products.
No responses yet